Как проверить производительность компрессора: Расчет производительности компрессора
Проверка производительности компрессора
16.03.10 12:08 все
Производительность компрессоров проверяют по времени повышения давления сжатого воздуха в главных резервуарах при закрытом разобщительном кране на напорном воздухопроводе.Ручка крана вспомогательного тормоза локомотива должна находиться в положении отпуска.
Если в главных резервуарах имеется сжатый воздух, то его выпускают через выпускные краны, пока компрессор не включится регулятором давления.
Эти регуляторы должны включать и отключать компрессоры при определенном давлении в главных резервуарах:
на электровозах — включать при 7,5 + 0,2, отключать при 9 + 0,2 кгс/см2;
на тепловозах — включать при 7,5 + 0,2, отключать при 8,5 + 0,2 кгс/см2;
на электросекциях, электропоездах и дизель-поездах — включать при 6,5 + 0,2, отключать при 8 + 0,2 кгс/см2.
Время повышения давления в главных резервуарах с 7 до 8 кгс/см2 каждым компрессором- в отдельности устанавливается в зависимости от типа компрессора и серии локомотива или моторвагонного подвижного состава, как указано в таблице.
Поиск по сайту
Рама и кузов вагона
Технология изготовления деталей из проката |
Технология изготовления котла цистерны |
Особенности изготовления из алюм. сплавов |
Изготовление деталей упругой площадки |
Ремонт кузовов |
Ремонт кузовов грузовых вагонов |
Автосцепное устройство
Изготовление деталей автосцепки |
Ремонт корпуса автосцепки |
Ремонт поглощающих аппаратов |
Расположение автосцепки |
Поглощающий аппарат |
Амортизирующие устройства |
Колесные пары
Производство черновых осей |
Механическая обработка оси |
Неисправности колесных пар и их элементов |
Технология ремонта колесных пар |
Изготовление и ремонт корпусов букс |
Изготовление и ремонт подшипников скольжения |
Внутреннее оборудование вагонов
Материалы внутр.![]() |
Монтаж внутреннего оборудования |
Cистема отопления и водоснабжения |
Защитные покрытия вагонов |
Металлические покрытия |
Тележки вагонов
Производство пассажирских тележек |
Ремонт тележек пассажирских вагонов |
Ремонт редукторных приводов |
Производство тележек грузовых вагонов |
Ремонт тележек грузовых вагонов |
Технология изготовления пружин и рессор |
Гидравлические гасители колебаний |
Тормоза ПС
Приборы управления тормозами |
Тормоза подвижного состава и локомативов |
Компрессоры |
Воздухораспределители |
Приборы автоматического регулирования |
Тормозные рычажные передачи |
Обслуживание тормозного оборудования Проверка пневматического тормоза локомотива Испытание тормоза при приеме вагона Положение ручек кранов Проверка тормозных цилиндров Проверка действия крана машиниста Проверка тормозного оборудования вагона Проверка плотности тормозной сети Проверка установки грузового авторежима Установка авторежима Проверка электропневматического тормоза Переносной прибор типа A635 Переносный прибор типа П-ЭПТ Проверка ЭПТ на пассажирских вагонах |
О автотормозной технике |
Электропневматический тормоз электропоездов |
Компрессор: Точный расчёт характеристик компрессора
На первый взгляд тема выбора источника сжатого воздуха для автомастерской не кажется достаточно интересной.
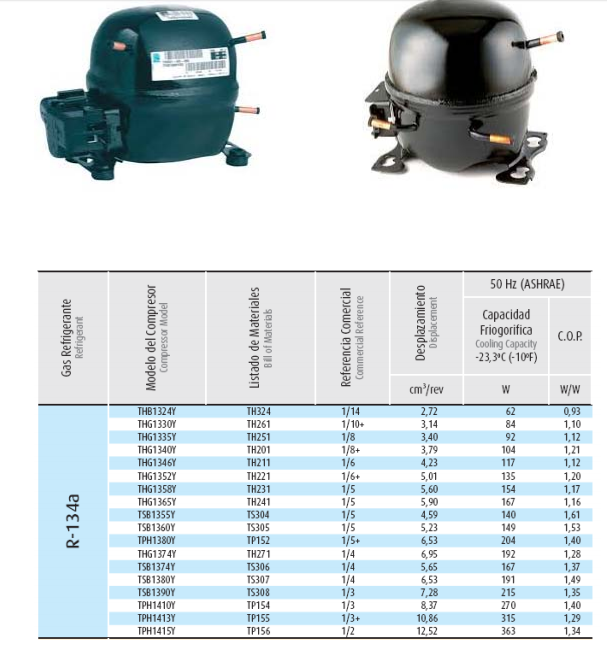
Сжатый воздух в условиях автосервисного предприятия находит применение не только для подкачки колес – это известно. Различное авторемонтное оборудование: шиномонтажные станки, окрасочно-сушильные камеры, некоторые типы автомоек используют пневмопривод. Окрасочные работы выполняются только с использованием сжатого воздуха, профессиональных окрасочных пистолетов с электроприводом нет в программе ни у одного производителя. Это те случаи, когда без сжатого воздуха просто не обойтись.
Что еще может заставить авторемонтника задуматься о приобретении компрессора? Конечно же, желание механизировать наиболее трудоемкие виды работ с использованием разнообразного пневмоинструмента. Его преимущества в сравнении с традиционно применяющимся электроинструментом не для всех очевидны, но тем не менее бесспорны.
Пневмоинструменты существенно превосходят своих электроконкурентов по надежности и ресурсу, побивая их почти вдвое по энерговооруженности – отношению мощности к единице веса. Именно поэтому они как нельзя лучше приспособлены для напряженной профессиональной работы, в условиях которой их применение наиболее экономически выгодно.
Не важно, какая из указанных причин привела вас к мысли приобрести компрессор, важно, как это сделать грамотно.
С чего начать выбор компрессора
<Скажите, у вас есть компрессор с пятидесятилитровым ресивером?> – нередко с такого или подобного вопросов начинается беседа покупателя с менеджером. После этого продавцу приходится тратить много времени на то, чтобы объяснить, что задать такой вопрос – все равно что спросить, есть ли в продаже автомобиль с четырьмя колесами и что объем ресивера никак не может являться отправной точкой при выборе компрессора. Из чего же нужно исходить, делая выбор?
Исходить нужно из потребностей. Мысль не очень оригинальная, но справедливая, причем справедливая при выборе любого оборудования. Поскольку лучше всего о своих потребностях осведомлены мы сами – за нами и первое слово. Перед тем, как нанести визит продавцу гаражного оборудования, нужно по возможности более точно подсчитать количество потребителей сжатого воздуха, определить их рабочие параметры (давление и номинальный расход воздуха) и предполагаемый режим работы.
Рабочие параметры пневмоинструмента или пневмооборудования указываются в паспорте. Если по каким-либо причинам эта информация отсутствует, можно у своих коллег или любого продавца пневмооборудования выяснить характеристики аналогичных устройств. Как правило, возможная небольшая ошибка не будет роковой. Для справки мы приводим параметры наиболее часто применяемого в автосервисной практике инструмента.
Понятно, что пневмоинструмент используется в работе не непрерывно, а время от времени, соответственно изменяется текущее воздухопотребление. Для определения характеристик компрессора ориентируются на усредненное значение потребности в сжатом воздухе. Чтобы ее рассчитать, нужно, исходя из опыта эксплуатации и знания технологии планируемых работ, представить, каковы будут продолжительность и периодичность между включениями инструмента, возможна ли одновременная работа нескольких устройств и каких.
Сказанное касается тех, кто впервые приобретает компрессор. Если вы уже используете источник сжатого воздуха, который по каким-либо соображениям не удовлетворяет потребностям вашего предприятия, например, в связи с ростом количества потребителей или увеличившейся интенсивностью работ, нужно знать технические характеристики используемого компрессора, включая объем ресивера, а также сформулировать конкретные претензии к его работе. Например, если компрессор не обеспечивает требуемый расход воздуха, что часто приводит к перерывам в работе, следует экспериментально установить, за какой период времени давление в ресивере падает ниже допустимого уровня.
Вооружившись этими сведениями, можно смело идти в хороший магазин, где опытный менеджер (а в хороших магазинах – именно такие менеджеры) на основании этих данных поможет вам подобрать оптимальную с точки зрения соотношения надежности и цены покупку.
Более того, в хорошем магазине вам дадут возможность в течение 2-3 дней опробовать покупку на практике и в случае, если она вас не устраивает – обменять на другую модель. При этом продавцы действуют, исходя и из своих интересов: неправильно подобранный компрессор не отработает гарантийного срока, который для различных видов компрессорного оборудования может составлять от 6 до 12 месяцев.
Если у вас на примете есть такой магазин, менеджерам которого вы доверяете, если вы нелюбознательны и не хотите узнать ответы на вопросы, поставленные в начале статьи, на этом можно закончить чтение. Если же вы хотите более осознанно подойти к вопросу приобретения источника сжатого воздуха – двигайтесь с нами дальше.
Гаражный компрессор
Существуют различные типы компрессоров, используемые в технике в качестве источников сжатого воздуха. В настоящее время в автосервисной практике находят применение в основном поршневые устройства. В компрессорах этого типа воздух сжимается в замкнутом пространстве цилиндра в результате возвратно-поступательного движения поршня. Конструктивно они представляют собой агрегат, включающий компрессорную головку, электропривод, ресивер и устройство автоматического регулирования давления (прессостат).
Популярность поршневых компрессоров среди работников автосервиса определяется их невысокой стоимостью, приемлемыми массогабаритными показателями, простотой в эксплуатации и обслуживании и выходными характеристиками, способными удовлетворить потребности практически любого авторемонтного предприятия.
К основным характеристикам компрессора относятся два параметра – максимальное давление (Pmax) и объемная производительность или подача (Q).
Большинство предлагаемых сегодня на рынке компрессоров развивают давление, превышающее потребности стандартного пневмооборудования и инструмента, используемого при авторемонте. На рынке представлены компрессоры с максимальным давлением 6, 8, 10, 13 бар.
Напомним, что номинальное рабочее давление окрасочных пистолетов – 3-4 бар, пневмоинструмента – до 6,5 бар. Исключение составляет пневмопривод шиномонтажных станков, для которого многие производители рекомендуют использовать сжатый воздух при давлении 8-10 бар. Впрочем, практика показывает, что пневматика шиномонтажного оборудования надежно работает и при использовании 8-барного компрессора.
Что еще нужно учитывать, определяя максимальное давление, развиваемое компрессором?
Во-первых, следует иметь в виду, что система автоматического регулирования давления всех компрессоров настроена таким образом, что обеспечивает поддержание давления в ресивере с допуском -2 бар от максимального значения. Это означает, что в процессе работы компрессора с Pmax=8 бар давление на выходе может изменяться в диапазоне от 6 до 8 бар, у 10-барного, – соответственно, от 8 до 10 бар. Заводские регулировки прессостата могут быть изменены пользователем только в сторону уменьшения минимального давления.
Во-вторых, необходимо учитывать, что наличие протяженных пневмомагистралей до потребителей сжатого воздуха вызывают падение давления в линии. При ошибках в проектировании пневмосети (применении труб малого диаметра, использовании водопроводных запорных устройств, нерациональной прокладке магистралей и т. д.) оно может достигать существенной величины и стать причиной неэффективной работы пневмооборудования. Чтобы избежать возможных неприятностей в таких случаях, нужно отдать предпочтение компрессору с более высоким максимальным давлением.
Из сказанного следует, что в качестве универсального гаражного источника сжатого воздуха можно использовать компрессор с максимальным давлением 8 бар. Если компрессор будет использоваться исключительно для окрасочных работ, можно обойтись и 6-барным, а в случае разветвленных пневмосетей надежнее использовать компрессор, развивающий давление до 10 бар.
Некоторый запас по давлению полезен и с другой точки зрения. Чем выше давление, развиваемое компрессором, тем большую массу воздуха он может закачать в ресивер и тем большее время последний будет опорожняться до минимально допустимого давления, обеспечивая компрессору время для отдыха.
Кстати, об отдыхе: а нужен ли он железному компрессору? В ответе на этот вопрос кроется ключ к пониманию особенности рабочего процесса в поршневом компрессоре. Учитывая ее, определяют важнейшую характеристику компрессора – производительность.
Режим работы поршневого компрессора
Сжимаясь в цилиндре поршневого компрессора, воздух нагревается. На выходе из одноступенчатого компрессора его температура превышает 150оС. При этом часть тепла поглощается деталями и элементами конструкции головки компрессора, что приводит к повышению их температуры и изменению тепловых зазоров в узлах трения.
Если не обеспечить отвод тепла, головка не успевает охлаждаться. Последствия представить несложно: температура смазываемых узлов возрастает выше допустимого уровня, полностью выбираются тепловые зазоры, горячее масло, подаваемое к парам трения разбрызгиванием, не держит “масляный клин”. В “лучшем” случае это грозит ускоренным износом механизма компрессора, в худшем – немедленным выходом из строя в результате заклинивания.
Это учитывается при проектировании компрессора. Для обеспечения теплосъема применяют принудительное охлаждение компрессорной головки – обдув воздухом. В качестве нагнетателя обычно используется вентилятор электродвигателя или шкив коленчатого вала компрессора. Чтобы повысить эффективность охлаждения, корпус головки изготавливают из сплавов с высокой теплопроводностью и делают оребренным.
Такие меры наиболее просты и дешевы, но недостаточны для того, чтобы обеспечить продолжительную непрерывную работу поршневого компрессора. Поэтому поршневой компрессор изначально рассчитывается на эксплуатацию со строго определенной скважностью, что предполагает обязательное наличие перерывов, необходимых для нормализации теплового режима головки.
Количественно режим эксплуатации оценивается коэффициентом внутрисменного использования (Кви), показывающим, какую часть времени компрессор способен работать непрерывно. Отечественный стандарт определяет три вида режимов работы компрессора: кратковременный (Кви = 0,15), непродолжительный (Кви = 0,5) и продолжительный (Кви = 0,75).
Способность дольше работать в непрерывном режиме означает в конечном счете большую надежность и ресурс техники. Она достигается использованием более совершенных материалов и схемных решений, больших запасов прочности конструктивных элементов, что, естественно, отражается на стоимости продукции.
В зависимости от допустимого режима эксплуатации, а также выходных характеристик зарубежные производители подразделяют свою продукцию на несколько серий: хобби (полупрофессиональную), профессиональную и промышленную. О том, чем они принципиально отличаются, мы расскажем далее.
Как обеспечивается требуемый режим эксплуатации компрессора? Прежде всего, рассчитывая его объемную производительность, нужно соблюсти правильный баланс между этой важнейшей характеристикой и средним воздухопотреблением. Эти параметры связаны между собой через коэффициент, зависящий от класса компрессора, который больше единицы для компрессоров всех серий.
Это означает, что подача компрессора должна быть всегда больше, чем среднее воздухопотребление. Производя сжатого воздуха больше, чем расходуется, компрессор сам создает для себя задел, позволяющий ему время от времени “расслабляться”. Величина запаса по производительности тем больше, чем ниже положение, занимаемое компрессором в “табели о рангах”. Отдав предпочтение более дешевой технике (например, полупрофессиональной серии), необходимо заложить в расчеты больший запас по производительности.
Функцию хранения запасенного сжатого воздуха выполняет ресивер, а в случае разветвленной пневмосети – также и внутренний объем магистралей.
В этом заключается наиважнейшая роль ресивера наряду с демпфированием пиковых нагрузок, сглаживанием пульсаций давления и охлаждением сжатого воздуха.
Может сложиться мнение, что чем больше емкость ресивера, тем легче жизнь компрессора. Это мнение ошибочно. Дело в том, что для наполнения ресивера до максимального давления, когда автоматика прессостата отключает компрессор, требуется время, и немалое. При необоснованном увеличении объема ресивера компрессор будет трудиться непрерывно на его восполнение, выходя из допустимого режима работы.
Объем ресивера связан как с производительностью компрессора, так и с характером воздухопотребления. По этой причине компрессорная головка одной производительности может комплектоваться ресиверами нескольких типоразмеров, объем которых отличается в несколько раз. В среднем объем ресивера таков, что компрессор способен наполнить его за 3-4 мин. Если потребности в сжатом воздухе примерно равномерные по времени, то в целях экономии средств можно ограничиться минимальным ресивером. Если возможны пиковые нагрузки, лучше предпочесть больший.
Итак, грамотно выбрать компрессор для заданного воздухопотребления означает определить его производительность и объем ресивера таким образом, чтобы при эксплуатации данный компрессор работал в режиме внутрисменного использования, на который он рассчитан. Несоответствие режима работы паспортному значению приводит либо к неэффективному использованию компрессора, либо к сокращению его ресурса и преждевременному выходу из строя.
Как упоминалось, поршневых компрессоров, имеющих Кви = 1, в природе не существует. Поэтому, если ваш компрессор на протяжении смены “молотит” без перекуров – это верный признак того, что он подобран неправильно и вскоре выйдет из строя.
Особенности расчета характеристик компрессора
Приступая к расчету характеристик компрессора, полезно знать следующее. Масса воздуха, перекачиваемая компрессором в единицу времени, – величина постоянная и зависит от его конструктивных особенностей. Однако производительность принято определять не в массовых, а в объемных величинах, что часто приводит к путанице и ошибкам в расчетах.
Дело в том, что воздух, как и другие газы, сжимаем. Это означает, что одна и та же масса воздуха может занимать разный объем в зависимости от давления и температуры.
Если объемная подача компрессора – переменная по времени, какая же цифра указывается в технических характеристиках? Согласно ГОСТ, производительность компрессора – это объем воздуха, выходящий из него, пересчитанный на физические условия всасывания. В большинстве случаев физические условия на входе в компрессор соответствуют нормальным: температура – 20oС, давление – 1 бар. ГОСТ также допускает возможность отклонения реальных характеристик компрессора от указанных в паспортных данных на величину +5%.
Кстати, на нормальные условия пересчитывают и параметры потребителей сжатого воздуха, чтобы привести их к общему знаменателю с характеристиками источника. Поэтому номинальный расход 100 л/мин означает, что при рабочем давлении
Зарубежные производители, не знакомые с содержанием наших ГОСТов, определяют производительность своей продукции иначе, что порой приводит к ошибкам. В паспортных данных на импортную технику указывается теоретическая производительность компрессора (производительность по всасыванию).
Теоретическая производительность определяется геометрическим объемом воздуха, который поместится в рабочей полости компрессора за один цикл всасывания, умноженный на количество циклов в единицу времени. Она отличается от реальной, выходной, в большую сторону. Отличие учитывается коэффициентом производительности (Кпр), зависящим от условий всасывания и конструктивных особенностей поршневого компрессора – потерь во всасывающих и нагнетательных клапанах, наличия недовытесненного, “мертвого”, объема, приводящих к уменьшению наполнения цилиндра. Для компрессоров профессиональной серии коэффициент производительности может составлять величину от 0,6 до 0,7, причем большие значения соответствуют большей подаче.
Различия характеристик, рассчитанных по входу и на выходе, могут достигать существенной величины. Может, это и является причиной того, что лукавые иностранные производители указывают данные по всасыванию: выглядят они значительно солиднее.
В хороших магазинах продавцы, как правило, имеют данные как по входным, так и по выходным характеристикам профессиональных импортных компрессоров. Для продукции бытовой серии таких данных не приводит никто, хотя из практики известно, что реальный “выход” бытовых компрессоров едва ли превышает 50% от заявляемой теоретической производительности.
Точный расчет характеристик поршневого компрессора сложен и связан с решением степенных уравнений. Приводимая методика выбора компрессора содержит упрощенные соотношения, которые тем не менее дают небольшую погрешность, и позволяет правильно определить его параметры.
Обратите внимание, что в ней определяется теоретическая производительность компрессора (по входу). Чтобы пересчитать полученные данные на “выход” (в случае расчета отечественного гаражного компрессора), нужно результат уменьшить на 30-40%.
Эксплуатационные испытания компрессоров – SINT TECHNOLOGY
Вместо того, чтобы быть просто контрактным требованием, эксплуатационные эксплуатационные испытания центробежных и поршневых компрессоров могут стать ценной возможностью оценить базовые характеристики агрегата после его ввода в эксплуатацию. Это может быть верно как для новых, так и для модернизированных агрегатов и может помочь руководству в составлении производственных планов в соответствии с реальными возможностями машины.
Очень часто новые компрессоры перед отправкой на стройплощадку проходят заводские испытания. Это должно определить разрыв между ожидаемыми проектными характеристиками и «проверенными» из-за производственного процесса. Почему тест производительности должен повторяться на сайте?
Основными причинами для проведения эксплуатационных испытаний являются:
- определение фактических рабочих характеристик и пригодности к эксплуатации агрегата при его установке на трубопроводе
- проверьте поведение компрессора после его соединения с другими компонентами, такими как охладители и скрубберы, а также с самим трубопроводом.
- проверить, соответствует ли компрессор спецификациям применимого договора купли-продажи, поэтому требуется ли неустойка или действия по «возмещению ущерба»
Кроме того, согласно коду ASME PTC 10 заводские испытания часто относятся к категории «Тип 2», т.е. испытание проводилось с использованием газа, отличного от контрактного. Эксплуатационные испытания в полевых условиях позволяют использовать правильный технологический газ, на котором основаны проектные характеристики компрессора.
SINT Technology является надежным и независимым поставщиком средств проверки производительности компрессоров, которые могут помочь вам в постоянном контроле вашей машины и в оценке ее состояния с точки зрения напора, эффективности и потребляемой мощности.
Компания SINT Technology уже несколько лет проводит эксплуатационные и приемочные испытания центробежных и поршневых компрессоров.
Клиент получает поддержку как на ранней стадии заключения договора, так и до начала коммерческой эксплуатации установки путем проверки выполнения гарантийных обязательств.
Соответствующая тестовая документация для компрессоров, соответствующих стандарту API, может быть подготовлена по запросу Заказчика. Подробная процедура испытаний компрессора может быть выпущена на основе имеющихся спецификаций и кривых заводских испытаний, объясняющих метод сравнения фактических характеристик компрессора с гарантированными.
SINT Technology также может контролировать относительную производительность компрессора на протяжении всего срока службы путем периодической проверки, чтобы помочь Заказчику предотвратить серьезные неисправности. Технология SINT также может обеспечить акустические исследования и измерения вибрации .
Наш опыт в этой области позволил нам стать первой итальянской лабораторией, получившей официальное признание ACCREDIA, Итальянского национального органа по аккредитации, за эксплуатационных испытаний центробежных компрессоров . Это гарантирует и удостоверяет качество наших результатов тестирования для всех наших клиентов. Наши стандарты установлены основными международными нормами, такими как ASME PTC 10, ISO 5389 и ISO 1217.
SINT Technology предлагает глобальные решения для тестирования производительности компрессоров всех размеров, включая:
- Одноступенчатый компрессор
- Многоступенчатые компрессоры и агрегаты сжатия
Эксплуатационные испытания центробежных компрессоров в полевых условиях — химическая технология
| Натан Поернер, Тим Эллисон, Гектор Дельгадо, Юго-Западный научно-исследовательский институт
Определение рабочих характеристик центробежных компрессоров может помочь в эксплуатации и обслуживании оборудования. Здесь представлен обзор параметров, которые необходимо измерить и рассчитать для эффективного тестирования
Компрессоры используются во всех областях производства и во многих различных секторах химической промышленности (CPI). Производственные объекты могут иметь несколько компрессоров различных типов и размеров. Три основных типа компрессоров — центробежные, осевые и поршневые. В этой статье основное внимание уделяется центробежным компрессорам (рис. 1) и тому, как можно проводить эксплуатационные испытания этого класса оборудования в интересах конечных пользователей, производителей и обслуживающего персонала. Преимущества полевых испытаний существующих установок включают возможность количественной оценки ухудшения характеристик в зависимости от возраста оборудования, определения того, следует ли и когда выполнять определенные задачи по техническому обслуживанию, а также определения конкретных компонентов оборудования для улучшения продукта. Для новых устройств полевые испытания помогают проверить производительность продукта.
Рисунок 1. Эксплуатационные испытания многоступенчатого центробежного компрессора, такого как показанный здесь, позволят количественно определить факторы энергии, напора, работы и расхода
Принципы работы
Независимо от типа компрессора существуют определенные термины и параметры которые будут использоваться для определения и количественной оценки производительности оборудования. Основными среди них являются энергия, голова, работа и поток. Энергия является параметром рассматриваемой жидкости и чаще всего определяется как полная энтальпия жидкости. Энтальпия представляет собой комбинацию кинетической (скорость жидкости) и потенциальной (статическое давление) энергии жидкости. Поскольку энтальпия является производным термином, прямого способа измерения энтальпии жидкости не существует. Вместо этого общепринятой практикой является использование уравнений состояния (УС), которые связывают измеряемые параметры (чаще всего температуру и давление) с производными условиями, такими как энтальпия и энтропия, для данного состава флюида. Доступны различные EOS, и каждый из них лучше всего подходит только для определенного набора составов жидкости в определенном диапазоне рабочих условий. По этой причине важно, чтобы все стороны, участвующие в тестировании производительности, понимали и принимали выбранный EOS.
Напор является мерой увеличения энергии внутри жидкости и обычно определяется как изменение энтальпии жидкости между условиями всасывания и нагнетания. Работа – это механическое средство передачи энергии жидкости.
Поток можно определить с точки зрения массы или объема, при этом объем принимает одну из двух распространенных форм. Во-первых, это пропускная способность или фактический расход, который учитывает объемный расход для фактического давления и температуры жидкости, обычно при условиях на входе. Второй называется стандартным или нормальным расходом и рассчитывает объемный расход для заданного массового расхода при «стандартных» условиях. Например, это может быть температура 60°F и давление, равное 14,7 фунтов на квадратный дюйм. Для любого термина объемного расхода массовый расход будет одинаковым.
Измерения и расчеты
Данные, собранные для определения рабочих характеристик, включают температуру, давление, расход и состав газа. Температуру и давление относительно просто собрать с помощью различных доступных датчиков. Однако определить поток может быть немного сложнее. Такие измерения часто зависят от дополнительных измерений, но по-прежнему доступно несколько вариантов датчиков. Состав газа, вероятно, является наименее доступной информацией для получения, требующей либо онлайнового газового хроматографа (редко доступного в большинстве установок), либо отбора жидкости для анализа в лаборатории после тестирования.
В дополнение к этим базовым измерениям, некоторые общие параметры производительности, которые будут сгенерированы, включают работу, напор и эффективность. Работа и голова, обсуждавшиеся ранее, приводят к определению эффективности, которую можно определить по-разному.
Во-первых, существует термодинамическая эффективность, которая включает только фактический процесс сжатия и связывает фактический напор с идеальным напором. Идеальная голова также может быть определена несколькими способами; двумя наиболее распространенными являются изоэнтропия и политропия. Очень важно понять, какое из этих двух определений используется в данном случае. Расчеты изоэнтропической эффективности предполагают, что термодинамический процесс является адиабатическим, и сравнивают фактический напор с идеальным напором, при этом предполагается, что энтропия на всасывании и нагнетании одинакова.
Политропическая эффективность сравнивает фактический напор с напором, концептуально рассчитанным путем разбиения всего шага сжатия на несколько меньших шагов с добавлением тепла на каждом шаге. Два процесса сходятся при низких соотношениях давлений, давая идентичные результаты. Одним из преимуществ использования политропического КПД является то, что для многоступенчатых машин, если все ступени имеют одинаковую политропическую эффективность, то политропический КПД всей машины равен политропическому КПД ступени. Общий изэнтропический КПД машины в этом случае будет ниже изэнтропического КПД ступени.
Другим способом определения КПД является механический КПД компрессора. Обычно это включает дополнительные измерения для оценки механической работы, поступающей в компрессор, обычно с помощью измерителя крутящего момента. Это позволяет рассчитать КПД компрессора как фактический напор по сравнению с механической работой, поступающей в компрессор.
Наконец, общая эффективность системы может быть достигнута, если будут проведены измерения общей энергии, вкладываемой в систему. Для компрессоров с электродвигателем общая энергия может быть определена на основе электрических измерений и сведений о двигателе. Для компрессоров с приводом от двигателя и газотурбинного двигателя знание состава топлива и расхода может быть использовано для определения общей подводимой энергии.
Рис. 2. Центробежные компрессоры имеют вращающуюся крыльчатку, которая придает жидкости напор
Центробежные компрессоры
Центробежный компрессор использует энергию вращения крыльчатки для придания напора жидкости, главным образом за счет сначала ускорения жидкости, а затем преобразования кинетическую энергию в потенциальную энергию за счет замедления жидкости. Типичное внутреннее устройство центробежного компрессора показано на рис. 2. Жидкость входит в компрессор и направляется на входе к вращающемуся рабочему колесу. Лопасти рабочего колеса предназначены для ускорения жидкости в осевом или радиальном направлении. Возможно повышение потенциальной энергии из-за геометрии лопастей крыльчатки, но большая часть увеличения энергии после выхода из крыльчатки будет в основном кинетической. Чтобы преобразовать эту энергию в статическое давление, секция диффузора будет преобразовывать кинетическую энергию в статическую, замедляя поток жидкости до того, как он будет направлен к выходу в коллекторе.
Конструкция каждого из этих отдельных компонентов может оказывать существенное влияние на производительность компрессора, и поэтому ее следует тщательно продумывать для каждого конкретного применения. Кроме того, центробежный компрессор может использовать несколько рабочих колес во многих различных конфигурациях для увеличения рабочего потока или степени сжатия всего агрегата, при этом каждый отдельный набор рабочих колес и диффузоров компрессора может иметь разные конструкции.
Рис. 3. На схеме показано расположение контрольно-измерительного оборудования центробежного компрессора [ 4 ]
Эксплуатационные испытания в полевых условиях
Одним из первых моментов, который следует учитывать при планировании эксплуатационных испытаний центробежного компрессора, является размещение датчиков для регистрации рабочих условий системы. Идеальная схема измерений показана на рис. 3. В комплект входит устройство для измерения расхода (желательно на стороне всасывания агрегата), приборы для измерения температуры и давления как на стороне всасывания, так и на стороне нагнетания (хотя температура нагнетания не обязательна). , средства для определения состава газа, средства измерения скорости вращения установки и приборы для измерения атмосферных условий (в основном для приведения измерений избыточного давления к абсолютным). Следует выбирать конкретное расположение фактических датчиков, чтобы избежать ошибок из-за искажения потока из-за трубопроводов, клапанов или датчиков выше по потоку. Допустимые места для датчиков определены в отраслевых стандартных документах, доступных в разделе ссылок.
На основе этих измерений и с помощью надлежащим образом выбранного и согласованного EOS могут быть получены рабочие параметры компрессорной установки, включая мощность, которая показана в уравнении (1).
( 1 )
Предполагая изоэнтропическое сжатие, эффективность установки можно рассчитать по уравнению (2).
( 2 )
Где:
s s = s(p s , T s )
h(p,T) = энтальпия (теплосодержание) газа
900 02 ч есть (р Д , s s ) – h(p s , T s ) = изменение изоэнтропической энтальпии газаs(p,T) = энтропия газа (термодинамическая величина, представляющая недоступную энергия; обязательно увеличивает с турбомашинным процессом за счет потерь на трение
м • компрессор = массовый расход компрессора
Наряду с выбором конкретных измерительных датчиков и определением их размещения подготовка к эксплуатационным испытаниям должна также включать следующие пункты:
- Определение рабочих условий, которые необходимо используется для контрольных точек
- Выбор подхода к сокращению данных и проверке неопределенности.
Точность расчетной производительности компрессора зависит от погрешности измерения давления и температуры на входе и выходе, состава газа и массового расхода. Погрешности в характеристиках могут варьироваться от менее 0,5% в лабораторных тестах [9].0117 6 ] до 2–3 % и более при полевых измерениях [ 7 ]. Общая погрешность измерения зависит от большого количества факторов, включая точность и калибровку датчика, правильную установку датчика, согласование сигнала, неравномерность или нестабильность потока и потери тепла из системы.
- Определение конечной цели теста. Например, в случае приемочного испытания результаты эксплуатационных испытаний будут использоваться в качестве критерия приемки. В тех случаях, когда данные испытаний производительности будут использоваться для планирования технического обслуживания, инженеры должны указать, как данные будут сравниваться с предыдущими измерениями для методов старения оборудования.
При сравнении текущих и предыдущих полевых измерений важно понимать, что измерения, выполненные в различных условиях эксплуатации, нельзя сравнивать напрямую. Следовательно, необходимо либо гарантировать, что для двух наборов измерений воспроизводятся одни и те же рабочие условия, либо иметь безразмерные параметры, которые можно использовать для сравнения данных испытаний, проведенных в разных рабочих условиях.
Шестью наиболее распространенными безразмерными рабочими параметрами, используемыми для центробежных компрессоров, являются удельный объемный коэффициент, машинные числа Маха и числа Рейнольдса, а также коэффициенты напора, расхода и работы. Эти термины определены в таблице 1. Ожидается, что условия испытаний, которые точно соответствуют конкретному объемному отношению и коэффициенту расхода, дадут аналогичные результаты для коэффициента напора и коэффициента подводимой работы с некоторыми отклонениями из-за разных чисел Маха и Рейнольдса. Эти отклонения могут быть минимальными или могут быть скорректированы на основе стандартов испытаний, если отклонения чисел Маха и Рейнольдса находятся в допустимых пределах.
Примерные графики, показывающие измеренный коэффициент изоэнтропического напора в зависимости от коэффициента расхода, представлены на Рисунке 4 для одной ступени центробежного компрессора, которая была испытана при нескольких числах Маха машины (MU2). Расчетные кривые (сплошные линии) достаточно хорошо сравниваются с измеренными кривыми (пунктирные линии), хотя измерения пикового напора и расхода в штуцере ниже расчетных значений, а эффективность вблизи расчетного коэффициента расхода 0,08 превышает прогнозы. Результаты для коэффициента напора показывают типичную характеристику увеличения подъема напора при более низких расходах с нулевым наклоном при низком расходе (точка помпажа). Показано, что дроссельная линия при высоком расходе сильно зависит от числа Маха машины. Результаты нормализованного КПД показывают пиковые КПД вблизи расчетного коэффициента расхода независимо от числа Маха машины, а также подчеркивают снижение эффективности и более низкий поток через штуцер при высоких числах Маха.
Рис. 4. На графиках показаны примерные данные о производительности центробежного компрессора [ 5 ]
Заключительные замечания
Эксплуатационные испытания могут помочь компрессорам на всех этапах срока службы оборудования. Для новых блоков тесты производительности могут подтвердить производительность продукта, а для существующих блоков тесты производительности могут помочь отслеживать методы обслуживания. Кроме того, производительность можно использовать для определения показателя окончания срока службы.
Показатели производительности центробежного компрессора основаны главным образом на измеренных температурах, давлениях, расходах и составе газа, а также на правильно выбранном уравнении состояния. Тщательный выбор и размещение измерительных преобразователей необходимы для уменьшения погрешности испытаний. Надлежащее планирование испытаний также необходимо для определения рабочих условий и желаемой конечной цели испытаний.
Под редакцией Скотта Дженкинса
Ссылки
- Содержание этой статьи взято из материалов, представленных на Симпозиуме по турбомашинам и насосам 2018 года.
- ASME PTC 10-1997, Кодекс эксплуатационных испытаний компрессоров и выхлопных газов, Американское общество инженеров-механиков, www.
asme.org.
- ASME PTC 19-5-2004, Измерение расхода, Американское общество инженеров-механиков, www.asme.org.
- ISO 5389, Турбокомпрессоры. Код проверки производительности. Международная организация по стандартизации, www.iso.org.
- Брун, К., и Норед, М., Руководство по полевым испытаниям характеристик газовых турбин и центробежных компрессоров, выпуск 2.0, GMRC 2006.
- Allison, T.C., Moore, J.J., Rimpel, A.M., Wilkes, J.C., Pelton, R., Wygant, K., Опыт производства и испытаний с прямым лазерным спеканием металлов для закрытых крыльчаток центробежных компрессоров, Материалы 43-го симпозиума по турбомашиностроению, Хьюстон, Сентябрь 2014.
- Смит, Н.Р., Кларк, К., Эллисон, Т.С., Кейв, М., и Уилкс, Дж.К., Сравнение данных об аэродинамических характеристиках, полученных в результате тепловых измерений и измерения крутящего момента на рабочем колесе компрессора, Труды ASME Turbo Expo, Документ № GT2018-77016, Осло, Норвегия, июнь 2018 г.
- Курц Р.
и Брун К., О неопределенностях при полевых испытаниях производительности, Материалы ASME Turbo Expo, документ № GT2015-42035, Монреаль, Канада, июнь 2015 г.
Авторы
Натан Поернер — старший инженер-исследователь отдела жидкостных машин Юго-Западного научно-исследовательского института (6220 Culebra Road, San Antonio, TX 78238; телефон: 210-864-5111; электронная почта: [email protected]; www. swri.org). Он держит B.S. и М.С. степени в области машиностроения Техасского технологического университета. Его опыт работы в основном связан с полевыми измерениями и поиском и устранением неисправностей механических систем, в частности проблем с пульсацией и механическим резонансом. Эта работа поддерживается механическим и гидродинамическим моделированием. Poerner участвует в многочисленных исследовательских проектах, посвященных вращающимся и возвратно-поступательным механизмам.
Тим Эллисон — менеджер отдела динамики вращающихся механизмов в Юго-Западном научно-исследовательском институте (тот же адрес, что и выше; электронная почта: [email protected]). Его исследования в SwRI включают анализ конечных элементов, модальные испытания, контрольно-измерительные приборы и испытания производительности для приложений, включая турбомашины высокого давления, центробежные компрессоры, газовые турбины, клапаны поршневых компрессоров, высокочастотную вибрацию трубопроводов и испытательные стенды для динамики ротора, динамики лопастей и аэродинамических характеристик. . Он опубликовал более 50 статей по различным темам турбомашин и является помощником редактора ASME Journal of Engineering for Gas Turbines & Power. Он имеет докторскую степень. в области машиностроения из Политехнического института Вирджинии и Государственного университета.
Гектор Дельгадо возглавляет группу машиностроения в Юго-Западном научно-исследовательском институте (тот же адрес, что и выше: электронная почта: [email protected]). Дельгадо получил B.S. и М.С. степени в области машиностроения Университета Нуэво-Леон (Мексика) и Техасского университета в Сан-Антонио соответственно.