Как спаять медь с алюминием: можно ли их паять и как это сделать в домашних условиях паяльником?
Соединение медного и алюминиевого провода: правила и способы
Любая кабельная продукция имеет токопроводящую жилу, выполненную из алюминия или меди. Так как эти материалы обладают хорошей токопроводимостью, теплоотдачей и стоят недорого, то при монтаже и подключении довольно часто возникает необходимость соединения этих двух разных по химическому составу элементов электрических цепей. Согласно правилам устройства электроустановок (ПУЭ глава 2.1. п 2.1.21) простая скрутка между собой двух проводов разного материала запрещена, если нет последующей пайки или сварки. Однако, существуют и более действенные способы для выполнения данной процедуры как в домашних условиях, так и на производстве. В этой статье мы расскажем, как правильно выполнить соединение медного и алюминиевого провода и каких ошибок не следует допускать.Какие проблемы могут возникнуть при соединении алюминия и меди
Не так давно электропроводку в квартире или частном доме выполняли из алюминиевого провода, так как её было достаточно чтобы обеспечить питанием все существующие немногочисленные электроприборы.
При касании алюминия и меди возникает химическая реакция, которая впоследствии ухудшает электрический контакт, место подключения начинает греться и в итоге может стать причиной возгорания проводки и даже пожара. При повышенной окружающей влажности этот процесс происходит достаточно быстро, так как между проводниками образуется тонкая плёнка, обладающая высоким сопротивлением, следствием чего является нагрев и обрыв цепи. Но всё же каждый электрик знает как соединить алюминиевый провод с медным, чтобы в дальнейшем избежать неприятной ситуации.
На видео ниже наглядно показаны последствия небезопасного контакта между медью и алюминием:
В любом случае рекомендуется заменить старую проводку на медную, которая будет иметь нагрузочную способность, соответствующую текущему потреблению электроприборов. Если нет возможности полностью заменить проводку на новую, то выполняют частичную замену проводки. В таком случае и возникает необходимость соединения старой и новой электропроводки – медного и алюминиевого проводов.
Способы соединения разных проводов
Существует несколько основных общепринятых распространённых приспособлений, которые дают возможность ликвидировать непосредственный контакт между двумя материалами, действующими друг на друга агрессивно. Рассмотрим каждый отдельно.
Клеммные колодки
Клеммные колодки могут быть оснащены болтовым или зажимным механизмом соединения. Данная конструкция даёт подключение к одному выводу алюминиевого, а к другому медного токопроводящего материала, которые контактируют между собой через стальную пластину. Пластина изготовлена из нейтрального металла, который не вступает в реакцию с медью и алюминием – обычно это латунные пластины либо медные луженые пластины. Например, широко применяемой клеммой Wago 2273, можно соединить одновременно от двух до восьми проводников разного сечения, выполнить крепёж на DIN-рейку с помощью специального монтажного адаптера.
Болтовой зажим в колодках более надёжен и применяется в силовых не высоковольтных цепях. Чаще всего он осуществляется с помощью «ореха». Это небольшая разветвительная коробка, выполненная из диэлектрического материала, в форме напоминающего грецкий орех, внутри которого расположен блок металлических пластин, через которые и происходит контакт между алюминиевыми и медными проводами. Все эти вышеописанные способы относятся к разъёмным соединениям, то есть для многоразового подключения и отключения, в случае необходимости.
На примере наглядно показывается выполненное скрепление меди и алюминия в распределительной коробке за счет использования латунных клеммников:
О том, как соединить провода клеммами WAGO, читайте в нашей отдельной публикации!
Метод опрессовки
Иногда, при прокладке и монтаже электропроводки, появляется необходимость в выполнении качественного неразъёмного соединения медных и алюминиевых проводов опрессовкой с помощью гильз. Чаще она встречается на вводе в электрический шкаф, распределительное устройство или при соединении кабеля с уже установленным агрегатом, где нельзя выполнить замену алюминия на медь, и наоборот.
Такой вид подсоединения проводников является более затратным, так как требует специального инструмента. Но в то же время, при проведении многочисленных монтажных работ такого плана, профессионалы часто выбирают именно его.
Опрессовка проводов гильзами обеспечивает более надёжный и долговечный контакт. Таким методом на производстве скрепляют медные и алюминиевые жилы даже к особо мощным и высоковольтным потребителям. Для выполнения этих работ необходим специальный инструмент и особые медно-алюминиевые гильзы. Их сжим может выполняться даже с помощью обычного молотка и металлических накладок, что не совсем правильно, или же существует профессиональный ручной гидравлический пресс.
Таким сжимом рекомендуется пользоваться не только при опрессовке гильз, но и наконечников. Кстати, они тоже могут быть выполнены наполовину из меди и алюминия, для подключения, например, алюминиевого кабеля к какому-либо аппарату с медными выводами или клеммами.
Обычно алюмомедные гильзы используют для соединения жил кабелей большого сечения. При небольших сечениях, например, в домашней электропроводке, выполняется опрессовка нескольких проводников одной гильзой. При этом провода заводят с разных сторон, для соединения как бы в стык, как показано на фотографии выше. Нельзя складывать алюминиевые и медные проводники параллельно друг другу (внахлест), как это было показано на иллюстрации с гидравлическим прессом, потому что в этом случае возникает прямой контакт алюминия и меди. Также нельзя использовать медные нелуженные гильзы с алюминиевым кабелем.
Болтовое соединение
Очень часто при работе с электропроводкой у простого человека, не занимающегося электромонтажными работами, в домашних условиях может появиться экстренная необходимость в создании хорошего и надёжного контакта между алюминиевым и медным проводом. Бежать в магазин для покупки специального инструмента и материалов не целесообразно при выполнении разовых работ, а их нужно сделать и при этом качественно.
Тогда имеет смысл воспользоваться обычным болтом с гайкой и несколькими шайбами. Главное, в этом методе — это разделить шайбами два металла, агрессивных друг к другу, так как показано на рисунке внизу.
Болтовое соединение алюминиевого и медного провода можно выполнить в распределительной коробке, которая является неотъемлемой частью любой проводки как в доме, так и в квартире. Таким образом, через болт с лёгкостью и достаточно качественно соединяются даже провода с разными жилами по сечению.
Колечки из провода должны быть завернуты в сторону затягивания гайки, при болтовом соединении. Это нужно чтобы при затягивании колечки не раскручивались и не увеличивались в диаметре, а наоборот плотнее оборачивались вокруг болта.
На видео наглядно показывается, как соединить жилы разного материала болтом:
youtube.com/embed/xkk7sH98qe8″ allowfullscreen=”allowfullscreen”/>Похожий способ — применение заклепочника. Ниже наглядно показывается, как соединить провода заклепкой:
Есть еще вариант применения алюмомедных наконечников и алюмомедных шайб. Можно опрессовать алюминиевый кабель наконечником и подсоединять к медной шине. Либо при использовании алюмомедной шайбы можно опрессовать алюминиевый кабель обычным алюминиевым кабельным наконечником и подключить на шину через данную шайбу.
Особенности соединения жил на улице
При монтаже кабельной линии по улице все элементы соединения подвержены воздействию внешних негативных факторов, таких как снег, обледенение, дождь и т. д. Поэтому для выполнения таких работ необходима только герметично закрывающаяся конструкция, устойчивая к ультрафиолетовым лучам и низким температурам. Осуществляя подключения на столбе, крыше и в другом открытом месте чаще всего применяются прокалывающие зажимы.
В помещениях при прокладке кабеля в стене под штукатуркой кабель укладывается в штробе цельным, и любое соединение даже однородных металлов нежелательно. Всё подключения в розетке или распределительной коробке выполняются любым вышеописанным способом, подходящим для каждой индивидуальной ситуации.
Распространённые ошибки, полезные советы и правила
К вашему вниманию несколько полезных советов, позволяющих безопасно соединить алюминиевый провод с медным между собой:
- Перед тем как соединить жилы пайкой нужно знать, что медь залудить будет очень просто, а алюминий только с помощью специального припоя.
- Нельзя слишком сильно сжимать места соединения как многожильных, так и одножильных проводников. В противном случае возникнет деформация и повреждение жил.
- Всегда стоит соблюдать маркировку и правильно подбирать клеммники в зависимости от сечения жилы и типа установки (в помещении или же на улице).
- Ни в коем случае не используйте для соединения алюминиевой и медной проводки обычные скрутки. Это один из самых небезопасных способов коммутации жил, который чаще всего приводит к пожару.
Это и все, что мы хотели рассказать вам о том, как выполнить соединение медного и алюминиевого провода. Надеемся, предоставленные способы и правила помогли вам понять всю сущность работ!
Будет полезно прочитать:
Пайка алюминия – флюс, припой, как и чем паять правильно
Пайка алюминия, как справедливо считают многие специалисты, является достаточно сложным в выполнении технологическим процессом. Между тем такое мнение можно считать верным лишь в отношении тех ситуаций, когда спаять изделия из алюминия пытаются, используя для этого припои и флюсы, которые применяются для соединения деталей из других металлов: меди, стали и др. Если же используется специальный флюс для пайки алюминия, а также соответствующий припой, то данный технологический процесс не представляет особых сложностей.
Пайка алюминия с использованием пропановой горелки
Особенности процесса
Сложности, которые вызывает пайка алюминия при помощи традиционных припоев и флюсов, объясняются рядом факторов, преимущественно связанных с характеристиками данного металла. Основным из таких факторов является наличие на поверхности деталей из алюминия оксидной пленки, которая отличается высокой температурой плавления и исключительной химической стойкостью. Такая пленка при выполнении пайки препятствует соединению основного металла и материала припоя.
Перед осуществлением пайки изделий из алюминия их поверхности необходимо тщательно очистить от оксидной пленки, для чего можно использовать механическую обработку или применять флюсы, в состав которых входят сильнодействующие компоненты.
Подготовленные к пайке дюралевые детали
Сам алюминий, в отличие от оксидной пленки на его поверхности, обладает достаточно низкой температурой плавления: 660 градусов, что также осложняет технологический процесс выполнения пайки. Такая характеристика алюминия приводит к тому, что при нагреве детали из него быстро теряют прочность, а при определенной температуре, находящейся в интервале 250–300 градусов, конструкции из данного металла начинают терять устойчивость. Самый легкоплавкий компонент, который входит в состав наиболее распространенных алюминиевых сплавов, начинает плавиться уже в интервале температур 500–640 градусов, что может привести к перегреву и даже к расплавлению самих соединяемых деталей.
Основу большей части легкоплавких припоев, использующихся для пайки, составляют олово, кадмий, висмут и индий. С этими элементами алюминий плохо вступает в соединения, что делает паяные соединения, полученные с их использованием, очень непрочными и ненадежными. Хорошей взаимной растворимостью обладают алюминий и цинк, поэтому данный элемент при его использовании в припоях обеспечивает полученному соединению высокую прочность.
Характеристики флюсов для пайки мягкими припоями
Состав флюсов, применяемых для пайки алюминия
Используемые материалы
При выполнении пайки изделий из алюминия можно использовать припои оловянно-свинцовой группы, если тщательно очистить поверхность деталей и применять высокоактивные флюсы. Соединения, полученные с их помощью, по причине плохой взаимной растворимости алюминия, олова и свинца отличаются невысокой надежностью, также они склонны к развитию коррозионных процессов. Чтобы сделать подобные соединения более устойчивыми к коррозии, их необходимо покрывать специальными составами.
Наиболее качественное, надежное и устойчивое к коррозии паяное соединение, позволяют получать припои, в составе которых содержится цинк, медь, кремний и алюминий.
Припои, включающие в свой состав данные элементы, производят как отечественные, так и зарубежные компании. Наиболее распространенными отечественными марками являются ЦОП40, содержащий в своем составе 40% цинка и 60% олова, и 34А, в составе которого содержится алюминий (66%), медь (28%) и кремний (6%). Цинк, содержащийся в припое для пайки изделий из алюминия, определяет не только прочность полученного соединения, но и его коррозионную устойчивость.
youtube.com/embed/GtlDb9v7PLg”/>Самую низкую температуру плавления из всех вышеперечисленных имеют оловянно-свинцовые припои. Наиболее высокотемпературными являются те, в составе которых содержится алюминий и кремний, а также материалы, содержащие алюминий вместе с медью и кремнием. К последним, в частности, относится припой популярной марки 34А, температура плавления которого находится в интервале 530–550 градусов.
Для информации: материалы на основе алюминия и кремния плавятся при температуре 590–600 градусов.
Учитывая температуру плавления, применяют такие припои в тех случаях, когда соединить необходимо крупногабаритные детали из алюминия, в которых обеспечивается хороший теплоотвод, либо изделия, выполненные из алюминиевых сплавов, плавящихся при достаточно высоких температурах.
Но, конечно, максимальное удобство в работе демонстрируют низкотемпературные припои, одной из распространенных марок которых является HTS-2000.
Припой HTS-200 для спайки деталей из алюминия и цветных металлов
Технология пайки алюминия обязательно предполагает использование специального флюса, который необходим для того, чтобы улучшить соединяемость основного металла с материалом припоя. Именно поэтому подходить к выбору такого материала необходимо очень ответственно. Особенно актуально это требование в тех случаях, когда детали из алюминия необходимо спаять при помощи оловянно-свинцового припоя. Состав флюсов содержит элементы, которые и формируют его активность по отношению к алюминию. К таким элементам относятся: триэтаноламин, фторборат цинка, фторборат аммония и др.
Флюс Ф-64 для пайки легких сплавов без предварительной механической обработки поверхностей
Одним из наиболее популярных отечественных материалов является флюс марки Ф64. Популярность Ф64 обусловлена тем, что данный материал отличается повышенной активностью. Благодаря такому качеству выполнять пайку с флюсом Ф64 можно, даже не зачищая поверхность алюминиевых деталей от тугоплавкой оксидной пленки.
Из популярных высокотемпературных флюсов следует выделить материал марки 34А, в состав которого входит 50% хлорида калия, 32% хлорида лития, 10% фторида натрия и 8% хлорида цинка.
youtube.com/embed/UIxPlva4ED8″/>Подготовка деталей
Для получения качественного и надежного соединения недостаточно просто знать, как паять алюминий, важно также правильно подготовить поверхности соединяемых деталей к пайке. Заключается такая подготовка в обезжиривании поверхностей и удалении с них окисной пленки.
Для обезжиривания используют традиционные средства: ацетон, бензин или любой подходящий растворитель.
Удаление окисной пленки перед пайкой, которое также несложно выполнить своими руками, преимущественно совершается при помощи механической обработки, для чего можно использовать шлифовальную машинку, наждачную бумагу, металлическую щетку или сетку из нержавеющей проволоки. Значительно реже применяется химический способ удаления такой пленки, который подразумевает травление поверхности алюминиевых деталей при помощи кислотных растворов.
Зачистка поверхностей перед пайкой с помощью шлифовальной насадки на болгарку
Как известно, окисная пленка на поверхности алюминия образовывается практически моментально при ее контакте с окружающим воздухом. Такой процесс происходит и на зачищенной перед пайкой поверхности, но смысл выполнения зачистки состоит в том, что вновь образующаяся пленка значительно тоньше удаленной, поэтому флюсу будет гораздо легче с ней справиться.
Источники нагрева
В качестве элемента, при помощи которого выполняется прогрев габаритных соединяемых деталей из алюминия и расплавление припоя, преимущественно используется газовая горелка, работающая на пропане или бутане. Если вы решили спаять изделия из алюминия своими руками в условиях домашней мастерской, то можно использовать и обычную паяльную лампу.
Удобная в использовании газовая паяльная лампа
При выполнении нагрева необходимо очень внимательно следить за тем, чтобы не расплавились соединяемые детали. С этой целью к поверхности деталей как можно чаще прикасаются припоем, чтобы проконтролировать начало его плавления. Это и будет свидетельством того, что достигнута рабочая температура.
Нагревая детали и припой перед началом пайки, также необходимо следить за пламенем газовой горелки: смесь газа и кислорода, которая его формирует, должна быть сбалансированной. Делать это необходимо по той причине, что сбалансированная газовая смесь активно нагревает металл, но не оказывает серьезного окислительного действия. О том, что газовая смесь сбалансирована, свидетельствует ярко-синий цвет пламени, которое имеет небольшой размер. Если пламя горелки слишком маленькое по размеру и имеет бледно-голубой цвет, то это является свидетельством того, что в газовой смеси слишком много кислорода.
Для пайки небольших изделий из алюминия используются электрические паяльники и припои, плавящиеся при невысокой температуре.
Технологические приемы пайки
Пайка деталей, выполненных из алюминия, по технологии выполнения практически ничем не отличается от процесса соединения изделий, изготовленных из других металлов. Сначала соединяемые детали обезжириваются и тщательно зачищаются, после этого их выставляют в нужное положение относительно друг друга. Затем на зону будущего соединения необходимо нанести флюс и начать ее прогрев вместе с припоем до рабочей температуры.
Процесс пайки деталей из алюминиевого сплава
При достижении рабочей температуры кончик припоя начнет плавиться, поэтому им необходимо постоянно прикасаться к поверхности деталей, контролируя процесс нагрева.
Пайка изделий из алюминия, для выполнения которой используется безфлюсовый припой, имеет свои особенности. Заключаются они в том, что для того, чтобы проникновению припоя к поверхности детали не препятствовала окисная пленка, его кончиком необходимо совершать чиркающие движения по месту будущего соединения. Таким образом нарушается целостность пленки, и припой беспрепятственно соединяется с основным металлом.
Посмотреть, как пайка выполняется практически, можно на обучающем видео.
Есть еще один технологический прием, позволяющий разрушить оксидную пленку в процессе пайки. Сделать это можно при помощи стержня из нержавеющей стали или металлической щетки, которыми водят по месту соединения и уже расплавленному припою.
Чтобы получить максимально прочное соединение методом пайки, соединяемые поверхности необходимо подвергнуть предварительному лужению.
Сфера применения процесса
Большое практическое значение имеет не только пайка алюминия в домашних условиях. Данную технологию также активно используют на ремонтных и производственных предприятиях. Применяя метод пайки, можно получать соединения, отличающиеся высокой прочностью, надежностью и эстетической привлекательностью.
При работе с тонким листовым алюминием пайка позволяет избежать деформацию материала
Большой популярностью данная технология пользуется при выполнении ремонтных работ с автотранспортными средствами, тракторами и мотоциклами. Объясняется такая популярность тем, что при пайке не происходит изменение структуры соединяемого металла, поэтому подобный способ соединения во многих случаях является даже более предпочтительным, чем сварка.
Практически безальтернативной пайка является тогда, когда необходимо восстановить герметичность алюминиевого радиатора или картера, отремонтировать изношенную или разрушенную деталь, изготовленную из алюминиевого сплава. Удобно и то, что сделать такой ремонт можно и своими руками, для этого не потребуется сложного и дорогостоящего оборудования.
Отремонтированный в домашних условиях автомобильный радиатор
Прогары, сколы и трещины, образовавшиеся в блоке цилиндров, изготовленном из алюминиевого сплава, также можно успешно отремонтировать при помощи пайки. Очень полезна данная технология в том случае, если необходимо восстановить изношенную внутреннюю резьбу. При этом изношенное резьбовое отверстие заполняется расплавленным припоем, а затем в него вворачивается болт. После того как припой застынет, болт из отверстия выворачивается, а внутри него оказывается сформированная по необходимым параметрам резьба. Такая несложная операция позволяет получить новую резьбу, которая по своим прочностным характеристикам ничем не уступает исходной.
Кроме этого, пайка успешно применяется для ремонта и восстановления герметичности труб, изготовленных из алюминия и сплавов данного металла. Такие трубы сейчас активно используются во многих технических устройствах. При помощи пайки вы можете своими руками, не прибегая к дорогостоящим услугам квалифицированных специалистов, отремонтировать многие предметы из алюминия и его сплавов, использующиеся в быту: посуду, лестницы, различные детали интерьера, водосточные желоба, элементы сайдинга и др. При помощи пайки можно не только ремонтировать, но и своими руками изготавливать любые конструкции из алюминия.
Использование качественных расходных материалов и строгое следование технологии, которой совсем несложно обучиться и по видео урокам, позволяет получать методом пайки соединения, отличающиеся высоким качеством, надежностью, привлекательным и аккуратным внешним видом.
Использование подручных средств
Нередки ситуации, когда под рукой нет активного флюса и припоя, который специально предназначен для соединения деталей из алюминия, а спаять их необходимо срочно. В таких ситуациях можно выполнить пайку обычным припоем, состоящим из алюминия и олова или олова и свинца. В качестве флюса в данном случае можно использовать канифоль.
Оксидная пленка при использовании данного метода пайки разрушается под слоем канифоли, в которую можно дополнительно добавить металлические опилки. Для ее разрушения применяется специальный паяльник со скребком, который необходимо предварительно залудить. Скребок наряду с опилками разрушает оксидную пленку на поверхности деталей, а канифоль не дает образоваться новой. Кроме того, скребок-паяльник, перемещая расплавленный припой по месту будущего соединения, обеспечивает его лужение.
Конечно, такой способ пайки очень хлопотный и не всегда гарантирует получение качественного и надежного соединения, поэтому использовать его можно только в крайних случаях. Целесообразнее всего потрать время и деньги на приобретение качественных припоя и флюса и не переживать за качество формируемого с их помощью соединения.
медь с алюминием | Советы электрика
16 Апр 2012 Советы специалиста
Очень часто в старых домах приходится при ремонте электропроводки соединять алюминиевые провода старой проводки с медными– вновь проложенными.
Кто незнаком с этой темой и делает ремонт своими руками- просто тупо скручивают их между собой и закрывают в распредкоробке, не понимая какую головную боль они себе приобретут в дальнейшем…
С этой темой- соединение меди с алюминием- сталкиваются не отлько при монтаже внутренней электропроводки, но и при замене ввода в дом
Дело в том, что провода воздушной линии (ВЛ)- алюминиевые и если вы делаете вводной кабель медный, то просто так накрутить на алюминиевый провод жилу кабеля- нельзя!
А ведь делают же! Сколько раз сам видел… А потом удивляются- “Почему это у меня свет в доме моргает?!”
Да, действительно, а почему? А вот из-за чего.
Немного химии. Алюминий- очень активный метал, попробуйте его спаять простым методом как медный провод, ничего не получится.
Алюминий активно реагирует на воздух, вернее даже не на сам воздух, а на влагу в воздухе, быстро образуя на своей поверхности тонкую пленку окиси.
Эта пленка оказывает высокое сопротивление электрическому току- появляется так называемое “переходное сопротивление” в месте соединения проводов.
Но медный провод тоже окисляется, однако не так сильно и интенсивно как алюминий и пленка окиси на поверхности меди оказывает гораздо меньшее сопротивление протеканию тока.
Получается что при соединении медного и алюминиевого провода они контактируют своими оксидными пленками.
Так же у этих двух металлов разное линейное расширение, поэтому при изменении температуры в помещении или величины тока, протекающего через скрутку медь-алюминий контакт между ними со временем ослабевает.
Переходное сопротивление в скрутке итак “тормозило” электрический ток, да еще ослабление контакта еще более увеличивало величину переходного сопротивления.
Это приводит к тому, что скрутка начинает греться, чем дальше- тем больше, греется изоляция провода. разрушается от нагрева даже может загореть.
Сами знаете сколько домов сгорело из-за неисправностей в электропроводке и зачастую виновато в этом именно переходное сопротивление или плохой контакт.
Кстати о переходном сопротивлении.
Это активное сопротивление, то есть вся мощность на нем на 100% преобразуется в теплоту, ну как в утюге например)))
Что бы понять что это такое- представтье что два провода соединены между собой нихромовой проволокой и по ним протекает электрический ток, который раскаляет нихром докрасна.
Вот внутри скрутки медного и алюминиевого провода и находится такая раскаленная докрасна нихромовая нить. А оно вам надо?!
Запомните- переходное сопротивление- аналог раскаленной нихромовой нити.
Так, химии достаточно. Теперь как выйти из положения если надо соединить медный провод с алюминиевым.
Тут суть вот в чем: главное что бы эти два металла не соприкасались между собой. Между ними должен быть нейтральный по отношению к ним материал, естественно токопроводящий.
Это может быть свинцовый припой, дюралюминий,сталь, нержавейка, покрытие из хрома.
Кстати интересно- нельзя: цинк, углерод (графит) и серебро с золотом и платиной.
Хотя я себе не представляю кто может себе позволить такое удовольствие- соединять медь с алюминием через платину)))
В такм случае если денег море- лучше совсем провода полностью из платины сделать, потери напряжения исчезнут напрочь)))
Итак, соединяем медь с алюминием:
-С помощью клемных зажимов;
-Болтовое соединение через шайбы
-Слой из нейтрального материала
Клемные зажимы- это ответвительные сжимы (так называемые “орехи”), wago, клемники в изоляции и т. п.
Ну болтовое соединение итак понятно- делается петля на проводе, вставляется болт, а между медью и алюминием- стальные шайбы.
Такое соединение гораздо надежнее всех клемников и зажимов, единственный минус- большие габариты, в распредкоробке много метса занимают.
Я так сам делал например на вводе в дом- когда надо было соединить медный кабель с алюминиевым вводом от ВЛ. Да еще кабель был четырехжильным, а сеть- 220.
Тогда сделал на фазу и ноль по две жилы кабеля, соединил через болтовое соединение с обрезком алюминиевого провода, и уже этот обрезок был подключен энергетиками на ввод.
Уже второй год прошел- замечаний нет))) Это при наличии электроплиты в доме и всего прочего- электротитан, чайник, утюг, микроволновка и т.д.
Сейчас про слой из нейтрального материала. Я имею ввиду- свинцово-оловянный припой.
Как это делается покажу на фото:
Это хороший выход из положения когда нет под рукой зажимов или не хочется их использовать, а болтовое соединение не помещается в коробку.
Тогда надо покрыть медный провод припоем и сделать скрутку с алюминием- соединение будет надежным! Хотя и по ПУЭ- неправильным…
Там требуется или пайка-сварка или клемники-болты, чистая скрутка по ПУЭ- вне закона…
Хотя я лично однажды вскрыл распредкоробку освещения в старом доме- там с выключателя медный провод шел, а на лампочку- алюминиевый. Скрутка была чисто медь с алюминием без вских клемников, припоя и т.д.
Так состояние- как будто только что скрутили!
Все чистенько, никакого окисла и подгара. Я думаю это потому, что в квартире было всегда сухо и к тому же распредкоробка была наглухо запечатана в стене- то есть воздух в нее не проникал.
А поэтому и алюминий не окислялся и к тому же нагрузка на скрутку была минимальная- всего одна лампочка подцеплена.
Поэтому если через соединение медь-алюминий будет проходить большой ток, то лучше сделать болтовое соединение как самое простое, посложнее- пайка.
А вот ваговский зажим в таком случае я бы не рекомендовал использовать, лучше другие клемники где провода хотя бы винтом зажимаются.
Итак, сейчас вы знаете как соединять медный провод с алюминиевым и если вам придется это делать- уверен, вы сделаете правильный выбор!
Качественное алюминиевое остекление балконов не дорого.
Узнайте первым о новых материалах сайта!
Просто заполни форму:
Теги: медь с алюминием, соединение проводов
Как правильно соединять медные и алюминиевые провода
В квартирах домов старой постройки зачастую электропроводка выполнена из алюминиевых проводов, соединенных между собой методом скрутки. При подключении к алюминиевой электропроводке светильников, установке дополнительных розеток и другого электрооборудования необходимо учитывать, что при повышенной влажности сопротивление контакта между алюминиевыми и медными проводами со временем увеличивается. Это приводит к нагреву места соединения и разрушению контакта.
Для надежного соединения медных и алюминиевых проводов между собой необходимо соблюдать простые правила, о которых и пойдет речь.
Способы соединения
алюминиевых проводов с медными
Подключать медные провода к уже существующей проводке из алюминиевых проводов, не так сложно, как кажется на первый взгляд. Главное соблюдать технологию.
Соединение скруткой
Скрутка, хотя правилами ПУЭ в настоящее время запрещена, является одним из самых распространенных способов соединения проводов в быту, благодаря простоте и не требующая дополнительных затрат. Но при соединении разнородных металлов, скрутка является и самым низко надежным способом соединения проводников.
При колебаниях температуры окружающей среды, из-за линейного расширения металлов, между проводами в скрутке образуется зазор, увеличивается сопротивление контакта, начинает выделяться тепло, провода окисляются, и контакт в конечном итоге между проводниками полностью нарушается. Конечно, это происходит спустя не один год, но, тем не менее, если планируется надежная долговременная работа электропроводки, то соединение проводов скруткой лучше заменить более надежным, например резьбовым или с помощью клеммных колодок.
Но если возникла необходимость скрутить провода, то скрутку нужно выполнять таким образом, чтобы проводники обвивали друг друга, а не один обвивал другой. На фотографии слева показана скрутка, которую делать недопустимо, так как не будет, обеспечена достаточная механическая прочность соединения. Скрутку медного проводника и алюминиевого без принятия мер по дополнительной герметизации ее недопустимо. Герметизировать скрутку можно любым водостойким защитным лаком.
Максимально надежное соединение медного и алюминиевого проводников получится, если медный провод предварительно залудить припоем. На правой фотографии скрутка медного и алюминиевого проводов выполнена правильно. Соединять провода можно разного диаметра, многожильный провод с одножильным проводом. Только многожильный провод необходимо предварительно пролудить припоем, сделав, таким образом, его одножильным. Витков в скрутке должно быть не менее трех для толстого провода и не менее пяти для тонкого, диаметром менее 1 мм.
Резьбовое соединение
алюминиевых проводов с медными
Соединение проводов, при правильном выполнении, с помощью винтов и гаек является самым надежным и способно обеспечивать надлежащий контакт на протяжении всего срока службы электропроводки и подсоединенных электроприборов. Легко разбирается и позволяет соединять любое количество проводников, ограниченное только длиной винта. С помощью резьбового соединения можно успешно соединять провода в любом сочетании, алюминиевые и медные, тонкие и толстые, многожильные и одножильные. Главное, не допускать непосредственного контакта проводов из меди и алюминия, и устанавливать пружинные шайбы.
Для того, чтобы выполнить резьбовое соединение необходимо снять с проводников изоляцию на длину, равную четырем диаметрам винта, если жилы окисленные, то зачистить металл до блеска и сформировать колечки. Далее на винт одевают пружинную шайбу, простую шайбу, колечко одного проводника, простую шайбу, колечко другого проводника, шайбу и в довершение гайку, завинчивая винт в которую весь пакет стягивают до выпрямления пружинной шайбы.
Для проводников с диаметром жил до 2 мм достаточно винта М4. Соединение готово. Если проводники из одного металла или при соединении алюминиевого провода с медным, конец которого залужен, то шайбу между колечками проводников прокладывать не нужно. Если медный провод многожильный, то его сначала нужно пролудить припоем.
Соединение алюминиевых проводов с медными
клеммной колодкой
В настоящее время широкое распространение получил способ соединения проводов с помощью клеммной колодки. Конечно, этот вид соединения проводов по надежности уступает соединению с помощью винта и гайки, но имеет ряд преимуществ. Позволяет надежно и быстро соединять алюминиевые провода и медные между собой в любом сочетании, не требуется формировать на концах проводов колечки, не нужно соединение изолировать, так как конструкция клеммной колодки исключает случайное прикосновение оголенных участков проводов друг с другом.
Для подсоединения провода к клеммной колодке, достаточно зачистить его конец от изоляции на длину 5 мм, вставить в отверстие и зажать винтом. Затягивать винт нужно со значительным усилием, особенно это важно при соединении алюминиевых проводов. Клеммная колодка незаменима при подключении люстры к коротким алюминиевым проводам, выходящим из потолка. От многократных скруток алюминиевые провода обламываются и становятся короткими. Даже если выходит алюминиевый проводник длиной всего в один сантиметр, то с помощью клеммной колодки можно подключить люстру надежно.
Очень удобна клеммная колодка для соединения перебитых в стене алюминиевых и медных проводов, так как длина перебитых проводов для соединения другими способами недостаточна. Но прятать клеммную колодку под штукатурку без размещения в распределительной коробке, не допустимо.
Соединение алюминиевых проводов с медными
с помощью клеммной колодки с плоско пружинным зажимом Wago
В настоящее время широкое распространение получили клеммные колодки с плоско пружинным зажимом Wago (Ваго) немецкого производителя. Клеммники Wago бывают двух конструктивных исполнений, одноразовые, когда провод вставляется без возможности изъятия, и многократного применения, с рычажком, позволяющим многократно как вставлять провода, так и вынимать.
На фото одноразовый клеммник Wago. Они рассчитаны для соединения любых видов одножильных проводов, в том числе и медных с алюминиевыми проводами сечением от 1,5 до 2,5 мм2. Колодка рассчитана на соединение электропроводки в соединительных и распределительных коробках с силой тока до 24 А, но я сомневаюсь в этом. Думаю, током силой более 5 А нагружать клеммы Wago не стоит.
Пружинные клеммники Wago очень удобные для подключения люстр, соединения проводов в соединительных и распределительных коробках. Достаточно просто с усилием вставить провод в отверстие колодки, и он надежно зафиксируется. Для того, чтобы вынуть провод из колодки потребуется значительное усилие. После изъятия проводов может произойти деформации пружинящего контакта и надежное соединение проводов при повторном соединении этой клеммой не гарантируется. Это является большим недостатком одноразового клеммника.
Более удобный клеммник Wago многоразовый, имеющий оранжевый рычажок. Такие клеммники позволяют соединять и в случае необходимости, разъединять между собой любые провода электропроводки, одножильные, многожильные, алюминиевые в любом сочетании сечением от 0,08 до 4,0 мм2. Рассчитаны на ток до 34 А.
Достаточно снять с провода изоляцию на 10 мм, поднять вверх оранжевый рычажок, вставить провод в клемму и вернуть рычажок в исходное положение. Провод надежно зафиксируется в клеммнике.
Клеммная колодка Wago является современным средством соединения проводов без инструмента быстро и надежно, но обходится дороже, чем традиционные способы соединения.
Неразъемное соединение
алюминиевых проводов с медными
Неразъемное соединение проводов обладает всеми преимуществами резьбового, за исключением возможности разборки и повторной сборки соединения без разрушения заклепки и необходимость наличия специального инструмента для выполнения заклепки – заклепочника. Сегодня заклепки широко используются для неразъемного соединения тонкостенных деталей конструкций при создании перегородок и интерьера в любых помещениях. Скорость, прочность, низкая цена и простота выполнения операции по заклепке – вот главное достоинство данного вида неразъемного соединения.
Принцип работы заклепочника простой, втягивание и отрезание стального стержня, продетого через трубчатую алюминиевую заклепку со шляпкой. Стержень имеет утолщение и когда втягивается в трубку заклепки, расширяет ее. Заклепки бывают разных длин и диаметров, так что есть возможность подобрать любую.
Для того, чтобы соединить проводники заклепкой, нужно их подготовить так же, как и для резьбового соединения. Диаметры колечек должны быть чуть больше диаметра заклепки. Оптимальный диаметр заклепки это 4 мм. На заклепку одевают сначала алюминиевый проводник, затем пружинную шайбу, далее медный и плоскую шайбу. Вставляют стальной стержень в заклепочник и сжимают его ручки до щелчка (это происходит обрезка излишков стального стержня). Соединение готово.
Надежность резьбового и неразъемного соединения заклепкой достаточно высокая. Такой способ соединения можно успешно применять для сращивания, например, поврежденных при ремонтных работах в стене алюминиевых проводников дополнительной вставкой. Только нужно позаботиться о хорошей изоляции оголенных участков соединений.
С другими видами и способами соединения проводов вы можете ознакомиться на странице «Как правильно соединять электрические провода».
Электрохимическая коррозия соединенных металлов
Существует мнение, что алюминиевые и медные провода соединять непосредственно вместе недопустимо и это действительно научно обоснованный факт. А можно ли соединять медный провод с оцинкованной клеммой? Конечно, Вы не можете сразу дать ответ, но через минуту будете ориентироваться в этом вопросе не хуже опытного химика.
Что же происходит при соприкосновении двух разных проводников тока? Если влаги нет, то соединение будет надежным всегда. Но в атмосферном воздухе всегда есть пары воды, которые и является виновником разрушения контактов. Каждый проводник тока обладает определенным электрохимическим потенциалом. Это свойство металлов широко используется в технике, например, изготавливают термопары.
Но если вода попадает между металлами, то образует короткозамкнутый гальванический элемент, начинает течь ток и как в гальванической ванне разрушается один из электродов, так и в соединении разрушается один из металлов. Электрохимический потенциал каждого токопроводящего материала известен, и зная величину можно точно определить, какие материалы допустимо соединять между собой.
Таблица электрохимических потенциалов (мВ)
возникающих между соединенными проводниками
Согласно требованиям стандарта допускается механическое соединение между собой материалов, электрохимический потенциал (напряжение) между которыми не превышает 0,6 мВ. Как видно из таблицы, надежность контакта при соединении меди с нержавеющей сталью (потенциал 0,1 мВ) будет гораздо выше, чем с серебром (0,25 мВ) или золотом (0,4 мВ)!
А если медный провод покрыть оловянно-свинцовым припоем, то можно его смело соединять любым механическим способом с алюминиевым! Ведь тогда электрохимический потенциал, как видно из таблицы, составит всего 0,4 мВ.
Сварка и пайка алюминия. Припои и флюсы.
Пайка различных металлов и сплавов
Изделия, очищенные и подготовленные для пайки, не должны храниться продолжительное время во избежание окисления. Их следует возможно скорее загружать в печь или контейнер с обеспечением защитной среды. Особенное внимание должно быть уделено удалению воздуха при пайке высоколегированных сталей и сплавов, содержащих легкоокисляемые элементы. Удаление воздуха может достигаться вакуумированием или продуванием защитного газа — аргона. При продувании температура должна повышаться постепенно, начиная от комнатной до 800—900 С (1073— 1173 К). Этот процесс требует значительного расход аргона. Вакуумирование более рационально, так как при этом значительно снижается расход аргона. Большое значение при пайке имеет контроль температуры нагрева изделия; перегрев может оказать вредное влияние.
Общее время пребывания припоя в расплавленном состоянии состоит из времени:
t = t1 + t2 + t3
где t1 — время нагрева от температуры плавления припоя до температуры пайки; t2 — время выдержки при пайке; t3 — время охлаждения от температуры пайки до температуры кристаллизации припоя.
В случае взаимодействия припоя с основным металлом t1 и следует, возможно, сокращать. После окончания процесса панки необходимо удалить флюс, очистить окисленные поверхности, устранить наплывы и участки растекания припоя, в особенности в тех местах, которые подлежат последующей обработке. Требование удаления флюса вызвано возможным отрицательным влияние его, например появлением коррозии (в алюминиевых сплавах).
Флюсы (для пайки алюминиевого сплава) удаляют промывкой горячей и холодной водой при условии последующей обработки в растворе хромового ангидрида. Флюсы на основе буры образуют на поверхности твердую корку. Их удаляют механическим путем или погружением деталей в горячую воду. Паяные швы на алюминиевых сплавах обрабатывают металлической щеткой и вторично промывают от флюсов, могущих остаться в порах швов. Растекающийся припой удаляют механическим, химическим или электромеханическим способами.
Для контроля качества паяных соединений применяют разные методы. Существенное значение имеет внешний осмотр швов. Швы проверяются на прочность, плотность, электропроводность. Паяные швы можно контролировать физическими методами: рентгеновским просвечиванием, применением радиоактивных изотопов, прозвучиванием.
Кроме испытания паяных образцов без их разрушения, нередко применяют испытания с доведением их до разрушения. Результаты, полученные при испытаниях до разрушения нескольких образцов, позволяют установить механические свойства серии аналогичных изделий.
К углеродистым и низколегированным сталям относится стали, имеющие температуру плавления 1450—1520 С (1723—1793 К). При низкотемпературной пайке сталей применяются главным образом оловянно-свинцовые припои с активными флюсами. Перед пайкой рекомендуется детали облуживать. Это ускоряет процесс пайки и позволяет обеспечивать высокие механические свойства соединений.
Более часто для пайки сталей применяют высокотемпературные медно-цинковые припои с добавкой серебра (температура плавления 940—700 С (1213—973 К). Однако вследствие легкого испарения цинка эти припои не применяют для вакуумной панки. Их целесообразно использовать при пайке в среде с низкими окислительными свойствами, например продуктов неполного сгорания азотно-водородной смеси с флюсом в виде буры, борного ангидрида и т. д. Для пайки углеродистых сталей в качестве припоя применяют также чистую медь, в особенности при пайке в печах в среде водорода. Медь хорошо растекается, заполняет малые зазоры. При этом прочность соединений превосходит прочность самой меди.
К высоколегированным сплавам относятся коррозионно-стойкие аустенитные стали 0Х18Н9, 12Х18Н9 со стабилизирующими добавками — титаном, ванадием, ниобием и т. д., кислотоупорные хромистые стали Х17, Х25 и другие ферритного класса, жароустойчивые никелевые сплавы, например, имеющие около 80% Ni и др.
Указанные сплавы могут паяться легкоплавкими припоями с применением активных флюсов. Однако пайка легкоплавкими припоями указанной группы сплавов технически нецелесообразна. Рациональнее применять для их соединений высокотемпературные припои (табл. 1).
В соответствии с маркой припоя применяются флюсы с различными составляющими. Некоторые припои при быстром нагреве т. в. ч. теряют свои составляющие.
Высоколегированные сплавы и стали можно паять в среде аргона, водорода, в вакуумных печах, Недостаток пайки в аргоне — не вполне удовлетворительная растекаемость припоя. Для улучшения растекаемости во флюсы вводят добавки, например литий. Пайка в атмосфере водорода требует высокой его чистоты; использование водорода всегда сопряжено с некоторой опасностью взрыва.
Пайка в вакууме дает хорошие результаты при применении припоев, не содержащих легко испаряющихся элементов (цинка и др.). При пайке указанных выше материалов могут возникать поры вследствие испарения некоторых составляющих припоя, например, цинка: непровары в результате неудовлетворительного смачивания расплавленным припоем соединяемых частей или недостаточной очистки поверхностей; трещины при проникновении жидкого припоя между границами зерен основного металла. Особенно часто образуются трещины при пайке медно-цинковыми и медно-серебряными припоями. Применением более высокотемпературных припоев можно избежать растрескивания паяных соединений.
Таблица 1. Состав припоев, %
Применение никелевых припоев иногда сопровождается образованием подрезов основного металла в местах перехода к швам. Это происходит вследствие того, что припой этого рода имеет способность растворять основной металл. Чтобы избежать этого явления, следует вести технологический процесс пайки при возможно более низкой температуре.При помощи пайки хорошо соединяются изделия из чистой меди и медных сплавов. Чистая медь хорошо паяется при нагреве в вакуумных печах, а также в атмосфере хорошо очищенного водорода без каких-либо примесей кислорода. Медно-цинковые сплавы, содержащие 4—38% Zn, при длительном нагреве теряют его (цинк испаряется), поэтому латунные детали перед пайкой целесообразно покрывать медью.
Пайка широко применяется для соединений различных бронз; алюминиевых, содержащих 5—10% Аl; бериллиевых, применяемых в приборостроении и имеющих в своем составе 2—2,5% Be; хромовых, содержащих около 0,5% Сr; оловянных, применяемых при обработке давлением, содержащих олово, а также фосфор и др.
Медь и ее сплавы легко паяются при применении низкотемпературных припоев с использованием канифольных флюсов, не вызывающих коррозии. Нередко перед пайкой поверхности деталей облуживают чистым оловом слоем толщиной 0,005 мм на стали и 0,0075 мм на меди. Низкотемпературные припои не обеспечивают высокой прочности паяных соединений, поэтому рекомендуется пайка в печах высокотемпературными твердыми припоями. Целесообразно применение медно-фосфорных и серебряных припоев и флюсов на основе буры с добавлением фтористых соединений. Алюминиевые бронзы хорошо паяются серебряными припоями с никелем, который препятствует проникновению в припой алюминия и повышает производительность технологического процесса.
Титан и его сплавы паяют в электрических печах, т. в. ч., газопламенным горелками. Наилучшие механические свойства спая достигаются при пайке ТВЧ. Это объясняется тем, что в результате сокращения термического цикла при этом способе пайки отсутствует рост зерна, приводящий к охрупчиванию соединений. При пайке титановых сплавов целесообразно применять серебряные припои, имеющие температуру плавления ниже температуры рекристаллизации титана и выше температуры, требуемой для удовлетворения условий смачивания припоем паяных деталей.
Очень важная задача производства — соединение пайкой различного рода керамических материалов и окислов друг с другом и с металлами. Возможны разные случаи: металлы более тугоплавки, нежели керамика, при этом соединение обеих деталей происходит в твердом состоянии, контакт обеспечивается необходимым давлением, применением покрытий. В последнем случае соединение достигается при температурах ниже температуры плавления каждой из соединяемых деталей.
Особенно благоприятные условия для соединения, когда металлы имеют температуру плавления ниже температуры плавления керамики и в результате своих специфических химических свойств склонны к образованию связи с последней. Гак, например, титан и цирконий имеют большое сродство к кислороду и образуют твердые растворы со многими металлами и окислами. Окислы титана и циркония весьма тугоплавки. При некоторых условиях эти металлы восстанавливают окислы металлов, образующих керамику, и присоединяют к себе освобожденный кислород. Такое восстановление, необходимое для прессовой пайки, следует проводить в условиях вакуума или в среде аргона.
Серьезные затруднение пайки керамик с металлами — существенная разница в их температурных коэффициентах расширения, в результате чего в соединениях образуются остаточные напряжения значительной величины. В неблагоприятных случаях, при недостаточной пластичности материалов в них возникают трещины. Для устранения этого явления иногда между соединяемым металлом и керамикой прокладывают пластины из пластичного металла, например молибдена. При пластических деформациях последнего опасность возникновения трещин в керамике значительно уменьшается.
С помощью специальных присадочных металлов можно получать качественные соединения не только однородных элементов, например Al2O3 + Al2O3, но и разнородных. Сплавы, содержащие сильные карбидообразующие элементы — молибден, тантал, титан, цирконий и др., – хорошо смачивают графит.
Припои и флюсы для пайки
Большинство способов пайки осуществляют с применением различных припоев и лишь в тех случаях, когда в процессе пайки между металлами могут образоваться легкоплавкие эвтектики, пайка возможна без специального припоя.
К припоям предъявляют ряд требований общего характера. Припой должен хорошо растекаться по поверхности основного металла, смачивать и растворять его, легко заполнять зазоры между деталями, обеспечивать необходимую прочность соединения и т. п.
Припои применяют в виде лент, паст, прутьев. Особенно распространены припои в виде проволочных контуров и прокладок из фольги, штампуемых в соответствии с поверхностью соединяемых частей.
Широкое применение в качестве припоев получили высокотемпературные припои — сплавы на основе серебра, алюминия, меди и др., обладающие, как правило, температурой плавления выше 450—500 С (723—773 К). Медно-цинковые припои ПМЦ 36, ПМЦ 48, ПМЦ 54 имеют предел прочности σв = 21-35 кгс/мм2 (206,0—343,2 МН/м3), относительное удлинение до 26%, рекомендуются для пайки изделий из меди, томпака, латуни, бронзы. Серебряные припои имеют температуру плавления 740—830 С (413—1103 К). Согласно ГОСТ 8190-56 марки припоев разделяют в зависимости от содержания в сплавах серебра, которое изменяется в пределах от 10 (ПСр 10) до 72% (ПСр 72). В них также содержатся цинк, медь и в небольшом количестве свинец. Эти припои применяют для пайки тонких деталей, соединения медных проводов и в случаях, когда место спая не должно резко уменьшать электропроводность стыковых соединений.
Низкотемпературные припои имеют температуру плавления ниже 450—400 С (723—673 К). Они обладают небольшой прочностью. Их применяют для пайки почти всех металлов и сплавов в разных их сочетаниях. В большинстве случаев низкотемпературные припои содержат значительный процент олова.
Низкотемпературные оловянно-свинцовые припои (ГОСТ 1499—70) имеют верхнюю критическую точку плавления 209—327° С (482—600 К). Олово имеет точку плавления 232 С (505 К). Его предел прочности при растяжении 1,9 кгс/мм2 (18,6 МН/м2), относительное удлинение 49%, НВ 6.2 кгс/мм2 (60,8 МН/м2). Оловянно-свинцовые припои ПОС-90, ПОС-61, ПОС-40 и др. применяют при пайке медных аппаратов, авиационных радиаторов, изделий из латуни и железа, медных проводов и т. д.
Образование качественного паяного соединения в значительной степени зависит от возможности наиболее полного удаления с поверхности металла окисных, адсорбированных газовых и жидких пленок. В практике пайки для удаления поверхностных пленок применяют различного рода флюсы, восстановительную атмосферу или вакуум. В последнее время для этой цели успешно используют механическое разрушение пленок с помощью ультразвуковых упругих колебаний.
Флюсы при пайке имеют несколько назначений. Они защищают основной металл и припои от окисления, растворяют или восстанавливают образовавшиеся окислы, улучшают смачивание поверхностей, способствуют растеканию припоев. Флюсы можно применять в твердом, жидком и газообразном виде (в виде порошков, паст, растворов газов). Роль флюса выполняют некоторые специальные газовые атмосферы и вакуум, которые также могут способствовать восстановлению окислов и улучшению условий смачивания. Флюсующее действие оказывают в некоторых случаях отдельные составляющие, входящие в состав припоев. Например, фосфористые припои не требуют флюсов при пайке медных сплавов.
Флюсы сварочные
Флюсами называют специально приготовленные неметаллические гранулированные порошки с определенным размером зерен.
Назначение флюсов – расплавляясь, они создают шлаковый купол над зоной дуги, а после химико-металлургического воздействия образуют шлаковую корку на поверхности, в ней остаются окислы, вредные примеси и газы.
Флюсы делят на неплавящиеся, керамические и плавильные.
Керамические флюсы.
Изготавливают так же, как и электродное покрытие.
Сухие компоненты шихты замешиваются в жидком стекле. Полученную массу измельчают путем продавливания. Потом прокаливают, просеивают для получения частиц определенного размера.
Частицы сухой смеси могут быть скреплены за счет спекания. Происходит это при повышенных температурах без расплавления. Затем гранулируют до необходимого размера.
Не плавильные флюсы приготавливаются в виде механической смеси. Наиболее распространенны керамические флюсы. По составу близки к составу основного покрытия.
Легирование металла флюсом достигается путем введения в их состав ферросплавов.
Сочетание легирующих элементов может быть различно, а это позволяет получать практически любой состав металла шва.
Это наиболее характерная особенность керамических флюсов.
Химический состав шва также зависит от параметров сварки.
Чтобы определить, как изменились свойства шва, надо замерить твердость в различных местах.
Наиболее критичная зона – зона сплавления и околошовная зона. Керамические флюсы имеют и свои недостатки: малая прочность, вследствие чего в процессе транспортировки или эксплуатации меняют свою грануляцию.
Часто применяют для сварки высоколегированных и специальных сталей, а также для наплавочных работ.
Плавильные флюсы.
Сплавы оксидов и солей металлов. Процесс их изготовления включает следующие стадии:
1. Расчет и подготовка шихты.
2. Выплавка флюса.
3. Грануляция.
4. Сушка, если использовалась мокрая грануляция.
5. Просеивание.
Предварительно измельченные части флюса загружают в дуговые или плавильные печи. После расплавления и выдержки до окончания реакции при температуре 1400 C флюс выпускают из печи.
При сухой грануляции флюс выливается в металлические формы. После остывания отливка дробится, при этом используются валки. Размер частиц 0,1-3 мм. Затем флюсы просеивают.
Сухая грануляция применяется для гигроскопических флюсов, содержащих большое количество фтористых и хромистых солей.
Преимущество этих флюсов в том, что они могут быть использованы несколько раз.
Используют для сварки алюминиевых и титановых сплавов.
Мокрый способ грануляции: расплавленный флюс выпускается из печи достаточно тонкой струей и попадает в емкость с проточной водой. В ряде случаев используют дополнительную струю воды.
Далее идет просеивание.
Получают различную грануляцию. Флюс сушат при температуре 250-300 C, а после дробят, если возникает необходимость. После этого просеивают.
Флюс представляет из себя неровные зерна светло-серого, красно-бурого и коричневого цвета.
Транспортируют в герметичной таре, полиэтиленовых мешках, бочках.
Плавильный флюс не может содержать легирующих элементов в чистом виде, так как они окисляются в процессе изготовления. Поэтому легирование происходит путем восстановления окислов флюсов.
В основу классификации флюсов по химическому составу положено содержание в нем оксидов и солей.
Различают окислительные флюсы, имеющие оксид марганца и кремния в составе.
Для получения определенных свойств флюса, в его состав вводят другие компоненты – плавиковый шпат, более прочные оксиды.
Чем больше во флюсе оксида марганца и кремния, тем сильнее он может легировать металл данными элементами, но тем больше он будет окислять этот металл.
Плавильные флюсы применяются для сварки углеродистых и низколегированных сталей.
Безокислительные флюсы практически не содержат оксидов марганца и кремния, в их состав входят фториды, используются для сварки высоколегированных сталей.
Также безокислительные флюсы могут состоять из фтористых и хлоридных солей и элементов, не содержащих кислород.
Используют для сварки высокоактивных металлов – алюминия и титана.
В связи с широким применением флюсов, есть ГОСТ на основные марки: ГОСТ 9087-81 «Флюсы сварочные плавильные».
Регламентирует химический состав.
Различают стекловидный и пемзовидный характер зерна.
Строение зерна зависит от состава расплава флюса, степени его перегрева.
В зависимости от этого, флюс может получаться плотным, прозрачным, пористым, рыхлым.
Следует учитывать, что пемзовидный флюс при том же химическом составе, имеет в полтора-два раза меньший вес, чем стекловидный.
Данные флюсы хуже защищают металл от воздействия воздуха, но обеспечивают хорошее формирование шва при больших плотностях тока и скоростях сварки.
Буквы в обозначениях флюсов:
- М – мелкий
- С – стекловидный
- П – пемзовидный
- СП – смешанный
Сварка под флюсом
На первый взгляд может показаться, что одно из основных преимуществ сварки под флюсом — возможность получения большой глубины проплавления свариваемого металла — противоречит условиям сварки тонколистовой стали. Однако при определенных условиях сварка под флюсом допускает регулирование глубины проплавления металла, начиная от долей миллиметра, и поэтому хорошо известные ее достоинства могут быть использованы для сварки тонколистовой стали.
Успешное внедрение в производство сварки под флюсом изделий из тонколистовой стали стало возможным, главным образом, благодаря применению тонкой сварочной проволоки. Известны примеры сварки тонколистовой стали и обычной электродной проволокой диаметром, например, 4 мм. Однако в этом случае удавалось сваривать сталь толщиной не менее 3—4 мм при условии весьма тщательной сборки изделия.
Для сварки тонколистовой стали большое значение имеет применение приспособлений, облегчающих точную сборку изделия и обеспечивающих надежное поджатие к свариваемому стыку медной или флюсомедной подкладки, флюсовой подушки и т. п. Опыт показывает, что производительность автоматической сварки изделий из тонколистовой стали со сравнительно короткими швами зависит не столько от машинной скорости сварки, сколько от затрат времени на подготовительные и вспомогательные операции. Поэтому важной задачей является разработка эффективно действующих сборочных и сборочно-сварочных приспособлений.
Чем меньше величина тепловой энергии, передающейся от дуги основному металлу в процессе сварки, тем меньше глубина его проплавления и, следовательно, тем более тонкий металл можно сваривать без прожогов. Тепловая энергия, передаваемая основному металлу, может быть уменьшена за счет уменьшения мощности дуги или увеличения скорости ее перемещения по свариваемому соединению.
Для сварки тонколистовой стали в основном применяют уменьшение мощности дуги, а не увеличение скорости сварки. Это в значительной мере объясняется тем, что применение больших скоростей сварки (более 150—200 м/час) связано с жесткими требованиями к точности поддержания режима сварки, необходимостью тщательной очистки свариваемых кромок, с очень точной сборкой стыков, в ряде случаев со специальным наклоном изделия и электрода и т. п. При указанных скоростях сварки металл шва может быть поражен порами, поперечными трещинами и другими дефектами. Если при этом учесть, что производительность сварки тонколистовой стали, как указывалось выше, главным образом, зависит от затрат времени на установочные и подготовительные операции, то станет ясным, почему увеличение скорости не стало основным способом уменьшения погонной тепловой энергии.
Устойчивость процесса сварки
При сварке тонколистовой стали равномерность глубины проплавления имеет особенно важное значение. Если сваривая сталь толщиной более 4—5 мм, можно допустить колебание глубины проплавления в пределах ± 1 мм, не опасаясь возникновения прожогов, то в случае сварки тонких листов стали такое же колебание совершенно недопустимо.
Равномерность глубины проплавления зависит от устойчивости режима сварки, главным образом, от колебаний сварочного тока. Колебания скорости сварки, а также напряжения дуги сказываются в меньшей степени. Исходя из этого, для сварки тонколистовой стали следует рекомендовать сварочные автоматы с постоянной скоростью подачи электродной проволоки, так как они обеспечивают практически почти постоянные значения тока при колебании напряжения в сети или случайных изменениях длины дуги в процессе сварки. При этом сохраняются почти постоянной глубина проплавления, а также количество наплавляемого металла. Сварочные головки с регулируемой скоростью подачи электродной проволоки в тех же условиях не обеспечивают постоянство тока и поэтому применять их не рекомендуется.
Понижение мощности дуги, требующееся для сварки тонколистовой стали, может быть осуществлено только до определенного предела, зависящего от диаметра электродной проволоки. Дальнейшее снижение мощности резко ухудшает устойчивость процесса сварки и приводит к неудовлетворительному формированию шва. В случае сварки переменным током этот предел достигается при значительно большей мощности дуги, чем в случае сварки постоянным током обратной полярности. Поэтому сварку тонколистовой стали рекомендуется осуществлять постоянным током обратной полярности (положительный полюс присоединен к электроду). В табл. 1 приведены полученные опытным путем значения минимально-допустимых сварочных токов для электродной проволоки различных диаметров при сварке под флюсом АН-348 постоянным током обратной полярности.
Как следует из табл. 1, для обеспечения устойчивого горения дуги при понижении ее мощности необходимо увеличивать плотность тока в электроде, что практически достигается путем уменьшения диаметра электродной проволоки. Эту таблицу можно использовать для выбора диаметра электродной проволоки при сварке на заданном режиме.
При рассмотрении условий устойчивого горения электрической дуги пользуются ее статическими вольтамперными характеристиками. Вольтамперной характеристикой называется зависимость между током и напряжением дуги при постоянной ее длине. На фиг. 1 приведены такие характеристики для дуг различной длины. Каждая вольт- амперная характеристика дуги состоит из нескольких участков: падающего (с ростом тока напряжение падает), почти горизонтального (жесткий участок) и растущего (с ростом тока напряжение увеличивается). В зависимости от условии сварки, дуге соответствует тот или иной участок характеристики. Так, например, при сварке неплавящимся угольным или вольфрамовым электродом, при ручной сварке качественными электродами, при автоматической сварке под флюсом со сравнительно небольшой плотностью тока и в некоторых других случаях характеристика сварочной дуги является падающей с переходом к жесткой. При сварке под флюсом или в защитной газовой среде с повышенной плотностью тока в плавящейся электродной проволоке характеристика дуги становится растущей.
Если дуга имеет падающую вольтамперную характеристику, то устойчивое ее горение возможно только при том условии, что внешняя характеристика сварочного генератора также будет падающей, т. е. напряжение холостого хода генератора значительно превышает напряжение дуги при сварке.
С ростом плотности тока в плавящемся электроде изменяются свойства сварочной дуги. Эти изменения настолько существенны, что позволяют предъявить совершенно другие требования к характеристикам источников питания постоянного тока.
Еще в 1950 г. в Институте электросварки им. Е. О. Па- тона было доказано, что при повышении плотности тока в плавящемся электроде может быть получен устойчивый процесс сварки при использовании в качестве источника питания генератора постоянного тока с жесткой внешней характеристикой (напряжение холостого хода генератора практически равно напряжению дуги при сварке). В отечественной и зарубежной практике в последние годы такие генераторы нашли широкое применение.
Генераторы с жесткими внешними характеристиками значительно более экономичны, чем обычные сварочные генераторы с крутопадающими характеристиками и высоким напряжением холостого хода, так как пропорционально снижению напряжения холостого хода генератора снижаются затраты на активные материалы, уменьшается вес генератора и его стоимость.
Чем больше скорость подачи электродной проволоки п меньше сварочный ток, тем труднее возбудить дугу путем непосредственной подачи электродной проволоки к изделию. Опыт показывает, что при использовании обычных сварочных генераторов с крутопадающей внешней характеристикой в ряде случаев этот способ возбуждения дуги практически оказывается неосуществимым. Совершенно иное наблюдается в случае применения генераторов с жесткими внешними характеристиками. Резкое нарастание тока при закорачивании электрода на изделие обеспечивает безотказное возбуждение дуги. Короткое замыкание не наносит ущерба генератору, так как тонкая электродная проволока выполняет роль плавкой вставки в цепи, ограничивая время протекания и величину тока короткого замыкания.
В тех случаях, когда генераторы с жесткими внешними характеристиками по какой-либо причине не могут быть применены для сварки тонкого металла, следует применять генераторы с весьма пологопадающими характеристиками, т. е. с большой величиной тока короткого замыкания.
Чем резче изменяется ток в цепи при случайных изменениях длины дуги, тем интенсивнее протекают процессы саморегулирования и тем быстрее восстанавливается заданный режим сварки. Генераторы с крутопадающими внешними характеристиками дают значительно меньшие изменения тока при случайных колебаниях длины дуги, чем генераторы с пологопадающими, жесткими или растущими характеристиками, благодаря чему обеспечивают большую устойчивость процесса сварки тонкой электродной проволокой.
Весьма характерно влияние внешних характеристик генераторов на процесс сварки и формирование шва при изменении величины зазора в соединении. Опыт показывает, что в случае питания дуги от генераторов с жесткой или пологопадающей внешней характеристикой можно допустить большие по величине зазоры в стыке, не нарушая нормального формирования шва. Такое же явление наблюдается при увеличении плотности тока в электроде.
В табл. 2 приведены режимы сварки стыковых соединений стали толщиной 3 мм, собранных с постепенно возрастающим зазором от 0 до 5 мм при длине образцов 500 мм. Образцы сваривались электродной проволокой диаметром 3 мм при питании от генератора с крутопадающей внешней характеристикой и генератора с пологопадающей характеристикой. Один из образцов был сварен электродной проволокой диаметром 1,6 мм при питании от генератора с крутопадающей характеристикой. Как следует из табл. 2 и фиг. 2, где изображены образцы сварных соединений, в случае внешней характеристики генератора, приближающейся к жесткой (пологопадающей), а также в случае большей плотности тока в электроде (меньший диаметр электрода), максимальный зазор, при котором еще происходит правильное формирование шва, значительно больше.
Не следует считать, что приведенные в таблице максимальные зазоры могут быть рекомендованы как допустимые при сборке стыков. В данном случае имеет место плавное возрастание зазора, что не равноценно резким изменениям зазоров, которые могут наблюдаться в практике.
Влияние формы внешней характеристики, а также плотности тока на формирование швов при сварке с зазорами в стыке связано, по-видимому, с изменением интенсивности процессов саморегулирования.
При автоматической сварке стыкового соединения одно из активных пятен дуги расположено на расплавленном металле ванны, заполняющей разделку. В отдельные моменты времени скорость перемещения ванны расплавленного металла может отличаться от скорости движения электрода вдоль стыка. Одной из причин этого бывает изменение величины зазора между свариваемыми кромками или изменение зазора между подкладкой и свариваемыми листами.
При увеличении зазора в стыковом соединении или возникновении большего зазора между подкладкой и свариваемыми листами скорость перемещения ванны расплавленного металла уменьшается. Так как скорость движения электрода при этом остается прежней, имеет место рост дугового промежутка. Резкое увеличение дугового промежутка вызывает обрыв дуги и нарушение процесса сварки. При плавном удлинении дуги процесс может не нарушиться, активное пятно успеет занять новое положение, обеспечивая восстановление прежней длины дуги.
Если питание дуги осуществляется от генератора с крутопадающей внешней характеристикой, то при удлинении дуги, как показали исследования, наблюдается рост ее мощности, что ведет к дополнительному оплавлению кромок в месте повышенного зазора, где начала удлиняться дута. При этом электродного металла окажется недостаточно для заполнения зазора между оплавленными кромками, в результате чего образуется не заполненный металлом участок — прожог.
Увеличение интенсивности саморегулирования дуги, имеющее место в случае применения генераторов с жесткими внешними характеристиками или при повышенной плотности тока в электроде, в известных пределах может предотвратить возникновение прожогов. Благодаря интенсивному саморегулированию значительное удлинение или обрывы дуги не будут наблюдаться при отставании ванны жидкого металла в месте увеличившегося зазора. При этом длина дуги будет поддерживаться постоянной и опасный участок с увеличенным зазором может быть пройден без нарушения процесса сварки (без обрывов дуги, прожогов и пр.). Этот участок от остальной части шва будет отличаться только меньшим усилением шва или даже полным отсутствием усиления.
Как известно из практики автоматической сварки под флюсом, с увеличением плотности тока в электроде глубина проплавления заметно возрастает. Например, при сварке на токе 500 а увеличение плотности тока приблизительно в 3 раза, за счет уменьшения диаметра электродной проволоки от 5 до 3 мм, вызывает увеличение глубины проплавления на 25%. Так как переход к сварке тонкой электродной проволокой связан с еще большим увеличением плотности тока в электроде, то возникает опасение, не может ли интенсивный рост глубины проплавления в этом случае стать препятствием на пути применения тонкой электродной проволоки и повышенной плотности тока для сварки тонколистовой стали. Проведенные опыты показали, что это опасение несостоятельно.
На фиг. 3 приведен график зависимости глубины проплавления от диаметра электродной проволоки. Как видно из графика, рост глубины проплавления с увеличением плотности тока (уменьшением диаметра электрода) наблюдается только при сварке на токах, превосходящих 300—350 а. Что же касается интересующего пас диапазона токов, применяемых для сварки тонкой стали (до 300—350 а), то в нем увеличение плотности тока не вызывает изменения глубины проплавления. Это объясняется некоторыми особенностями, отличающими маломощные электрические дуги от дуг большей мощности.
Материал с сайта: http://ruswelding.com
Как паять сталь, медь, алюминий и сплавы в домашних условиях?
Как паять сталь, медь, алюминий и сплавы в домашних условиях?На сегодняшнее время существует два самых распространённых способа соединения металлов — это пайка и сварка. Последняя технология связана с использованием сварочной дуги и газа.
Сложность сварки обусловлена и применением специального оборудования предназначенного для этих целей. Поэтому в домашних условиях наибольшее распространение получила именно пайка металлов.
И если перед вами остро стоит вопрос запаять кастрюлю или спаять провода, то вы должны освоить технологию пайки металлов. Используя припой и флюс, можно легко паять такие металлы, как медь с алюминием. Также пайке поддаются и изделия, которые были изготовлены из стали.
Само собой разумеется, что для всех вышеперечисленных металлов применяются свои определенные флюсы с припоями. Какие именно, и как правильно паять, вы сможете узнать из этой статьи.
В чем преимущества пайки металлов перед свариванием?
Рассмотрим, а какие же именно преимущества нам дает пайка металлов, в отличие от сварки:
- Первое и самое главное преимущество заключается в том, что спаиваемые металлы не нагреваются до температуры плавления. Плавится только припой. В результате этого не нарушаются химические свойства металлов, они не теряют своих характеристик;
- Перед пайкой металлов нет необходимости более тщательно подготавливать заготовки, как это делается в случае сварки;
- Можно использовать простое и неприхотливое оборудование для пайки, которое не такое требовательное к питанию домашней электросети.
Ну и что касается прочности пайки, то она практически ничем не уступает сварке. Таким образом, пайка металлов является отличным вариантом для выполнения ремонтных работ или изготовления сложных конструкций.
Как паять цветные металлы: медь, латунь и алюминий
Пайка цветных металлов происходит с использованием высоко- и низкотемпературных припоев. Помимо олова и свинца, в составе припоев для пайки цветных металлов могут содержаться висмут, сурьма, селен, а также серебро и другие компоненты.
Изделия из цветных металлов требуют более тщательной подготовки. Важная особенность любой пайки металлов заключается в том, чтобы избежать любой подвижности в процессе соединения металлов. Именно по этой причине заготовки во время пайки следует надежно фиксировать на столе, особенно если речь идёт о габаритных изделиях.
Как паять черные металлы
Изделия из черных металлов также неплохо поддаются спаиванию. Для их соединения применяются оловянные и латунные припои. Соединение получается достаточно прочным на разрыв, а также стойким к механическому роду повреждениям.
Технология пайки черных металлов практически ничем не отличается от технологии спаивания изделий из меди, алюминия или латуни. Здесь всё также необходимо подготовить поверхности: очистить их от ржавчины, грязи, жирных пятен.
Если пайка стали осуществляется обычным паяльником, то нужен будет инструмент, мощность которого составляла бы не менее 100 Вт. В противном случае паяльник не сможет достаточно хорошо нагреть спаиваемые заготовки, что негативным образом скажется на прочности полученного соединения.
Вопрос: Как паять алюминий? – Дом и сад
Содержание статьи:
Как обычной турбогорелкой паять алюминий.
Видео взято с канала: Glavnyiy Mehanik
✔️КАК ПАЯТЬ ЗАЛУДИТЬ АЛЮМИНИЙ | ЛЕГКИЙ СПОСОБ | ПАЙКА ЛУЖЕНИЕ АЛЮМИНИЯ паяльником БЕЗ ГОРЕЛКИ
Видео взято с канала: Evseenko Technology
ПАЙКА АЛЮМИНИЯ. АРГОН НЕ НУЖЕН!
Показать описание⇒ Нашел припой на Алиэкспресс, 20шт: http://ali.pub/4516ly еще 10-20-50шт: https://ali.ski/BlSC7.
ВНИМАНИЕ! На Али есть лоты дешевле 2-3 доллара, но это продают просто проволоку без флюса!
Привет друзья! В этом видео покажу как можно просто и дешево паять алюминий без использования аргона. Шов получается прочный, аккуратный и герметичный..
В видео используется припой марки CASTOLIN 192, еще можно использовать HTS-2000. Припой продается в магазинах с медными трубками и радиаторами..
Покупал тут: “Магазин медных труб”, Московская обл, г. Реутов, шоссе Энтузиастов, владение 19. Торговый комплекс ‘Владимирский Тракт’, пав. 28Ф, сайт: http://eurometalgroup.ru (звонить им смысла нет, просто приезжаете в точку продаж и покупаете, на сайте несколько адресов).
♦♦♦♦♦♦♦♦♦♦♦♦♦♦♦♦♦♦♦♦♦♦♦♦.
⇒ Скидка от 5% на все товары Алиэкспресс: http://voltnik.ru/cashback.
⇒ Видео о том как работает скидка: https://youtu.be/D959at2-ChY.
⇒ Мобильное приложение EPN cashback: http://voltnik.ru/cash-mobile.
♦♦♦♦♦♦♦♦♦♦♦♦♦♦♦♦♦♦♦♦♦♦♦♦.
Мой профиль на ThinkerCAD: https://goo.gl/ee2ExZ.
ALIEXPRESS: http://voltnik.ru/aliexpress.
BANGGOOD: http://voltnik.ru/bngd.
GEARBEST: http://grbe.st/XBBp5O.
♦♦♦♦♦♦♦♦♦♦♦♦♦♦♦♦♦♦♦♦♦♦♦♦.
✔ Группа ВК: https://vk.com/voltnik.
✔ Сайт канала: http://voltnik.ru/.
#voltnikИнструменты
Видео взято с канала: voltNik
ПАЙКА АЛЮМИНИЯ БЕЗ АРГОНА! В домашних условиях.

Видео взято с канала: Сам себе КОЛХОЗНИК
как запаять алюминий оловом
Видео взято с канала: АС МАСТЕР ремонт авто в омске
Паять алюминий? Легко!
Видео взято с канала: MotoDalnoBoy
Как припаять к алюминию? Легко. Нужен только паяльник! Без флюсов, без горелки!
Видео взято с канала: Lithium Master
HVAC Соединение алюминия с медью
Целостность соединения меди с алюминием
Производители HVAC, оценивающие использование алюминиевых компонентов, должны рассмотреть лучший метод соединения деталей, таких как змеевики испарителя и конденсатора, с линиями или сборками вторичной меди. Можно использовать несколько методов соединения, в том числе: клеи, механическое соединение, ультразвуковое соединение, пайку и пайку.
При пайке или пайке необходимо контролировать несколько параметров, чтобы гарантировать надлежащую целостность соединения:
- Конструкция соединения (зазор стыка, глубина сдвига и ориентация Cu-Al)
- Материалы для пайки или пайки (сплавы и флюсы)
Отраслевые стандарты в настоящее время недоступны, и рекомендации различаются. Чтобы помочь производителям в решении этой проблемы, Lucas-Milhaupt провела испытания, в которых изучается влияние различных конструкций соединений и типов припоев / расходных материалов на общее качество переходных соединений меди с алюминием.
Процесс испытаний
Серия образцов с различными зазорами в стыках была паяна / паяна горелкой с использованием сплавов Al / Si и Zn / Al с некоррозионными флюсами. Затем образцы были испытаны механически и под давлением, чтобы определить качество соединения.Металлургические исследования были выполнены для характеристики качества пайки / припоя для каждого семейства соединений.
В таблице 1 показаны комбинации сплав / флюс в форме сердечника из флюса, которые были оценены в ходе этого исследования.
Таблица 1. Распространенные сплавы, используемые для соединения Cu с Al
Переходные муфты медь-алюминий часто используются для подключения полностью алюминиевых компонентов к вспомогательным медным линиям. Из-за рабочего давления до 35 бар (500 фунтов на квадратный дюйм) прочные герметичные соединения являются основным фактором при выборе конструкции соединения, метода соединения и расходных материалов.Для сплавов, представленных в таблице 1, были проведены испытания на растяжение, сдвиг и давление для соединений пайки / пайки с различными зазорами.
Зазоры в стыках и результирующая прочность
Были проведены два отдельных испытания прочности для оценки влияния выбора сплава и зазоров в стыках на итоговую прочность соединения меди с алюминием:
1. В первом испытании стандарт AWS C3.2 использовался в качестве руководства для оценки прочности паяных / паяных соединений.Сборки нагревали кислородно-ацетиленовым пламенем до тех пор, пока оба основных металла не достигли температуры пайки, а затем нанесли твердый припой / припой на поверхность стыка.
После того, как сборки были спаяны и подготовлены к испытаниям, четыре образца на растяжение для каждого набора зазоров в стыках и использованных расходных материалов были испытаны на растяжение. Значения разрывной нагрузки для каждого набора образцов были записаны и использованы для расчета результирующего напряжения сдвига в присадочном металле. Данные были собраны для зазоров швов 0 мм (0.000 дюймов), 0,08 мм (0,003 дюйма) и 0,15 мм (0,006 дюйма). Средние значения напряжения сдвига, полученные для всех комплектов испытанных образцов, показаны на рисунке 1.
Рис. 1. Средняя прочность на сдвиг в зависимости от типа сплава и толщины соединения
Результаты показывают, что самая высокая прочность на сдвиг была достигнута с сплавом 98Zn / 2Al для каждого из трех испытанных зазоров в стыках. Разница в прочности, наблюдаемая между этим сплавом и сплавами с более высоким содержанием алюминия, может быть связана с возможностью образования хрупких интерметаллидов между припоями с более высоким содержанием алюминия и медным основным материалом, как указано Berlanga-Labari et al.Среди испытанных зазоров в швах 0,08 мм и 0,15 мм обеспечили наиболее стабильное качество и прочность шва. Незначительный зазор в стыке или его отсутствие приводили к избыточным пустотам для флюса и ограниченному заполнению сплавом, что, в свою очередь, снижало целостность и прочность соединения.
2. Второе испытание на прочность оценивало паяные / паяные сборки «труба-труба», соединенные с помощью различных комбинаций сплавов и зазоров между стыками. Считалось, что этот тест более репрезентативен для того, что наблюдается в промышленности для переходных соединений медь-алюминий.В результате проведенного выше испытания на прочность на сдвиг были выбраны зазоры в стыках 0,08 мм (0,003 дюйма) или 0,15 мм (0,006 дюйма). Сборки нагревали пламенем природного газа / кислорода до тех пор, пока оба основных металла не достигли температуры пайки, а затем нанесли твердый припой / припой на поверхность стыка.
После соединения четыре образца между трубками для каждого набора зазоров в стыках и расходных материалов были испытаны на растяжение универсальным прибором для испытания на растяжение под нагрузкой 60 К. Паяные / спаянные сборки тянули до отказа.Разрушение всех комплектов образцов произошло в образцах алюминий-основной металл. Хотя всегда в материале на основе алюминия, место разрушения зависит от типа сплава, используемого для соединения. Все образцы, спаянные сплавом 98Zn / 2Al, вышли из строя примерно на 12-25 мм (0,5-1 дюйм) над швом, в то время как образцы, спаянные сплавом 88Al / 12Si, разрушились в алюминии непосредственно над паяным швом. Различие в месте разрушения, вероятно, связано с более высокой температурой и повышенным взаимодействием сплава (эрозией), наблюдаемым со сплавом 88Al / 12Si.Образцы, соединенные сплавом 78Zn / 22Al, показали смесь разрушения алюминия и основного материала над паяным соединением и непосредственно рядом с пайкой.
Значения разрывной нагрузки для каждого набора были записаны и использованы для расчета результирующего растягивающего напряжения в алюминиевом основном металле при разрушении. Данные были собраны для зазоров в стыках 0,08 мм (0,003 дюйма) и 0,15 мм (0,006 дюйма). Средние значения растягивающего напряжения, полученные для всех комплектов испытанных образцов, показаны на Рисунке 2 и нанесены на график.
Результаты показывают, что самый высокий предел прочности на растяжение при зазоре 0,08 мм был достигнут со сплавом 98Zn / 2Al, в то время как самый высокий предел прочности при зазоре 0,15 мм был получен со сплавом 78Zn / 22Al. .
Зазоры в стыках и сопротивление давлению
Компоненты HVAC часто представляют собой закрытые системы, требующие герметичных герметичных соединений. Это относится к переходным соединениям алюминий-медь, которые обычно используются для подключения змеевиков испарителя и конденсатора к медным жидкостным и всасывающим линиям.Рабочее давление для этих систем различается в зависимости от типа используемого хладагента, но обычно находится в диапазоне 20-35 бар (290-500 фунтов на кв. Дюйм). Принимая во внимание этот диапазон, была подготовлена серия образцов, которые прошли контрольные испытания и находились под давлением до разрушения. Подготовленные и соединенные трубчатые образцы имели те же основные материалы и размеры, что и для испытаний на растяжение трубной сборки.
Таблица 2. Сводка результатов испытаний под давлением
Примечание 1: испытательный образец не прошел в галтели шва при 131 бар (1900 фунт / кв. Дюйм)
Примечание 2: испытательный образец не прошел в галтели шва при 138 бар (2000 фунт / кв. Дюйм)
Примечание 3: Образец для испытаний разрушился в основном металле алюминия при 164 бар (2384 фунт / кв. Дюйм)
Как видно из таблицы 2, давление разрыва, превышающее 173 бар (2500 фунтов на квадратный дюйм), было реализовано в большинстве испытанных паяных / паяных сборок.Отказы при этих давлениях произошли как в основном алюминии, так и в галтели стыков для сборок, соединенных сплавами 88Al / 12Si и 98Zn / 2Al, тогда как сборки, спаянные со сплавом 78Zn / 22Al, вышли из строя только в основном алюминиевом материале. Многие производители считают давление разрыва 138–173 бар (2000–2500 фунтов на кв. Дюйм) приемлемым минимумом для отказа полностью алюминиевых компонентов. Все переходные соединения, испытанные в ходе этого исследования, кроме одного, соответствовали этому диапазону или превышали его. Один образец, вышедший из строя при давлении ниже 173 бар (2000 фунтов на квадратный дюйм), был соединен с 88Al / 12Si при номинальном зазоре 0.006 дюймов с каждой стороны.
Сравнение качества соединений
Срезы паяных / припаянных образцов на сдвиг и растяжение были сохранены и подготовлены для металлургического исследования, чтобы оценить качество соединения для различных сплавов и конфигураций соединений.
Общее качество соединения было наиболее стабильным для соединений, спаянных с использованием 98Zn / 2Al. Эти соединения показали наименьшую пористость, наряду с ограниченным взаимодействием наполнитель / основной металл. Полное проплавление шва наблюдалось с 98Zn / 2Al с некоторой газовой пористостью.Все стыковые зазоры, спаянные сплавом 78Zn / 22Al, показали значительную сферическую и неравномерную пористость, которая обычно указывает на захват газа или флюса и усадочные пустоты соответственно. Комбинация этих двух пустот может увеличить вероятность открытия пути утечки во время работы под давлением.
Паяные соединения, выполненные из сплава 88Al / 12Si во время этих испытаний, показали только сферическую пористость, которая чаще всего обнаруживалась на границе раздела медь / наполнитель. Эта испытательная группа также показала наибольшее количество взаимодействий между наполнителем и основным металлом или эрозии среди испытательной группы.Это взаимодействие усиливается при использовании чрезмерных температур пайки, что часто можно увидеть при более высокой температуре ликвидуса этого сплава. Хотя герметичность этого сплава может быть хорошей, целостность / прочность основного металла может быть нарушена из-за этой эрозии.
Как наблюдалось на образцах для испытаний на сдвиг, аналогичные особенности соединения, связанные с взаимодействием сплавов, газовой пористостью и усадочными пустотами, также наблюдались в сборках припой / паянная труба-труба. В целом, несоблюдение согласованных зазоров в стыках с каждой стороны привело к несоответствию в величине вытягивания сплава и взаимодействия основного металла.
Выводы
На основании данных и визуальных наблюдений, обсужденных выше, в таблице 3 представлена качественная оценка переходных соединений медь-алюминий, изготовленных с использованием трех различных испытанных присадочных металлов.
Таблица 3. Качественный рейтинг протестированных систем из сплавов
Мы надеемся, что это исследование поможет вам при оценке конструкций соединений и расходных материалов для пайки / пайки при соединении меди с алюминием для компонентов систем отопления, вентиляции и кондиционирования воздуха.
Вопросы? Эксперты Lucas-Milhaupt по пайке могут помочь вам решить проблемы, связанные с соединением алюминия. Для получения дополнительной информации о пайке алюминия, пайке алюминия с медью, пайке катушек HVAC и связанных процессах, пожалуйста, свяжитесь с нами. Для получения информации о продуктах для пайки алюминия Handy One® от Lucas-Milhaupt щелкните здесь.
______ [i] AWS C3. 2: 2001 Стандартный метод оценки прочности паяных соединений, Американское сварочное общество (AWS).
Пайка алюминия: основы – Weld Guru
Алюминий и алюминиевые сплавы на его основе можно паять способами, аналогичными тем, которые используются для других металлов.
Абразивная и реакционная пайка чаще применяется с алюминием, чем с другими металлами. Однако для алюминия требуются специальные флюсы. Флюсы канифоли неудовлетворительны.
Не используйте припой, если припой контактирует с уровнем нагрева, превышающим температуру плавления припоя.
На фото: алюминиевая ложа с фрезерованным пазом 0,2 дюйма. Очищение поверхности металлической щеткой из нержавеющей стали. Далее вставлен алюминий 1/8 ″. Используемые алюминиевые сварочные стержни Alumiweld требуют нагрева основных материалов примерно до 760 ° F. Как только основной материал станет достаточно горячим, паяльный стержень плавится и протекает в стык.
Пайка алюминиевых сплавов
Наиболее легко паяемые алюминиевые сплавы содержат не более 1% магния или 5% кремния.
Сплавы, содержащие большее количество этих компонентов, имеют плохие характеристики смачивания флюсом. Сплавы с высоким содержанием меди и цинка имеют плохие характеристики пайки из-за быстрого проникновения припоя и потери свойств основного металла.
МодельРебра ракеты, припаянные к трубе
Совместное проектирование
Конструкции соединений, используемые для пайки алюминиевых сборок, аналогичны тем, которые используются с другими металлами. Чаще всего используются конструкции с простыми соединениями внахлест и Т-образными соединениями.
Зазор в стыках зависит от конкретного метода пайки, состава основного сплава, состава припоя, конструкции стыка и состава используемого флюса. Однако, как правило, при использовании химических флюсов требуется зазор между стыками от 0,005 до 0,020 дюйма (от 0,13 до 0,51 мм). Расстояние от 0,002 до 0,010 дюйма (от 0,05 до 0,25 мм) используется, когда используется флюс реакционного типа.
Стыки должны плотно прилегать, но не настолько, чтобы припой не мог попасть в зазор.
Препарат
Жир, грязь и другие инородные материалы должны быть удалены с поверхности алюминия перед пайкой.
Поверхность должна быть чистой. Хорошо подойдет щетка из нержавеющей стали или стальная мочалка. В большинстве случаев требуется только обезжиривание растворителем. Однако, если поверхность сильно окислена, может потребоваться чистка проволочной щеткой или химическая очистка.
ВНИМАНИЕ
Каустическая сода или очистители с pH выше 10 не следует использовать для обработки алюминия или алюминиевых сплавов, так как они могут вступать в химическую реакцию.
Участок подготовлен проволочной щеткой из нержавеющей стали для удаления жира или масла.Паяльная лампа используется для нагрева основного металла, а затем плавления алюминиевых сварочных стержней Harbor Freight Alumiweld.
Методы пайки
Припои с более высокой температурой плавления, обычно используемые для соединения алюминиевых сборок, плюс отличная теплопроводность алюминия диктуют необходимость использования источника тепла большой мощности для доведения области соединения до надлежащей температуры пайки. Должен быть обеспечен равномерный, хорошо контролируемый обогрев.
Лужить алюминиевую поверхность лучше всего, покрыв материал лужей расплавленного припоя и затем протерев поверхность не поглощающим тепло предметом, например щеткой из стекловолокна, зубчатой деревянной палкой или волокнистым блоком.Не рекомендуется использовать металлическую щетку или другие металлические предметы. Они имеют тенденцию оставлять металлические отложения, поглощать тепло и быстро замораживать припой.
Припои
Коммерческие припои для алюминия можно разделить на три основные группы в соответствии с их температурами плавления:
- Низкотемпературные припои .
Температура плавления этих припоев составляет от 300 до 500ºF (от 149 до 260ºC). Припои этой группы содержат олово, свинец, цинк и / или кадмий и создают соединения с наименьшей коррозионной стойкостью.
- Припой для промежуточных температур . Эти припои плавятся при температуре от 500 до 700 ºF (от 260 до 371ºC). Припои этой группы содержат олово или кадмий в различных комбинациях с цинком, а также небольшое количество алюминия, меди, никеля или серебра и свинца.
- Высокотемпературные припои . Эти припои плавятся при температуре от 700 до 800ºF (от 371 до 427ºC). Эти припои на основе цинка содержат от 3 до 10 процентов алюминия и небольшое количество других металлов, таких как медь, серебро, никель; и железо для изменения их характеристик плавления и смачивания.Припои с высоким содержанием цинка обладают наивысшей прочностью по сравнению с алюминиевыми припоями и образуют наиболее стойкие к коррозии паяные сборки.
Правила пайки алюминия
- Перед тем, как приступить к пайке алюминия, очистите металл от жира и масел
- Соединение должно быть плотным, но с зазором для припоя
- Не позволяйте деталям двигаться во время пайки, это приведет к плохому результату
- Просмотрите инструкции производителя, чтобы определить необходимое количество тепла.
- Используйте правильный флюс.
Ссылки для пайки алюминия
Процессы пайки
Пайка алюминия |
Медь имеет более высокую охлаждающую способность, чем алюминий, и является предпочтительным материалом для теплоотвода для телекоммуникаций и электроники большой мощности. Однако вес и стоимость меди ограничивают размер радиаторов. Следовательно, для больших корпусов электроники гибридная конструкция с использованием меди для локализованного радиатора, соединенного с алюминиевой рамой с хорошим тепловым контактом, может значительно улучшить охлаждающую способность корпуса радиатора.
Соединение меди с алюминием создает проблемы. Сваривать Cu и Al нелегко из-за интерметаллидов, которые образуются, когда Cu сплавляется с Al в сварочной ванне. В качестве альтернативы пайка не может быть выполнена, поскольку температура плавления алюминия ниже типичных присадочных металлов Cu-Ag для пайки (серебряные припои), используемых для пайки меди. Эти проблемы оставляют «пайку» в качестве предпочтительного процесса соединения металлических наполнителей. Но одна только пайка Cu с Al вызывает проблемы. Припои, обычно на основе Sn-Ag, не могут легко смачиваться и прилипать к алюминию без предварительного покрытия алюминия никелем или использования очень агрессивных химических флюсов, которые сами по себе несовместимы с пайкой с медью.
S-Bond Technologies, работая со своими клиентами, продемонстрировала свой активный припой S-Bond 220-50, соединяющий Cu с Al во всех конфигурациях. На рисунках ниже показан пример того, где узел радиатора с медными оребрениями был соединен S-Bond в алюминиевый корпус с оребрениями. В этой сборке медные ребра были по отдельности припаяны S-образным соединением к медному основанию радиатора, после чего сборка медного ребра-основания была затем соединена S-соединением с алюминиевым основанием при 250 ° C. Эта температура пайки значительно ниже температур размягчения алюминиевой рамы и достаточно низка, чтобы несоответствие теплового расширения между Cu и Al не искажало соединенный узел при охлаждении.
Гибридные радиаторы, сочетающие в себе тепловые преимущества меди и легкого алюминия, используют преимущества активного соединения припоем. Свяжитесь с нами, если вам нужны жесткие разнородные материалы и проблемы со склейкой меди и алюминия.
Присоединится: медь и алюминий
Сварка трением стала лучшим выбором для компаний, желающих соединить разнородные металлы. Поскольку сварка трением – это процесс соединения в твердом состоянии, который не требует плавления, он позволяет склеивать два металла, например медь и алюминий, что может быть невозможно соединить с помощью более традиционных методов сварки.
При использовании таких процессов сварки плавлением, как MIG и TIG, соединение разнородных металлов может оказаться сложной задачей, поскольку они часто существенно различаются по составу, а также физическим, механическим и металлургическим свойствам.
Медь и алюминий имеют совершенно разные температуры плавления. Медь имеет температуру плавления 1984 ° F; Алюминий имеет температуру плавления 1221 ° F.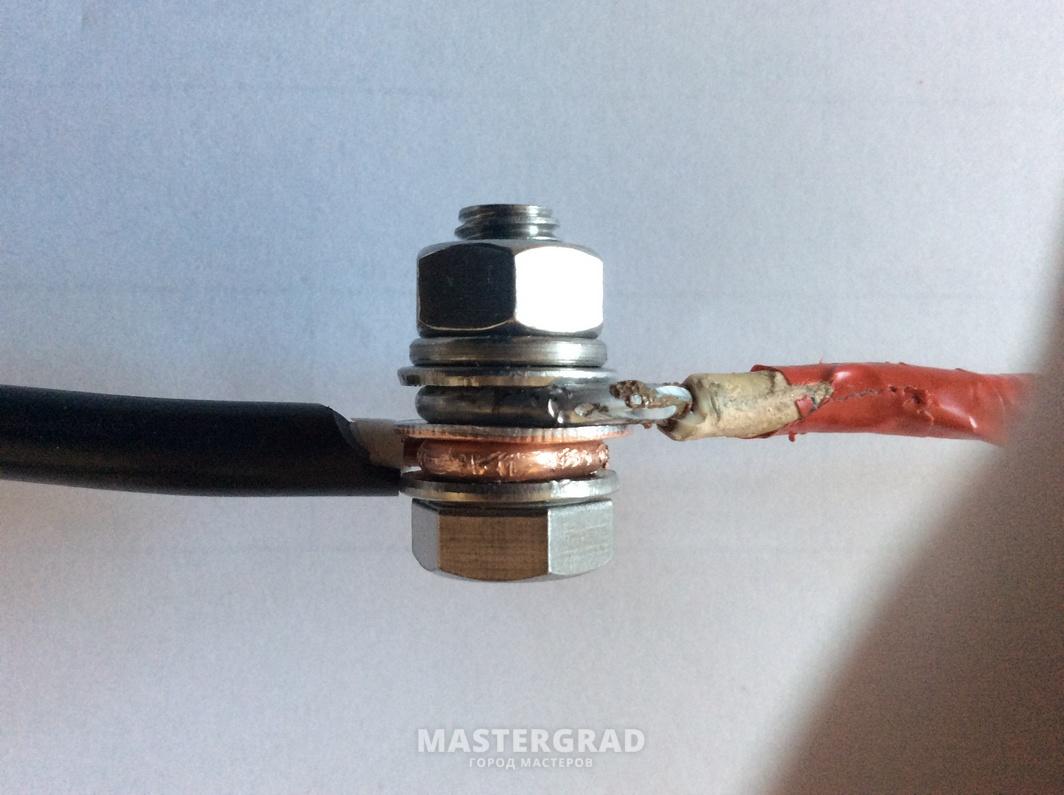
Итак, как нам более эффективно соединить эти два материала?
Сварка трением – это наиболее эффективная из имеющихся технологий биметаллического соединения. При сварке трением сварные швы имеют кованое качество, а материалы пластифицируются, а не расплавляются, что создает более прочные сварные швы, чем процессы плавления.Кроме того, правильно выполненный сварной шов трением не вызовет гальванической коррозии, также известной как биметаллическая коррозия, вокруг соединения.
Вот три распространенных способа сварки трением комбинаций меди с алюминием:
1. Линейная сварка трением медно-алюминиевой пластины теплообменника
Используя линейную сварку трением, MTI соединяет медь с алюминием, формируя пластины теплообменника для транспортных средств. В то время как медь передает тепло быстрее, чем почти любой другой металл, медь не очень хорошо или очень жестко крепится к другим поверхностям.Итак, медь приваривается к алюминию, что позволяет использовать алюминий в качестве монтажной поверхности.
2. Сварка трением медных и алюминиевых электрических компонентов при вращении
MTI использует ротационную сварку трением для соединения алюминиевых сплавов с медными сплавами для электрических соединителей. Таким образом, мы получаем преимущества теплопередачи меди в сочетании с экономией алюминия.
3. Сварка трением медных и алюминиевых кабелей аккумуляторных батарей
MTI также использует ротационную сварку трением для соединения меди с алюминием в кабелях аккумуляторных батарей.В этом случае медь и алюминий идеально подходят по разным причинам. Медь обеспечивает высокую электропроводность при небольшом сопротивлении, в то время как алюминий – гораздо более легкий металл. Заменяя алюминий на более тяжелые металлы, когда это применимо, мы можем снизить вес конечного автомобиля, что называется облегчением. Вот почему сочетание алюминия с другими материалами стало критически важным аспектом автомобильного производства.
Другие биметаллические комбинации
Загляните в наш Центр решений вместе с Дуэйном Нойербургом из MTI, чтобы увидеть некоторые из других популярных биметаллических комбинаций MTI и узнать, почему переход на биметаллическую деталь может сэкономить время и деньги компании:
Почему MTI
MTI имеет многолетний опыт работы с биметаллическими приложениями.Наш главный металлург с более чем 30-летним опытом работы вместе с инженерами-технологами разрабатывает технологию сварки. Как эксперты по сварке трением, MTI обладает знаниями, ноу-хау и сертификатами качества для решения ваших производственных проблем, а также имеет более чем 300-летний опыт комбинированной сварки трением. Мы построим машину, которая сделает вашу деталь, мы сделаем ее для вас или поможем сделать вашу деталь еще лучше.
Низкоплавкий припой – электроды и сплавы
Просмотреть техническое описание продукта
Просмотреть паспорт безопасности продукта
МЕЖДУНАРОДНАЯ КЛАССИФИКАЦИЯ |
НЕТ
Обладая более низкой температурой соединения, чем серебряные припои, он идеален в качестве промежуточного сплава для соединения.
Отлично подходит для низкотемпературных швов на:
- Алюминиевая труба, медная труба, холодильные установки и кондиционеры
- Радиаторы алюминиевые
- Работа с листовым металлом
- Изготовление и ремонт инструментов
- Литье под давлением на основе цинка
- Соединение разнородных металлов
- Может также использоваться на анодированном алюминии
Прочный низкотемпературный припой для соединения алюминия с другими металлами
– Отличные характеристики смачивания и текучести практически для всех черных и цветных металлов.
– Сохраняет высокую прочность даже при температурах до 350 ° F (175 ° C).
– Лучшая коррозионная стойкость и более высокая прочность, чем у обычных мягких припоев.
Типичные механические свойства |
Неразбавленный металл шва Максимальное значение До:
Прочность на растяжение до 20000 фунтов на квадратный дюйм (145 МПа)
Электропроводность Хорошая
Коррозионная стойкость Хорошая
Очень хорошее соответствие цветов на алюминии
Методы пайки: Зона стыка должна быть тщательно очищена.Наилучшие результаты достигаются при сохранении зазора не более 0,006 ″. Вся область стыка должна быть полностью покрыта флюсом 5140. Нагрейте деталь косвенно мягким пламенем, стараясь не поджечь флюс. Как только флюс начнет пузыриться, окуните припой во флюс и перенесите его на стык. Продолжайте нагревать, пока припой не протечет через все соединение. Дайте медленно остыть. Остатки флюса можно удалить горячей водой и жесткой щеткой.
СохранитьСохранить
Прилипает ли припой к алюминию? – AnswersToAll
Прилипает ли припой к алюминию?
Чистый алюминий можно паять, хотя работать с ним непросто.Многие алюминиевые предметы на самом деле являются алюминиевыми сплавами. Большинство из них можно припаять таким же образом, но с некоторыми из них очень трудно работать, и, возможно, придется обратиться к профессиональному сварщику.
Что будет связывать алюминий с алюминием?
Алюминий можно приклеить к другому металлическому или другому материалу с помощью клея, который обеспечит его надежность. Эпоксидный клей для металлов или водонепроницаемая эпоксидная смола связывает непористые поверхности, такие как алюминий, с другими поверхностями. Эпоксидный клей содержит пары.
Какой припой используется для алюминия?
В твердых припоях на основе цинка для активации используются флюсы, обеспечивающие более высокую температуру плавления. Остатки некоторых флюсов для мягкой пайки могут оставаться активными после пайки и должны быть удалены. Припои, используемые для алюминия, обычно содержат цинк с некоторым количеством свинца, кадмия, олова, меди или алюминия.
Подойдет ли водопроводный припой для алюминия?
Что можно использовать для склеивания алюминия?
Можно припаять медь к алюминию?
Когда его можно паять, это можно сделать только путем предварительного лужения поверхности алюминия. Также имейте в виду, что пайка алюминия с алюминием всегда является наиболее сложной задачей.Но при пайке алюминия к более удобному для пайки металлу, например, к меди, вы получаете преимущество. Подумайте, ТЕПЛО!
Можно ли паять алюминий мягким припоем?
Какой флюс используется для алюминия?
Флюсы для образования окалины способствуют отделению расплавленного алюминия, заключенного в окалине (иногда до 80%). Флюсы для образования окалины помогают снизить потери алюминия, что делает его очень экономичным, особенно при переплаве алюминиевого лома.
Пайка алюминия так же прочна, как сварка?
Правильно выполненное паяное соединение (например, сварное соединение) во многих случаях будет таким же прочным или прочным, как соединяемые металлы.Такая целостность основного металла характерна для всех паяных соединений, включая соединения как тонкого, так и толстого сечения. Кроме того, более низкий нагрев сводит к минимуму опасность деформации или коробления металла.
Вам нужен флюс для пайки алюминия?
Вы также можете использовать стержни с флюсовым покрытием, чтобы исключить этот шаг. Покрытые флюсом стержни наносят флюс во время пайки алюминия. Нагрейте отремонтированный участок пропановой или ацетиленовой горелкой, пока алюминий не станет оранжевым. Вам также понадобится флюс.
Как прикрепить алюминий к алюминию?
Алюминий можно приклеить к другому металлическому или другому материалу с помощью клея, который обеспечит его надежность.Эпоксидный клей для металлов или водонепроницаемая эпоксидная смола связывает непористые поверхности, такие как алюминий, с другими поверхностями. Эпоксидный клей содержит пары. Используйте его на улице и наденьте маску для лица и перчатки, чтобы быть особенно осторожным.
Можно ли припаять алюминий серебром?
Тот факт, что флюс достаточно прочен для пайки сплава, такого как нержавеющая сталь, не означает, что он будет работать с алюминием. Определенные комбинации присадочных сплавов, такие как олово-цинк, олово-серебро, SN100C ™ и ALUSAC-35 ™, лучше подходят для создания этой специальной связи.
Можно паять без флюса?
Ничего страшного, если можно, а без флюса паять очень сложно. Флюс разрушает оксидные слои на металлических поверхностях и позволяет припою «смачивать» их. Если он не мочится, значит, нет соединения. Обычно при пайке всегда необходимо использовать флюс.
Работает ли JB Weld для алюминия?
J-B Сварка алюминия или ЛЮБОЙ металлической поверхности, кроме свинца. JB Weld хорошо работает с алюминием. Если вы думаете, что есть вероятность того, что вы когда-нибудь захотите разделить части, используйте механический фиксатор. Мне нравится JB Weld, но теперь я использую загущенную эпоксидную смолу West Gflex для ремонта, связанного с металлом.
Какой металл нельзя паять?
Некоторые металлы паять легче, чем другие. Медь, серебро и золото легко. Следующими по сложности являются железо, низкоуглеродистая сталь и никель. Из-за их тонких и прочных оксидных пленок паять нержавеющую сталь и некоторые алюминиевые сплавы еще сложнее.
Можно ли сваривать алюминий с помощью горелки?
Горелка, которую я использую, имеет широкое пламя, поэтому она, вероятно, не так эффективна для нагрева определенной области для сварки.Лучше подойдет фонарик с большим острием. В любом случае, если у вас есть пропановая горелка и прутки для пайки, вы можете сваривать алюминий. Все это можно найти в вашем местном хозяйственном магазине.
Можно ли эпоксидный алюминий?
При правильном обращении и подготовке эпоксидная смола может хорошо сцепляться с большинством алюминия и алюминиевых сплавов. Для получения дополнительной информации о совместимых металлах для эпоксидного склеивания см. Технический совет 12 EPO-TEK. Алюминий представляет особую проблему при склеивании, поскольку он легко окисляется с образованием изолирующего / пассивирующего слоя оксида алюминия.
Можно ли паять алюминий пропановой горелкой?
Горелка, которую я использую, имеет широкое пламя, поэтому она, вероятно, не так эффективна для нагрева определенной области для сварки. В любом случае, если у вас есть пропановая горелка и прутки для пайки, вы можете сваривать алюминий. Все это можно найти в вашем местном хозяйственном магазине. Удилище стоило около 3 долларов.
Можно ли припаять латунь к алюминию?
Алюминий можно паять с алюминием, а латунь с медью, но не с алюминием. В некоторых крупных магазинах бытовой техники есть «комплект для пайки алюминия» с припоем и флюсом.Обычно, если вы можете припаять алюминий, медь / сталь не проблема.
Когда его можно паять, это можно сделать только путем предварительного лужения поверхности алюминия. Также имейте в виду, что пайка алюминия с алюминием всегда является наиболее сложной задачей. Но при пайке алюминия к более удобному для пайки металлу, например, к меди, вы получаете преимущество.
Можно ли сваривать алюминий с алюминием?
Алюминий можно сваривать с помощью газовой горелки, но этот метод сложнее, чем сварка MIG и TIG.Для сварки алюминия горелкой требуется ловкий сварщик, который может надлежащим образом управлять горелкой и присадочным стержнем.
Какой клей лучше для алюминия?
Однокомпонентные эпоксидные смолы идеально подходят для склеивания алюминия. Рассмотрим ES550 или ES558. Двухкомпонентные эпоксидные смолы также образуют прочную связь с алюминием. Permabond ET515 и MT382 – популярные варианты для склеивания тонких алюминиевых панелей, поскольку они минимизируют или исключают считывание (просвечивание).
Как паять алюминий?
Вы можете сравнительно легко сваривать алюминий с большинством других металлов с помощью клеевого соединения или механического крепления. Однако для того, чтобы сварить алюминий со сталью, требуются специальные методы. Чтобы этого избежать, вы должны изолировать другой металл от расплавленного алюминия во время процесса дуговой сварки.
Можно ли припаять алюминий к меди?
Пайка алюминия и меди – не сложная задача. Вам понадобятся некоторые необходимые инструменты и материалы, которые доступны на любой паяльной станции в Индии, например, обычный паяльник, хорошая смазка, кусок наждачной бумаги или жесткая кисть, а также оловянно-свинцовый припой.
Можно ли паять без флюса?
Имейте в виду, что чаще всего проволока для припоя представляет собой канифольный сердечник, внутри которого находится одно или несколько сердечников из флюса.В сантехнических приборах нет флюса, потому что они наносят флюс снаружи. Так что вы можете паять этим припоем. При слабом нагревании припой может плавиться недостаточно быстро, что может привести к образованию холодного паяного соединения.
Как склеить алюминий?
Цианоакрилат – также известен как мгновенные клеи, суперклей, безумный клей, клей для окиси углерода и т. Д. Все марки хорошо склеивают алюминий. Для очень высокой прочности используйте металлическое связующее, такое как 170 или оригинальный 910®. Для приклеивания алюминия к разнородным поверхностям с разными коэффициентами теплового расширения рассмотрите закалку 737.
Как паять тонкий алюминий?
Используя биметаллические переходные вставки или покрывая нержавеющую сталь алюминиевым или серебряным припоем, вы можете сваривать детали из алюминия и нержавеющей стали методом TIG более эффективно, чем механическое соединение их с помощью заклепок.
Как прикрепить сталь к алюминию?
Лучше всего это сделать с помощью болтов и гаек для соединения. Используйте изолирующее покрытие или краску на алюминии и стали, чтобы изолировать их электрически.Однако все ваши усилия будут напрасными, если вы просто скрепите соединение болтами. Вы должны изолировать болт и гайку от алюминия и стали.
припой-алюминий
ключевые слова: алюминий, оловянно-свинцовый припой, пайка, металлургические соединения, пайка медь с алюминием, больше невозможно, электрические связи
нарушают самопроизвольный пассивирующий слой оксида алюминия.

аннотация: общепринятое мнение гласит, что паять нельзя алюминий. Представлен метод, позволяющий легко паять медь непосредственно на алюминиевую подложку, которая легко воспроизводимы только лицами с базовыми навыками металлообработки, использующими только пропановая горелка, использующая «припой из алюминиевого сплава» и обычный полимерный флюс. Припой 60/40 Pb / Sn.
Ральф Климек VK3ZZC Февраль 2011 г., c opyleft
My
Интерес к этой технике проистекает из моих интересов радиолюбителей. я
часто хотели обеспечить хорошее электрическое соединение с металлическим алюминием
антенные элементы и были сорваны бескомпромиссной химией
элементов и металла. Связь давления до сих пор была только
реальная возможность, и те, у кого есть опыт, узнают на собственном горьком опыте, что
соединение под давлением длится всего пару недель при воздействии
Погода.Антенна, которая хорошо зарекомендовала себя сразу после того, как покинула мастерскую
становится все более неудовлетворительным после всего лишь нескольких недель воздействия. И это несмотря на то, что соединения защищены от атмосферных воздействий и даже пассивируются.
стыки силиконовой смолой. Простое соединение давления может
проводят постоянный ток, но РЧ-проводимость по переменному току может быть очень низкой.
Алюминий конструкции антенн часто ограничены трудностью выполнения операция соединения металлов при низком РЧ импедансе, для например, в центральном стыке антенны наземной плоскости или в центре дипольного элемента.Затем следует очень реальная трудность в заделке медных коаксиальных проводов на алюминиевый привод элемент. Те, у кого есть опыт, слишком хорошо знают коррозионное воздействие двух разнородных металлов, подверженных воздействию погодных условий. Точка подачи импеданс ведомого элемента в многоэлементной решетке яги составляет порядка пяти Ом или меньше, и я подозреваю, что многие из моих только в этой точке питания антенны были неисправны.
Для
ВЧ проводимость, единственные верные варианты – все медные элементы
обеспечение хорошо спаянных соединений с низким сопротивлением; ценой тяжелого
вес и денежная стоимость. Все мои самые успешные антенны яги имели
медные ведомые элементы. Если бы только можно было сделать правду
Металлургическая связь с алюминием при умеренной температуре, которая
быть совместимым с медью.
Можно, иногда и с припои из экзотических сплавов и экзотические флюсы. Алюминиевая пайка – это ничего новые производители, однако, держат свои методы при себе и производителях Примечания по использованию припоев не выдаются. Здесь я представляю хорошо воспроизводимый метод, который может воспроизвести компетентный радиолюбитель используя только простую и недорогую газовую горелку на пропане.
Метод требует использования широко продаваемого в настоящее время алюминиевого прутка для пайки.
Этот стержень производится под торговой маркой Alumalloy и продается в США.
Штаты под названием Durafix. Я считаю, что это тройной сплав, сделанный из
из алюминия, меди и магния с температурой плавления 430
градусов C. Он был доступен под различными торговыми названиями в
Австралия уже несколько лет известна здесь, в Озе, как «алюминий. натирание припоя ». Нет абсолютно никакой информации по применению.
опубликовал об этом.(здесь приветствуются теории заговора!)
недавно научился применять этот замечательный сплав для изготовления алюминия.
к алюминиевым паяным соединениям после просмотра нескольких видеороликов на Youtube. Поиск
Youtube по термину «Alumalloy» и убедитесь сами. Я использовал это
с успехом сделать из него некоторые антенные элементы. Только следующий шаг
осталось …. приклеивание медных проводников к алюминиевым элементам антенны.
Кому понять метод, вы должны быть знакомы с поверхностью химия алюминия.Элемент 13 – один из самых электроположительные металлические элементы. Реакция между Al и Кислород – одна из самых экзотермических реакций из известных, образует химическая основа термитного метода сварки стали и питает Твердотопливные ракетные ускорители Space Shuttle, сжигающие алюминиевый порошок и аммоний Перхлорат. Что мешает вашей алюминиевой кухонной посуде и алюминиевой фольге самопроизвольно загорается? (и сжигая свой обед)
Когда
чистый Al подвергается воздействию атмосферы, он немедленно реагирует с
Кислород и образует оксидный слой на поверхности. Этот оксидный слой
обычно толщиной всего в несколько атомов. Оксид очень жесткий и связывает
очень сильно к металлической поверхности. Оксид алюминия – это химическое
основа из твердых абразивов, рубина, сапфира и интегральной схемы
подложки. Более толстые слои оксида могут быть искусственно выращены в
процесс называется анодированием. Оксидный слой полностью пассивирует металл.
поверхность от дальнейшего окислительного воздействия при нормальных атмосферных
условия. Оксид растворим в большинстве минеральных кислот и сильных
щелочи. Именно этот оксидный монослой препятствует смачиванию
припой и обычные припои.Этот монослой может быть
механически нарушена и образована прямая связь металл-металл при условии
что кислород можно ненадолго исключить или активно сканировать.
А
сцепление под давлением с поверхностью металла Al на самом деле является оксидом
бутерброд. Оксид очень тонкий, поэтому умеренное давление
можно подвести электрод достаточно близко к основному металлу Al, чтобы
электронное туннелирование происходит через монослой оксида. Возможно, когда
соединение давления новое, оксид поврежден, и это позволяет хорошо
электрическое подключение.Через некоторое время кислород должен проникнуть в
приклейте и медленно отделите электрод от основного металла. Этот
вот почему, как я и бесчисленное множество радиолюбителей обнаружили, их
недавно отчеканенный массив яги быстро портится, когда оказывается вне досягаемости
на твоей башне.
Техника.
Припой из алюминиевого сплава плавится при температуре около 430 ° C, чистый Al и его обычные сплавы при температуре около 700 град. 400 градусов вполне в пределах мощность пропановой горелки, но совершенно за пределами верхнего диапазона паяльник.
Нагрейте основной металл снизу. Прикоснитесь к
припой к основному металлу. Не нагревайте пруток для пайки напрямую.
с горелкой … он просто расплавится и окислится.
Когда металл на
При правильной температуре припой начнет плавиться. Когда он тает, потрите
недрагоценный металл со стержнем. Это нарушает монослой оксида и позволяет
мгновенная связь металл-металл, образующаяся под расплавленной поверхностью. В
Монослой оксида нестабилен на паяемой поверхности, и жидкая пайка будет
буквально заройтесь под нее.Протрите расплавленный припой
нож из нержавеющей стали и «олово» поверхность основного металла. В
цель трения стальным лезвием – пробить большие участки
оксидный слой под расплавом припоя. Требуется постоянный нагрев, пока
вы делаете это. Первоначальный валик расплавленного припоя не смачивает
Поверхность алюминия до появления царапин ПОД валиком. В
расплавленный шарик временно исключает кислород из воздуха и только после этого будет
он сцепляется с основным металлом.
Протереть слой окисленного окалины
держите лезвие ножа подальше от паяемой поверхности и дайте ему остыть.Разогрейте снизу. Нанесите обычную свинцово-оловянную смолу 60/40 с флюсом.
припаяйте к паяемой поверхности и не допускайте перегрева и не допускайте попадания смолы
флюс для сжигания. Сформируется валик припоя идеальной формы! Разрешить
сформировать крупную бусину на поверхности и остудить. Ваш медный проводник
теперь его можно припаять к этой поверхности. На данный момент очень
тяжелому железу 100 Вт может хватить мощности, газ лучше из-за
очень высокая теплопроводность металлического алюминия. Идеально подходит
Таким образом образуется припой между медью и алюминием.
основной металл должен быть подготовлен опиливанием до голого металла с очень мелким ублюдком напильником для получения максимально гладкой поверхности. Польский с Проволочная щетка FINE, щетка для замши – это то, что здесь действительно нужно. Если поверхность анодирована, ее необходимо полностью отшлифовать, чтобы оголенный метал.
Почему это работает и как работает пайка из алюминиевого сплава?
Алюминий
не требует флюса! Мне потребовалось время, чтобы оценить это
факт как бы бросает вызов здравому смыслу и условностям.Пайка
представляет собой сплав алюминия, меди и магния и, возможно, других
нераскрытые металлы. Я полагаю, что цель магния
в пайке выполняет функцию поглотителя кислорода. Под этим
расплавится, поврежденная поверхность Al будет соединяться напрямую, и магний
предотвращает динамическое образование свежего монослоя оксида алюминия за счет конкуренции
с Al для растворенного кислорода в расплаве. Магний – это флюс
! Я не знаю этого факта, это только мое обоснованное предположение.
Однако верно, что магний имеет большое сродство к кислороду и
в отличие от алюминия оксид магния не сильно связан с
металлическая поверхность.Может быть, это вещество с высоким содержанием меди.
паяльный, не знаю. У меня нет способов и средств
химически анализируя это, может быть, кто-то там делает.
Я был поражен тем, что стандартный электрический припой Pb-Sn совместим с паяной поверхности, этого не ожидалось, и я нашел это только эксперимент.
Не верьте мне на слово, попробуйте сами.
Алюминий доступен в Австралии, в розницу. Я купил свой в Баннингсе где он продается как пруток для пайки алюминия Bernzomatic.Это очень дорогие, 2 маленьких стержня стоят 10 австралийских долларов. В нем нет абсолютно никаких совет по применению. Может быть, вы купили и выбросили отвращение, потому что “не работает”? Поверьте, это работает но только с правильной техникой, как описано. Наблюдение, что пайка совместима со стандартным электрическим припоем приходит ко мне, и я подозреваю, что весь остальной мир Ham, как полный и желанный сюрприз!
Продолжение поисков хорошего способа электрического соединения с погодостойкими алюминиевыми элементами I недавно нашел лист тонкой нержавеющей стали во время недавнее погружение в мусорную корзину. ![]() ![]() ВЫРЕЗАТЬ нержавеющая сталь с угловой шлифовальной машиной и специально разработанная отрезные диски из нержавеющей стали. Они будут иметь обозначение INOX. Вы также можете осторожно и грубо использовать очень тяжелые ножницы для жести. сила. ДРЕЛЬ
нержавеющая сталь, сначала с новым 1/8 дюймовым кобальтом
просверлите пилотное отверстие, затем увеличьте.Особый секретный метод
сверление нержавеющей стали ФОРМА
из нержавеющей стали, поверх оправки, которая немного тоньше, чем
алюминиевая трубка. Это можно сделать с помощью сверхмощных тисков и стандартных тисков.
сверла. Вам придется немного поэкспериментировать, чтобы найти правильный
оправка. Не используйте оправку 12 мм для трубки 12 мм, фитинг не будет
“кусать”. |
Постскрипты
- Сделано
вы знаете, что можно было сделать некачественный стандарт 60/40
паять напрямую с алюминием? Расплавьте припой на алюминии во время царапания
под валиком припоя.
Возникает некоторая связь; действительно занимает слишком много времени, кислород растворенный в расплавленном припое быстро вступит в реакцию, и валик припоя больше не будет связывать. Это почти не работает, и я бы не стал полагаться на такая связь.Бусина самопроизвольно отвалится от основного металла. через несколько недель, хотя поначалу кажется, что граница. Почему ? Я считаю, что нестабильность этого сустава из-за атмосферного кислорода, который растворяется в расплавленном свинце оловянный сплав. Примерно через 2 недели этот кислород диффундирует через твердый припой к алюминиевому слою, где он непосредственно реагирует и эта реакция высвобождает валик припоя. Интересно, если тройной сплав свинец-олово-цинк может работать. Цинк будет действовать как сканер кислорода в затвердевшем шарике.Помните что металлы не являются полностью газонепроницаемыми. Химически реактивный газ будет диффундировать через твердый металл, хотя и очень медленно при комнатной температуре.
- шт.