Засор капиллярной трубки холодильника признаки: Как устранять засор капиллярной трубки холодильника?
Статьи по ремонту холодильников LIEBHERR (Либхер)
Тонкая капиллярная трубка, по которой циркулирует хладагент, считается одной из самых уязвимых частей холодильной камеры. Из-за небольшого внутреннего пространства, не превышающего 1,5-2 мм, попадание в нее мелких посторонних частиц может осложнить проход фреона или полностью перекрыть его. Результат – серьезная неисправность, связанная с нерабочим состоянием холодильной или морозильной камеры. Специалистам, выполняющим ремонт холодильников Liebherr, приходится часто сталкиваться с подобным дефектом. Поэтому процедура его устранения хорошо известна и отработана до мелочей.
Причины засорения капиллярной трубки
Обычно засорение капиллярной трубки вызывает попадание внутрь мелких частиц силикона, капель масла или взвесей из компрессора. Обладая достаточно плотной и вяжущей структурой, они легко оседают на внутренние стенки, постепенно увеличиваясь в размерах за счет частиц пыли или других загрязнений. Закупоренная трубка перестает пропускать фреон в полном объеме, что немедленно сказывается на рабочих показателях холодильной камеры. Температура внутри устройства становится выше, и обеспечить сохранность продуктов не удается.
Основная причина попадания мелких взвесей в полость капиллярной трубы – засор или выход из строя фильтра-осушителя. В его основные «обязанности» входит задержка посторонних частиц на входе в трубопровод для хладагента. Поэтому устранение проблемы засора всегда связано с осмотром и заменой неисправного фильтра, что позволяет свести к нулю риск повторного возникновения неисправности.
Справиться с дефектом самостоятельно владельцу техники не удастся, даже если он обладает неплохими познаниями в области строения холодильных установок. Кроме того, неквалифицированное вмешательство может вызвать появление еще более серьезного дефекта, который поставит под сомнение возможность дальнейшей эксплуатации холодильника. Поэтому при обнаружении первых признаков неисправности стоит немедленно пригласить специалиста для диагностики и ремонтных работ.
Симптомы засорения капиллярной трубки холодильника
В числе основных признаков неисправности стоит отметить:
- Ощутимое снижение производительности холодильной камеры, когда температура внутри практически не отличается от температуры окружающего воздуха;
- Чрезмерное нагревание компрессора и других рабочих элементов холодильника. Это может быть вызвано интенсивной работой техники, пытающейся справиться с возникшей неисправностью и компенсировать эффект повышения температуры.
Перечисленные признаки стоит отличать от симптомов других типов поломок, например, выхода из строя фильтра или утечки фреона. Единственно правильное решение – провести тщательную диагностику с использованием специального измерительного оборудования и инструментов. Если предварительное мнение о причинах поломки подтверждено, специалист подбирает тактику дальнейших действий по устранению дефекта.
Способы очистки капиллярных трубок
Имея в своем распоряжении запас фреона и полный комплект инструментов, мастер может выбрать оптимальный способ прочистки труб от засора с учетом технического состояния, срока эксплуатации и конструктивных особенностей холодильного оборудования.
Сравнительно простым методом считается обрезка трубы в предположительном месте ее засорения и установка на ее место нового фрагмента тех же размеров. Сделать это можно в течение нескольких минут. Однако зачастую бывает сложно предугадать, в каком именно месте произошел засор, поэтому обрезка трубки на небольшое расстояние может оказаться неэффективной и не поможет в решении проблемы.
Второй вариант – механическая прочистка трубки с применением растворителя. Для этого элемент обрезается на всю длину и подключается к компрессору через медную трубку и резиновый шланг, внутрь которого заблаговременно вводят растворитель в объеме приблизительно 10 куб. см. После включения мотора компрессора жидкость под давлением до 25 атмосфер подается в трубку, прочищая внутренний диаметр. Если с первого раза сделать это не удалось, процедуру повторяют до 5-10 раз, что гарантирует прочистку трубки и ее пригодность для дальнейшей эксплуатации.
Третий вариант устранения дефекта подразумевает устранение засоров с помощью специального пресса. Технически данный способ практически идентичен второму варианту, позволяя добиться результата за несколько циклов очистки.
Если справиться с проблемой не удалось, специалист может предположить, что образовавшийся засор имеет крупные размеры и пластичную структуру, за счет которой посторонние включения надежно удерживаются на внутренних стенках трубки. В этом случае принимается решение о ее полной замене новым элементом, имеющим такой же диаметр и пропускную способность. Таким образом удается полностью устранить дефект и обеспечить безотказную работу капилляра на несколько лет.
Возможные сложности при очистке капиллярной трубки
Любые работы, связанные с прочисткой капиллярной трубки, требуют времени и определенных усилий. Это связано с небольшим диаметром детали и возможной плотностью загрязнения, полное удаление которого механическим способом возможно лишь после нескольких попыток. Кроме того, обязательным условием проведения ремонтных работ является замена фильтра-осушителя. Если в ходе работ обнаруживается неисправность других комплектующих, их также необходимо привести в исправное состояние или заменить. Однако при условии обращения к опытным мастерам справиться с проблемой можно будет за несколько часов без необходимости отправки оборудования в сервисную мастерскую.
Поскольку прочистка капилляра связана с остановкой циркуляции фреона, после завершения работ и герметизации контура необходимо повторно заполнить систему определенным количеством газа. Для этого из нее вакуумным насосом выкачивается воздух, после чего на его место закачивается хладагент.
Доверив ремонт холодильника профессионалам, вы сохраните право на гарантийное обслуживание техники и сможете быть уверены в ее работоспособности в течение последующих нескольких лет.
капиллярный трубопровод
Устранение засора капиллярного трубопровода холодильника
это одна из услуг, которые по приемлемой цене оказывает
сервис по ремонту холодильников Доктор холод
заказчикам в Тольятти.
При оформлении заказа гарантированы:
- Выполнение работы квалифицированным специалистом
- Использование оригинальных запчастей
- Выезд на место в удобное для заказчика время
- Вызов мастера по ремонту холодильников в Тольятти и
- диагностика бесплатно
- Ремонт холодильников в районах Тольятти :
- Автозаводский, Центральный, Комсомольский
- Гарантия на ремонт холодильника до 12 месяцев
- Срочное устранение засора капиллярного трубопровода в день звонка
- Недорогой ремонт холодильников по приемлемой цене
- Бесплатная консультация по телефону.,
- ответим на ваши вопросы по ремонту холодильников
- Удобный график работы,
- ремонт холодильников без праздников и выходных
- Мобильная мастерская по ремонту холодильников
- Устранение засора капилляра холодильника на дому
- Профессиональное оборудование для ремонта холодильника
- Работа со всеми типами фреонов

Однако с середины 90-х годов, когда началось активное продвижение на рынок новых конструкций компрессоров с повышенным допуском нагрева и новыми марками масел, появилась холодильная техника, предназначенная для работы с хладагентом R134a.
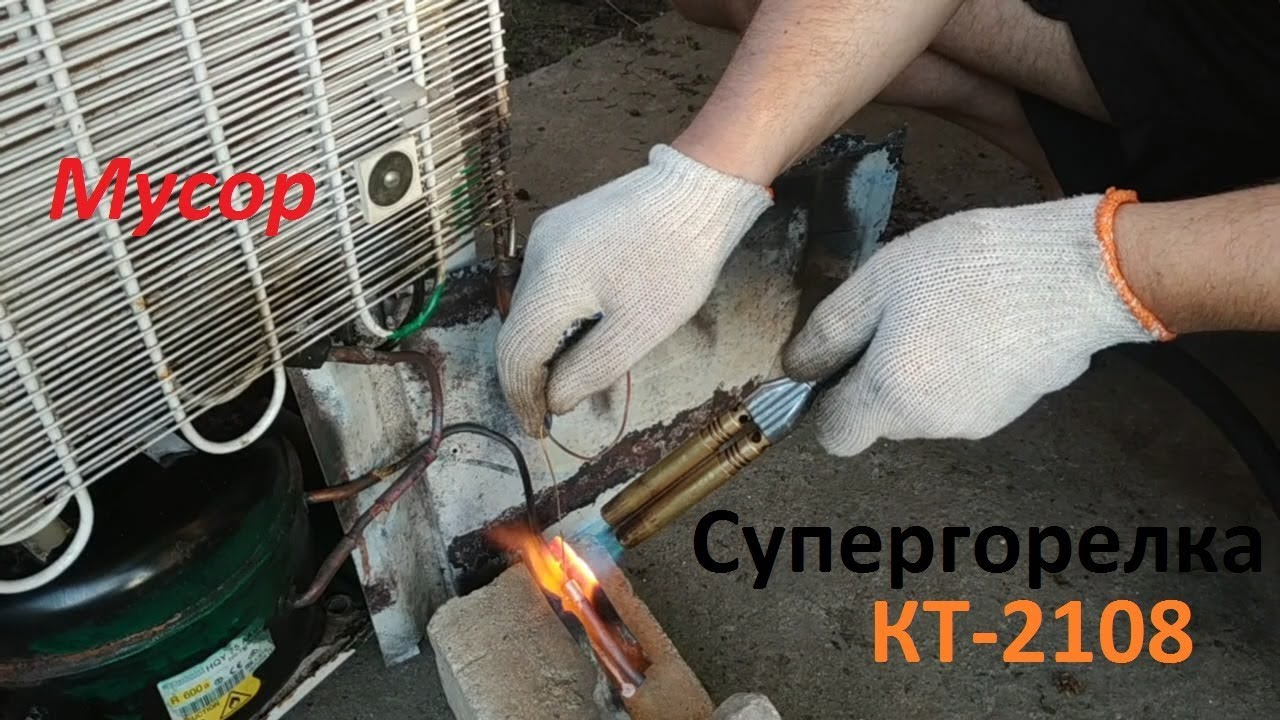

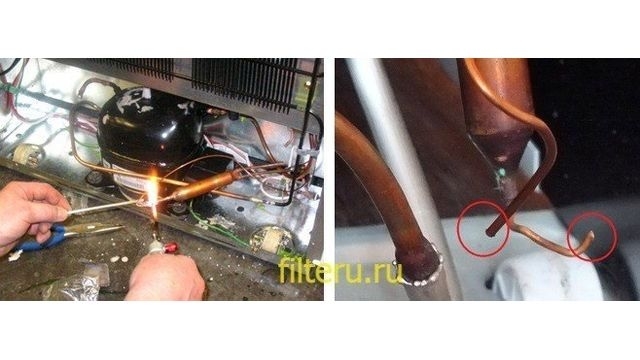
Основные причины засоров, возникающие в капиллярных трубках
Сама природа проявления засоров в КТ может иметь несколько причин. Перечислим некоторые из них:
1 Сужение геометрии внутреннего диаметра трубы как в продольном, так и поперечном сечениях.
В этом случае перед появившейся складкой (заусенцем) возможно скопление небольшого количества механической взвеси, она пропитывается вязкими составляющими масла и затем уплотняется. Как вариант, возможно простое смерзание частиц (если расположение засора находится вблизи от впрыска в испаритель). За выступающие из массы бесформенные кусочки цепляются новые соринки, и процесс идет по нарастающей. Такого рода засор тяжело продавить по ходу газа, так как впереди засора будет находиться именно сужение трубы, и подобная “пробка” будет только уплотняться. В последнее время подобное явление встречается из-за “закуса” (сужение при отрезе) кончика трубы на впрыске в испаритель при обрезании КТ изготовителем, без дальнейшей обработки торца трубы.
2 Расширение геометрии внутреннего диаметра трубы как в продольном так и поперечном сечении.
В этом случае появляется своеобразный “карман”, где могут осесть при остановке движения среды относительно крупные частицы, а их выступающие кромки послужат своеобразной гребенкой для улавливания из среды других механических включений. Такого рода засор тяжело продавить в любом направлении, предпочтительнее пропитать засор моющим раствором и промывать трубу до полного удаления следов засора.
3 Появление в системе липких компонентов, например, за счет парафинизации или других эффектов разложения среды.
Выделившиеся парафины или другие компоненты, свободно циркулирующие по системе за счет миграции масла, оседают внутри полости КТ за счет резкого охлаждения у входа в испаритель (на расстоянии 20. ..30 см от него). Для устранения подобной пробки бывает достаточно слегка прогреть этот участок при включенном компрессоре, чтобы разность давлений при работе агрегата выдавила размягченную нагревом массу по направлению в испаритель. Состав подобных засоров условно можно классифицировать по нескольким признакам.
1 Порошок темного или серого цвета.
По разным оценкам, подобный порошок может появляться от разрушения гранул осушителя или взаимодействия материалов в системе циркуляции хладагента. Чаще всего удаляется применением пропитки засора моющим раствором с последующим чередованием плавного приложения давления с обеих сторон КТ.
2 Густая темная пластичная масса (чаще – коричневого цвета), близкая по вязкости к пластилину.
Данная масса создает наибольшие проблемы при устранении засора КТ, так как достаточно легко сминается и уплотняется в процессе попытки устранения дефекта. Похоже, что она появляется вследствие коррозии черных металлов деталей внутри системы. Если удается пропитать пробку из этой массы моющим раствором для уменьшения вязкости, “продавливают” данный засор повышенным давлением в направлении, обратному нормальному движению хладагента.
3 Хлопья темного цвета – мелкие, бесформенные или иглообразные.
Засор КТ из подобных хлопьев легко устраняется пропиткой моющим раствором с последующей продувкой избыточным давлением в направлении, обратном нормальному движению хладагента. Подобные твердые включения напоминают обычный технологический мусор (возможно, продукты износа деталей), а мягкие – более схожи с продуктами лакокрасочных материалов (в одном из источников упоминалось применение в заводских условиях специальной краски для нанесения рисунков каналов) или отходы разрушения пластиковых деталей, входящих в состав мотор-компрессора.
4 Темная масса, напоминающая по консистенции гель.
Удаление засоров из этой массы не представляет затруднений при мягком и продолжительном приложении давления с любой стороны КТ. Вероятный источник появления подобного засора – разрушение продуктов среды (парафинизация масла, химическая реакция хладагента) или взаимодействия их составляющих с деталями агрегата.
Способы устранения засоров в КТ.
Заводские технологии устранения засоров немногочисленны. Перечислим их:
1 Применение для пропитки и промывки специализированных растворов, например “жидкого осушителя”.
Как утверждается, состав данных растворов не оказывает разрушительного действия на детали в составе системы циркуляции хладагента. Хочется отметить, что использование для подобных целей метанола неприменимо в связи с его высокой агрессией к материалу испарителя – алюминию.
2 Продувка системы сжатым осушенным азотом.
Азот можно подавать из баллона через редуктор в любом направлении, важно только помнить, что капиллярная трубка способна выдержать большие значения давления, чем каналы алюминиевого испарителя. Причем давление на стенки трубы будет пропорционально выше с увеличением внутреннего диаметра трубы. В этом случае играют большую роль и применяемые материалы. При подаче избыточного давления в КТ необходимо предусмотреть, чтобы в системе обязательно был раскрытый заправочный патрубок. Это необходимо для того, чтобы обеспечить сброс избыточного давления в случае прорыва газа через засор КТ в полость испарителя. При подаче давления в направлении против нормального движения хладагента (то есть через обратную трубу испарителя) важно помнить, что вначале давление воздействует на внутреннюю полость алюминиевого испарителя, а затем прикладывается к КТ.
3 Воздействие на засор масла под высоким давлением с помощью специальных гидравлических прессов.
Внешне подобные прессы напоминают обычные домкраты для легковых автомобилей. Но в отличие от последних, они оснащены удобным захватом для КТ и манометром высокого давления(до 400.600 кгс/см2). При использовании данного метода важно не сделать одну характерную для ремонтников ошибку – при продавливании засора КТ в системе для хладагента R-134а нельзя применять минеральное масло. И вообще, для прочистки КТ желательно применять такое же масло, которое заправлено в компрессор. Отметим, что внутри пресса имеется специальный предохранительный клапан, сбрасывающий давление при достижении определенной (критической) величины.
4 Замена КТ на новую.
Подобная методика в большинстве своем доступна только сервисным партнерам производителей. В технологических картах, предоставляемых производителями, указаны даже параметры КТ в зависимости от модели холодильника. Если в съемных испарителях эта операция достаточно технологична, то в современных полу-разборных конструкциях она весьма трудоемка, так как в некоторых конструкциях необходимо вначале удалять теплоизоляцию, а после производства работ восстанавливать удаленное покрытие. В этом случае, не зная точно параметров применяемой КТ, можно получить непредсказуемые результаты.
Основные требования к материалам, применяемым для устранения засоров КТ.
Рассмотрим основные требования и возможности применения материалов, используемых для устранения засоров КТ.
1 Осушенные нейтральные газы.
Их применение наиболее оптимально, но есть и ограничения. Например, использование подобных газов неэффективно при устранении “сухих” или непластичных по составу засоров большой протяженности – слишком велико сопротивление пробки засора при движении по трубкам. Помимо азота в разных источниках описывались попытки устранения засоров пропаном (хороший растворитель парафинов). Используемая для этих целей пропанбутановая смесь из бытовых отопительных баллонов технической чистоты имеет большие допуски по наличию влаги и примесей, поэтому подобное решение чревато отрицательными последствиями. К тому же подобная газовая смесь огнеопасна, а в случае удаления ее из системы необходимо предпринимать известные меры по обеспечению пожарной безопасности данной операции.
2 Применение холодильных масел при продавливании прессом.
За счет высокого давления масло может попасть в полость испарителя. Использовать минеральное масло нельзя, если система предназначена для хладагента R-134а – неизвестно как поведет себя смесь из “родного” компрессорного масла и масла, примененного при процессе. Поэтому на этот аспект нужно обратить особое внимание.
3 Жидкие легкоиспаряющиеся растворы (растворители).
Подобные вещества легко проникают в толщу засора, снижают вязкость “пробки”, легко удаляются из системы вакуумированием с продувкой. К таким можно отнести ацетон и, возможно, растворители типа 646 и им подобные. Однако ацетона класса ХЧДА (химически чистый для анализа) в открытой продаже недоступен. “Бытовой” ацетон для удаления засоров использовать проблематично, так как в его составе может быть вода.
Отдельно хочется предупредить о возможных негативных последствиях при применении для рассматриваемых целей дихлорэтана. Это вещество является хорошим растворителем пластмасс, поэтому при его использовании существует большой риск повреждения пластиковых деталей бандажа компрессора. В свою очередь, продукты разложения могут стать впоследствии основой для появления новых засоров. Кроме того, применение дихлорэтана может отрицательно сказаться на электрической прочности изоляции электродвигателя компрессора. Возможно, неплохой альтернативой могут послужить фреоны 113, 114, применяющиеся в промышленности, как обезжиривающие жидкости. Если учесть, что расход их невелик, то высокая цена не сильно повлияет на цену ремонта.
4 Жидкие нефтепродукты – керосин, солярка (применяют в прессах как рабочее тело), бензин для зажигалок.
Первые два вещества достаточно эффективны в прессах. Но они плохо испаряются, еще хуже удаляются из испарителя продувкой. Класс чистоты этих веществ может быть технический. Они имеют свойство густеть/замерзать при низкой температуре. Необходимо учесть, что эти вещества могут дать неожиданные результаты (не всегда с положительным выходом) в смеси с нефтяными маслами.
Технологические приемы по устранению засоров КТ.
При проведении операций по устранению засоров КТ важно понять суть процесса, в противном случае, например, попытки излишне ускорить процесс могут привести к уплотнению массы “пробки”, что значительно усложнит устранение дефекта.
Пропитка.
Применение этого приема рассчитано на свойстве засора менять свою подвижность и пластичность в результате впитывания раствора для пропитки. Наиболее мелкие, пластичные и максимально подвижные частицы могут пройти при этом сквозь всю толщу “пробки”, что позволит промыть и расширить имеющиеся каналы для прохода более крупных частиц. В свою очередь это увеличивает площадь соприкосновения препарата с оставшейся массой, что резко повышает качество пропитки наиболее удаленных от внешней поверхности слоев.
Пропитку проще всего выполнить следующим образом:
– в обычный одноразовый шприц набирают небольшое количество раствора, сам шприц одевают на КТ, и вывешивают штоком вниз;
– через заправочный патрубок создают примерно половину возможного вакуума, чтобы раствор из шприца не слишком быстро двигался в проходе капилляра;
– если раствор из шприца не впитывается, оставляют на месте шприц, разрежение (вакуум) доводят до максимально возможного уровня;
– оставляют все в подобном состоянии на несколько часов (возможно, до 24 часов), периодически контролируя уровень раствора в колбе шприца.
Вскоре после всасывания раствора в КТ систему герметизируют резиновыми патрубками от компрессоров. В этом случае раствор должен будет остановиться в капилляре, тем самым будут созданы условия для проникновения его, в том числе, в участки возможного “частичного засора”. Этот прием наиболее удобен с точки зрения учета использования раствора – не из экономии, а для ограничения его количества при попадании в систему. Если раствор для пропитки всасывается из полости шприца крайне медленно или не убывает совсем, можно применить следующий способ:
– на конец КТ припаивают трубку большего диаметра длиной 150-200 мм. Ее располагают открытым концом вверх, туда и заливается нужное количество раствора, одевается муфта, постепенно на этом входе увеличивают давление;
– через заправочный патрубок создают разрежение, туда для контроля давления подключают чувствительный манометр. Если давление на линии всасывания начинает подниматься – можно сделать вывод, что жидкость просачивается в полость разрежения. Практика показала – если раствору удалось “пройтись” по полости КТ, то шансы устранения засора максимальны. После определенной выдержки, чтобы засор максимально оказался пропитан раствором, можно приступать непосредственно к продавливанию.
Продавливание.
Вариантов реализации этого приема много. Дальнейшие действия могут иметь различное развитие, в первую очередь это связано с уверенностью в качестве прогнозирования состояния засора, с опытом исполнителя, а также с наличием необходимого инструмента. Но самое главное, нельзя провоцировать появление резких движений массы засора (вследствие этого возможно появление новых уплотнений). Лучше плавно увеличивать давление газа (в направлении против нормального хода хладагента в системе) – чаще всего в “голове” засора имеется какое-то сужение прохода. Но важно помнить, что нельзя прилагать чрезмерное избыточное давление в трубках испарителя, оно имеет свои пределы (у разных производителей заявленная прочность на разрушение избыточным давлением лежит в пределах 8. 15 Бар). Поэтому превышать давление выше 10 Бар не рекомендуется. Давление можно создавать как “родным” для системы фреоном, так и сжатым азотом. Нужно учитывать, что использование для подобных целей других типов фреонов нужно соотносить с их совместимостью с маслом, уже залитым в систему. В это же самое время можно со стороны КТ создать разрежение. Спустя небольшой промежуток времени (определяется опытным путем), точки приложения разрежения и избыточного давления можно поменять местами. Чаще всего после нескольких подобных попыток “расшатать” пробку, засор успешно удаляется. В тяжелых случаях “продавливают” засор в КТ с помощью специализированного пресса, способного создать избыточное давление в десятки и сотни атмосфер. Иногда “продавливание” засора можно выполнить другим способом – если обычное “расшатывание” пробки изменением вектора приложения давления не помогает, меняют фильтр-осушитель, и пробуют произвести штатную заправку. В этом случае заправку выполняют небольшими дозами с интервалами в 10.
15 минут. Часто нужный эффект достигается уже через 2.3 часа.
Окончательная промывка КТ от следов загрязнений.
Чаще всего, вследствие успешного “продавливания” засоров, резкий прорыв газа / масла прочищает основной проход трубки, но на ее стенках могут еще оставаться значительные следы загрязнений, и нужно еще некоторое время для полного освобождения прохода. Иначе это в дальнейшем станет причиной для повторения дефекта. Затем прогревается испаритель до температуры +40.50°С для улучшения испарения агента, применяемого в процессе “продавливания” засора. Если применялось масло, то его лучше попытаться удалить через КТ продувкой газом в направлении против нормального движения хладагента. Следующим этапом выполняют стандартное вакуумирование, после чего заправляют систему половиной “ремонтной” дозы хладагента и включают аппарат на прогон. Заправка малой дозой хладагента активирует процесс, при котором в КТ будет циркулировать не жидкость, а парожидкостная смесь – при движении она создаст эффект, близкий к “кавитации” (т.
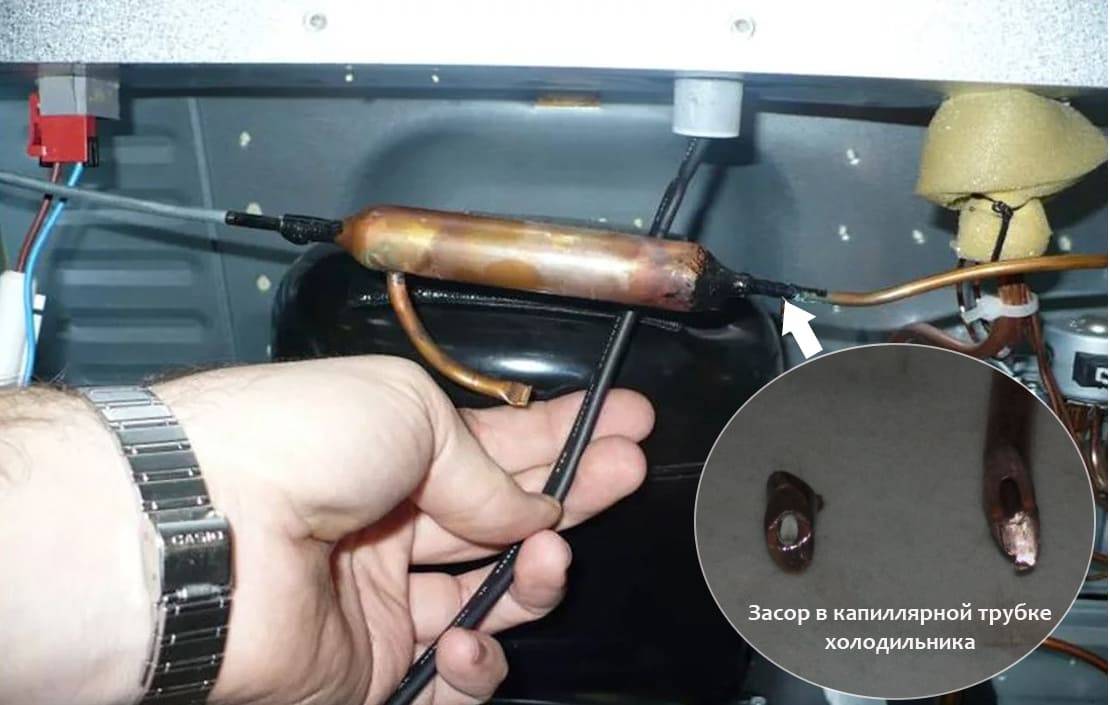
Капиллярная трубка
в сборе с всасывающей трубкой служит регулирующим устройством для подачи жидкого хладагента в испаритель. Она представляет собой медную трубку с внутренним диаметром 0,6…0,8 мм и длинной 2800…8500 мм, соединяющей стороны высокого и низкого давления в системе холодильного агрегата
нормы заправки холодильников
1 2 3 4 5 6 7 8 9 10
источник
Способ устранения неисправности системы охлаждения
Новости
Система охлаждения — общий термин для оборудования и трубопроводов, по которым протекает хладагент, включая компрессоры, конденсаторы, дросселирующие устройства, испарители, трубопроводы и вспомогательное оборудование. Это основной компонент системы оборудования для кондиционирования воздуха, холодильного и холодильного оборудования.
В системе охлаждения существуют различные виды неисправностей, связанных с засорением, например, засорение льдом, засорение грязью и засорение маслом. На байпасном заправочном клапане индикация отрицательного давления, звук работы наружного блока слабый, а жидкость, протекающая через испаритель, отсутствует.
Причины и симптомы закупорки льдом
Неисправности, связанные с забиванием льдом, в основном вызваны избыточной влажностью в системе охлаждения. При непрерывной циркуляции хладагента влага в холодильной системе постепенно концентрируется на выходе из капилляра. Поскольку температура на выходе из капилляра самая низкая, вода замерзает и постепенно повышается, до определенной степени капилляр будет полностью заблокирован, хладагент не сможет циркулировать, и холодильник не будет охлаждаться.
Основным источником влаги в системе охлаждения является: изоляционная бумага двигателя в компрессоре содержит влагу, которая является основным источником влаги в системе. Кроме того, компоненты и соединительные трубы холодильной системы имеют остаточную влажность из-за недостаточной сушки; масло холодильника и хладагент содержат влагу, превышающую допустимое количество; Поглощается изоляционной бумагой двигателя и холодильным маслом. По вышеперечисленным причинам содержание воды в системе охлаждения превышает допустимое количество системы охлаждения, и происходит закупорка льдом. С одной стороны, засорение льдом приведет к нарушению циркуляции хладагента, и холодильник не сможет нормально охлаждаться; с другой стороны, вода вступит в химическую реакцию с хладагентом с образованием соляной кислоты и фтористого водорода, что вызовет коррозию металлических труб и компонентов и даже приведет к повреждению обмоток двигателя. Изоляция повреждена, и в то же время это приведет к ухудшению качества холодильного масла и повлияет на смазку компрессора. Поэтому влажность в системе должна быть сведена к минимуму.
Признаки засорения льдом системы охлаждения заключаются в том, что на начальном этапе она работает нормально, в испарителе образуется иней, конденсатор рассеивает тепло, агрегат работает ровно, звук работы хладагента в испарителе четкий и стабильный . При образовании ледяного завала слышно постепенное ослабление и прерывистость воздушного потока. При серьезной закупорке звук воздушного потока исчезает, цикл хладагента прерывается, и конденсатор постепенно остывает. Из-за блокировки повышается давление выхлопа, усиливается звук машины, в испаритель не поступает хладагент, площадь обледенения постепенно уменьшается, а температура постепенно повышается. При этом вместе с этим повышается и капиллярная температура, поэтому кубики льда начинают таять. Хладагент снова начинает циркулировать. Через некоторое время блокировка льдом будет повторяться, образуя периодическое явление проходной блокировки.
Причины и симптомы грязного засорения
Грязные неисправности блокировки вызваны чрезмерными загрязнениями в системе охлаждения. Основными источниками примесей в системе являются: пыль и металлическая стружка при изготовлении холодильников, оксидный слой на внутренней стенке труб при сварке, не очищенная при обработке внутренняя и внешняя поверхности деталей, трубы не герметичны. В трубе есть примеси в холодильном масле и хладагенте, а в осушительном фильтре – порошок-влагопоглотитель низкого качества. Большая часть этих примесей и порошков удаляется фильтром-осушителем, когда они проходят через фильтр-осушитель, а когда в фильтре-осушителе больше примесей, некоторые мелкие загрязнения и примеси попадают в капиллярную трубку хладагентом с более высокой скоростью потока. Части с более высоким сопротивлением накапливаются и накапливаются, а сопротивление увеличивается, что облегчает загрязняющим веществам оставаться до тех пор, пока капилляр не заблокируется и система охлаждения не сможет циркулировать. Кроме того, если расстояние между капилляром и сетчатым фильтром в сухом фильтре слишком мало, легко вызвать грязную закупорку; кроме того, при сварке капилляра и сухого фильтра также легко приварить капиллярную насадку.
После того, как система охлаждения загрязнена и заблокирована, поскольку хладагент не может циркулировать, компрессор работает непрерывно, испаритель не холодный, конденсатор не горячий, корпус компрессора не горячий, и нет звука воздушного потока. в испарителе. Если он частично засорен, в испарителе будет ощущаться прохлада или лед, но не иней. Когда вы прикасаетесь к внешней поверхности сухого фильтра и капилляра, вы чувствуете, что он очень холодный, есть иней, и даже образуется слой белого инея. Это связано с тем, что когда хладагент протекает через микрозабитый сухой фильтр или капиллярную трубку, это вызывает дросселирование и снижение давления, так что хладагент, протекающий через засорение, расширяется, испаряется и поглощает тепло, что приводит к конденсации или конденсации на наружная поверхность засора. Мороз.
Отличие ледяного засора от грязного засора: через некоторое время ледяной затор может возобновить охлаждение, образуя периодическое повторение открывания на некоторое время, блокирования на время, повторного открытия после блокирования и повторного блокирования после открытия. После появления грязного блока его нельзя охлаждать.
В дополнение к грязным капиллярам, если в системе много загрязнений, сухой фильтр будет постепенно забиваться. Поскольку способность самого фильтра удалять грязь и примеси ограничена, он будет заблокирован из-за постоянного накопления примесей.
Отказ от закупорки нефтью и другие отказы от закупорки трубопровода
Основной причиной масляного засорения холодильной системы является сильный износ цилиндра компрессора или слишком большой зазор между поршнем и цилиндром.
Выходящий из компрессора бензин сливается в конденсатор, а затем вместе с хладагентом поступает в сухой фильтр. Из-за высокой вязкости масла оно блокируется осушителем в фильтре. Когда масла слишком много, оно засоряет вход фильтра, в результате чего хладагент не может нормально циркулировать, и холодильник не охлаждается.
Причиной закупорки остальных трубопроводов является: при сварке трубопровода блокируется припоем; или при замене трубки сама замененная трубка заблокирована и не найдена. Вышеупомянутые блокировки вызваны человеческим фактором, поэтому требуется сварка и замена трубы, ее следует эксплуатировать и проверять в соответствии с требованиями, это не приведет к искусственному отказу от блокировки.
Способ устранения засора холодильной системы
1 Устранение засорения льдом
Засорение системы охлаждения льдом из-за чрезмерной влажности в системе, поэтому всю систему охлаждения необходимо просушить. Есть два способа справиться с этим:
1. Используйте сушильную печь, чтобы нагреть и высушить каждый компонент. Снимите компрессор, конденсатор, испаритель, капилляр и трубу возврата воздуха в системе хладагента из холодильника и поместите их в сушильную печь для нагрева и просушки. Температура в боксе около 120°С, время высыхания 4 часа. После естественного охлаждения продуйте и высушите азотом один за другим. Замените на новый сухой фильтр, а затем приступайте к сборке и сварке, обнаружению утечки давления, вакуумированию, заполнению хладагентом, пробной эксплуатации и герметизации. Этот метод является лучшим способом устранения засорения льдом, но он применим только в гарантийном отделе производителя холодильника. Отделы общего ремонта могут использовать такие методы, как нагрев и эвакуация, для устранения неисправностей, связанных с засорением льдом.
2. Используйте нагрев и вакуумирование, а также вторичное вакуумирование для удаления влаги из компонентов холодильной системы.
2 Устранение грязных засоров
Существует два способа устранения закупорки грязного капилляра: первый заключается в использовании азота под высоким давлением в сочетании с другими методами для продувки засоренного капилляра. исключать. Если капилляр серьезно засорен и указанный выше метод не может устранить неисправность, замените капилляр для устранения неисправности следующим образом:
1. Азотом под высоким давлением продуть грязь в капилляре: перерезать технологическую трубу для слива жидкости, приварить капилляр от сухого фильтра, подсоединить трехходовой ремонтный клапан к технологической трубе компрессора и заполнить его азотом под высоким давлением 0,6-0,8 МПа и расправить капилляр, нагреть его газовым сварочным пламенем карбонизации, науглерожить грязь в трубке и продуть грязь в капилляре под действием азота высокого давления . После того, как капилляр очистится, добавить 100 мл четыреххлористого углерода для газоочистки. Конденсатор можно очистить четыреххлористым углеродом на устройстве для очистки труб. Затем замените фильтр-осушитель, затем заполните азотом для обнаружения утечек, вакуумируйте и, наконец, заполните хладагентом.
2. Замените капилляр: Если грязь в капилляре не может быть вымыта описанным выше способом, вы можете заменить капилляр вместе с трубкой низкого давления. Сначала снимите трубку низкого давления и капилляр с медно-алюминиевого соединения испарителя с помощью газовой сварки. При разборке и сварке место соединения медь-алюминий следует обмотать влажной хлопчатобумажной пряжей, чтобы алюминиевая трубка не прогорела при высокой температуре.
При замене капиллярной трубки необходимо измерить скорость потока. Выход капиллярной трубки не следует приваривать к входу испарителя. Установите регулирующий клапан и манометр на входе и выходе компрессора. При одинаковом внешнем атмосферном давлении показание манометра высокого давления должно быть стабильным на уровне 1~1,2 МПа. Если давление превышает, это означает, что скорость потока слишком мала, и часть капилляра можно отрезать до тех пор, пока давление не станет подходящим. Если давление слишком низкое, это означает, что скорость потока слишком велика. Вы можете свернуть капилляр несколько раз, чтобы увеличить сопротивление капилляра, или заменить капилляр. После того, как давление станет подходящим, приварите капилляр к входному патрубку испарителя.
При сварке нового капилляра длина, вставляемая в соединение медь-алюминий, должна составлять от 4 до 5 см, чтобы избежать закупорки при сварке. Когда капилляр приварен к сухому фильтру, длина вставки должна составлять 2,5 см. Если капилляр вставлен слишком глубоко в сухой фильтр и слишком близко к сетке фильтра, крошечные частицы молекулярного сита попадут в капилляр и заблокируют его. Если капилляр вставлен слишком мало, примеси и частицы молекулярных сит во время сварки попадут в капилляр и непосредственно заблокируют капиллярный канал. Поэтому капилляры вставляются в фильтр не слишком много и не слишком мало. Слишком много или слишком мало создает опасность засорения. На рис. 6-11 показано место соединения капилляра и фильтра-осушителя.
3 Устранение масляных пробок
Неисправность забивания маслом указывает на то, что в системе охлаждения осталось слишком много масла для холодильной машины, что влияет на охлаждающий эффект или даже не обеспечивает охлаждение. Поэтому масло холодильной машины в системе необходимо очищать.
Когда масло фильтра забито, необходимо заменить новый фильтр, и в то же время использовать азот под высоким давлением, чтобы продуть часть масла холодильной машины, скопившейся в конденсаторе, и использовать фен для нагрева конденсатора, когда вводится азот.
Время публикации: 06 марта 2023 г.
Справочник по компонентам морозильной камеры
Вы полагаетесь на свою морозильную камеру круглый год для оптимального длительного хранения всех любимых замороженных блюд и ингредиентов вашей семьи. Для замораживания продуктов в морозильных камерах используется испаряющийся хладагент, который проходит цикл через различные части устройства, такие как компрессор, конденсатор и испаритель.
Следуйте этому руководству, чтобы узнать больше о том, какМорозильник 0072 работает как , чтобы заморозить продукты и обеспечить их надлежащее хранение до тех пор, пока они вам не понадобятся.
Из каких компонентов состоит морозильник?
Узнайте, где расположены различные части морозильной камеры и как они работают для длительного хранения замороженных остатков, овощей, мяса и многого другого.
1. Компрессор
Обычно расположенный в нижней задней части морозильной камеры, компрессор увеличивает температуру и давление хладагента, работая вместе со змеевиками конденсатора.
2. Змеевики конденсатора
Змеевики конденсатора работают вместе с компрессором для перемещения хладагента на следующую стадию его цикла через морозильную камеру. Компрессор нагнетает хладагент под высоким давлением к змеевикам конденсатора, превращая его из пара в жидкость за счет передачи тепла.
3. Капиллярная трубка
Капиллярная трубка представляет собой небольшую структуру, ответственную за сильное падение давления, которое снижает температуру хладагента, превращая его из жидкости в пар.
4. Испаритель
Испаритель поглощает тепло, заставляя хладагент снова переходить в состояние низкого давления в виде пара. В результате пар становится очень холодным, создавая оптимальные условия для длительного хранения замороженных блюд и продуктов. Испаритель является конечным пунктом назначения хладагента перед тем, как он вернется в компрессор, снова начав цикл замораживания.
Как называется воздух, выходящий из морозильной камеры?
Чтобы помочь заморозить продукты для более длительного хранения, морозильные камеры поддерживают низкую температуру воздуха внутри. Когда вы открываете дверцу морозильной камеры, теплый наружный воздух смешивается с холодным воздухом изнутри. В результате происходит конденсация, которая создает мутный воздух или туман, который вы видите выходящим из двери.
Вы можете купить запасную дверцу морозильной камеры?
От фильтров для воды и льдогенераторов до термостатов и полочных ящиков — в зависимости от модели доступны сменные детали для приборов, включая сменные дверцы морозильной камеры. Если вы не уверены, какая деталь вам нужна, проконсультируйтесь со специалистом, прежде чем покупать сменную деталь для морозильной камеры с помощью Whirlpool ® Услуги по ремонту или замене .
Где вентиляционные отверстия в моей морозильной камере?
Независимо от того, есть ли у вас отдельный морозильный ларь/вертикальный морозильник или морозильная камера как часть вашего холодильника, вы обычно можете найти вентиляционные отверстия внутри морозильной камеры, которые направляют поток холодного воздуха в холодильник.
Эти вентиляционные отверстия могут располагаться в разных местах в зависимости от модели морозильной камеры. Если у вас возникли проблемы с их поиском, обратитесь к руководству пользователя для получения информации о конкретном продукте.
Что произойдет, если вентиляционные отверстия морозильной камеры заблокированы?
Когда вентиляционные отверстия морозильной камеры засоряются, может возникнуть несколько проблем, в том числе скопление влаги или чрезмерный иней, проблемы с температурой и непостоянная или колеблющаяся температура в морозильной камере.
Переупаковка морозильной камеры может привести к закрытым вентиляционным отверстиям и блокировке потока воздуха. Чтобы предотвратить это, проверьте, являются ли элементы блокировка вентиляционных отверстий морозильной камеры . Избегайте переполнения морозильной камеры и храните ровно столько продуктов, сколько позволяют размеры вашего холодильника.
Как очистить вентиляционные отверстия в морозильной камере?
Все вентиляционные отверстия и вентиляторы морозильной камеры должны быть чистыми, чтобы обеспечить оптимальный поток воздуха и регулирование температуры. Чтобы очистить вентиляционные отверстия морозильной камеры, найдите вентиляционное отверстие внутри морозильной камеры и осторожно удалите излишки инея, а также удалите видимую грязь или пыль мягкой тряпкой.
При необходимости вы также можете вымыть внутренние стены смесью теплой воды и пищевой соды. При очистке любой внутренней части морозильной камеры избегайте абразивных или жестких чистящих средств, а также бумажных полотенец, губок для мытья посуды или других жестких чистящих средств.
Почему мой морозильник не морозит?
Оптимальная температура в морозильной камере имеет важное значение, когда речь идет о безопасном хранении продуктов. Если ваш морозильник не замораживает , это может быть вызвано несколькими причинами, в том числе неправильными настройками элементов управления, чрезмерной упаковкой, грязным змеевиком конденсатора или избыточным накоплением инея.
Если ваш прибор неправильно замораживает продукты, следуйте этим полезным советам:
Проверьте настройки и термостат
Очистка полок морозильной камеры
Очистка змеевиков конденсатора
Разрушение наростов льда для устранения заторов
Магазин для холодильников и морозильников Whirlpool
® Whirlpool 9 с удобными вариантами размеров и продуманной организацией пространстваВ холодильниках и морозильных камерах 0103 ® есть все необходимое, чтобы ваши продукты и напитки оставались холодными круглосуточно. Изучите полную коллекцию холодильников и морозильных камер бренда Whirlpool, чтобы получить свежие и вкусные продукты, когда они вам больше всего нужны.
Узнайте больше о морозильных камерах Whirlpool
®Как разморозить морозильник Не знаете, как разморозить морозильник? Наше руководство покажет вам, как разморозить морозильную камеру, чтобы вы могли продолжать свой день.
Морозильный ожог: что это такое и как его предотвратить? Что вызывает ожог морозильной камеры? Узнайте больше об этой проблеме хранения продуктов и получите советы, которые помогут предотвратить ожоги при замораживании мяса, овощей, мороженого и других продуктов.
Какая оптимальная температура в морозильной камере? Если вам интересно, на какую температуру должна быть установлена ваша морозильная камера, вы не одиноки.