Точность вакуумирования – Диссертация на тему «Комплексное исследование влияния вакуумирования на размерно-геометрическую точность и физико-механические свойства моделей и оболочковых форм с целью получения качественных точных отливок в литье по выплавляемым моделям» автореферат по специальности ВАК 05.16.04 – Литейное производство
Вакуум: контроль качества
Последние данные, полученные современной физикой, свидетельствуют о том, что вакуум – это не абсолютная пустота, а сложная система, имеющая свои законы, в которой рождаются и исчезают простейшие частицы. Другими словами, вакуум – это эфир, в котором материя существует как волна в радиоэфире. Поэтому развитие вакуумной техники – одна из самых перспективных отраслей, связанная со многими видами производства. Ученые считают, что, раскрыв все секреты вакуума, человечество получит неиссякаемый источник природной энергии, использование которой произведёт революцию в его развитии.
Свойства и применение вакуума
Вакуумом принято называть состояние газов, плотность которых меньше плотности воздуха на уровне земли, и, чем она меньше, тем чище вакуум. Одним из характерных свойств разреженных газов является уменьшение их химической активности. Например, окисление кислородом происходит намного медленнее. Также при разрежении наблюдается изменение в поведении заряженных частиц, траекториями полётов которых можно управлять в таких условиях.
Чем измеряется вакуум
Для измерения давления в системах используются манометры, а при пониженном давлении эти приборы называют вакуумметрами. Нижний предел давления, получаемый современной техникой, составляет 10-14 мм рт. ст. Измерить такое количество порядков одним прибором просто невозможно, поэтому существует несколько их видов.
Классический вакуумметр. Это самый простой вид прибора для измерения давления, не имеющий принципиальных конструктивных отличий от обычного манометра. Исключение составляет нулевая отметка справа и меньшая жёсткость пружинящего элемента. Основным его недостатком является небольшой диапазон измеряемых давлений, однако его низкая стоимость позволяет применять его в соответствующих условиях работы.
Рабочей жидкостью вакуумметра является масло, плотность которого известна, с минимальным парообразованием при низком давлении. Для повышения точности применяется вымораживание паров жидким азотом.
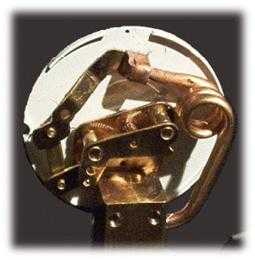
Тепловые вакуумметры делятся на терморезисторные и термопарные. Работа первых основана на свойстве терморезистора реагировать на изменение давления и подаваемого на него напряжения, а во втором типе используется термопара и изменение теплопроводности с изменением давления.
Ионизационный вакуумметр представляет собой вакуумный диод, состоящий из анода и коллектора, ток ионизации в котором падает с понижением давления, поскольку количество ионов, способных переносить заряд тоже уменьшается. В некоторых конструкциях катод остаётся холодным, а в других применяется его накал.
В настоящее время производятся комбинированные приборы, работающие сразу по двум и более методам. Их использование позволяет достигать высокой точности измерения и увеличении его диапазона.
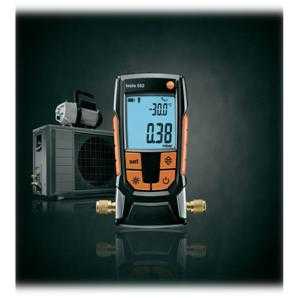
Вакуумметр может использоваться в различных системах как для измерения текущего давления, так и для контроля утечек. Обычно его подсоединение выполняется при помощи Т-образной трубки или тройника к насосу. В этом случае отсутствует регулятор или клапан сброса давления, поэтому его нельзя регулировать, что является существенным недостатком такого способа.
В некоторых видах производства на разных его стадиях необходимы различные значения чистоты вакуума для достижения определённого эффекта. В этих случаях в систему включается вакуумный регулятор.
Следующим способом является подключение датчика непосредственно к рабочей камере вакуумного агрегата. Измерения, полученные при таком способе подключения являются наиболее точными, поскольку все изменения давления от трения о стенки трубопроводов и потери на соединениях не влияют на показания.
Dim lights Embed Embed this video on your site
www.pro-vacuum.ru
Измерение вакуума
Измерение вакуума и давления играет огромную и важную роль в современном мире.
Области применения :
-
ядерная,
-
энергетическая,
-
газовая,
-
нефтехимическая,
-
биологическая,
-
фармацевтическая,
-
метеорологическая,
-
автомобильная,
-
экологическая,
-
полупроводниковая,
-
оптическая,
-
аэрокосмическая,
-
оборонная,
-
вентиляция,
-
фильтрация,
-
управление технологическими процессами в целом.
Давление, как правило, является следствием того, что молекулы в газе или жидкости воздействуют на окружающую среду? Обычно это стенки сосуда. Его величина зависит от силы ударов по определенной площади; отсюда появились такие единицы измерения: фунт силы на квадратный дюйм.
Соотношение между давлением (р), усилием (F) и площадью (А) определяется по формуле:
P=F/A
И эта формула работает при измерении вакуума (например космическое пространство) и при измерении избыточного (в гидравлических системах).Что же такое вакуум? Его определение не является точным, но обычно принято понимать, что давление ниже атмосферного. У него нет отдельных единиц измерения.
Другое определение различия между давлением и вакуумом – это отрасли, которые используют и производят оборудование для измерения вакуума и давления. В широком смысле, если сила на стенках вмещающего сосуда достаточна, чтобы позволить ее измерение непосредственно, мы имеем дело с измерением давления, но если сила слишком мала и должна быть косвенно выведена, мы находимся в области измерения вакуума.
Абсолютное и относительное измерение вакуума
Давления, измеренные на шкале, которая использует нулевое значение в качестве опорной точки, называются абсолютными давлениями. Атмосферное давление на поверхности Земли изменяется, но составляет приблизительно 105 Па (1000 мбар). Это абсолютное давление, потому что оно выражается в отношении нулевого.
Датчик предназначенный для измерения давления, выраженного в отношении атмосферного давления, и, таким образом, показывающий ноль, когда его измерительный порт содержит молекулы при атмосферном давлении. Измерения проводимые таким датчиком известны как измерение давления в относительном режиме. Таким образом, разница между значением абсолютного давления и значением избыточного является переменным значением атмосферного:
Абсолютное = избыточное + атмосферное.
Чтобы избежать серьезных ошибок, важно знать какой режим измерения вакуума используется: абсолютный или относительный. Обратите внимание, что эталонная линия для измерений калибровочной моды не является прямой, что иллюстрирует изменчивость атмосферного давления.
Единицы измерения вакуума и давления
Исторические единицы
К сожалению, в измерениях вакуума и давления существует множество единиц, что создает значительные проблемы как для новичков, так и для опытных специалистов. К счастью, жизнь становится легче, так как устаревшие и плохо определенные единицы исчезают в пользу единицы измерения СИ.
Многие старые единицы имеют очевидное практическое и историческое происхождение; Например, дюйм воды был единицей, используемой, когда давление измерялось водяным столбом, верхняя поверхность которого была видна на дюймовой шкале. Первоначально точность измерений вакуума, требуемая для таких систем, соответствовала довольно грубым методам измерения вакуума, и никто не беспокоился, была ли вода горячей или холодной. По мере роста технологических потребностей возникла потребность в более последовательных измерениях. Математические модели измерительных приборов были значительно усовершенствованы. Например, в одной традиционной схеме измерения вакуума ртутного барометра было принято для дифференциальных разложений между ртутью в колонне, стеклом, из которого изготовлена колонна, латунью, из которой изготовлена шкала, и стальным резервуаром. Однако даже с уточненными определениями и связанной с ними математикой многие традиционные единицы не могут использоваться в рамках современных технологий.
Единица измерения СИ
Единица измерения СИ – это паскаль, сокращенно обозначаемый Па, имя дано давлению одного ньютона на квадратный метр (Н/м2). В то время как легко визуализировать один квадратный метр, один ньютон сложнее, но он примерно равен нисходящей силе, действующей на руку, когда держит маленькое яблоко (если держатель стоит на поверхности земли!) Что касается повседневной жизни, один паскаль представляет собой очень небольшую величину, при этом атмосферное составляет примерно 100 000 Па. На дне кастрюли, наполненной водой, давление из-за глубины воды будет примерно на 1000 Па больше, чем на поверхности воды. Чтобы избежать использования громоздких чисел, кратным 103 и 0,001 назначаются префиксы, так что, например, 100 000 Па (105 Па) могут быть записаны как 100 кПа или 0,1 МПа.
Единицы измерения вакуума и конвертация
Взаимоотношения между паскалем и некоторыми другими единицами показаны в таблице, но обратите внимание, что не все могут быть или могут быть точно выражены. Надстрочные римские цифры в таблице относятся к примечаниям, которые следуют за ней.
Величина |
Символ |
В паскалях |
Паскаль |
Pa |
1 |
Атмосфера |
bar |
1 x 105 (примерно) |
миллибар |
mbar |
100 (примерно) |
гектопаскаль |
hPa |
100 (примерно) |
мм. рт. столба |
mmHg |
133.322… |
Дюйм рт. столба |
inHg |
3 386.39… |
Дюйм водяного столба |
inH2O |
248.6… to 249.1… |
Торр |
torr |
101 325/760 (примерно) |
Кгс/см2 |
kgf/cm2 |
98 066.5 (примерно) |
Методы измерения вакуума
Общие положения
В приборах для измерения вакуума используется ряд совершенно разных принципов. Некоторые из них имеют фундаментальный характер, например, измерение высоты столба жидкости с известной плотностью. Одним из таких примеров является ртутный барометр, в котором атмосферное давление может быть уравновешено столбом ртути. Расширение этой идеи для использования при высоких давлениях – использование металлических гирь, действующих над известной площадью, чтобы обеспечить силу, а не вес жидкости.
Часто вакуум может быть определено путем измерения механической деформации чувствительного элемента, который подвергается упругой деформации, когда изменяется разность давлений на его поверхностях. Механический прогиб может быть реализован и воспринят несколькими способами. Одним из наиболее распространенных типов движущихся механических элементов является эластичная диафрагма. Другим примером является труба Бурдона, где внутреннее давление вынуждает выпрямляться изогнутую трубку.
Такая механическая деформация может быть обнаружена несколькими способами: серией механических рычагов для непосредственного отображения деформации, измерения сопротивления в тензодатчике, измерения емкости, изменения частоты резонирующего элемента при растяжении или сжатии и т. д.
Когда вакуума глубокий и поэтому механическое отклонение слишком мало для измерения вакуума, используются косвенные средства, которые измеряют физические свойства, такие как теплопроводность, ионизация или вязкость, которые зависят от плотности числа молекул.
Столб жидкости
Один из самых ранних методов измерения вакуума, и все еще один из самых точных сегодня, состоит в том, что столб жидкости способен вытеснять жидкость из трубы.
Манометр, показанный на рисунке, представляет собой, по существу, заполненную жидкостью U-образную трубку, где вертикальное разделение поверхностей жидкости дает измерение разности давлений. На уровне нулевой точки d; давление L, обеспечивается жидкостью над ней, плюс давление p2 в верхней части трубки. В равновесии колонка поддерживается восходящим давлением p1, которое передается через жидкость из другой конечности.
Давление p1 на нижней поверхности жидкости определяется как:
p1= Pgh + p2
Где h – вертикальная высота столбца жидкости выше уровня нулевой точки,P Плотность жидкости, g – локальное значение ускорения силы тяжести. Если верхняя труба соединена с атмосферой (р2 = атмосферное давление), то р1 является калибровочным давлением; Если верхняя труба вакуумирована (т. Е. Р2 = ноль), то р1 является абсолютным давлением и прибор становится барометром.
Ртуть, вода и масло используются в различных конструкциях манометра, хотя для барометрических целей всегда используется ртуть; Его плотность более чем в 13 раз превышает плотность воды или масла, и поэтому требуется гораздо более короткая колонна. Около 0,75 м при измерении атмосферного давления. Плотность ртути также значительно более стабильна, чем плотность других жидкостей.
Измерение вакуума путём деформации упругого элемента.
Когда давление приложено к деформирующему элементу, он будет двигаться. Для создания датчика давления перемещение должно быть достаточно маленьким, чтобы оставаться в пределе упругости материала, но достаточно большим, чтобы быть обнаруженным с достаточным разрешением. Поэтому при более низком давлении используются тонкие гибкие компоненты, а при более высоких давлениях – более жесткие. Существует несколько методов, используемых для определения степени отклонения. Они варьируются от механического усиления, производя видимое отклонение указателя до электронных методов обнаружения.
Перечисленные ниже инструменты включают не все типы, а те, которые обычно широко используются в промышленности.
Диафрагмы
Мембрана, прикрепленная к жесткому основанию, будет подвергаться воздействию силы, если между каждой стороной существует разница в давлении. Диафрагмы проще производить круглыми, но возможны и другие формы. Разность вызовет отклонение диафрагмы с максимальным отклонением в центре, и это отклонение можно измерить с помощью различных механических и электронных датчиков. Поскольку центр отклоняется, поверхность диафрагмы также напряжена и может показать, с одной стороны, сжимающие напряжения вокруг внешней кромки и растягивающие напряжения вокруг центральной части диафрагмы. Эта конфигурация напряжений может быть обнаружена с помощью тензодатчиков, и из этой информации можно рассчитать вакуум.
Капсулы. По существу капсулы изготавливаются из пары диафрагм, соединенных по их внешним краям. У одного будет центральная арматура, через которую поступает давление, а перемещение центра другой диафрагмы относительно первого определяется датчиком некоторого типа. Ясно, что действие двух диафрагм, действующих последовательно, должно удвоить отклонение.
Сильфоны. Не существует четкого различия между сильфоном и капсулами, но сильфоны обычно имеют несколько секций, последовательно уложенных друг в друга, и, как правило, гофры малы по сравнению с диаметром. Сильфоны могут быть свернуты из трубы, образованы под давлением или образованы из сварных элементов.
Трубка Бурдона
Существуют различные конструкции, но типичной формой является закрытая труба с овальным поперечным сечением, изогнутая вдоль ее длины. Когда трубка находится под давлением, на стремится выпрямиться, и датчик обнаруживает это движение. Они могут быть сконструированы для работы в широком диапазоне, а также в манометрическом, абсолютном и дифференциальном режимах. Доступны простые «C» – образные, спиральные и спиральные типы. Электронное обнаружение движения конца обычно используется с кварцевыми спиральными устройствами.
Измерения вакуума путём измерения теплопроводности
Для измерения вакуума можно использовать передачу энергии от горячей проволоки через газ. Тепло переносится в газе путем молекулярных столкновений с проволокой, т.е. теплопроводностью, а скорость передачи тепла зависит от теплопроводности газа. Таким образом, точность этих приборов имеет сильную зависимость от состава газа. В области глубокого вакуума, где имеется молекулярный поток (число Кнудсена больше 3, где число Кнудсена = длина свободного пробега / характерный размер системы), теплопередача пропорциональна вакууму. Когда число молекул увеличивается, газ становится более плотным, и молекулы начинают сталкиваться друг с другом чаще. В этой так называемой переходной области потока (или потока скольжения, 0,01 <число Кнудсена <3) простая пропорция теплоотдачи к давлению не действительна. При еще более высоких давлениях (число Кнудсена <0,01) теплопроводность практически не зависит от него. Здесь конвекционное охлаждение горячих поверхностей обычно является основным источником теплообмена.
Вакуумметры Пирани
Тепловые потери от провода (обычно от 5 до 20 мкм) могут быть определены косвенно с помощью мостовой схемы Уитстона, которая нагревает провод и измеряет его сопротивление и, следовательно, его температуру. Существует два основных типа нагреваемых элементов. Традиционная и гораздо более распространенная конфигурация состоит из тонкой металлической проволоки, подвешенной в измерительной головке. Другая конфигурация – микрообработанная структура, обычно изготовленная из кремния, покрытого тонкой металлической пленкой, такой как платина. В обычной конфигурации тонкая металлическая проволока подвешена, по меньшей мере, с одной стороны, электрически изолированной в измерительной головке и находящейся в контакте с газом. Вольфрам, никель, иридий или платина могут быть использованы для проволоки. Провод электрически нагревается, и теплопередача измеряется электронным способом. Существует три общих метода работы: метод постоянной температуры, мост с постоянным напряжением и мост с постоянным током. Все эти методы косвенно измеряют температуру провода по его сопротивлению. Основным недостатком использования датчиков Пирани является их сильная зависимость от состава газа и их ограниченная точность. Воспроизводимость датчиков Пирани, как правило, достаточно хороша до тех пор, пока не произойдет сильное загрязнение. Диапазон измерения вакуума датчиков Пирани составляет приблизительно от 10-2 Па до 105 Па, но наилучшие характеристики обычно получают между приблизительно 0,1 Па и 1000 Па.
Ионизационные датчики измерения вакуума
Когда вакуум в системе ниже приблизительно 0,1 Па (10-3 мбар), прямые методы измерения вакуума с помощью таких средств, как отклонение диафрагмы или измерение свойств газа, таких как теплопроводность, уже не могут быть легко применимы , Поэтому необходимо прибегнуть к методам, которые в основном подсчитывают количество присутствующих молекул газа, т. е. измеряет плотность, а не вакуум. Из кинетической теории газов для данного газа с известной температурой Т давление р непосредственно связано с плотностью числа n через уравнение (в пределе идеального газа):
р = cnT
Где с – постоянная. Одним из наиболее удобных методов измерения плотности числа является использование некоторой методики ионизации молекул газа и последующего сбора ионов. В большинстве практических вакуумных датчиков для осуществления ионизации используются электроны с умеренной энергией (50 эВ до 150 эВ). Результирующий ионный ток напрямую связан с вакуумом и, таким образом, может быть выполнена калибровка. Последнее утверждение верно только в отношении конечного диапазона давлений, который определит рабочий диапазон прибора. Верхний предел давления будет достигнут, когда плотность газа будет достаточно большой, что при создании иона имеет значительную вероятность взаимодействия с молекулами нейтрального газа или свободными электронами в газе, так что ион сам нейтрализуется и не может достичь коллектора, для практических целей в типичных лабораторных системах или промышленных установках это можно принять за 0,1 Па (10-3 мбар).
Нижний предел вакуума манометра будет достигнут, когда электрический ток утечки в измерительной головке или измерительной электронике станет сравнимым с измеряемым ионным током или когда другой физический эффект (например, влияние посторонних рентгеновских лучей) вызовет появление токов этого величина. Для большинства датчиков, описанных в Руководстве, эти пределы лежат ниже 10-6 Па (10-8 мбар).
Основным калибровочным уравнением для ионизационной калибровки является:
Iс=K*n*Ie
Ic – ионный ток K – постоянная, содержащая вероятность ионизации молекулы газа какими бы то ни было средствами и вероятность сбора результирующего иона n – плотность числа молекул газа Ie – ток ионизирующего электрона.
Вероятность ионизации молекулы газа будет зависеть от множества факторов, и поэтому ионизационный датчик будет иметь разные значения чувствительности для разных видов газа. Большинство практических вакуумных датчиков используют электронное воздействие для ионизации молекул газа, и это может быть достигнуто просто «кипящими» электронами от нити накаленной проволоки и притягивающей их к какому-то электронному коллектору. Затем ионы притягиваются к коллектору. К сожалению, вероятность ионизации молекулы газа электроном настолько мала за один проход в калибровке нормальных размеров, что необходимо увеличить длину пробега электронов и тем самым увеличить вероятность того, что какой-либо один электрон создает ион.
Широко используются два метода. В калибровочном ионизационном датчике горячего катода электроны, полученные в горячей нити накала, притягиваются к сетке, изготовленной из очень тонкой проволоки и при положительном электрическом потенциале. Поскольку сетка открыта, есть очень большая вероятность того, что электрон пройдет через сетку и не ударит провод. Если сетка окружена экраном с отрицательным электрическим потенциалом, электрон будет отражен этим экраном и будет притягиваться обратно к сетке. Этот процесс может происходить много раз, прежде чем электрон окончательно попадает в сетку . В результате очень длинные траектории электронов могут быть достигнуты в небольшом объеме. В противоположность этому, ионы притягиваются непосредственно в коллектор.
Ионизационная лампа с холодным катодом обходится без горячей нити и использует комбинацию электрических и магнитных полей. Любой электрон будет вращаться вокруг магнитных силовых линий до того, как он, в конечном счете, будет собран на положительно заряженном аноде. Фактически, длина пути будет такой большой, а вероятность ионизации настолько велика, что после запуска будет создан самоподдерживающийся газовый разряд, при условии, что ионы будут быстро вытесняться из области разряда ионным коллектором.
Выбор устройства для измерения вакуума
Прежде чем выбрать прибор для измерения вакуума и определить подходящего поставщика, важно установить критерии отбора. Они будут включать множество факторов, и этот раздел призван помочь потенциальному пользователю сделать выбор.
-
Глубина измерения вакуума
-
Характеристики среды
-
Внешняя среда
-
Физические характеристики прибора
-
Тип использования
-
Безопасность
-
Установка и обслуживание
-
Преобразование сигнала
tako-line.ru
Вакуумирование – Справочник химика 21
При взрыве сорвало крышку мерника, были деформированы другие аппараты и коммуникации и выбиты стекла в производственном помещении и пункте управления. Взрыв произошел при случайном смешении меланжа (смесь азотной и серной кислот) с органическим растворителем (по всей вероятности, с ацетоном), который оказался в мернике в момент заполнения его меланжем. При подго-товке производства к пуску после длительной консервации оборудование и коммуникации промывали органическим растворителем. После промывки мерник был просушен вакуумированием, однако качество осушки аппарата не было проконтролировано. Через 5 мин после начала заполнения сборника меланжем в соединениях шланга, связывающего сборник с наполнительным трубопроводом, началось обильное выделение окислов азота, после этого последовал взрыв. [c.362]Отбор проб воздуха для определения в нем концентрации химических соединений производится чаше всего аспирационным методом, основанным на протягивании известного объема воздуха через поглотительную систему. Соединения улавливаются жидкими или твердыми поглотителями. Аспирация анализируемого воздуха через поглотительные среды производится электроаспираторами ( Малыш , АЭРА, ПРУ-4, МК-1, УЛМК-3, ЛК-1 и др.) и реже вакуум-насосами. Так как приборы с жидким поглотителем основаны на принципе абсорбции, то степень улавливания соединений в них будет зависеть от начальной концентрации соединений в газе. С уменьшением концентрации в отбираемой пробе снижается степень улавливания и увеличивается разница между полученным и истинным значениями. В табл. 2.1 приведены сравнительные данные для жидкостных поглотительных приборов, наиболее часто используемых в промышленной практике. При концентрации химических соединений в газах (например, KF, НС ) > 1000 мг/м степень улавливания в указанных поглотителях составляет 97— 99 %. В этом случае ошибка определения не превышает 0,1—3 %, что вполне допустимо. Применение поглотителей для отбора проб с концентрацией соединений 100 мг/м вызывает сомнение. В этом случае более надежен отбор проб в вакуумированные сосуды (стеклянные, металлические) емкостью 1,5—5 л, заполненные на 0,05— 0,1 жидким поглотителем. Этот метод отбора проб основан на явлении адсорбции химических соединений на стенках сосуда. В результате получасового промывания стенок имеющимся в сосуде жидким поглотителем соединения из газа количественно переходят в жидкий поглотитель. Для повышения чувствительности метода [c.23]
Рис. 16. Схема прибора для вакуумирования катализатора и заполнения его пор водой | ![]() |
Если доступ к сварному шву возможен только с наружной или только с внутренней стороны аппарата, испытание на плотность проводится методом вакуумирования сварных швов. Сварной шов смачивается мыльным раствором. На исследуемый участок накладывается коробка, имеющая по всему периметру уплотнение из губчатой резины. Коробка соединяется с вакуум-насосом, а через смотровое стекло, смонтированное на коробке, или через стенки коробки, если она изготовлена целиком из оргстекла, ведется наблюдение за сварным швом. Наличие мыльных пузырей указывает на дефекты сварки. Этот способ проверки применяется также при контроле сварки отдельных листов крупных резервуаров. [c.141]
Обеспечив необходимую герметичность в колбе, включают вакуум-насос и вакуумируют колбу при остаточном давлении 5—6 мм рт. ст. в течение 20—30 мин. Время вакуумирования можно сократить, если колбу с катализатором подогреть до 350—400° С. [c.46]
Термохимическое рафинирование — термотехнологический процесс получения металлов обработкой расплавленных черновых металлов с помощью различных присадок (солей, шлаков), окислением примесей, вакуумированием расплава и т. д. Этим способом получают медь, цинк, кадмий, олово, сурьму, ртуть и т. д. [c.41]
Считается, что тренировка поверхности катализатора при адсорбции из растворов меиее важна, чем при адсорбции газов. Поэтому обычно обходятся без предварительного вакуумирования. [c.87]
ПОДЛОЖКОЙ. Некоторые газы и пары (особенно водяной пар), сорбированные гидрофильной пористой подложкой, трудно удаляются с помощью вакуумирования и остаются в системе, вызывая неконтролируемые эффекты в процессе плазменной полимеризации. [c.81]
В газоразрядных лампах используется излучение положительного столба низкого давления или непосредственно, или путем последующего возбуждения флуоресценции ультрафиолетовым излучением (люминесцентные лампы). В натриевых и ртутных лампах в качестве источника света используется дуга с горячим катодом, которая зажигается в парах указанных элементов. Величина давления в лампе определяется ее рабочей температурой, поэтому вакуумный объем, в котором происходит разряд, термически изолируют, заключая лампу в еще один вакуумированный стеклянный баллон. Лампы работают на переменном токе, и поэтому каждый электрод снабжен термоэлектронным эмиттером электронов в виде слоя оксида. Зажигание и разогрев лампы происходят под воздействием высоковольтных импульсов, вырабатываемых при размыкании индуктивной цепи или при введении дополнительного газа (неона). [c.94]
В технологии используются режимы вакуумирования и другие, не дающие эффективного результата. Необходимо осуществить поток газа из капилляров и встречный поток жидкости, замещающий в них газ. Этого можно достигнуть, придав жидкости характер струй, направленных внутрь тела и не перекрывающих полностью их сечения. Подобные струи в результате кумуляции образуются на капиллярных менисках при выходе ка них фронта ударной волны. [c.131]
Влияние на фазовый переход могут оказать внутренние источники тепла, создаваемые инфракрасными лучами (радиационная сушка) и электромагнитными колебаниями (ТВЧ- и СВЧ-сушка), а также ультразвук (акустическая сушка) и вакуумирование (сублимационная сушка). [c.161]
Реактор недостаточно вакуумирован 0,0015 Нечистый азот в линии [c.170]
В качестве возможных компонентов судовых высоковязких топлив были выбраны остатки прямой перегонки нефти мазуты (М3), гудроны из смеси сернистых западносибирских (ГЗ) и высокосернистой арланской (ГА) нефтей и асфальтиты (А) процесса деасфальтизации гудронов, а также остатки вторичных процессов крекинг-ос-татки процесса висбрекинга гудронов тех же западносибирских (КЗ) и арланской (КА) нефтей, утяжеленный вакуумной перегонкой крекинг-остаток из остаточного сырья – вакуумированный крекинг-остаток (ВКО) и крекинг-остаток из дистиллятного сырья – дистиллят-ный крекинг-остаток (ДКО). [c.48]
Коррозионные свойства тяжелых остаточных компонентов судового высоковязкого топлива вакуумированного крекинга-остатка-ВКО, асфальта А и арланского гудрона – ГА не исследовались из-за неполного отмывания металлических шариков от этих нефтепродуктов. [c.97]
Прибор имеет вертикальную кипятильную трубку 3 с внутренним диаметром 34 мм и длиной 500 мм. Регулируемое нагревание жидкости обеспечивается снизу электрической свечой И, размещенной в углублении 10. Наружные стенки углубления для усиления парообразования покрыты наплавленным стеклянным порошком. С помощью колпака 12, доходящего почти до дна, все образующиеся пузырьки пара собираются, смешиваются с жидкостью и направляются в разбрызгивающую трубку 9 диаметром 4 мм, где происходит дополнительное перемешивание в двух шарообразных расширениях. Затем смесь через конец 7 трубки 9 в виде брызг попадает на карман 6 термометра. Разбрызгивающая трубка в.месте с шариками окружена вакуумированной рубашкой 8. Отделившаяся от пара жидкость стекает с кармана термометра и через узкую кольцевую щель между рубашкой 8 и кипятильной трубкой 3 возвращается в цикл. Кончик термометра погружен в небольшое количество ртути и защищен карманом 6 с припаянным [c.56]
Прозрачность стекла позволяет наблюдать за ходом процесса. В адиабатических процессах, протекающих при температурах примерно до 120 °С, кожух из стекла, вакуумированный до остаточного давления 10 мм рт. ст., обеспечивает достаточную термоизоляцию аппарата. При более высоких температурах, а также при использовании крупногабаритных аппаратов в качестве термоизоляционного материала применяют стекловолокно в слое изоляции оставляют смотровую щель, предназначенную для визуального наблюдения за ходом процесса (см. разд. 7.7). Важным преимуществом стекла является его высокая коррозионная стойкость. Поэтому многие химические реакции и процессы разделения проводят в аппаратах и установках, изготовленных из стекла или других керамических материалов. Широкому применению стекла в химической промышленности способствует высокая твердость и незначительная шероховатость поверхности стеклянных изделий. Стенки стеклянных аппаратов во время работы незначительно загрязняются и легко поддаются очистке. Ценным свойством стекла является также сравнительно небольшой коэффициент линейного расширения. Использование стеклянных аппаратов при переработке фармацевтических продуктов и однократной или двойной перегонке воды дает возможность получать продукты без запаха, вкуса й, главное, без примесей металлов. [c.325]
Юнге [233] провел измерения тепловых потерь в колонне с вакуумированной рубашкой и в колонне с тепловой изоляцией из стекловолокна толщиной 50 мм. Результаты этих исследований в зависимости от температуры внутри колонны приведены на рис. 111 на рисунке представлены также данные Роуза [153], взятые из табл. 32. [c.178]
Дефлегматор представляет собой сосуд с изолирующей вакуумированной рубашкой, который предназначен для загрузки [c.250]
Харрис [125] разработал удобную номограмму (рис. 187), с помощью которой можно определить размеры вакуумных линий и производительность насоса. При разработке номограммы предполагалось, что скорость вакуумирования изменяется не более чем на 30%. [c.265]
Пример I Пример 2 р — давление в вакуумированном сосуде, [c.266]
СКОЛЬКО СОТ калорий на 1 люль. При хемосорбции тепловые эффекты по величине приближаются к тепловым эффектам химических реакций и составляют41 900—419000 кдж/кмоль (10—100 ккал/моль). Так, например, теплота адсорбции кислорода на углероде равна 335 200 кдж/кмоль (около 80 ккал/моль), а теплота сгорания углерода составляет 393860 кдж/моль ккал/моль). В этом случае действительно образуется стабильное соединение и при попытках удалить адсорбат с поверхности путем вакуумирования вместе с кислородом выделяется некоторое количество окиси углерода. [c.205]
При иогружепии вакуумированного катализатора в смачивающую жидкость выделяется тепло, количество которого пропорциопалыю величине поверхности навески [c.86]
Образцы окисленного и остаточного битумов с примерно равной консистенцией после предварительного вакуумирования выдерживались при повышенных температурах. Чтобы обеспечить равную скорость газообразомния для обоих битумов, температуру окисленного битума меняли в пределах 240—287°С, а остаточного — 272—341°С продолжительность нагрева составляла 32 и 19 ч соответственно. В результате термической обработки оба образца стали более жидкими, состав выделенных при этом газов (мл в нормальных условиях на 1 кг битума) был разным [c.19]
Рис. 1. Инфракрасные спектры цеолитов после вакуумпрования при. ТЗ ), 673 (2), 773 (3), 673 К, а таки е цеолита, обработанного пиридином и вакуумированного при | ![]() |
Спектр катализатора МдСг Оуу – AI Oj после 3 часов тренировки в кислороде с последующим вакуумированием при 400 С аналогичен спектру образца, тренированного в вакууме. Однако после адсорбции [c.119]
Иногда проводят бестигельную зонную плавку тугоплавких веществ. Ес применяют, если нельзя подобрать материал для лодочки не реагирующий с расплавом. В данном методе пруток очищаемого материала располагают верти- кально в вакуумированной камере и создают расплавленную зону с помощью электронного луча. Жидкость удерживает от стекания поверхностное натяжение расплава. [c.380]
В сосуде при 273 К и 1,01 10 Па находится 10 моль одноатом- юго газа в идеальном состоянии. Рассчитайте конечную температуру, давление газа и работу процесса расширения газа до объема, в дьз раза превышающего первоначальный а) при медленном изотермическом расширении в цилиндре с поршнем, двигающемся без трения б) п])И адиабатическом расширении в аналогичных условиях в) при мгновенном удалении перегородки между сосудом и вакуумированным просгранством того же объема. Объясните различие результатов, полученных в трех процессах. [c.58]
Великолепные свойства жестких и эластичных пенополиуретанов, а также вспененных эпоксидных смол и некоторых других реактопластов обратили на себя внимание многих фирм США ио выпуску оборудования для переработки пластмасс. Отличительной чертой переработки этих материалов является их ограниченная жизнеспособность , чем, в свою очередь, определяются конструктивные особенности оборудования [234]. Смешивание ингредиентов осуществляется, главным образом, в аппаратах непрерывного действия. Применяемое мешалки отличаются относительно простой конструкцией. Рабочие скорости их весьма велики и достигают 5 тыс. об/мин. Оборудование для формования пенополиуретанов фирмы выпускают в виде комплексных агрегатов, содержаигих устройства для перемешивания компонентов, транспортировки смеси и формования. Можно отметить два основных типа агрегатов для переработки пенополиуретана — это машины для формования блоков и изделий и устройства для нанесения покрытий. Формование блоков может осуществляться как в индивидуальных формах, так и непрерывно (в нескольких формах). При непрерывном получении пенополиуретановых блоков исходные компоненты подаются в цилиндрическую смесительную камеру, из которой через щелевой канал смесь поступает на непрерывно движущийся бумажный короб. При перемещении вместе с коробом смесь подвергается тепловому воздействию и вакуумированию в специальных камерах, при выходе из которых смесь оказывается полностью отвержденной. Производительность описанной установки достигает 75 кг мин плотность конечного продукта— 24 кг/м , максимальная ширина листов — 2 м. Непрерывное производство позволяет значительно улучшить качество готового продукта и стабилизировать его свойства. [c.194]
Наблюдение с помощью лупы за подсвеченной сзади шкалой термометра и подсчет десятичных делений шкалы через пленку конденсата и не представляет трудностей, если верхнюю часть эбуллиоскопа предварительно протравить в течение 2мин 1%-ной фтористоводородной кислотой и затем прокипятить в мыльной воде. Кипятильная трубка 3 до самого конденсатора 2 окружена изолирующим слоем стекловолокна 4, в котором оставлена узкая смотровая щель. Под теплоизоляцией 4 на трубку 3 намотана спираль компенсационного электрообогрева 5, выполненная из тонкой проволоки. Мощность обогрева можно рассчитывать, условно представляя спираль в виде охватывающей прибор бесконечно длинной цилиндрической оболочки с равномерно распределенными источниками тепла. Электрообогрев регулируют с помощью амперметров и калибровочной кривой таким образом, чтобы без включения системы подогрева кубовой жидкости приближенно устанавливалась ожидаемая температура. В этом случае даже ттары труднолетучих веществ доходят до конденсатора, расположенного на 250 мм выше кармана термометра. Адиабатический режим в разбрызгивающей трубке обеспечивается четырехкратной защитной системой, включающей вакуумированную рубашку, слой нагретой до кипения жидкости, стекающей в кольцевой щели, спираль компенсационного электрообогрева и слой теплоизоляции. Через штуцер 1 обычно загружают жидкость, а при работе под вакуумом к нему присоединяют вакуумную линию. [c.57]
Очень изящный метод, однако обеспечивающий точность измерения всего лишь =tO,5 мм рт. ст., описан Нательсоном и Цукерманом [36]. Он основан на том явлении, что капля жидкости, висящая на конце вертикального капилляра (трубки термометра), в результате постепенного вакуумирования окружающего пространства отрывается от капилляра. В момент отрыва капли считывают показание ртутного манометра, соответствующее достигнутому давлению. [c.58]
Паровая камера 7 и насос Коттрелля 4 в усовершенствованном приборе, показанном на рис. 49, с целью исключения частичной конденсации паров, помещены в вакуумированную рубашку 12. Наружная стенка вакуумированной рубашки поддерживается при температуре кипения смеси с помощью циркуляционного термостата. [c.89]
В отличие от полых трубок (см. разд. 7.3.1) колонна Вигре обладает большей орошаемой поверхностью за счет большого числа заостренных глубоких вмятин, кроме того в средней части она имеет ввод для питающей смеси. Шрадер и Рицер 15] использовали такую колонну в качестве дефлегматора в приборе для микроперегонки (рис. 129). Он содержит плоскодонную колбу 1, которая обеспечивает постоянную поверхность испарения, и приемник 3 со стеклянными трубками 2 емкостью 0,1 мл. Дистиллят стекает к трубкам 2 по стеклянной нити 4. Разумеется, прибор можно применять только для разделения высококипяищх веществ, так как в нем не предусмотрен водяной холодильник. Более вместительный прибор Кленка [6] также имеет только воздушное охлаждение (рис. 130). Колонка длиной 8,5 или 13 см со спиральной металлической лентой длиной 120 мм и вакуумированной рубашкой обеспечивает хорошее разделение при очень малом количестве смеси. [c.199]
Перед проведением ректификации проверяют качество герметичности кожуха колонны с помощью высокочастотного течеиска-теля. При герметичности кожуха (в затемненном рабочем помещении) в его полости не должно возникать свечения, возможна зеленая флюоресценция стеклянных стенок кожуха. Если возникает свечение, проводят повторное вакуумирование. Для этого используют трехступенчатый диффузионный ртутный насос. Пары ртути вымораживают в глубокоохлаждаемом адсорбере с активным углем или силикагелем, установленном между насосом и колонной. Для смазки кранов применяют высоковакуумную смазку (см. разд. 9.4). При достижении высокого вакуума, соответствующего остаточному давлению 10″ мм рт. ст. и ниже, кран закрывают. [c.252]
После сборки вакуумной установки необходимо испытать ее на герметичность. Сначала проверяют вакуум, создаваемый насосом, путем присоединения его к буферной ёмкости на 5—10 л. Затем проверяют герметичность кранов, шлифовых соединений и мест спаев. Целесообразно размещать краны или клапаны на установке таким образом, чтобы можно было отдельно испытать на герметичность различные ее части. Для проверки герметичности применяют высокочастотный течеискатель типа Тесла с электродом в виде щетки (рис. 191). Принцип работы прибора основан на возникновении искры от электрода в месте пропускания воздуха. Можно также проверить герметичность аппарата с помощью стетоскопа или смазать предполагаемые места пропусков мыльным раствором и создать в установке избыточное давление около 0,5 кгс/см . Изящный метод проверки герметичности состоит в том, что на поверхность вакуумированной установки наносят кисточкой слабощелочной раствор флоуресцина или эозина в метаноле, затем ее облучают в темноте ультрафиолетовым светом, при этом в герметичных местах будет отчетливо наблюдаться флуоресценция. Специальные методы испытаний установок, работающих в условиях высокого вакуума, описаны Лаппорте [119] и Мён-хом [126]. [c.268]
Подогретую исходную смесь непрерывно с определенной скоростью впрыскивают в вакуумированную колбу 8. При этом жидкость распределяется по стенкам колбы в виде тонкой пленки. В результате дополнительного разрежения при впрыскивании низкокипящая фракция сразу же испаряется. Пленка, образованная на нагретых стенках колбы, имеет большую поверхность испарения, поэтому в течение небольшого периода времени испа- [c.269]
Колонну с елочным дефлегматором обычно изготавливают со съемным теплоизоляционным кожухом, а колонну Янцена — с вакуумированным кожухом. Для всех безнасадочных колонн важно поддерживать в ходе ректификации температуру стенки ниже температуры стекающей флегмы, так как в противном случае нарушается равномерное образование пленки на поверхности стенки. Следует отметить, что эффективность безнасадочных колонн возрастает при уменьшении нагрузки. Используя многотрубчатые колонны, состоящие из параллельно соединенных труб небольшого диаметра, можно получить любую необходимую производительность. Подобную многотрубчатую колонну еще в 1936 г. запатентовал Фенске [201. [c.338]
Штаге [35 ] предложил для непрерывных процессов разделения лабораторные и промышленные колонны с колпачковыми тарелками, предназначенные для работы в широком интервале нагрузки по жидкости. Эффективность этих колонн не зависит от нагрузки по жидкости и соотношения нагрузок паровой и жидкой фаз, а также от кратковременных нарушений технологического режима процесса. В лабораторных установках широко применяют тарельчатые колонны Брууна [37] (рис. 262). По конструктивному выполнению они приближаются к промышленным колоннам с колпачковыми тарелками. Их недостаток заключается в том, что переточ-ные трубы для флегмы размещены снаружи колонны, и это может приводить к значительному переохлаждению жидкости. Степень охлаждения можно уменьшить, поместив колонну в заполненный воздухом или вакуумированный кожух (рис. 263). Трубы для подвода 1 и отвода 3 жидкости (см. рис. 262) расположены таким об- [c.346]
chem21.info
Способ контроля герметичности в вакуумной камере
Использование: в испытательной технике для повышений точности контроля герметичности изделий космической техники в вакуумной камере. Сущность изобретения: заполняют изделие контрольным газом до заданного давления и одновременно подают в камеру тарированный поток контрольного газа, замеряют концентрацию контрольного газа в камере от тарированного потока и от изделия, прекращают подачу в камеру тарированного потока, замеряют концентрацию контрольного газа в камере от изделия, удаляют контрольный газ из изделия, замеряют остаточную концентрацию контрольного газа в камере и по степени уменьшения концентрации контрольного газа от изделия с учетом степени уменьшения концентрации контрольного газа от тарированного потока определяют величину негерметичности изделия.
Изобретение относится к области испытательной техники, в частности к испытаниям изделий космической техники на герметичность.
Известны способы контроля герметичности изделий в вакуумной камере, сущность которых заключается в следующем. Над контролируемой поверхностью изделия создается разрежение с помощью откачных средств. Изделие заполняется контрольным газом. Контрольный газ под действием разности давлений проникает через микронеплотности изделия в отвакуумированную полость, которая сообщается с течеискателем. По приращению показаний выносного прибора течеискателя определяют величину негерметичности изделия [1] Недостатком известных способов является значительная длительность испытаний изделий на герметичность (особенно сложных, состоящих из множества проверяемых элементов, каковыми являются изделия космической техники). Наиболее близким по технической сущности к предложенному является способ контроля герметичности изделий в вакуумной камере, заключающийся в том, что заполняют изделие контрольным газом до заданного давления, замеряют концентрацию контрольного газа в камере, удаляют контрольный газ из изделия, повторно замеряют концентрацию контрольного газа в камере и по степени уменьшения концентрации контрольного газа определяют величину негерметичности изделия [2] Этот способ принят заявителем за прототип. Недостатком прототипа является его невысокая точность контроля, то есть невысокая точность определения величины негерметичности изделия, обусловленная тем, что определение величины негерметичности изделия по соотношению степени уменьшения концентрации контрольного газа от изделия к остаточной концентрации контрольного газа (теоретически к реакции течеискателя на атмостерный воздух с содержанием в нем гелия 1/200000 а практически на среду испытательного помещения, окружающую камеру, содержание в которой гелия значительно выше и постоянно меняется) приводит к погрешностям определения, причем в меньшую сторону, что способствует пропуску микронеплотностей на изделии. Техническим результатом предложенного способа является повышение точности контроля. Указанный технический результат достигается тем, что в известном способе контроля герметичности изделий в вакуумной камере, заключающемся в том, что заполняют изделие контрольным газом до заданного давления, замеряют концентрацию контрольного газа в камере от изделия, удаляют контрольный газ из изделия, замеряют остаточную концентрацию контрольного газа в камере и по степени уменьшения концентрации контрольного газа от изделия определяют величину негерметичности изделия, одновременно с заполнением изделия подают в камеру тарированный поток контрольного газа, замеряют концентрацию контрольного газа в камере от тарированного потока и от изделия, прекращают подачу тарированного потока, а определение величины негерметичности изделия проводят с учетом степени уменьшения концентрации контрольного газа от тарированного потока. Определение величины негерметичности изделия по соотношению степени уменьшения концентрации контрольного газа от изделия к степени уменьшения концентрации контрольного газа от тарированного потока контрольного газа, поступающего в камеру аналогично поступлению контрольного газа через микронеплотности изделия, повышает точность определения, то есть повышает точность контроля. Предложенный способ осуществляется следующим образом. Помещают изделие в вакуумную камеру и вакуумируют камеру до рабочего вакуума. В процессе вакуумирования камеры заполняют изделие контрольным газом до заданного давления и одновременно подают в камеру тарированный поток контрольного гада величиной Qкт (величину Qкт выбирают в пределах (0,5-1,0) допустимой величины негeрметичности изделия Qизд.доп. заданной в конструкторской документации на изделие). После достижения в камере рабочего вакуума замеряют концентрацию контрольного газа в камере Акт+изд от тарированного потока и от изделия. Прекращают подачу тарированного потока. Замеряют концентрацию контрольного газа в камере Аизд от изделия. Удаляют контрольный газ из изделия (из элементов высокого давления контрольный газ стравливают до атмосферного давления, из элементов низкого давления после стравливания до атмосферного давления остатки контрольного газа удаляются вакуумированием этих элементов дополнительным вакуумным насосом). Замеряют остаточную концентрацию контрольного газа в камере Аост. По степени уменьшения концентрации контрольного газа от изделия с учетом степени уменьшения концентрации контрольного газа от тарированного потока определяют величину негерметичности изделия Qизд из соотношения При использовании предложенного способа появляется возможность более качественного (за счет подобности измерения всех концентраций контрольного газа в камере) контроля герметичности изделий космической техники, особенно тех (например комбинированной двигательной установки), которые имеют в своем составе клапаны, пропускающие на начальном этапе заполнения изделия (при низких давлениях) значительные количества контрольного газа и герметизирующиеся по мере повышения давления.Формула изобретения
Способ контроля герметичности изделий в вакуумной камере, заключающийся в том, что заполняют изделие контрольным газом до заданного давления, замеряют концентрацию контрольного газа в камере от изделия, удаляют контрольный газ из изделия, замеряют остаточную концентрацию контрольного газа в камере и по степени уменьшения концентрации контрольного газа от изделия определяют величину негерметичности изделия, отличающийся тем, что одновременно с заполнением изделия подают в камеру тарированный поток контрольного газа, замеряют концентрацию контрольного газа в камере от тарированного потока и от изделия, прекращают подачу тарированного потока, а определение величины негерметичности изделия проводят с учетом степени уменьшения концентрации контрольного газа от тарированного потока.www.findpatent.ru
Измерение скорости откачки вакуумных насосов
Для измерения скорости откачки применяют в основном три метода: измерение при постоянном объеме, основанное на изменении давления в откачиваемой системе за определенный промежуток времени; измерение при постоянном давлении, при котором измеряется скорость поступления газа в непрерывно откачиваемую вакуумную систему; измерение методом сравнения.
Для измерения этим методом насос присоединяют к сосуду с известным объемом V, причем объем должен быть достаточно большим. При откачке воздуха из объема V измеряется разность давлений (рх—р2) за определенный промежуток времени t = t2 — t1. Падение давления в вакуумной системе объемом V при постоянной скорости откачки можно описать уравнением
откуда следует, что
Это уравнение справедливо только при отсутствии в сосуде течей или газовыделения. На практике поступают следующим образом: сначала откачивают вакуумную систему до предельного давления р0, затем опять заполняют ее газом и снимают данные только до тех пор, пока линия изменения давления Ig р — tau остается прямой в полулогарифмическом масштабе. Иначе говоря, конечное измеренное давление должно еще значительно превышать предельное давление.
Соединение резервуара с насосом должно быть выполнено с максимальной пропускной способностью. Для вычисления точного значения скорости откачки насоса следует учесть пропускную способность соединительного трубопровода L по уравнению
где S — скорость откачки по графику.
Метод постоянного объема не требует специального оборудования, кроме манометров, однако его применяют не во всех случаях. Точность определения ограничена значением пропускной способности соединительного трубопровода. Приведенное уравнение справедливо только при изотермической откачке, которая характерна для молекулярного потока. Кроме того, этот метод пригоден в. основном для насосов с относительно небольшой скоростью откачки. Объем измерительного сосуда должен быть примерно равен объему газа, удаляемого испытываемым насосом за 1 с. Для больших насосов со скоростями откачки порядка нескольких сот литров в секунду метод этот мало пригоден, так как требуются измерительные сосуды очень большого объема.
Метод заключается в том, что создается поток газа в насос, при котором устанавливается некоторое постоянное давление на входе в насос р. Скорость откачки насоса тогда
Для создания и измерения потока газа, поступающего в насос, применяют способы: натекания газа через специальный натекатель или капилляр; циркуляции; калиброванного трубопровода или калиброванного отверстия; накопления.
Если газ поступает в насос через натекатель, то количество проходящего газа можно измерить бюреткой, ротаметром, дроссельной шайбой, мерным соплом и др. При приближении к предельному давлению данного насоса скорость откачки 5 уменьшается согласно уравнению
где Sp — скорость откачки в сечениии с давлением р; р0 — предельное давление.
При этом поток газа через сечение
(92)
Если присоединить к системе натекатель и сделать искусственную течь, через которую будет протекать газ объемом V л/с воздуха, измеренный при атмосферном давлении, то поток газа через течь
(93)
Тогда общий поток через рассматриваемое сечение
(94)
так как давление в системе повысится на величину Др. Подставляя значения Q и Q’ из уравнений (92) и (93) в уравнение (94), получим
откуда
или
или
где V — объем воздуха, поступающего в установку, при давлении 760 мм рт. ст., в л/с; P1 — давление при натекании V в мм рт. ст.; р0 — предельное давление с закрытым натекателем в мм рт. ст.
При измерении с помощью бюретки последовательно с натекателем помещают измерительную бюретку с трехходовым краном (рис. 527), погруженную открытым концом в стакан с вакуумным маслом. При измерении открывается натекатель, и по манометру в системе устанавливается определенное давление рх; после этого бюретка с помощью трехходового крана отсоединяется от атмосферы и присоединяется к натекателю. Воздух из объема бюретки через натекатель поступает в насос, уровень масла в бюретке повышается, так как на наружную поверхность масла в стакане давит атмосферное давление, а внутри бюретки создается вакуум. Время подъема масла на определенную высоту измеряется секундомером, после чего бюретка вновь соединяется с атмосферой.
По скорости подъема масла в бюретке h/? определяют количество вытесненного из бюретки воздуха ?Q. С учетом того, что
где р — давление и V — объем газа в бюретке, можем записать
(95)
где V0 — начальный объем бюретки и соединительного шланга от уровня масла в стакане до натекатели в л; рб — давление внешней среды в мм рт. ст.;
— давление столба масла в бюретке, поднявшегося за время tau в мм рт. ст.
— объем столба масла, поднявшегося в бюретке
за время т, в л;
h — высота градуированной части бюретки в мм; n — число делений градуированной части бюретки;
V6 — объем градуированной части бюретки в л;
рм— плотность масла в г/см3;
ррт— плотность ртути в г/см3; h — высота подъема масла в бюретке за время т (в делениях шкалы).
Пренебрегая величиной ΔpΔV в уравнении (95) по сравнению с первыми двумя слагаемыми в скобках, получим
Соответственно
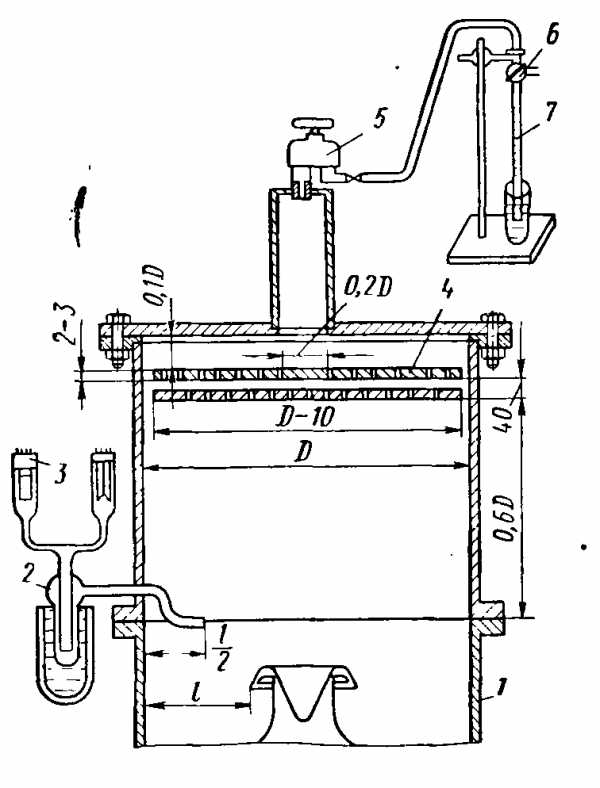
Рис. 527. Измерительный колпак для измерения скорости откачки
диффузионного насоса методом постоянного давления: 1 — корпус насоса; 2 —
ловушка, охлаждаемая жидким азотом; 3 — манометры; 4 —
рассеивающие диски с отверстиями диаметром 5 мм, расположенными по
квадратной сетке, отверстия для второго диска смещены на
половину диагонали квадрата по отношению к отверстиям первого диска; 5 — натекатель; 6 — трехходовой кран; 7 — бюретка
Если нужно найти скорость откачки насосом не воздуха, а другого газа, то следует применить закрытую измерительную бюретку (рис. 528). При измерении описанным методом нужно следить за тем, чтобы температура бюретки во время измерения была постоянной, в противном случае ошибки при измерении будут значительными. При измерении методом циркуляции впускной патрубок насоса соединен с его выпускным патрубком трубопроводом, пропускная способность которого известна; тогда
а скорость откачки насоса
Схема измерения дана на рис. 529. После откачки всей системы до определенного давления закрывается кран 4 и измеряется перепад давлений двумя манометрами M1 и M2. Этот метод нельзя считать достаточно точным, так как режим течения газа в трубопроводе может изменяться, и рассчитать точно пропускную способность трубопровода в каждой точке измерения не удается.
Метод калиброванного трубопровода состоит в том, что в насос впускается газ через трубопровод, пропускная способность которого известна, и измеряется перепад давлений на концах трубопровода.
Тогда скорость откачки
где P1 и р2 — показания двух манометров. Этот метод имеет тот же недостаток, что и предыдущий, и применять его можно только, если режим течения газа по длине трубопровода не изменяется.
Метод калиброванной диафрагмы применяют для измерений в молекулярном режиме. Здесь газ проходит через диафрагму, пропускная способность которой известна, и измеряется перепад давлений по обеим сторонам диафрагмы.
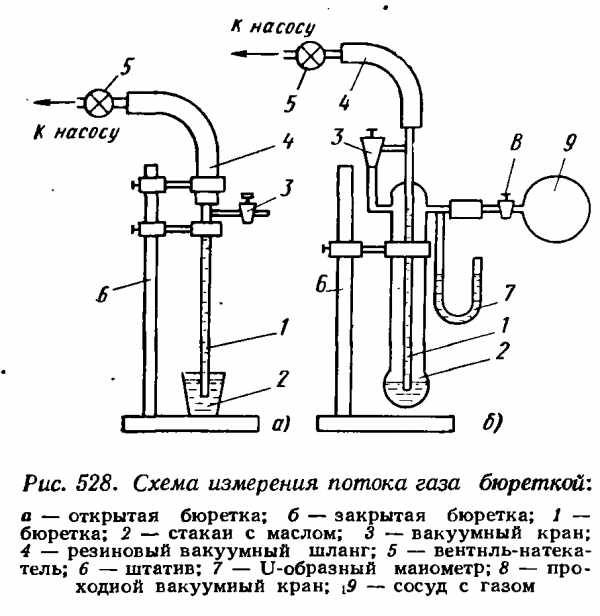
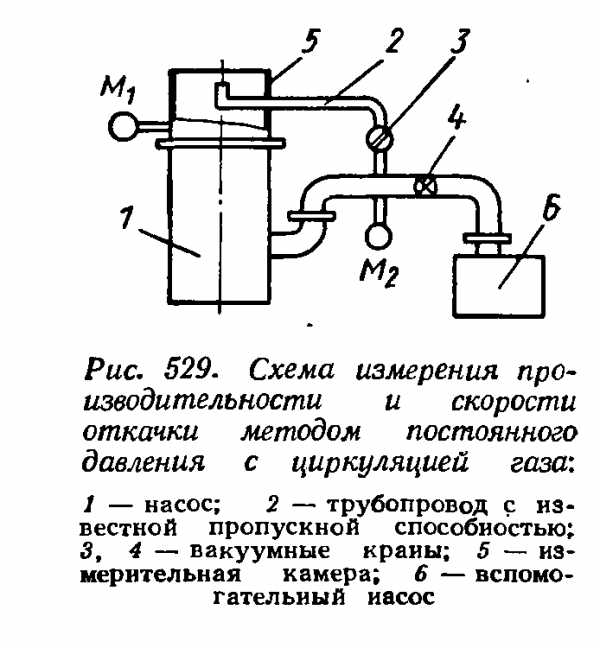
Чтобы измерить скорость откачки насоса методом сравнения, в сосуд впускают газ и создают поток Q.
После того как в результате одновременной откачки сосуда насосом и напуска потока газа Q (непрерывного) в сосуде установится давление ри к нему подключают еще один насос, скорость откачки которого известна. При параллельной работе двух насосов и том же потоке газа Q установится новое значение давления. При этом нужно,чтобы соблюдалось условие
так как в противном случае нельзя точно измерить понижение давления в сосуде.
Тогда пренебрегаем давлением р0 и записываем
Из этого уравнения можно исключить неизвестный поток Q; решая его относительно S, получим
где S1 — известная скорость откачки вспомогательного насоса.
Этим методом удобно пользоваться, если имеется калиброванный насос с известной скоростью откачки. При постоянном потоке Q можно быстро проводить измерения, особенно если отношение — записывается с помощью специального прибора.
Недостаток этого метода в том, что рабочие давления должны значительно превышать предельное давление р0, a S1 должно быть по меньшей мере одного порядка с искомой скоростью откачки S.
www.pro-vacuum.ru
Способ контроля вакуумирования жидкой стали
Сущность изобретения: способ заключается в том, что в процессе вакуумирования измеряют разность температур между входом и выходом газоохладителя, находят отношение расхода тепла охлаждающей воды к измеренному перепаду температуры газа и дегазацию прекращают при достижении этим отношением величины 2-20 Вт/°С. 2 ил.
СОЮЗ СОВЕТСКИХ
СОЦИАЛИСТИЧЕСКИХ
РЕСПУБЛИК (51)5 С 21 С 7/10
ГОСУДАРСТВЕННЫЙ КОМИТЕТ
ПО ИЗОБРЕТЕНИЯМ И ОТКРЫТИЯМ
ПРИ ГКНТ СССР
ОПИСАНИЕ ИЗОБРЕТЕНИЯ
К АВТОРСКОМУ СВИДЕТЕЛЬСТВУ
Qe= /гСг Pr (тг 1г ) 17, (21) 4752232/02 (22) 25,09.89 (46) 23.07.92. Бюл. N. 27 (71) Всесоюзный научно-исследовательский институт металлургической теплотехники (72) В.И,Половников, А,B.Ïðoòàñoâ и B,È.Ðåøåòîâ (56) Заявка Японии N 59-116315, кл. С 21 С 7/10, С 21 С 5/00, опублик. 1982, Заявка ФРГ ¹ 3706742, кл, С 21 С 7/10, С 21 С 5/30, опублик. 1987.
Изобретение относится к металлургии, а именно к способам контроля вакуумной дегазации жидкой стали.
Известны способы контроля, в которых продолжительность дегазации определяют посредством химанализа расплава и отходяших газов.
Недостатком указанных способов является повышенная инерционность, приводящая к затягиванию процесса вакуумной обработки и ухудшению технико-экономических показателей плавки, Известен способ контроля технологического процесса, включающий измерение расхода тепла, воспринимаемого охлаждающей водой и определение длительности процесса по величине измеренного расхода, Способ недостаточно точен для контроля вакуумирования стали, что связано с зависимостью тепловосприятия воды в гаэоохладителе не только от расхода отходящего газа, но и от условий теплопередачи.
При одинаковом расходе газа возможно различное тепловосприятие воды, что при, î9> 5U
2 ил, водит к ошибочному определению момента окончания вакуумирования.
Целью изобретения является повышение точности контроля вакуумирования жидкой стали.
Поставленная цель достигается тем, что согласно способу контроля, включающему определение расхода тепла охлаждающей воды в газоохладителе, в процессе вакуумирования дополнительно измеряют разность температур между входом и выходом газоохладителя, находят отношение расхода тепла охлаждающей воды к измеренному перепаду температуры газа и дегазацию прекращают при достижении этим отношением величины 2 — 20 Вт/ С.
Физическое обоснование способа заключается в следующем, Из теплового баланса газоохладителя; где Qe — расхода тепла, воспринимаемого охлаждающей водой, Вт;
Vr — расход отходящего газа (скорость газовыделений), HM /с:
1749248 де
С, — удельная теплоемкость газа, Дж/кг С; р- плотность газа, кг/нм; з, tr lr — температура газа на входе и выходе газоохладителя, С; 5
r — коэффициент теплопотерь в окружающую среду.
Выражение (1) можно представить в ви10
Ч; — а, „, (2) т, — т, где а=1/р, С,, мз C/Äæ.
Следовательно, зная отношение тепловосприятия воды к разности температуры газа и установив а, можно определять скорость газовыделений при вакуумировании.
Прекращение дегазации производится при отсутствии окиси углерода в отходящем га- 20 зе, В атом случае газ содержит практически один аргон, подаваемый на ингенсификацию процесса. Для аргона в рассматриваемой области температур: С =519 Дж/кг С, p= 1,78 кг/нмз, g = 0,95 а = 1,14 10 м С/Дж, Расход аргона при вакуумировании: 0,15…1,4 м /мин. Этому диапазону соответствуют значения (4/(т — tr )=2 — 20 Вт/ С.
На фиг, 1 приведена схема реализации изобретения, на фиг. 2 — график изменения скорости газовыделений и величины отно-, шения тепловосприятия воды к температурному перепаду газа в течение ва куумирования.
Схема (фиг. 1) содержит рабочую камеру вакууматора 1, соединенную вакуумпроводом 2 с газоохладителем 3. На линии подачи и отвода воды из газоохладителя 3 установлены датчик 4 расхода и два датчика 5 температуры. В вакуумпроводе 2 на входе и выходе газа из газоохладителя 3 установлены датчики 6 температуры, Устройства 4 — 6 подключены к измерительному блоку 7, снабженному сигнализатором 8.
В процессе вакуумирования отходящий из камеры 1 газ отводится по вакуумпроводу 2 через газоохладитель 3. Сигналы от датчиков 4 — 6 непрерывно поступают в блок
7, который содержит теплосчетчик воды и делительное устройство, Теплосчетчик фиксирует расход тепла, воспринимаемого охлаждающей водой в газоохладителе 3, а делительное устройство производит опре4 деление отношения тепловосприятия воды к перепаду температуры газа. При достижении заданного значения этого-отношейия срабатывает сигнализатор 8 и вакуумирование прекращается.
Пример. Вакуумирование стали производится в агрегате ВП-130 ЧМК. Расход аргона для технологических целей 0,15…1,4 м /мин, Температура газа на выходе из раз бочей камеры =1600 С, на входе B газоохладитель 850 — 1100 С. Площадь пове2охности теплообмена газоохладителя
56 м, Расход воды 11,4 кг/с. Перепад температуры воды 1 — 15 С. Отношение тепловосприятия воды к перепаду температуры газа пропорционально расходу газа, При достижении указанного отношения величины от 2 Вт/ С при расходе аргона О, 15 м /мин до 20 Вт/ С при 1,4 м /мин дегазация прекращается. По сравнению с известным предлагаемый способ позволяет на 10-12/ (2 мин) повысить точность определения времени завершения вакуумирования.
Аппаратурное обеспечение изобретения не вызывает затруднений. Расход тепла с охлаждающей водой измеряется водяным теплосчетчиком, например ТС-20, в комплект которого входят датчик 4 расхода воды и термометры 5 сопротивления. Температура газа фиксируется с помощью хромельалюмелевых термопар и вторичного прибора типа КСП.
Таким образом, изобретение обеспечивает повышение точности контроля за счет дополнительного измерения разности температуры газа между входом и выходом газоохладителя. Кроме того, способ прост в осуществлении и не требует значительных материальных затрат, так как используется оборудование (газоохладитель), являющееся частью технологического агрегата.
Формула изобретения
Способ контроля вакуумирования жидкой стали, включающий определение расхода тепла, воспринимаемого охлаждающей водой в газоохладителе, о т л и ч а ю щ и йс я тем, что, с целью повышения точности, в процессе вакуумирования дополнительно измеряют разность температур между входом и выходом газоохладителя, находят отношение расхода тепла охлаждающей воды к измеренному перепаду температуры газа и дегазацию прекращают при достижении этим отношением величины 2 — 20 Вт/ С.
1749248 дода юг. 1
550
ФУ5 до
220
Редактор Н.Рогулич
Заказ 2564 Тираж Подписное
ВНИИПИ Государственного комитета по изобретениям и открытиям при ГКНТ СССР
113035, Москва, Ж-35, Раушская наб., 4/5
Производственно-издательский комбинат “Патент”, г. Ужгород, ул.Гагарина, 101
22
В
Я с» Я ю ь
8 б ч
2 с 4 Ю 8 0 12 f4 1о 1Â 20 2с
В,оЕлгя, èåå
Составитель B,Ïîëîâíèêîâ
Техред M.Ìîðãåíòàë Корректор Т,Палий
www.findpatent.ru
Вакуумный метод
Этот метод является, по существу, разновидностью пневматического метода контроля с обмазкой пенообразующим веществом. Его применяют для контроля герметичности открытых изделий при одностороннем доступе к контролируемой поверхности.
При испытании на исследуемый участок изделия 6 накладывают переносные вакуумные камеры, состоящие из рамки 4 с резиновыми уплотнителями 5. На контролируемое изделие наносят пенообразующее вещество. Вакуумную камеру устанавливают на изделие и с помощью вакуумного насоса создают в ее полости разрежение (обычно 0,02…0,09 МПа). В результате разрежения воздух через неплотности в изделии поступает в полость камеры. Наблюдение за появлением пузырьков в пенообразующем веществе 7 ведут через прозрачное смотровое окно камеры 3.
Схема контроля герметичности сварных соединений вакуумным методом
Давление в камере контролируют вакуумметром 1. При испытаниях применяют форвакуумные механические насосы. По окончании контроля трехходовым краном 2 в полость камеры напускают атмосферный воздух и перемещают ее на следующий контролируемый участок.
Широкое распространение вакуумный метод получил при контроле сварных соединений. В зависимости от конфигурации сварных изделии и видов сварных соединений применяют плоские, угловые и кольцевые вакуумные камеры. Чувствительность такого метода контроля достигает 10-2 мм3 · МПа/с.
Иногда контроль изделий осуществляют способом бароаквариума с использованием накладных вакуумных камер. Камеру устанавливают на изделии и вакуумным насосом создают в ней требуемое разрежение, после чего в ее внутреннюю полость подают контрольную жидкость (воду). Пузырьки газа в местах течей наблюдают через смотровое окно. Такой способ контроля по сравнению с обычными вакуумными испытаниями обеспечивает большую стабильность регистрации течей, поскольку пузырьки воздуха наблюдаются устойчиво в течение длительного времени.
Пузырьковые методы контроля герметичности имеют широкое распространение благодаря простоте, наглядности, возможности осмотра одновременно всей поверхности объекта, малой стоимости материалов и оснастки. К их недостаткам относятся субъективность оценки, большая трудоемкость и длительность испытания, а также сравнительно низкая чувствительность.
ndt-testing.ru