Как проверить масло в компрессоре холодильника: Ремонт холодильников в Краснодаре и пригороде! Отзывы !
холодильное оборудование и расходные материалы
Масло, применяемое для смазки холодильных компрессоров, очень хорошо смешивается с обычными хладагентами.
Сильная близость свойств масла и хладагентов является причиной многочисленных и, как правило, малоизученных проблем, которые могут вызывать механические (разрушение клапанов, заклинивание компрессора…), электрические (перегорание двигателя) и термодинамические (недостаток холодопроизводительности, нежелательные срабатывания предохранительных систем…) неисправности и поломки.
Предметом настоящего раздела является получение ответов на многочисленные вопросы, встающие перед большинством ремонтников.
А) Почему масло увлекается хладагентом?Все подвижные части поршневоrо компрессора (кривошипы, шатуны, цапфы, поршни…) требуют постоянной смазки, в противном случае они прижиrаются друr к друry, вызывая полное заклинивание.
В частности, в смазке нуждаются трущиеся между собой поршни и цилиндры (точнее, поршневые кольца и цилиндры).
В процессе нормальной работы, даже если компрессор новый или имеет безупречное механическое состояние, это неизбежно приводит к тому, что каждый раз вместе со сжатыми газами из цилиндра уходит в виде масляноrо тумана, состоящеrо из мельчайших капелек, какое-то очень небольшое количество масла (см. рис. 37.1).
Дополнительно к этому в периоды, когда компрессор стоит, масло, находящееся в eгo картере, неизбежно поглощает какое-то количество хладагента в зависимости от температуры масла и процедуры остановки компрессора.
Когда компрессор вновь запускается, резкое падение давления в картере вызывает быстрое вскипание хладагента, растворённомго в масле и, следовательно, образование газомасляной эмульсии (т. н. эффект «вспенивания»).
Такая эмульсия всасывается поршнями и нагнетается в конденсатор. В результате в момент запуска из компрессора в контур уходит самое большое количество масла.
Прежде всего, поскольку масло предназначено для смазки подвижных узлов компрессора, оно должно находиться не в контуре, а в картере.
Однако из за большой схожести свойств масла и хладагента невозможно воспрепятствовать тому, что какое-то количество масла регулярно проходит в нагнетающий патрубок компрессора.
Таким образом, с одной стороны необходимо по возможности максимально ограничить выброс масла из компрессора, а с другой стороны обеспечить, чтобы масло, которое ушло из компрессора, могло беспрепятственно возвратиться в картер для выполнения своих функций смазывающее о агента.
В самом деле, если количество вышедшеrо через нагнетающий патрубок масла будет превышать количество масла, вернувшегося через всасывающий патрубок (масло будет задерживаться в неудачно спроектированном контуре), то через какое-то время уровень масла в картере понизится до опасноrо предела, за которым нормальная смазка компрессора будет невозможной.
С другой стороны, если вместе с маслом в картер будет возвращаться аномально большое количество хладагента, его количество, растворенное в масле может стать очень большим. При запуске бурная дегазация масла, обусловленная резким падением давления в картере, приведет к образованию большоrо количества газомасляной эмульсии, что может вызвать срыв подпитки масляноrо насоса. Кроме тогo, образование большоrо количества эмульсии может привести к такому интенсивному выходу масла из компрессора, что к концу пускового режима картер окажется совершенно «пустым» и в течение более или менее продолжительноrо периода компрессор будет оставаться без нормальной смазки (характерное «вспенивание», которое сопровождает образование эмульсии, легко наблюдается в стекле указателя уровня масла). Поэтому настройка ТРВ на небольшой nepeгрев, уrрожая возможностью появления периодических гидроударов (самых легких), уrрожает также опасностью аномальных выбросов масла в контур.
Работа компрессора с повышенной частотой включений и выключении (либо в результате срабатывания предохранительных систем, либо по командам от системы регyлирования) также создает уrрозу опасного понижения уровня масла, поскольку при запусках оно выводится в контур наиболее интенсивно, а короткое время работы не дает ему возможности нормального возврата.
Заметим, что в этом случае положение не спасет даже предохранительный прессостат давления масла, который может быть установлен в компрессоре, поскольку он очень медленно реагирует на изменение давления, (собственное время eгo инерционности составляет около 2 минут), и повреждения, обусловленные плохой смазкой при каждом очередном запуске, могут накапливаться, приводя через более или менее длительный промежуток времени к непоправимым механическим разрушениям подвижных деталей компрессора.
Другая проблема возникает при неудачно спроектированной конструкции или прокладке трубопроводов, главным образом,всасывания. Действительно, вместо тогo, чтобы регyлярно возвращаться в картер компрессора, масло может накапливаться в застойных зонах или участках с отрицательным уклоном.
При опорожнении застойных зон масляная пробка может быть резко всосана компрессором, что приводит к сильному гидроудару, порождающему те же повреждения, что и обычный гидроудар.
Так, например, на рис. 37.2 вверху показано, что слишком большая длина L застойной зоны, в основном на всасывающей магистрали. приводит к тому, что в ней обязательно будет накапливаться значительное количество масла.
Давление Р2 будет падать до тех пор, пока разность давлений Р1 и Р2 не окажется достаточной для тогo, чтобы протолкнуть масляную пробку во всасывающую полость головки блока.
В этот момент в полость резко поступит большое количество масла. Такой прилив масла создает опасность возникновения сильногo гидроудара, последствия которого строго идентичны последствиям обычноrо гидроудара.
Очевидно, точно такие же проблемы могут возникнуть, если масло накапливается на участке трубопровода всасывания с отрицательным уклоном (см. рис. 37.2 внизу).
3аметим, однако, что опасность возникновения перечисленных проблем снижается, если всасывание производится через картер компрессора, а также если он оборудован эффективным устройством демпфирования гидроударов (отделителем жидкости).
Наконец, присутствие масла внутри трубопроводов создает на их внутренней поверхности тонкую изолирующую масляную пленку, что препятствует нормальному теплообмену между воздухом и хладагентом и снижает коэффициент теплоотдачи для конденсатора и испарителя.
Такое снижение интенсивности теплообмена особенно заметно в испарителе, где холодильное масло и хладагент легко разделяются из за низкой температуры.
Если в результате каких то проблем в холодильном контуре в негo попадает слишком многo масла, это может повлечь за собой снижение холодопроизводительности испарителя.
Причем потери холодопроизводительности могут быть столь значительными, что окажутся достаточными для тогo, чтобы появились признаки неисправности типа «слишком слабый испаритель» (в некоторых крайних случаях потери холодопроизводительности испарителя могут достигать 20%).
Вначале нужно напомнить, что в результате отличного перемешивания масла с хладагентом в жидком состоянии, циркуляция масла в конденсаторе и в жидкостной магистрали проходит без всяких проблем
Однако в магистралях всасывания и нагнетания хладагент находится в паровой (газовой) фазе, поэтому масло и хладагент склонны к разделению.
Следовательно, в этих магистралях могут возникнуть серьезные проблемы с перемещением масла, так как для eгo возврата в картер компрессора необходимо добиться свободноrо перемещения масла по холодильному контуру.
Проблема возврата масла имеет различную остроту в зависимости от расположения участков трубопроводов.
В горизонтальных участках (см. рис. 37.3) основная часть масла течет естественным образом в направлении наклона (если он существует). В отсутствие наклона, если скорость газа в трубопроводе низкая, масло стремиться под действием силы тяжести осесть на дно трубы и застаивается там.
Точно также, как скорость ветра порождает волны на поверхности моря, скорость хладагента над слоем масла порождает возникновение маленьких волн, которые перемещаются в направлении движения хладагента даже в отсутствие наклона, если скорость газа превышает 2,5 м /с
В вертикальных участках (см. рис. 37.4) проблема возврата масла немного осложняется действием силы тяжести, которая заставляет масляную пленку двиеаться вниз. Лоrично предположить, что на
вертикальных участках трубопроводов для преодоления силы тяжести и подъема масла в трубопроводе механическое воздействие газа на масло должно быть гораздо более значительным, чем на горизонтальных участках.
Действительно, эксперименты показывают, что масло легко поднимается в вертикальных трубопроводах, как всасывания, так и нагнетания, если скорость газа в них превышает примерно 5 м/с. С друrой стороны, если в какой то момент скорость газа в вертикальной трубке падает ниже 5 м/с, масло очень быстро остановится и начнет стекать вниз под действием силы тяжести.
ВНИМАНИЕ! Если диаметр вертикальной трубы больше 2 дюймов или если температура испарения
ниже 10° C, минимальная скорость газа, необходимая для подъема масла во всасывающих трубопроводах, расположенных вертикально, становится равной 8…9 м /с
3аметим также, что для всех горизонтальных трубопроводов рекомендуется минимальный наклон 12 мм/м в направлении движения потока.
Кроме тогo в общем случае считается, что скорость газа в трубопроводах не должна превышать 20 м/с с тем, чтобы сохранить в разумных пределах потери давления и уровень шума.
D) Влияние разности уровней на возврат масла
Первая проблема возникает, если конденсатор расположен над компрессором с разностью уровней более 3 метров.
При каждой остановке компрессора движение газа в маrистралях прекращается и масло, находящееся в вертикальном участке, под действием силы тяжести стекает вниз, создавая опасность ero накопления в нагнетающей полости головки блока.
Если высота компрессора над конденсатором превышает 3 метра (см. рис. 37.5), количество масла, которое может скопиться в этой полости, становится весьма значимым. Дополнительно к этому, из за тогo, что окружающая температура по сравнению с температурой нагнетания относительно невысока, при остановке компрессора может сконденсироваться более или менее значительное количество находящихся в магистрали нагнетания паров хладагента, и образовавшаяся жидкость также может стечь в полость нагнетания головки блока компрессора. Скопление там жидкоrо хладагента и масла создает опасность того, что при очередном запуске компрессора произойдет сильный гидроудар.
Точно такая же проблема возникает, если испаритель расположен ниже компрессора, поскольку при остановках последнеrо, масло, находящееся в восходящем трубопроводе, также стекает в нижнюю часть (см. рис. 37.6). Как и в случае нагнетающеrо трубопровода, количество накапливающеrося внизу масла становится значительным, если высота Н трубопровода превышает 3 метра.
Ситуация может еще более ухудшиться, если в застойную зону в нижней части восходящего трубопровода будет стекать масло, выходящее из испарителя, что в целом приведет к накоплению там значительного количества жидкости.
При запуске компрессора образовавшаяся в застойной зоне масляная пробка может попасть во всасывающую полость головки блока и спровоцировать возникновение сильного гидроудара.
Во избежание подобных гидроударов, являющихся причиной многочисленных поломок
клапанов, в тех случаях, когда разность уровней превышает 3 метра, необходимо в нижней части каждой восходящей трубы устанавливать маслоподъемную петлю, а горизонтальные участки прокладывать с наклоном в направлении движения потока.
На выходе из испарителя может возникнуть еще одна проблема, если жидкость, находящаяся в застойной зоне, представляет собой смесь масла с хладагентом (для получения такой смеси достаточно совсем немногo жидкоrо хладагента, вытекающеrо из испарителя в застойную зону при остановках компрессора). В момент запуска резкое падение давления во всасывающей магистрали вызывает очень бурное вскипание смеси в результате испарения хладагента, растворённого в масле.
При испарении хладагент поглощает тепло!
Необходимое тепло в значительной степени отбирается от трубопровода, что приводит к резкому падению eгo температуры. Иногда такое заметное охлаждение трубопровода может дойти до термобаллона ТРВ (см. рис. 37.6).
Тогда в момент запуска термобаллон может среагировать на резкое падение температуры и, следовательно, обусловить резкое закрытие ТРВ в особенно критический момент (в момент запуска давление конденсации понижено, также как и производительность ТРВ, и для тогo, чтобы как можно лучше запитать испаритель, необходимо, напротив. полное открытие ТРВ).
Таким образом, ТРВ аномально закрывается, пропуская ничтожно малое количество жидкости, и отключение компрессора предохранительным пресостатом НД обеспечено (неисправность легко обнаружить, дотронувшись до всасывающеrо трубопровода в месте установки термобаллона ТРВ).
Чтобы избежать таких проблем, настоятельно рекомендуется внизу любой восходящей магистрали всасывания, высота которой превышает 3 метра, устанавливать жидкостную ловушку (т. е. маслоподъемную петлю), и быть очень внимательным при прокладке трубопроводов, на которых будет установлен термобаллон, особенно тщательно соблюдая уклоны.
Мы уже увидели, что для обеспечения подъема масла по вертикальным участкам трубопроводов, скорость газа в них постоянно должна быть выше 5 м/с, какими бы ни были условия работы
Однако если разность уровней (высота Н на рис. 37.7) превышает примерно 7,5 м, проблема усложняется еще больше.
Начиная с этой высоты как на магистралях всасывания, так и на магистралях нагнетания, масляная пленка, поднимающаяся по стенкам трубопроводов, разрушается и отрывается от стенок, падая вниз под действием силы тяжести, даже если скорость газа выше 5 м/с.
Дополнительно к этому при нормальной работе каждый погонный метр трубопровода содержит какое-то количество масла.
Но чем больше растет разность уровней, тем больше повышается длина труб и тем больше возрастает содержание масла в этой трубе.
При большой разности уровней количество масла, стекающее вниз при каждой остановке компрессора, может оказаться настолько значительным, что полностью зальет маслоподъемную петлю, расположенную в нижней части восходящей трубы.
На восходящем трубопроводе нагнетания подобный наплыв масла при остановке компрессора создает опасность возврата масла в нагнетающую полость головки блока, если маслоподъемная петля окажется переполненной (см. схему на рис. 37.8).
Попадание масла в полость головки блока при очередном запуске компрессора может вызвать гидроудар, причем если существует опасность конденсации хладагента внутри трубопровода во время остановки компрессора, ситуация еще более ухудшается.
В восходящих трубопроводах всасывания, имеющих большую высоту, значительное количество масла, скапливающееся в маслоподъемной петле при остановке компрессора, во время очередноrо запуска может быть засосано в компрессор в виде масляной пробки и тоже привести к возникновению сильного гидроудара, смертельно опасноrо для клапанов (ситуация также может ухудшиться из за натекания в маслоподъемную петлю хладагента, выходящеrо из испарителя).
Во избежание перечисленных неприятностей, способных спровоцировать серьезные механические повреждения компрессора, в том случае, когда разность уровней очень большая, маслоподъемные петли необходимо устанавливать не более чем через каждые 7,5 метров восходящих трубопроводов как на всасывающей, так и на нагнетающей магистралях (см. рис. 37.9).
Такая конструкция позволяет маслу при работе установки подниматься от петли к петле и исключает
возможность возврата масла из верхней маслоподъемной петли в нижнюю.
Во время остановки в каждой маслоподъемной петле масло накапливается в разумных пределах, не переполняя ее.
3аметим, что разность уровней более 30 м совершенно не рекомендуется так как потери давления в трубопроводах такой высоты с 4-мя последовательно установленными маслоподъемными петлями становятся совершенно неприемлемыми (вообще-то соворя, всегда рекомендуется иметь как можно меньшую разность уровней).
Наконец, заметим, что установка маслоотделителя в нагнетающем трубопроводе компрессора (это техническое решение очень редко используется в воздушных кондиционерах) полностью не решает проблему возврата масла.
Действительно, даже тщательно подобранный и смонтированный маслоотделитель, несмотря ни на что будет пропускать от 1 до 2% масла, выходящеrо из нагнетающей полости компрессора.
Следовательно, все равно нужно обеспечить возврат этого масла в компрессор, и описанные выше требования к подбору и прокладке трубопроводов остаются в силе и для установок, оснащенных маслоотделителями.
Е ) Как изготовить маслоподъемную петлю?
Напомним, что маслоподъемная петля, обеспечивая улучшение процесса циркуляции масла в холодильном контуре, служит для удержания жидкости (масла или сконденсированноrо хладагента) в нижней части всех вертикальных трубопроводов, по которым хладагент циркулирует снизу вверх и длина которых превышает 3 метра.
Маслоподъемная петля не является емкостью для хранения жидкости и очень важно, что ее размеры должны быть как можно меньше с тем, чтобы уменьшить количество удерживаемой жидкости (место масла не в петле, а в картере компрессора) и избежать появления в контуре значительных масляных пробок, которые будут перемещаться по контуру (особенно во всасывающей магистрали компрессора).
Чтобы изrотовить маслоподъемную петлю, лучше всегo использовать покупной U-образный патрубок, если это возможно (радиус закругления очень небольшой), или два 90 градусных уrольника (но в любом случае сторона L должна быть как можно меньше, см. рис. 37.10).
Необходимо также всегда пунктуально соблюдать направление уклона (не менее 12 мм/м).
По мере накопления масла в маслоподъемной петле, eгo уровень
поднимается, снижая проходное сечение для газа, что вызывает
плавное повышение скорости газа.
Повышение скорости газа и eгo воздействие на поверхность масла способствуют разрушению этой поверхности (см. рис. 37.11) с образованием очень мелких капелек и увлечению масла в вертикальный трубопровод в виде масляноrо тумана и масляной пленки, которая продвиrается вперед по длине стенок трубопровода в результате механическоrо воздействия на нее проходящеrо газа (если eгo скорость не ниже 5м/с).
F) Проблема установок с переменной холодопроизводительностью
Эта проблема относится к установкам, в которых в процессе эксплуатации расход хладагента в контуре может меняться, например, когда имеется несколько параллельно работающих компрессоров, или когда может меняться число оборотов компрессора, или если регyлирование производительности осуществляется за счет исключения из работы отдельных цилиндров путем воздействия на всасывающие клапаны.
Действительно, если расход хладагента в контуре переменный и зависит от режима работы установки, скорость газа в трубопроводах также будет меняться. Для лучшего понимания рассмотрим в качестве примера установку, оборудованную двумя одинаковыми компрессорами, смонтированными в параллель, то есть установку с двумя ступенями мощности (100% или 50%).
Допустим, что диаметр восходящей магистрали этой установки с длиной 7 м был выбран из условия, чтобы при работе обоих компрессоров (при 100% расхода хладагента) скорость газового потока в магистрали была равна 6 м/с (см. рис. 37.12).
При полной мощности скорость газа выше 5 м/с и масло поднимается вполне нормально.
Однако, коrда один из двух компрессоров остановлен, расход хладагента вполовину уменьшается и падает примерно до 50% полного расхода. Поскольку диаметр трубы остался прежним, скорость газа в вертикальной трубе упадет примерно до 3 м/с, что не позволит маслу подниматься надлежащим образом.
Масло начнет накапливаться в маслоподъемной петле, закупоривая проходное сечение так, как если бы труба перекрывалась постепенно закрывающимся краном.
Разность давлений с одной и с другой стороны петли будет при этом обусловливать периодический подъем в трубе масляной пробки со всеми вытекающими из этоrо нежелательными последствиями, главным образом, если речь идет о всасывающей магистрали компрессора (опасность гидроудара, особенно на запуске).
Когда установка имеет несколько ступеней производительности, обусловливающих изменение расхода, диаметр трубопроводов, в которых хпадагент циркулирует снизу вверх, должен подбираться таким образом, чтобы обеспечь минимальную скорость газа не ниже 5 м/с при наименьшем расходе хладагента.
Однако в дальнейшем потребуется обеспечить более высокий расход, коrда установка начнет работать на 100% мощности. При этом нужно обеспечить следующие условия:
* Полные потери давления в трубопроводах (длина вертикальных участков + длина горизонтальных участков + местные сопротивления) не должны быть слишком высокими, то есть не выше перепада, эквивалентного температуре примерно 1 С, как для магистралей всасывания, так и нагнетания;
* Скорость газа никогда не должна превышать 20 м/с, так как это создает опасность возникновения в трубопроводах очень сильного шума.
Если диаметр трубопровода, выбранный исходя из условия обеспечения минимальной скорости газового потока не ниже 5 м/с при наименьшей мощности, становится слишком малым и приводит к значительным потерям давления при работе на полной мощности, возникает необходимость использования сдвоенных трубопроводов с тем, чтобы обеспечить бесперебойный подъем масла при любых условиях работы и при любом расходе хладагента.
При монтаже сдвоенных трубопроводов (см. рис. 37.13) диаметр малой трубы выбирается из условия обеспечения в ней скорости выше 5 м/с для минимальное о расхода хладагента.
Действительно, при пониженной мощности скорость газа в обеих трубах настолько мала, что масло не может подниматься и накапливается в маслоподъемной петле вплоть до полного перекрытия большой трубы.
С этого момента газ начинает проходить через малую трубу со скоростью, достаточной для нормального подъема масла. Обратная петля в верхней части трубопровода (поз.1 на рис. 37.13) предотвращает проход масла, поднявшегося по малой трубе, в большую трубу.
Когда мощность установки возрастет, повышение расхода хладагента протолкнет масло, собравшееся в ловушке, и газ вновь начнет циркулировать по обеим трубам.
Когда разность уровней большая, нужно устанавливать сдвоенные трубопроводы на каждом участке длиной не более 7,5 м, тщательно соблюдая изложенные выше требования и направления уклонов.
Тем не менее, несмотря на все, можно столкнуться с проблемой понижения уровня масла в картере компрессора установок с переменным расходом хладагента, даже если выбор диаметров и прокладка трубопроводов произведены по всем правилам.
Чтобы понять причину этоrо явления, рассмотрим в качестве примера 6 цилиндровый компрессор с тремя ступенями производительности (100%, 66% и 33%), обеспечиваемыми изменением числа действующих цилиндров, который расположен над испарителем.
Допустим, что при максимальной мощности (100%, задействовано 6 цилиндров) через нагнетающую магистраль компрессора вместе с хладагентом выходит 1,5 литра масла в час.
Поскольку конструкция установки и ее монтаж выполнены по всем правилам, вместе с хладагентом в компрессор возвращается такое же количество масла (то есть 1,5 л/час) и уровень масла по указателю уровня (см. рис. 37.14) находится в норме.
В какойто момент температура в охлаждаемом объеме падает и система реryлирования снижает производительность компрессора до 66% от номинала, исключая из работы 2 цилиндра (1 блок). Всасываемое компрессором количество хладаrента уменьшается и расход через компрессор падает до 66%
Но каждый килоrрамм приходящеrо в компрессор хладагента может содержать только cтpoгo определенное количество масла, которое не зависит от расхода, следовательно приход масла тоже упадет пропорционально падению расхода, то есть до 66% или примерно до 1 л/час (также, как и расход масла из компрессора).
Следовательно, через всасывающую магистраль в компрессор будет поступать с этого момента только 1 л/час масла, в то время как перед этим через магистраль нагнетания уходило 1,5л/час. Это значит, что количество масла, эквивалентное расходу 0,5 л/час, остается в контуре
Если компрессор расположен над испарителем, масло не может возвратиться в картер под действием силы тяжести. Следовательно, количество масла, эквивалентное расходу 0,5 л/час, остается в контуре, елавным образом, в испарителе, где падение температуры приводит к разделению масла и хладагента, и уровень масла в компрессоре падает (см. рис. 37.15).
Если система регyлирования переводит теперь компрессор на уровень 33% производительности, повторится точно такая же картина, поскольку расход хладагента станет еще меньше и будет уносить из компрессора еще меньше масла, однако и поступление масла во всасывающий патрубок тоже уменьшится.
В результате в контуре опять останется количество масла, эквивалентное eгo расходу 0,5 л/час, и уровень масла в картере вновь понизится (см. рис. 37.16).
Таким образом, если компрессор будет работать с мощностью 33% от наминала, количество масла, оставшееся в испарителе, окажется достаточным, чтобы уровень масла в картере заметно понизился. В этот момент, если задающий термостат отключит компрессор, ничто не позволит больше маслу, находящемуся в испарителе, возвратиться в картер.
При последующем запуске такая же картина будет повторяться всякий раз, когда компрессор будет переходить на режим пониженной производительности, а опасность понижения уровня масла будет еще более значительной вплоть до тогo, что обусловит либо серьезную механическую аварию из за плохой смазки, либо отключение компрессора датчиком давления масла (если он существует либо прохождение во всасывающую магистраль огромной масляной пробки (гyбительной для клапанов всасывания вследствие сильноrо гидроудара), если испаритель окажется слишком переполненным маслом.
Во избежание перечисленных явлений необходимо перед каждой остановкой компрессора по команде от регулятора каждый раз возвращать накопившееся в испарителе масло с тем, чтобы приеотовиться к последующему запуску.
Для этоrо остановки компрессора должны обязательно производиться с использованием метода
предварительного вакуумирования (см. раздел 29. Остановка холодильных компрессоров).
Замечание 1. В каждой маслоподъемной петле всегда остается более или менее значительное количество масла. Поэтому при первом запуске вновь собранной установки с большим числом ловушек считается допустимым понижение уровня масла в компрессоре.
Можно также перед запуском установки предварительно заполнить ловушки тем же маслом, что используется для смазки компрессоров.
Замечание 2. Постепенное исключение из обращения хлорфторуrлеродов CFC (RI2, R502…) и появление новых хладагентов серии фторуrлеводородов HFC (R134a, R404A…) с эфирными маслами вместо минеральных приводит к возникновению новых проблем в вопросах возврата масла (см. раздел 56. Проблемы, возникшие с появлением новых хладагентов).
Почему компрессор кидает масло и что нужно делать
Винтовые компрессоры широко используются в различных сферах. Их активно применяют в технических установках и другом оборудовании. Дизельный компрессор может пригодиться в загородном доме, на экспедиции, предприятии и в других местах, где необходимо нагнетать воздух в систему или выполнять другие операции. Винтовая компрессорная техника имеет высокий КПД, поэтому популярна как в быту, так и в промышленности.
Чтобы поддерживать дизельный компрессор в исправном состоянии, необходимо с установленной периодичностью проводить техническое обслуживание, с выполнением всех операций, которые предполагает завод изготовитель. Если не делать этого или эксплуатировать устройство в неправильном режиме, то со временем оно перестанет выполнять свою основную задачу и сломается.
Конечно, винтовой компрессор может выйти из строя и по другим причинам, не связанным с проведением обслуживания. Одним из признаков неисправности системы является вынос масла из компрессора. С этой проблемой достаточно часто сталкиваются владельцы, но определить причину этого явления самостоятельно достаточно сложно. Во-первых, это может быть один из множества возможных неисправностей компрессора. Во-вторых, чтобы понять суть проблемы, необходимо знать устройства генератора в целом и принцип его действия.
Определение места течи поможет определить, из-за чего происходит вынос масла из компрессора
Почему компрессор гонит масло
Чтобы определить причину выноса масла из компрессора, необходимо определить направление течи. Исключая все сверхъестественные и маловероятные варианты, останется всего несколько направлений, по которым масло может уходить из системы:
- уплотнение винтового блока;
- в систему оборудования, с которым работает генератор;
- в воздушный фильтр;
- в корпус компрессора;
Любой из этих путей выноса масла связан с различными неполадками. Нарушение герметичности в уплотнениях винтового компрессора приведет к появлению масла в поддоне компрессора. Еще одной причиной может быть изнашивание манжеты. При этом необходимо отметить, что заводская манжета может выйти из строя достаточно быстро.
Поступление масла в оборудование потребитель, с которым связан агрегат, означает, что свое функциональное предназначение не выполняет воздушно-масляный сепаратор. Чтобы устранить эту проблему, достаточно заменить сепаратор на исправный. Проблема также может быть связана с неисправным впускным клапаном.
Реже всего случается потеря герметичности трубопроводов. Это приводит к разбрызгиванию масла в компрессоре. Обычно это связано с неправильной транспортировкой или неаккуратным ремонтом. Иногда к растрескиванию трубок приводит неквалифицированное техническое обслуживание.
Слабым местом компрессора дизельного является дренажная линия. Проблемы, связанные с дренажной линии, которые могут привести к выносу масла из системы:
- недостаточная длина дренажной трубки, которая должна достигать чаши сепаратора;
- механические загрязнения дренажной линии;
- трещины и другие механические повреждения трубки;
- неправильно подключение дренажной трубки;
- использование неподходящего дренажного клапана;
Если не производить своевременное техническое обслуживание, то в первую очередь начнет загрязняться масляный контур. В него попадают различные механические загрязнения, такие как грязь, пыль, шлак. Для того чтобы справляться с такими проблемами, система оснащается тремя различными фильтрами, которые обеспечивают фильтрацию частиц, имеющих различные размеры. Когда эти элементы загрязняются, загрязняющие элементы принимает на себя сепаратор. В результате при резком перепаде давления элемент может взорваться, что приведет к выгону масла.
Если использовать в системе компрессорное масло, которое не подходит к установке по вязкости или другим свойствам, то начнется его унос. Необходимо быть внимательным при замене масла и заправлять строго по уровню. В случае полного заполнения смотрового окна необходимо сливать его часть, чтобы не вывести из строя сепаратор.
Вынос масла в ходе работы установки
Кратковременный унос масла может происходить в системе, когда подвергается длительным периодам холостого хода. Такое может происходить как с мобильными, так и со стационарными компрессорами. Это является следствием того, что сепаратор перенасыщается маслом. Как правило, происходит это тогда, когда компрессора начинает активно работать.
Повыситься унос масла может и при длительных периодах нагрузки. Когда установка долго работает на предельной мощности, создавая высокое давление, через 15-30 минут может произойти вынос масла. Снижение рабочего давления вернет все на свои позиции.
Использование пневмопотребителей, которые отличаются значительным потреблением сжатого воздуха, может также привести к высокому уровню уноса масла или же разрушению или разрыву сепаратора. В качестве такой установки может выступать кузнечный молоток, отличающийся амплитудными потреблениями значительных объемов воздуха.
Разрыв сепаратора также может произойти вследствие резких изменений давления на впускном клапане или во время неправильного выключения установки. Как правило, компрессоры, после нажатия кнопки выключения, останавливаются только через 30 секунд. Так происходит постепенное уменьшение давления.
Ремонт компрессоров
Помните, что точно определить причину выноса масла с компрессора и устранить неисправность может только квалифицированный специалист. Если вы хотите, чтобы ваше оборудование служило долго – доверьтесь профессионалам, которые имеют достаточный опыт и могут предоставить гарантию на ремонт.
ООО “ГК ПРОМОБОРУДОВАНИЕ” предлагает Вам качественный ремонт и обслуживание Ваших компрессоров. За 10 лет работы у нас накопился большой опыт в работе со сложным компрессорным оборудованием.
Наша компания выполняет все виды технического обслуживания и ремонта компрессоров. Профессионалы быстро выявят причину проблемы и исправят ее. Количество возможных вариантов, из-за которых происходит выгон масла, очень велик. Разобраться в этом вопросе, не зная устройство и принцип работы, а также особенности модели очень трудно. Специалисты сэкономят время для Вас и восстановят производительность компрессора и другие характеристики, которые имело оборудование при покупке. Оставьте заявку на бесплатную консультацию ниже, наши специалисты свяжутся с вами и помогут подобрать запчасти и комплектующие для вашего оборудования.
Какое масло заливать в компрессор: Вопросы и Ответы
СОДЕРЖАНИЕ
Компрессорное масло – материал для смазки, который обеспечивает качественную работу установки. Категорически не рекомендовано использование моторного масла в поршневых компрессорах, а в винтовые заливаются исключительно специальные смазочные материалы.
Масло, заливаемое в компрессор, позволяет значительно повысить КПД установки, а также снизить износ деталей и продлить срок безопасного и эффективного использования, снижает опасность самовозгорания. Анализируя, какие масла заливают в компрессоры, необходимо учесть целый ряд особенностей.
Главные характеристики масел
Можно выделить три основные характеристики, которые необходимо учитывать при выборе масла для компрессора: вязкость, температурные показатели и наличие присадок.
Вязкость
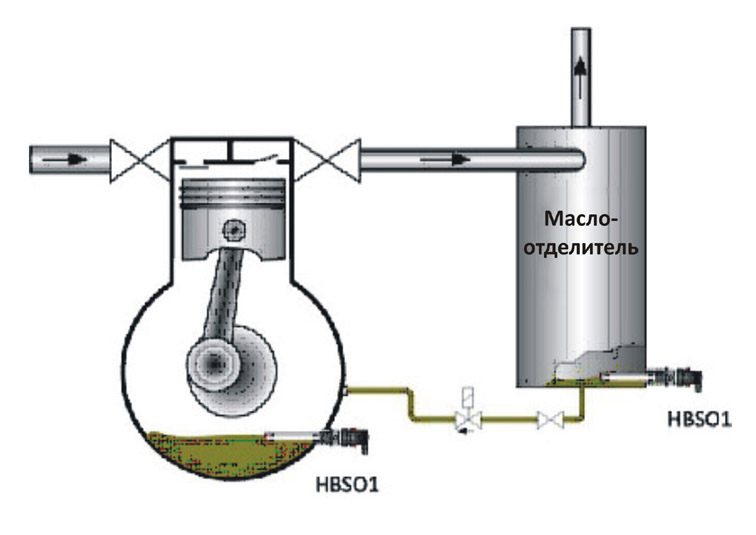
Оптимальным значением для заправки в компрессор является вязкость от 10 и до 12 единиц. Такое масло для компрессора не только хорошо держится на деталях, но и не создает большого сопротивления движению поршня.
Показатель вязкости «К» еще характеризует устойчивость к термоокислению – свойству смазки разлагаться при нагревании (под действием высоких температур). Чем выше показатель вязкости, тем при больших температурах масло способно сохранять свои свойства.
Присадки
Специальные добавки, которые улучшают характеристики масел, могут быть:
- противопенными, антиокислительными;
- моющими, противокоррозионными, диспергирующими;
- предназначенными для повышения термической стабильности.
На наличие присадок указывает буква «П» в маркировке, их состав и процентное содержание должны быть подробно указаны в описании. В качестве присадки может использоваться вода (для улучшения противопожарных свойств), но при этом ее содержание не должно превышать 1,5%.
Температурные характеристики
Масло сгорает на поверхности, нагретой до высокой температуры, загрязняя поршень и воздух внутри компрессора сажей, золой и другими продуктами, выделяющимися в результате горения. Если сравнивать два различных масла, то у более качественного материала температура вспышки будет выше. Для универсальных (всесезонных) масел она равна 110 °C.
Чтобы обслуживать поршневые компрессоры, рекомендовано заливать масло, у которого температура вспышки не ниже 140 °C. Также следует учесть такие параметры:
1. Температура самовоспламенения. Чтобы не допустить самовозгорания и сделать эксплуатацию компрессора безопасной, самовоспламенение масла не должно происходить при температуре меньше 350 °C.
2. Температура застывания масла. Используется и другое обозначение характеристики – потери текучести. Это самая низкая температура, при которой масло еще может течь (как пример – его можно перелить из канистры). Это важный параметр, если планируется использовать компрессор в осенне-зимний период и на открытом воздухе.
Какое масло лучше: синтетическое или минеральное?

Минеральные
Получаются в результате переработки нефти, обычно содержат минимальное количество присадок. Их основное преимущество – очень доступная стоимость. Но при этом минеральное масло имеет большие температурные ограничения. Его не рекомендуется использовать при отрицательных температурах. Оно сохраняет свои свойства при стабильном температурном режиме. Из-за неоднородности молекул минеральное масло быстрее теряет свои свойства.
Синтетические
В результате глубокой химической переработки исходного сырья и удаления примесей из нефти удается получить однородный по размеру молекул состав. Это позволяет минимизировать силу трения. Среди других преимуществ необходимо отметить следующие:
- синтетическое масло не теряет текучести при низких температурах;
- низкая окисляемость при нагревании, не разлагается под воздействием высокой температуры;
- повышенные антифрикционные качества;
- низкой коэффициент испаряемости, высокое значение температуры вспышки.
Синтетика дольше сохраняет свои смазочные свойства по сравнению со смазками на минеральной основе. Но при этом ее стоимость может быть в несколько раз выше.
Полусинтетические
Их получают путем смешивания синтетической и минеральной основы в соотношении 70% на 30%. Это позволяет получить масло с хорошими температурными и вязкостными характеристиками по доступной цене.
Периодичность замены
После этого масло рекомендовано менять после 500 часов работы, но не реже, чем один раз в год.

- побелело – это говорит о том, что процент содержания воды превышает установленные нормы;
- потемнело – причиной является сильный перегрев.
Для винтовых видов оборудования после 4000 часов работы необходимо провести замену не только смазки, но и масляного фильтра, а также сепаратора.
Алгоритм замены масла
Для замены смазки потребуется выполнить следующие операции (на примере компрессора FUBAG FC230/24 CM2):1. Прекратить работу компрессора, отключить его от сети, отсоединить все подключенные инструменты.
2. Дать деталям остыть.
3. Стравить воздух, закачанный в ресивер. Добиться нулевых показателей на манометрах давления.
4. Установить под картером компрессора емкость, куда будет стекать отработанное масло.
5. Снять пробку (гайку) заливного отверстия – она расположена в верхней части картера, на поршневом блоке компрессора.
6. Открутить гайку слива и дать маслу стечь.
8. Залить новое масло в компрессор, контролируя его уровень через смотровое стекло, при его отсутствии – с помощью щупа. Рекомендуется проводить заправку чуть выше отмеченного максимального уровня, так как масло из картера поступает для смазки всех узлов.
9. Спустя некоторое время необходимо проконтролировать уровень масла. Для оптимального режима работы компрессор должен находиться на высоте, составляющей 2/3 расстояния между максимальной и минимальной отметкой на смотровом стекле (щупе). При недостатке смазки компрессор может прекратить работу, при избытке – масло будет интенсивно подаваться в систему, что резко повышает риск гидроудара.
Нельзя смешивать масло от разных производителей. Содержащиеся в нем присадки, особенно при нагревании внутри компрессора, могут вступить в реакцию. Это приведет к их выпадению в осадок и оседанию на внутренних компонентах, провоцируя возрастание силы трения и ускорение износа устройства.
Определяемся с выбором: какое масло заливать в компрессор
Выбирая, какое масло заливать, чтобы обеспечить лучшие рабочие характеристики, следует отдавать приоритет требованиям производителя, которые указаны в техописании.
Часто использование любого другого, несертифицированного компанией масла, залитого в течение гарантийного срока, может стать причиной отказа производителей от выполнения своих обязательств. Для обслуживания линейки моделей FUBAG необходимо использовать масло FUBAG VDL 100. Даже после окончания гарантийного срока следует придерживаться той марки, которую рекомендует производитель.
Какое масло будет самым лучшим? Тут стоит придерживаться следующих правил:
- Для бытового компрессора, который не так интенсивно используется и находится в отапливаемом помещении, где температура не опускается ниже +5 °C, но при этом не превышает +25 °C, можно использовать минеральное масло. Это обеспечит оптимальное соотношение цена/качество.
- Для мобильных компрессоров, которые будут использоваться на открытом воздухе, лучше использовать синтетическое масло.
Если эксплуатацию оборудования будут осуществлять слабо подготовленные специалисты или компрессор не имеет постоянно закрепленного за ним работника, то лучше залить синтетику.
Соблюдение правил подбора масла – гарантия, что компрессор не только безотказно прослужит долгие годы, но и будет эксплуатироваться с лучшим соотношением цена/качество.
компрессор из холодильника (доработка) :: АвтоМотоГараж
Замена масла и долив до нужного уровня.
При работе компрессор имеет некую особенность – он немного гонит масло совместно с сжатым воздухом. Следовательно, масло нужно время от времени подливать, а после определённой наработки его вообще нужно полностью менять. По опыту трёхлетней эксплуатации компрессора могу сказать, что масла он гонит очень и очень мало. За всё время ушло не более 30ти – 40ка грамм. Принципиально до этой доработки не сливал масло ни с ресивера, ни с масловлагоотделителя. В итоге за время эксплуатации в ресивер вообще ничего не попало, всё собрал масловлагоотделитель. Теперь дальше. Контролировать уровень масла не представляется возможным (покрасней мере пока). И чтобы при доливе не перелить масло выше положенного уровня, было решено, что с компрессора сливать нужно всё масло, и после этого заливать нужный объём. В ходе этих размышлений выявился ещё один момент. При изготовлении компрессора, слив масла предусмотрен не был (слив был сделан только с ресивера).
Изготовление слива масла с компрессорного агрегата.
Слив изготавливается путём просверливания отверстия в корпусе компрессора. Корпус выполнен из толстой листовой стали около 4х – 5ти миллиметров. Этой толщины вполне достаточно для нарезания резьбы М6. После того как резьба готова завинчивается болт-пробка. Эта доработка кажется простой только на первый взгляд.
Инструмент для выполнения работ: керн, молоток, два сверла метчик, держатель метчика, два магнита, металлический круглый щуп. Детали: болт М6х10 (если подходящего болта по длине нет, то его нужно обрезать), медная шайба.
Итак, в нижней части корпуса компрессора сначала сверлится отверстие диаметром 2,0 – 3,0 мм, после чего сверлим отверстие диаметром 5 мм.
Далее метчиком нарезаем резьбу М6. Очень ответственный момент! В процессе нарезания резьбы очень важно чтобы внутри компрессора находилось масло. Это необходимо чтобы стружка и опилки, которые вдруг попадут внутрь (а они к сожалению туда немного попадут), вымывались маслом наружу. Ещё одно ухищрение – при нарезании резьбы – нужно прикрепить к метчику небольной магнит, чтобы он удерживал стружку на себе и не давал попадать внутрь.
Нарезать резьбу необходимо поэтапно, по полтора – два оборота, потом метчик нужно выкручивать и очищать (по крайней мере, я делал так).
Масло во время нарезания резьбы нужно будет подливать. После того как резьба нарезана, дожидаемся когда всё масло стечёт.
Теперь необходимо промыть изнутри компрессор маслом. Для этого можно воспользоваться слитым маслом, но перед этим очищаем его при помощи фильтра для краски. Для этого берём два фильтра, вставляем их друг в друга, внутрь помещаем магнит и переливаем масло из одной ёмкости в другую.
Завинчиваем пробку и заливаем масло. Затем вновь откручиваем пробку и опять сливаем масло. Пока масло вытекает, с помощью круглого щупа и прикрепленного к нем у магнита, пытаемся собрать частички металла просовывая внутрь отверстия щуп. Процедуру проделываем до тех пор пока щуп и вытекающее масло из компрессора не перестанут содержать металлические опилки.
Осмотрим слитое масло на наличие металлических частичек и если их нет, то завинчиваем пробку (болт с медной шайбой) на герметик и заправляем компрессор необходимым количеством чистого масла.
Самая трудоёмкая и муторная операция это отлов опилок, но она является значимой. От качества выполнения этой операции зависит ресурс компрессора.
И ещё один момент: после того как пробка закручена, к нижней части самого компрессора крепим магнит. На всякий случай для перестраховки вдруг что осталось из металлической стружки.
Работа по доработке закончена.
Как подключить холодильный компрессор, важные моменты
18 марта 2021
Подключение холодильного компрессора
Для того, чтобы подключить компрессор, необходимо знать, как он работает и в чем заключается его функция. Компрессор в холодильниках необходим для откачки нагретого хладогента, находящегося в испарителе, а в последствии, для нагнетания этого хладогента в конденсатор, расположенный на задней стенке. Конденсатор выполняет роль разжижения и охлаждения хладогента, а уже затем он оказывается в испарителе – так происходит процесс внутрикамерного охлаждения.
После того, как принцип работы компрессора понятен, необходимо изучить из чего он состоит сам. В большинстве случаев, в наше время используют поршневые компрессоры, но лучше проверить, какой компрессор находится в распоряжении при установке.
Конденсатор играет не маленькую роль в составляющей холодильника. Он необходим для теплообмена. Коэффициент полезного действия холодильника повышается на двадцать процентов, при наличии в нем конденсатора. Следует знать, что залог хорошо работающего холодильника – это бесперебойная работа конденсатора.
Компрессор и конденсатор холодильника подключены между собой, а обратной трубкой происходит подключение к испарителю. Для того, чтобы компрессор не сгорел раньше, чем пройдет год или пару лет, на которые он был куплен, то необходимо его проверить на наличие пробоев, так как при их наличии, ток в холодильнике будет сильно превышать норму.
Если было принято решение, подключить к сети компрессор холодильника без конденсатора, то это будет допустимо только в тех случаях, когда было решено использовать компрессор в других назначениях.
Для подключения компрессора к холодильнику, подойдет как компрессор со старого холодильника, так и новый. Важной задачей будет – правильно подключить его. Инструкция по установке компрессора следующая:
- Снять компрессор с холодильника, при этом оставить масло в нем, не расплескав.
- Необходимо проверить работоспособность компрессора с помощью подключения его к сети.
- Взять реле, подходящее к конкретному холодильнику.
- Холодильник оборудуется ресивером.
- Соединить холодильник с компрессором шлангами (для стеклоомывателя вполне подойдут).
- Проверять периодически уровень масла.
Приобрести качественный товар, выбрать из множества оборудования то, что необходимо, а также получить консультацию – можно на Нашем сайте!
Масляные системы циркуляционного компрессора – Справочник химика 21
МАСЛЯНЫЕ СИСТЕМЫ ЦИРКУЛЯЦИОННОГО КОМПРЕССОРА [c.174] Система охлаждения компрессорной установки закрытая, двухконтурная. Охлаждающая вода подается к цилиндрам компрессора, к воздухоохладителям приводного электродвигателя и к масляному холодильнику системы циркуляционной смазки под давлением не более 0,3 МПа и с температурой не выше 30 С. Нагретая вода поступает в общецеховой сливной коллектор, откуда насосами подается на аппараты воздушного охлаждения, расположенные вне помещения компрессорной станции. [c.340]
Машинист выполняет следующие работы по контролю за смазкой компрессора проверяет давление в системе циркуляционной смазки, которое должно быть в пределах 1,8—2 атм-, проверяет открытием контрольных краников поступление масла на все точки следит за нагревом коренных подшипников по показаниям термометров расширения или манометрическим термометрам, за нагревом сальников — на ощупь, параллелей рам и промежуточных фонарей — на ощупь контролирует температуру масла до и после масляного холодильника (подавать следует столько воды, чтобы температура масла после холодильника не превышала + 35°С) периодически переключает секции масляного фильтра и производит чистку выключенной секции поддерживает установленный для нормальной работы уровень масла в маслосборнике и маслонасосах агрегата смазки цилиндров и сальников следит за плотностью всех соединений маслопровода если имеются качающиеся опоры промежуточных фонарей и цилиндров, то один раз в смену проверяет их смазку.
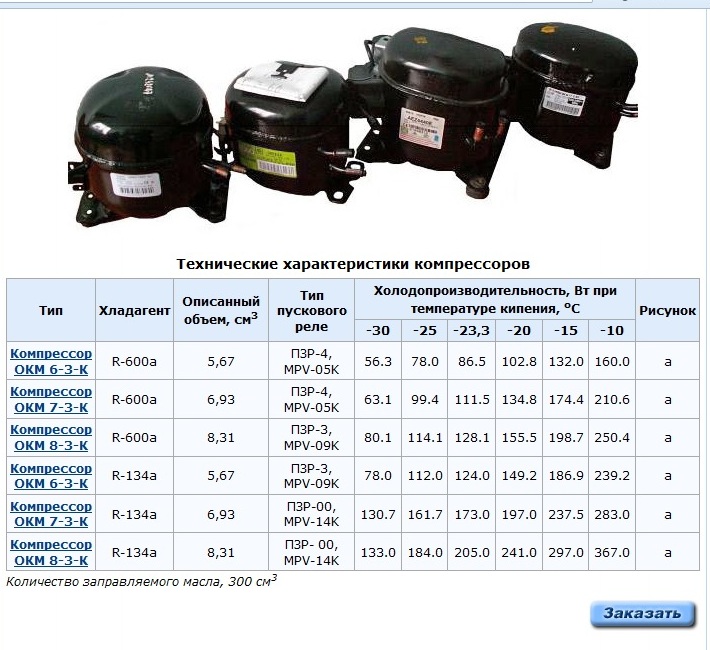
Постепенное падение давления масла в системе циркуляционной смазки происходит по причинам неплотности в соединениях трубопроводов масляной коммуникации надо подтянуть болты на фланцах, пропускающих масло. Если при этом течь не устраняется, следует остановить компрессор, выпустить масло и заменить прокладки на фланцах. Если засорена приемная сетка масляного насоса, ее нужно прочистить при работе компрессора если засорен масляный фильтр, надо перейти работать на другой фильтр. [c.219]
Монтаж циркуляционной смазочной системы. Циркуляционная смазочная система (рис. 26) включает следующие основные узлы шестеренный масляный насос 1 с приводом от электродвигателя или от коленчатого вала компрессора, фильтры грубой 2 и тонкой 3 очистки, холодильник 4, перепускной клапан 5 маслопровода, коллектор 6 для распределения масла с маслопроводами. На крупных компрессорах имеется бак 7 для масла со змеевиком для подогрева или охлаждения масла. [c.65]
Такой компрессор представляет собой однокорпусную четырехступенчатую машину со спиральными отводами газа в выносные межступенчатые холодильники после каждой ступени (колеса). Чугунный литой корпус компрессора состоит из двух половин, рабочие колеса закрытого типа. Случайно возникающие при работе турбокомпрессора осевые усилия воспринимаются упорно-опорным подшипником, расположенным со стороны привода. Принудительная циркуляционная смазка подшипников осуществляется от общей масляной системы. Количество масла, подаваемого в подшипник, регулируется диафрагмами, установленными на входе смазки в подшипник. Расход масла 80—100 л/ч, его подача производится шестеренчатым насосом. [c.48]
Первый пуск компрессора. Его осуществляют обычно без клапанов. Перед пуском компрессора необходимо проверить уровень масла в системе циркуляционного смазывания и баке многоплунжерного насоса пустить воду для охлаждения компрессора и масляного холодильника.

Принципиальные схемы систем маслоснабжения компрессорных агрегатов. На рис. 1-2 приведена принципиальная схема системы циркуляционного маслоснабжения центробежной компрессорной машины с электроприводом. Компрессор / приводится электродвигателем 5 через редуктор 4. Валы двигателя редуктора и компрессора соединены муфтами 2. Масло на смазку подается главным зубчатым маслонасосом 3, приводимым от вала редуктора. Для обеспечения маслом подшипников в период пуска и останова компрессора служит пусковой насос 9 с электроприводом. Главный масляный насос забирает масло из маслобака 10 и прокачивает его через маслоохладители 8. [c.18]
У поршневых компрессоров могут быть вспомогательные механизмы, получающие движение от коленчатого вала масляные насосы для смазки механизма движения, потребляющие мощность масляные насосы (лубрикаторы) для смазки цилиндров компрессоров, мощность которых Л/ ,2. В некоторых компрессорах (например, на транспортных установках) может быть установлен циркуляционный водяной насос для системы охлаждения компрессора (его мощность обозначим Л ) и вентилятор для обдува цилиндров, водяных или воздушных холодильников. Потребляемую вентилятором мощность обозначим Тогда мощность, потребляемая вспомогательными механизмами, в общем случае будет [c.57]
Для шестеренчатых насосов циркуляционных систем поршневых компрессоров принят следующий ряд производительностей 6—10—16—25—40— 50—80—120—160—250—400 л/мин [67]. Этим рядом производительностей обеспечиваются масляные системы всех отечественных компрессоров. [c.346]
Система смазки. Масляная система центробежных нагнетателей и компрессоров выполняется принудительной, циркуляционной. [c.427]
Смесь газа и реакционной жидкости выходит с верха колонны 8, охлаждается водой в холодильнике 9 и попадает в сепаратор 10 высокого давления. В нем окись углерода и водород отделяются от жидкости, а непрореагировавший пропилен (степень конверсии более 90%) и пропан остаются главным образом в жидкой фазе. Газ циркуляционным компрессором 6, компенсирующим потери давления в аппаратуре, снова подают на реакцию, но часть его выводят из системы во избежание чрезмерного накопления инертных примесей. Жидкость из сепаратора 10 проходит редукционный клапан И, где ее давление снижается почти до атмосферного, и попадает в сепаратор 12 низкого давления. Там отделяются растворенные газы том числе пропилен и пропан) и происходит частичное разложение карбонилов кобальта с выделением окиси углерода. Так как с газом уносится значительное количество летучих масляных альдегидов, его промывают в абсорбере 18 высшими спиртами и затем используют в качестве топлива. Раствор альдегидов из абсорбера 13 направляют на разделение или на гидрирование. [c.652]
В период работы компрессора необходимо следить за давлением и температурой газа по ступеням, не допуская отклонения от нормального технологического режима температура подшипников не должна превышать 60 °С. Нужно систематически наблюдать за работой системы циркуляционной смазки и пресс-масленок (избыточное давление масла должно быть не менее 1 ат, а уровень масла в бачке не должен опускаться ниже контрольной черты) за состоянием масляной коммуникации, не допуская пропусков масла через неплотности за работой межступенчатых холодильников и подачей воды в них (температура газа по выходе из холодильника должна быть не выше 30—40 °С). Наконец, необходимо вести непрерывный контроль за работой собственно компрессора, прислушиваясь к появлению всевозможных посторонних шумов, стуков, ударов и др. [c.43]
Долгое время машины и механизмы консервировали только углеводородными смазками — техническим вазелином или пушечным (нефтяным) салом. В настоящее время ассортимент защитных смазок расширился благодаря появлению консервационных масел и летучих ингибиторов коррозии. Однако углеводородные защитные смазки до сих пор не утратили своего ведущего положения. Около 75% всех изделий из металла защищают от коррозии пластичными смазками. Лишь внутренние, труднодоступные поверхности механизмов, оборудованных циркуляционными масляными системами (двигатели внутреннего сгорания, компрессоры и т. п.), консервируют специальными маслами (НГ-203, К-17 и др.). [c.138]
Первый пуск компрессоров осуществляют обычно без клапанов. Перед этим необходимо проверить уровень масла в циркуляционной смазочной системе и баке лубрикатора, пустить воду для охлаждения компрессора и масляного холодильника. Если компрессор будет работать под нагрузкой, то воду пускают в холодильники всех ступеней. Затем включают масляные насосы, если они имеют индивидуальные приводы. Для компрессоров, у которых насосы приводятся в движение от коленчатого вала, масло первоначально подают к цилиндрам и сальникам, вращая вал лубрикатора вручную на 50.

Системы смазывания компрессоров. В поршневых компрессорах применяются две разновидности циркуляционных систем смазывания без смазочного насоса и с применением насоса. Циркуляционная система смазывания без смазочного насоса применяется только в поршневых воздушных компрессорах малой производительности, которые не предназначены для длительной работы. Смазывание по такому принципу отличается простотой устройства, но не обеспечивает эффективного отвода теплоты от трущихся пар. В этих компрессорах подвод масла к трущимся парам механизма движения и цилиндрам осуществляется разбрызгиванием. При работе компрессора черпачок, прикрепленный к шатуну, или специальное кольцо, насаженное на вал, захватывают масло, в результате чего во внутренней полости картера образуются масляный туман и брызги, которые смазывают стенки цилиндров, поршневые пальцы, коренные и шатунные подшипники. При таком методе смазывания требуется [c. 38]
Для компрессоров, у которых привод масляного насоса циркуляционной системы смазки механизма движения осуществляется от коленчатого вала машины, откачку масла из маслобаков осуществлять общим для нескольких машин насосом. [c.26]
В воздушно-реактивных двигателях узлами, нуждающимися в смазке, являются шариковые и роликовые подшипники газовой турбины и компрессора, подшипники приводов и вспомогательные механизмы. Большинство реактивных двигателей снабжено циркуляционной системой смазки и только немногие имеют незамкнутую систему с выбросом отработанного масла в атмосферу. На фиг. 173 показана принципиальная схема масляной системы реактивного двигателя. [c.358]
В ЦКМ применяют главным образом циркуляционные системы смазки под давлением. Масло подается на подшипники компрессора, подшипники и зубчатую передачу редуктора, зубчатые соединительные муфты, подшипники электродвигателя, герметичные масляные уплотнения концов вала машины, в систему регулирования и защиты. [c.270]
Смазку цилиндров производят под давлением с помощью лубрикаторов, т. е. многоплунжерных насосов с приводом от механизма компрессора. Каждый плунжер насоса подает строго определенное количество масла в отдельную точку смазки. Система смазки цилиндров проточная, т. е. без замкнутого контура, Система смазки механизма движения — циркуляционная. Она осуществляется принудительно по замкнутому контуру маслосборник — масляный насос (обычно шестеренный) — фильтр-холодильник — детали механизма движения — маслосборник (рис. 17.9). [c.224]
Цикл оборотной системы охлаждения состоит из циркуляционных насосов, объектов охлаждения, охладительных устройств для воды, из трубопроводов и расширительных баков. Объекты охлаждения — двигатели и компрессоры, а также газовые, масляные и водяные потоки в охладителях. В качестве охладительных устройств служат градирни, холодильники (оросительные и кожухотрубные) и брызгательные бассейны. [c.284]
Следует периодически очищать воздушный и масляный фильтры компрессора от пыли и грязи, клапаны, воздухопроводы, холодильники и газосборники — от нагара, холодильники и водяные рубашки цилиндров — от накипи и в установленные сроки заменять масло в циркуляционной системе смазки. [c.345]
Так обычно называют компрессоры, работающие с небольшим перепадом давления и осуществляющие циркуляцию газа в замкнутой системе высокого давления. Циркуляционные насосы изготовляют преимущественно поршневого типа с масляной смазкой и приводом от паровой машины или асинхронного электромотора с фазным ротором. Регулирование оборотов последнего производится реостатом, включаемым в цепь ротора. Хорошие результаты дает применение многоскоростных электродвигателей для ступенчатого регулирования. Регулирование [c.145]
Газовые холодильники бывают промежуточные, концевые и байпасные. Для охлаждения масла, идущего на смазку подшипниковых узлов и на охлаждение роторов, применяются масляные холодильники. В установках с винтовыми компрессорами сухого сжатия чаще всего применяется для охлаждения вода. Однако применяется и воздушное охлаждение, в особенности для небольших машин. Маслосистема установки обеспечивает смазку подшипников и синхронизирующей пары, а также охлаждение роторов. В нее входят пусковой и циркуляционный насосы, фильтры грубой и тонкой очистки, система трубопроводов. Для обеспечения подогрева масла при пуске, если ее температура ниже допустимой, предусматривается подвод к маслоохладителю горячей воды или установка подогревателя. [c.12]
Системы смазки центробежных компрессорных машин. В ЦКМ применяются главным образом циркуляционные системы смазки под давлением. Масло подают на подшипники компрессора, подшипники и зубчатую передачу редуктора, зубчатые масляные уплотнения кон-, цов вала машины, в системы регулирования и защиты компрессорной установки. [c.14]
Рекомендуются также для масляных ванн или циркуляционных систем большинства механизмов, таких как цапфа, подшипники, антифрикционные подшипники, кривошип, гипоидные передачи, не требующих использования масел с ЕР-свойствами, сцепления, работающие в масляной ванне. Используются для смазывания воздушных компрессоров. Масла класса вязкости VG 32,46, 68 и 100 соответствуют уровню V L DIN 51506, а класса вязкости VG 150,220, 320 и 460 соответствуют уровню VBL. Могут применяться в картере многих двигателей с раздельной системой смазывания и водяным охлаждением поршней. [c.27]
Защита компрессора с. в. д. от повышения давления нагнетания осуществляется реле высокого давления 34, от повышения температуры нагнетания — реле температуры 35, от нарушения работы масляного насоса — реле контроля смазки 36. В схеме предусмотрен автоматический перепуск масла из маслоотделителя в картер компрессора через поплавковый регулятор 37. Приборы защиты от гидравлического удара (общей для всех компрессоров данной системы) устанавливают на вертикальном циркуляционном ресивере или отделителе жидкости (реле уровня 38) и на промежуточном сосуде (реле уровня 39). По действующим правилам техники безопасности защита от гидравлического удара дублируется, т. е. устанавливают два реле, выполняющих одну и ту же функцию. Работоспособность защитных реле уровня периодически проверяют, подавая жидкий хладагент в коллектор через вентиль 40 при закрытом вентиле 41. [c.165]
Компрессор имеет две автономные системы смазки. Смазка кривошипно-шатунного механизма циркуляционная от шестеренчатого насоса с индивидуальным приводом от электродвигателя. Насосная установка состоит из маслосборника, масляного холодильника, двухсекционного фильтра, перепускного клапана, за-порно-регулирующей арматуры и контрольно-измерительных приборов. Цилиндры и сальники смазываются маслом от поршневых лубрикаторов, приводимых в действие электродвигателем. [c.143]
Смазку к коренным подшипникам и параллелям крейцкопфа подводят по трубкам. Масло к кривошипной головке шатуна поступает от коренного подшипника по сверлениям в валу. Подвод масла к крейцкопфной головке шатуна осуществляется в машинах по-разному либо от кривошипной головки по каналу в стержне шатуна, либо от параллелей по сверлениям в корпусе и пальце крейцкопфа. Смазка параллелей промежуточных и концевых фонарей также входит в циркуляционную систему. В последних конструкциях компрессоров с целью упрощения масляных трубопроводов и предохранения масла от загрязнения смазку параллелей фонарей производят от системы смазки цилиндров. [c.155]
Для каждого компрессорного агрегата в цехах имеются подробные инструкции по уходу и обслуживанию. Прежде всего проводится тщательная подготовка к пуску. Проверяют уровень масла в маслобаке циркуляционной системы смазки, а в поршневых компрессорах — и уровень в корпусах масляных насосов агрегата смазки цилиндров и сальников. Включают электродвигатели насосов смазки и проверяют подачу масла во все места смазки. [c.159]
Масляная система агрегата (компрессор—редуктор—электродвигатель) — принудительная циркуляционная. Масло всасывается из бака через фильтры и обратный клапан в главный масляный насос и нагнетается в систему под давлением 5 кг/сж . Высокое давление масла необходимо для работы автоматического противопомпажного устройства. Смазка подшипников осуществляется давлением масла 0,5 0,75 кг1см . Понижение давления обеспечивается установкой редукционного клапана. По пути к подшипникам масло охлаждается в водяных маслоохладителях. [c.103]
Наблюдение за смазкой является наиболее важным элементом Е общем комплексе работ по ежедневному обслуживанию компрессора. Нарушение режима смазки может привести к весьма быстрому выходу компрессора из строя. К каждой точке должно подводиться определеппое количество соответствующего масла. В техническом паспорте каждой машины указаны нормы расхода масла. В цилиндры должно подаваться такое количество масла, чтобы на его стенках и поршнях образовалась сплошная тонкая масляная пленка. Недостаточная смазка усиливает износ зеркала цилиндра и поршневых колец, излишняя способствует увеличению отложений нагара в клапанах, трубопроводах и на поршнях, что приводит к ухудшению работы компрессора, к авариям и взрывам установок. Недостаточная подача масла к трущимся поверхностям механизма движения может привести к чрезмерному их нагреву. Температура подшипников компрессора не должна превышать 50—60° С. Снизить температуру нагрева можно повышением давления смазки в системе циркуляционной смазки. Если нагреваются подшипники с кольцевой и капельной смазкой, то необходимо промыть подшипник на ходу большими порциями свежего масла и после промывки дать обильную смазку. [c.295]
На фиг. 219 и 220 изображены типовые системы циркуляционной смазки механизма движения горизонтальных и вертикальных компрессоров. Масло всасывается шестеренчатым насосом 3 из маслосборника 1 через приемный фильтр 2. В вертикальных компрессорах роль маслосборника выполняет картер (фиг. 220). Из шестеренчатого насоса масло под давлением 2—4 кПсм поступает в фильтр грубой очистки 6. Затем основной поток масла, пройдя через холодильник 7 и узлы трения 8, стекает в маслосборник или картер. Около 5—15% производительности масляного насоса после фильтра грубой очистки направляется в фильтр тонкой очистки 5 и затем очищенное масло стекает в маслосборник. Для поддержания постоянного давления перед фильтром грубой очистки устанавливается перепускной клапан 4, который при превышении давления масла перепускает часть его в маслосборник, минуя основной круг циркуляции. Наличие перепускного клапана облегчает работу масляной системы при пуске машины, когда вязкость холодного масла велика и для перемещения всего расхода масла через систему требовалось бы создание насосом большого напора. [c.343]
Обязательной принадлежностью циркуляционной системы является перепускной клапан для регулирования давления масла и манометры. На масляной магистрали следует ставить два манометра — до фильтра и после него, для своевременной очистки фильтра. Давление масла в системе циркуляционной смазки выбирают от 1,0 до 4,0 кПсм , большие значения — для многооборотных компрессоров. Циркуляционную смазку применяют при длительной работе компрессоров. В небольших и средних машинах в качестве маслосборника часто используют поддон картера и не устанавливают холодильник, в котором при малых количествах масла нет необходимости. [c.171]
Смазка компрессоров осуществляется двумя независимыми маслосистемами. Первая система смазки —от многоплунжерного насоса (лубрикатора) —предназначена для подачи масла в цилиндры и сальники. В компрессорах без смазки цилиндров эта система смазки отсутствует. Вторая (циркуляционная) система предназначена для смазки кривошипно-шатунного механизма. В блок смазки входят шестеренчатый масляный насос, щелевой фильтр и масляный охладитель. Конструкция масляного фильтра позволяет без остановки машины очнидать фильтрующие элементы скребками, поворачиваемыми рукояткой. [c.228]
Лабораторная конструкция циркуляционного насоса производительностью 1000 л час сжатого газа, при чйсле оборотов п = 250 об/мин., изображена на рис. 74. Насос работает при давлении до 1000 ат. Это насос двойного действия с обыкновенными тарельчатыми клапанами, применяющимися у рассмотренного выше компрессора на 1000 ат. Смазка цилиндра масляная, замкнутая, масло возвращается из первого по ходу газа маслоотделителя 1. Регулировка производительности на ходу производится байпасом 2, перепускающим часть газа из системы нагнетания во всасывающую линию. Подача при этом способе регулирования довольно часто колеблется из-за попадания в вен- [c. 148]
Первые пуски и остановки компрессора проводят в следующем порядке. Пускают охлаждающую воду и проверяют слив ее в воронки из всех линий. Проверяют уровень масла в Гу .асляыо.м баке циркуляционной смазочной системы и резервуаре плунжерного насоса. Пускают в работу масляный агрегат. Давление в циркуляционной смазочной системе доводят до рабочего. Подачу масла ко всем точкам цилиндров и сальников проверяют по контрольным крапам и по смотровым стеклам в плунжерном насосе. Если подача масла осуществляется приводом от коленчатого вала, то перед пуском прокачивают масло с помощью ручного насоса. Проверяют исправность контрольно-измерительных приборов, предохранительных клапанов. Коленчатый вал с помощью валоповоротного устройства проворачивают на один-два оборота для проверки отсутствия помех и равномерного распределения масла по трущимся поверхностям. Затем устройство для поворота вала выводят из зацепления с зубчатым венцом электродвигателя и стопорят в этом положении. [c.81]
Для заполнен1 я водой контуров и пуска системы к работе необходимо подготовить в первую очередь источник электроэнергии для привода электродвигателей и всех насосов системы охлаждения. На схеме, приведенной па рис. 116, источником электроэнергии является электростанция, оборудованная двигателями внутреннего сгорания, система охлаждения которых включена в общую централизованную циркуляционную систему охлаждения КС. В таких случаях при опробовании централизованной циркуляционной системы охлаждения КС двигатели электростанции можно охлаждать по временной схеме, которая выбирается в каждом случае отдельно и зависит от конструктивных особенностей централизованной циркуляционной системы КС. Временная схема охлаждения двигателей электростанции состоит из водонапорной башни 44 или пневмоустановки, водопровода, масляного холодильника 35, полостей охлаждения двигателя 37, трубопроводов открытого контура 38, охлаждения масляных. холодильников, компрессорных цилиндров 34, газомоторных компрессоров 2, верхнего поддона градирни 17 и бассейна градирни 22 с вентиляторной установкой 16. По этой схеме вода для охлаждения двигателей электростанции подается из водонапорной башни или пневмоустановки. После охлаждения двигателя 37 вода по трубопроводам 38 поступает в верхний поддон градирни 17, а из него — в бассейн градирни 22. Целесообразность такой временной схемы заключается в том, что одновременно с охлаждением двигателей электростанции можно заполнить открытый контур системы охлаждения градирни. [c.157]
Порядок технического обслуживания
2. Порядок технического обслуживания
Безотказная работа тепловоза зависит от его своевременного технического обслуживания. Ниже приведен перечень и содержание работ, которые необходимо выполнять при техническом обслуживании и текущих ремонтах.
Техническое обслуживание ТО-1.
Дизель.
1) Произвести наружный осмотр дизеля, приборов и арматуры.
2) Проверить уровень масла в картере и регуляторе, при необходимости добавить масло.
3) Проверить уровень воды и при необходимости добавить воду в расширительный бак.
4) Проверить уровень жидкости в жидкостном манометре, который должен быть на нулевой отметке шкалы.
5) Проверить легкость хода реек, отключенных на 1-й позиции топливных насосов цилиндров.
6) Проверить, нет ли зазора между прижимаемыми пружиной рычагами механизма управления топливными насосами при перестановке этого механизма из нулевого положения в положение максимальной подачи топлива. Проверить на нулевой позиции контроллера разность выходов реек отключенных и работающих топливных насосов.
7) Проверить крепление форсуночных трубок.
8) Слить отстой топлива из топливного бака и фильтра грубой очистки топлива (каждое четвертое ТО-1).
9) Проверить затяжку хомутов стартера [зазор между хвостовиком и венечной шестерней должен быть в пределах (3±0,3) мм], при необходимости произвести дозатяжку (каждое восьмое ТО-1).
10) Слить грязное масло из поддона дизеля, фильтров и масляных баков. При обнаружении воды в масле сдать пробу для анализа в лабораторию. Если анализ подтвердил наличие воды, устранить причину ее попадания в масло.
11) Осмотреть паровоздушный клапан в крышке заливочной горловины водяного бака, нажатием на стержень проверить легкость его хода в направляющей втулке (каждое восьмое ТО-1).
12) Слить отстой воды из корпусов воздушных фильтров.
13) Промыть воздухоочистители дизеля [в условиях большой запыленности (100—500 мг/м3) каждое восьмое ТО-1, нормальной запыленности — один раз в месяц].
Гидропередача.
1) Проверить, нет ли следов течи масла по наружной поверхности гидропередачи из разъемов корпуса, по поверхностям прилегания крышек люков, фланцев и т. д.
2) Проверить уровень масла в верхнем и нижнем картерах гидропередачи. Уровень масла должен совпадать с отметкой на щупе верхнего картера и находиться между верхней и нижней отметками щупа нижнего картера. При необходимости долить масло.
3) Проверить давление масла, идущего на смазывание УГП, которое должно быть не менее 0,07 МПа (0,7 кгс/см2) на нулевой позиции контроллера и 0,15—0,2 МПа (1,5—2,0 кгс/см2) при номинальной частоте вращения коленчатого вала. Температура масла при замерах давления должна быть в пределах 60—98 °С. Давление масла должно быть устойчивым (не должны наблюдаться резкие скачки или колебания стрелки манометра). Устойчивое давление бывает при прогретой гидропередаче, когда температура корпуса не ниже 60 °С.
4) Проверить четкость реверсирования на поездном и маневровом режимах.
5) Провернуть рукоятки путевых фильтров и фильтра системы управления.
6) Проверить, нет ли посторонних шумов внутри работающей гидропередачи.
Экипажная часть.
1) Осмотреть ходовую часть тепловоза (колесные пары, реактивные тяги, карданные валы, тормозное оборудование, осевые редукторы). В случае обнаружения течей в осевом редукторе уровень смазки в нем контролировать на каждом ТО-1, при отсутствии течей — на ТО-3 (один раз в месяц).
2) Проверить работу автосцепок.
3) Проверить выход штока тормозного цилиндра (должен быть не менее 150 мм), состояние тормозных колодок, рычажной передачи и воздушной системы тормоза (каждое четвертое ТО-1).
4) Проверить уровень смазки в опорах на раме тележки и масленках для смазывания шкворней (каждое четвертое ТО-1).
Вспомогательное оборудование.
1) Проверить соединение топливного, масляного, воздушного и водяного трубопроводов, убедиться в отсутствии подтеков и ослаблений соединений (без надобности резьбовые соединения не подтягивать).
2) Проверить, нет ли течи масла и утечки воздуха в наружных соединениях компрессора, течи масла по разъемам корпусов, крышкам, люкам и валам гидроредуктора привода компрессора, привода вентилятора и редуктора генератора
3) Проверить крепление агрегатов дизеля и соединение дизеля и УГП с упругой муфтой и рамой тепловоза, а также крепление приводов компрессора, вентилятора и генератора.
4) Слить конденсат из главных резервуаров.
5) Проверить уровень масла в корпусе компрессора и давление в системе смазки. Если уровень масла приближается к нижней риске маслоуказателя, долить масло. Работа компрессора при опускании уровня масла в картере за нижнюю риску недопустима. Давление масла должно быть не ниже 0,15 МПа (1,5 кгс/см2).
6) Произвести очистку масляного фильтра компрессора поворотом рукоятки на два-три оборота.
7) Очистить компрессор от пыли, грязи.
8) Проверить уровень масла в корпусах воздушного фильтра.
9) Проверить, нет ли посторонних шумов внутри гидроредуктора привода компрессора, привода вентилятора и редуктора генератора.
Электрооборудование.
1) Проверить работу регулятора напряжения и величину поддерживаемого им напряжения.
2) Осмотреть аккумуляторную батарею, при необходимости долить в банки дистиллированную воду.
Техническое обслуживание ТО-2 производится в период между ТО-1 и ТО-3 по указанию руководителя депо.
Техническое обслуживание ТО-3. Выполнить работы, предусмотренные ТО-1 и, кроме того, произвести операции, перечисленные ниже.
Дизель.
1) Проверить работу цилиндров на минимальной частоте вращения коленчатого вала без нагрузки.
2) Через люки блока цилиндров осмотреть шплинтовку гаек болтов подвесок и шатунных болтов, шпилек поршня, а также рабочую поверхность втулок цилиндров и поршней. Проверить осту-киванием затяжку шатунных болтов и шпилек поршня.
3) Прокачать систему смазки дизеля и убедиться в поступлении масла к шатунным и коренным подшипникам, втулкам верхних головок шатунов, на охлаждение поршней, к рычагам привода клапанов и гидротолкателям.
4) Осмотреть клапанный механизм и проверить крепление контргаек и состояние штанг.
5) Проверить величину зазоров на масло в гидротолкателях.
6) Промыть центробежный фильтр масла.
7) Промыть фильтр грубой очистки масла; при перепаде давления 0,15 МПа (1,5 кгс/см2) фильтр необходимо промыть, не дожидаясь ТО-3.
8) Отобрать пробы воды и масла и произвести анализ.
9) Проверить и при необходимости восстановить крепление топливных насосов (на первом ТО-3 после ввода дизеля в эксплуатацию и после каждого ТР-2 и ТР-3).
10) Проверить крепление гаек тяг привода управления топливными насосами, зашприцевать смазку ЖРО в соединения рычажной передачи и смазать этой смазкой сухари механизма управления топливными насосами.
11) Заменить фильтрующие элементы фильтра тонкой очистки топлива, если перепад давления достиг 0,17 МПа (1,7 кгс/см2).
12) Промыть фильтр грубой очистки топлива.
13) Очистить от нагара сопло эжектора.
14) Осмотреть зубья диска валоповоротного механизма и при наличии забоин зачистить их.
15) Проверить размер от торца зубчатого венца диска до торца шестерни и зазоры в зацеплении шестерни стартера и зубчатого венца.
16) Заменить масло в системе, если истек срок его службы, при этом перед заливкой свежего масла очистить масляную ванну и фильтрующую сетку маслозаборника. Заменить фильтрующие элементы в корпусе фильтра тонкой очистки масла в случае замены масла. При перепаде давления 0,18 МПа (1,8 кгс/см2) элементы заменить, не дожидаясь указанного срока. Гидропередача.
1) Промыть фильтр откачивающего насоса.
2) Промыть путевой фильтр, установленный перед холодильником.
3) Снять масляный фильтр системы управления и промыть его.
4) Проверить чистоту клапанов опорожнения гидромуфты (работа проводится при первом ТО-3 после пуска тепловоза в эксплуатацию, а далее только на ТР-1 и на первом ТО-3 после замены масла в гидропередаче).
5) Проверить состояние внешних крепежных деталей (болтов, гаек, винтов, шпилек), в случае ослабления произвести подтяжку и стопорение.
6) Проверить работу фиксатора сервоцилиндров путем подъема и опускания штока фиксатора вручную. Поршень фиксатора в этом случае должен перемещаться без заеданий.
7) Проверить, нет ли заклинивания стержня механической блокировки, при необходимости отрегулировать ее. Зазор между барабаном и стержнем блокировки должен быть 0,05—0,8 мм.
8) Проверить крепление блокировочного клапана.
9) Зашприцевать солидол Ж (ГОСТ 1033—79) в масленки сервоцилиндров.
10) На каждом третьем ТО-3 снимать блокировочный клапан, проверять люфт хвостовика (допускаемый люфт 1,5 мм). При повышенном люфте заменить пружину хвостовика. Проверку производить щупом, замеряя зазоры между стержнем пружины и втулкой наконечника. Проверить герметичность резиновых манжет, при необходимости манжеты заменить.
11) Проверить целостность изоляции электропроводки, состояние открытых частей электромонтажа. Пыль, грязь и масло с проводов удалить. Устранить повреждения изоляции.
12) Открыть крышки конечных выключателей фиксатора, проверить состояние контактов и надежность подсоединения к ним проводов. При необходимости отрегулировать положение подвижной контактной колодки относительно неподвижных контактов при нейтральном положении сервоцилиндров. Неподвижные контакты конечного выключателя должны занимать примерно среднее положение между контактными пластинами подвижной колодки. Подгоревшие контакты конечного выключателя зачистить стеклянной шкуркой.
13) Проверить нажатие контактов на подвижную колодку, которое должно быть 4—6 Н (0,4—0,6 кгс).
14) Проверить надежность крепления электропневматических вентилей, убедиться в отсутствии утечки воздуха. У вентилей, имеющих утечку воздуха, притереть клапаны, неисправные вентили при невозможности ремонта заменить.
15) Снять крышки контактных барабанов сервоцилиндров. Проверить состояние контактов и надежность подсоединения проводов к ним. Загрязненные и подгоревшие контакты зачистить стеклянной шкуркой. Контактное нажатие должно быть 4—10 Н (0,4—1,0 кгс). Контакты в замкнутом положении должны находиться посередине контактных пластин барабанов. При необходимости контактное нажатие и положение контактов относительно контактного барабана отрегулировать путем смещения контактной стойки в пазах кронштейна или смещения контактов в пазах панели.
Экипажная часть.
1) Проверить крепление фланцев карданных валов, осевых редукторов и реактивных тяг.
2) Подтянуть крепеж разъемов осевого редуктора (на втором ТО-3 после ввода тепловоза в эксплуатацию).
3) Проверить уровень масла в нижнем картере осевого редуктора, при необходимости добавить масло.
4) Проверить уровень смазки в полости осевого упора буксы щупом; уровень должен быть не ниже 5 мм и не выше нижней кромки контрольного отверстия.
5) Добавить смазку в подшипники реактивных тяг и в подшипники и шлицы карданных валов согласно карте смазки.
Вспомогательное оборудование.
1) Промыть воздушные фильтры кузова машинного отделения [в условиях сильной запыленности (100—500 кг/м3) эту работу выполнять через каждые 15 ТО-1].
2) Проверить наружное состояние приводов компрессора, генератора, вентилятора и крепление подпятника вентилятора.
3) Осмотреть швы приварки лопастей вентилятора и убедиться, что в лопастях нет трещин.
4) При необходимости обдуть секции холодильника сжатым воздухом (в летнее время). Продуть холодильник компрессора сжатым воздухом.
5) Проверить крепление опор генератора и тумбы компрессора, а также компрессора к тумбе.
6) Проверить дюритовые соединения и трубопроводы.
7) Проконтролировать работу клапанов и подачу масла насосом, проверить натяжение клиноременной передачи вентилятора компрессора; осмотреть воздушные фильтры, при необходимости промыть их [при сильной запыленности воздуха (1 г/м3) воздушные фильтры промывать через каждые 20 ч работы компрессора]. Производить первую и вторую смены масла в картере компрессора, последующие смены — при ТР-1.
8) Убедиться в отсутствии течи масла по сальникам маслоохладителя.
Электрооборудование.
1) Продуть сухим сжатым воздухом электрические машины и аппараты.
2) Осмотреть электроаппараты, электропровода и их крепление, пайку наконечников. Проверить сопротивление изоляции цепей вспомогательного оборудования и цепей управления. Подтянуть болты, винты и гайки крепления проводов к аппаратам. Убедиться в надежности крепления датчиков давления.
3) Проверить чистоту поверхности силовых и блокировочных контактов всех реле и контакторов. Контакты, имеющие повреждения и подгары, зачистить.
4) Осмотреть крепление аккумуляторных ящиков в отсеках и перемычек между элементами. Проверить и записать в журнал значение напряжения и данные о плотности и уровне электролита во всех элементах батареи.
5) Очистить от пыли и осмотреть электрические машины.
6) Проверить на ощупь нагрев подшипников качения электрических машин (непосредственно после остановки дизеля).
7) Осмотреть коллекторы, нет ли на них почернений, обга-ра, задиров. Поверхность коллектора должна быть гладкой, полированной с красновато-фиолетовым оттенком. Проверить механизм щеткодержателей, давление пальцев на щетки, затяжку шунтов и наконечников, износ щеток и состояние их поверхностей. Негодные щетки заменить. При замене запрещается устанавливать на одном коллекторе щетки разных марок. При установке новых щеток их следует притереть к поверхности коллектора при помощи тонкой стеклянной шкурки, протягивая ее по направлению вращения.
8) Убедиться в отсутствии обуглившейся или поврежденной изоляции катушек полюсов, соединений обмоток полюсов и якоря.
| Маневровый тепловоз ТГМ6а |
Секреты смазки холодильных компрессоров
Компрессоры являются очень чувствительными компонентами, которые необходимо правильно смазывать, чтобы обеспечить длительный срок службы. Смазка должна не только смазывать все детали внутри компрессора, но и справляться с хладагентом, с которым она контактирует (в случае компрессоров холодильных установок и кондиционеров).
Некоторые смазочные материалы лучше работают с определенными хладагентами, и это должно быть сбалансировано с потребностями компрессора, чтобы выбрать надлежащие свойства базового масла и присадок.Понимая, как смазочные материалы взаимодействуют с хладагентами, а также требования к смазочным материалам, вы можете гарантировать, что ваши компрессоры будут работать максимально эффективно и результативно.
Как работают компрессоры
Функция компрессора довольно проста. Газ поступает в компрессор под низким давлением, где сжимается, а затем выходит под более высоким давлением. У этого сжатия есть несколько побочных продуктов, наиболее распространенными из которых являются тепло и влага.Эти побочные продукты очень вредны не только для здоровья машины, но и для здоровья смазки.
Хотя компрессоры могут использоваться в различных областях, в этой статье основное внимание будет уделено компрессорам в системах охлаждения или отопления, вентиляции и кондиционирования воздуха (HVAC). В этих приложениях система хладагента обычно является герметичной и замкнутой. В большинстве этих систем требуется вакуумирование контура перед заправкой хладагентом.
Втягивая эти линии в глубокий вакуум, влага внутри линий испаряется и удаляется, сохраняя систему максимально сухой. Это помогает уменьшить количество воды, образующейся в результате процесса сжатия.
Тип компрессора
Как и большинство машин, компрессоры бывают разных типов в зависимости от области применения. Как правило, тип необходимого компрессора определяется хладагентом или требуемым объемом охлаждающей способности.Существует три основных типа компрессоров, используемых с хладагентами: поршневые, роторные и центробежные.
Поршневые компрессоры работают аналогично автомобильному двигателю. Поршень скользит вперед и назад в цилиндре, который всасывает и сжимает хладагент низкого давления, направляя его вниз по потоку под более высоким давлением.
Часто поршневые компрессоры представляют собой многоступенчатые системы, что означает, что нагнетание одного цилиндра будет вести на входную сторону следующего цилиндра. Это обеспечивает большее сжатие, чем одноступенчатое. Эти компрессоры имеют множество смазываемых деталей, таких как цилиндры, клапаны и подшипники.
Ротационные компрессоры обычно используют набор винтов или лопастей для всасывания газа и его сжатия в камере сжатия. Это можно сравнить с работой лопастного насоса. Подобно поршневым компрессорам, эти системы имеют множество смазываемых компонентов, включая шестерни, подшипники, клапаны и т. д.
Центробежные компрессоры используют вращательное движение привода для вращения ряда крыльчаток, которые обеспечивают действие сжатия.Эти системы часто вращаются со скоростью несколько тысяч оборотов в минуту. Смазочный материал должен быть достаточно жидким, чтобы правильно смазываться на этих скоростях, но также и достаточно густым, чтобы выдерживать тепло и загрязнение хладагентом, которые могут возникнуть.
Для всех этих компрессорных систем необходимо тщательно выбирать базовое масло, присадки и класс вязкости смазочного материала. Совместимость со сжимаемым хладагентом, пожалуй, самый важный фактор при выборе базового масла, так как не все смазочные материалы могут справиться с этим типом загрязнения.
Пакет присадок обычно должен обладать некоторыми противоизносными свойствами, а также деэмульгируемостью в случае загрязнения влагой. Вязкость варьируется в зависимости от нагрузки, скорости и температуры, при которых будет работать компрессор.
Понимание холодильного оборудования
Холодильное оборудование произвело революцию во многих отраслях промышленности. Почти на каждом заводе используется какое-либо охлаждение, либо для отвода тепла, либо просто для комфорта сотрудников.Принцип работы цикла охлаждения довольно прост. Он включает в себя закон идеального газа и то, как газы претерпевают изменение температуры при изменении давления.
Компрессор действует как насос для циркуляции хладагента. Хладагент выходит из компрессора в виде газа под высоким давлением и поступает в конденсатор. Здесь газ конденсируется в жидкость, которая затем течет по трубе, пока не достигнет дозирующего устройства. Это дозирующее устройство часто называют ТРВ, поршнем или дросселем.
По сути, он сужает отверстие в линии и вызывает большой перепад давления на задней стороне. Когда давление падает, падает и температура хладагента.
Сразу за дозирующим устройством находится испаритель. Здесь происходит передача тепла. Воздух, проходящий через испаритель, теплее желаемого. Тепло воздуха поглощается хладагентом в испарителе, а затем переносится обратно в конденсатор, где оно удаляется. Компрессор – это то, что вызывает это движение.
Возможно, вы слышали выражение, что кондиционеры или холодильники не охлаждают, а на самом деле перемещают тепло. Именно так работает цикл. Тепло перемещается из места, где оно нежелательно, в место, где его можно высвободить. Вы можете испытать этот эффект в жаркий летний день, подойдя к внешнему блоку кондиционирования воздуха (конденсатору). Воздух, выходящий из верхней части конденсатора, будет горячее окружающего воздуха.
Типы хладагентов
Хладагенты должны быть способны поглощать и передавать тепло.Существует несколько типов хладагентов, которые выбираются исходя из желаемой температуры. Хладагенты должны легко переходить из жидкого состояния в газообразное. Именно это изменение состояния допускает резкое падение температуры после прохода через дозирующее устройство. В зависимости от используемого хладагента вы можете получить очень низкотемпературное охлаждение или просто базовую холодопроизводительность.
Возможно, наиболее известными типами хладагентов являются хладагенты на углеводородной основе.Это похоже на то, что вы купили бы для своего дома или автомобиля. Их часто называют такими названиями, как R-22, R-134a и т. д. Аммиак — еще один распространенный хладагент, используемый в основном на промышленных объектах. Он хорошо работает и может достигать низких температур для охлаждения или замораживания.
В общей сложности существуют десятки различных хладагентов, состоящих из хлорфторуглеродов (CFC), водородсодержащих CFC (HCFC) и соединений фтора и углерода (HFC), а также их комбинаций.
Смазочные материалы для компрессоров
Смазочные материалы выполняют несколько функций в компрессорной системе. Конечно, они должны уметь смазывать машину. В некоторых системах смазка должна действовать как охлаждающая жидкость, а также как герметик. Вот почему так важно выбрать правильную смазку для вашего компрессора. Если вы сомневаетесь, уточните у производителя правильное масло для системы.
Смазочные материалы для компрессоров часто представляют собой специальную смесь присадок и базовых масел, чтобы обеспечить необходимые смазывающие свойства, сохраняя при этом совместимость с хладагентом.Любая несовместимость базового масла и хладагента может иметь катастрофические последствия для оборудования.
Большинство смазочных материалов для компрессоров являются синтетическими. Это позволяет им иметь более длительный срок службы и лучше справляться с трудностями системы, чем жидкости на минеральной основе. Большинство домашних кондиционеров теперь используют смешанный хладагент, известный как R-410a. Базовое масло на основе полиэфира (POE) используется для смазывания системы, но это масло также может отделяться от хладагента.
Хотя совместимость между хладагентом и смазкой, возможно, является наиболее насущной проблемой с точки зрения смазки, есть и много других.Например, загрязнение влагой может быть очень вредным для некоторых синтетических базовых масел, которые гидролитически нестабильны. Влага вступает в реакцию с базовым маслом с образованием кислот, изменяет вязкость и ухудшает смазочные свойства масла. Это может привести к преждевременному выходу из строя компрессора, а также к неправильному охлаждению системы.
Проблемы со смазкой встречаются в любой системе. Один из способов избежать проблем со сжатием газов — просто исключить смазку из уравнения. Это частое явление, поскольку «сухие» компрессоры получают все более широкое распространение. «Сухой» относится к отсутствию масла в камере сжатия.
Если смазка не находится в камере сжатия, вероятность того, что она смешается с хладагентом и вызовет проблемы, гораздо меньше. Однако в мокрых или затопленных компрессорах масло находится в камере сжатия и тесно смешивается с хладагентом. В этих системах совместимость смазки с хладагентом имеет первостепенное значение.
Многие крупные компрессоры используют систему принудительной смазки, которая включает масляный резервуар, трубопровод и насос.Насос нагнетает масло через трубопровод в компрессор, где оно смазывает и охлаждает, а затем возвращает обратно в резервуар. Эти системы позволяют фильтровать, охлаждать и отделять газы и воду от масла во время его эксплуатации.
Компрессоры меньшего размера обычно представляют собой системы смазки со статическим корпусом, в которых компрессор удерживает масло, а система полностью герметична. При условии очистки и герметизации перед вводом в эксплуатацию система этого типа имеет низкую вероятность выхода из строя смазки.Чаще всего эти системы будут работать годами без замены масла.
Масло находится в компрессоре, чтобы смазывать его, но часть масла будет течь по линиям хладагента. В некоторых случаях необходимо использовать маслоуловитель или заглушку, чтобы масло не засоряло линии и не снижало охлаждающую способность системы.
Отбор проб масла
На промышленных предприятиях компрессорные системы, как правило, являются одними из наиболее важных машин.Поэтому важно периодически получать образцы масла, чтобы проверять исправность смазки и машины. Среди анализов масла, проводимых для этих жидкостей, есть элементный анализ, анализ вязкости и анализ продуктов износа.
Необходимо контролировать вязкость, поскольку разбавление хладагента может привести к снижению вязкости и увеличению износа машины.
В некоторых случаях образцы нефти необходимо дегазировать перед отправкой в лабораторию или анализом. Поскольку газ расширяется с температурой, это может привести к увеличению давления в бутылке, что приведет к утечке или выплескиванию масла при открытии бутылки.
Хотя с этими бутылями можно использовать крышки для сброса давления, помните, что каждый раз, когда вы открываете бутылку, вы подвергаете ее загрязнению, что может повлиять на результаты подсчета частиц.
При надлежащем уходе и внимании компрессоры в ваших холодильных системах могут безотказно работать долгие годы.При замене масла в этих системах имейте в виду, что оно должно быть совместимо с хладагентом и жидкостью, ранее использовавшейся в системе.
Наконец, старайтесь, чтобы каждый компрессор был герметичным, чистым, прохладным и сухим. Если вы сможете добиться этого, вы будете сохранять прохладу, даже когда температура на улице становится жаркой.
67% | специалистов по смазочным материалам говорят, что пробы масла периодически берутся из компрессоров на их заводе, основываясь на недавнем опросе, проведенном MachineryLubrication.![]() |
Практический совет по компрессорному маслу
Компрессорное масло: все, что вам нужно знать
Все компрессоры кондиционеров DENSO поставляются в сборе, предварительно заполненными компрессорным маслом соответствующего типа.
Компрессорное масло предназначено для смазки и охлаждения движущихся частей компрессора.Масляная пленка также защищает резиновые уплотнения в линиях хладагента и соединениях, уменьшая количество утечки хладагента. Однако существуют огромные различия в типах и качестве компрессорного масла. Чтобы гарантировать надлежащую циркуляцию масла
в контуре хладагента, компрессорное масло должно быть устойчивым к давлению и температуре во всех условиях эксплуатации. Автомастерские должны заправлять компрессор только рефрижераторным маслом, одобренным производителем автомобиля или компрессора, а также избегать использования универсальных или всесезонных масел.
Осторожно, универсальное масло!
Недостаточная смазка из-за универсального масла является второй наиболее распространенной причиной выхода из строя компрессора кондиционера
Анализ претензий по гарантии на компрессоры кондиционеров DENSO показывает, что в четверти всех случаев автомастерские использовали не то масло PAG, которое необходимо для компрессоров DENSO. Использование неправильных масел, таких как универсальные масла или смеси масел, неизбежно приводит к заклиниванию и повреждению. Это связано с тем, что универсальные масла, часто предпочитаемые автомастерскими, представляют собой масла PAO или минеральные масла с вязкостью, отличной от вязкости синтетических масел PAG.PAO-масла плохо смешиваются с PAG-маслами и хладагентами R134a или R1234yf, что приводит к плохой смазке и повышенному износу.
Кроме того, из-за разной вязкости между цилиндром и поршнем образуется более тонкая масляная пленка, что приводит к заклиниванию или сокращению ожидаемого срока службы компрессора. Чтобы определить правильный тип масла, всегда обращайтесь к идентификационной табличке компрессора, прикрепленной к задней или боковой части компрессора. На новой этикетке также будет отображаться количество масла внутри нового компрессора.
В некоторых случаях это может отличаться от спецификации автомобиля! Поэтому всегда проверяйте данные производителя автомобиля.
Убедитесь, что используется правильное количество масла
Основные действия при снятии компрессора:
- После восстановления хладагента: При удалении хладагента некоторое количество компрессорного масла смешивается с хладагентом и удаляется из контура хладагента вместе с хладагентом. Очень важно, чтобы это масло было слито на станции технического обслуживания кондиционеров и точно измерено его количество.Слитый объем необходимо заправить в контур хладагента при повторном заполнении хладагентом.
- После снятия старого компрессора: Слейте масло из компрессора и измерьте количество.
Ознакомьтесь с руководством по установке компрессора, чтобы узнать о соответствующей процедуре слива масла.
Внимание! Необходимо слить от 30 до 50 % от общего количества масла. В противном случае система может быть перегружена из-за заправки слишком большого количества компрессорного масла или УФ-красителя утечки во время обслуживания кондиционера.Для систем с хладагентом до 1000 грамм допустимо от 3 до 5 см3 УФ-красителя для утечек!
Распределение масла в системе кондиционирования (справочные значения, варьирующиеся в зависимости от температуры наружного воздуха и нагрузки на двигатель)
Советы по установке компрессора:
Все компрессоры кондиционеров DENSO представляют собой готовые узлы, предварительно заполненные соответствующим типом компрессорного масла.
Если система была промыта: Оригинальные компрессоры DENSO, которые поставляются с правильным количеством масла, могут быть установлены напрямую. Систематически проворачивайте компрессор вручную для равномерного распределения масла. Это позволит избежать повреждений, когда компрессор начнет движение или во время запуска.
Если промывка системы НЕ требуется: Используйте следующий расчет, чтобы подтвердить правильное количество масла, которое необходимо удалить из нового компрессора кондиционера DENSO.
Пример расчета:
Общий объем масла в новом компрессоре (А) составляет 120 см³.
Количество масла, слитого из старого компрессора (В), составляет 50 см³.
Количество масла, которое необходимо удалить (C) из нового компрессора, равно A-B, 120-50= 70 см³.
3. В некоторых случаях необходимо доливать масло. Для некоторых применений необходимо доливать масло. Например, если имеется один и тот же номер детали для одинарного и двойного циклов испарителя или когда количество масла в новом компрессоре отличается от технических характеристик автомобиля. В этом случае всегда проверяйте данные производителя автомобиля, чтобы подтвердить правильность количества масла.Никогда не добавляйте масло непосредственно в компрессор, всегда добавляйте его в конденсатор, ресивер-осушитель или второй контур испарителя.
Специальные инструкции для компрессоров 5SE/SL, типы
Масло для воздушного компрессора — как проверить и сколько использовать
Воздушные компрессорымогут стать основой нашей мастерской. Если они сломаются, мы мало что сможем сделать в этот день. Поэтому важно правильно за ними ухаживать. Мониторинг масла является одним из лучших методов, когда речь идет о надлежащем обслуживании воздушных компрессоров.
Необходимо следить за маслом воздушного компрессора, чтобы убедиться, что компрессор хорошо смазан. Выработав привычку регулярно проверять масло в воздушном компрессоре, вы будете знать, когда вам нужно его заменить. Постоянное наличие достаточного количества масла обеспечивает охлаждение и герметичность воздушного компрессора, что продлевает срок его службы.
Если ваш воздушный компрессор изнашивается или ломается, его ремонт может быть очень дорогостоящим. Читайте дальше, чтобы узнать, как мониторинг масла предотвращает повреждение компрессоров.
Важность контроля масла воздушного компрессора
При использовании смазываемого воздушного компрессора важно проверять масло, потому что:
1.Масло действует как чистящее средство
Воздушные фильтрыпредназначены для улавливания большинства загрязняющих веществ и частиц до того, как они попадут в компрессор. Однако некоторые наночастицы, которые трудно уловить, все еще находятся в воздухе.
Эти наночастицы могут быть в форме свободной воды из водяного пара в воздухе. Они также могут быть в виде пыли от сжатых молекул воздуха.
Масло улавливает эти наночастицы и все другие частицы, которые производятся металлическими частями компрессора.Затем частицы можно удалять каждый раз, когда вы меняете масло. В свою очередь, это позволяет компрессору работать эффективно.
2. Масло способствует процессу сжатия
Маслопомогает в процессе сжатия, герметизируя зазоры между винтовыми элементами. Винты, которыми соединяются металлические детали, иногда могут затруднять сжатие воздуха, поскольку оставляют зазоры в машине.
Маслохорошо проникает в самые маленькие точки, что обеспечивает полную герметичность системы. Следовательно, уплотнение маслом предотвращает утечку воздуха и сохраняет его сжатым.
3. Масло охлаждает систему
Поскольку сжатие воздуха представляет собой непрерывный процесс, при котором выделяется много тепла, температура в камере сжатия имеет тенденцию к повышению. Масло действует как первичный хладагент, охлаждая компрессор. Если тепло не будет быстро отведено из камеры, подшипники, уплотнения и шестерни выйдут из строя.
4. Масло предотвращает износ и коррозию
Как мы упоминали в начале статьи, смазка является одной из функций масла для воздушных компрессоров. Поскольку ряд движущихся частей, таких как подшипники, помогают сжимать воздух, важно, чтобы они были смазаны.
5. Экономия масла на стоимости
Мониторинг масла воздушного компрессора снизит затраты на:
- Минимизация затрат на плановое обслуживание
- Увеличение срока службы компрессора
- Снижение расхода топлива
Зная, насколько важно масло для бесперебойной работы и долговечности компрессора, имеет смысл следить за ним. Вы должны проверить свою смазку на загрязнение, которое может повлиять на кислотность и вязкость жидкости.
Как проверить масло в воздушном компрессоре
Если вы еще не контролировали масло в компрессоре, вы можете начать это делать, воспользовавшись следующими советами:
#1 Проверка уровня масла
Проверяйте уровень масла 3–4 раза в неделю, чтобы убедиться, что масло в компрессоре не заканчивается.Компрессоры имеют либо щуп, либо смотровое стекло, которые можно использовать для проверки уровня масла.
Все маслоизмерительные щупы откалиброваны, и вы должны следить за тем, чтобы уровень масла всегда был около максимальной отметки. Некоторые смотровые стекла не откалиброваны. Однако это не должно вас беспокоить. Хитрость заключается в том, чтобы убедиться, что уровень масла на смотровом стекле составляет 2/3.
#2 Проверка на утечки масла
Необнаруженная утечка масла оставит ваш масляный поддон пустым, что может привести к повреждению двигателя.Регулярно проверяйте наличие утечек, наблюдая за скоплением масла в основании компрессора и двигателя.
Обратите внимание: если вам постоянно приходится доливать масло в масляный поддон, из компрессора может вытекать чрезмерное количество масла.
#3 Проверка качества масла
По мере использования масла в камере компрессора оно стареет и изнашивается. Старое и изношенное масло может повлиять на эффективность вашего воздушного компрессора. Если ваше масло густое и непрозрачное, имеет зернистые частицы и плохо пахнет, значит, его качество ухудшилось.Поэтому вы должны изменить его.
Для проверки качества масла используйте щуп или смотровое стекло. Если эти методы не дают четкого ответа, используйте другие методы, такие как промокательный тест.
Если вы подозреваете, что ваше масло разлагается быстрее, чем должно, из-за загрязнения, профессионал проведет тест IR или TAN, чтобы подтвердить это.
№4 Замена компрессорного масла
Если ваше масло устарело, замените его. Помните, что масла различаются в зависимости от их вязкости.Ознакомьтесь с рекомендациями производителя перед покупкой нового масла. Обычно рекомендуется менять масло через каждые 1000-2000 часов работы.
Часто задаваемые вопросы
Можно ли использовать моторное масло в воздушном компрессоре?
Вопрос о том, следует ли использовать моторное масло в воздушном компрессоре, задает большинство людей. Тем не менее, использование моторного масла не является разумной идеей по этой причине.
Моторное масло содержит моющие и другие присадки, которые при нагреве при сжатии образуют пену.Эта пена тормозит процесс смазки.
Кроме того, моторное масло может вызвать отложения в насосе компрессора. Отложения создают нагрузку на помпу, снижая ее эффективность и вызывая более быстрый износ.
Какое масло следует использовать в моем воздушном компрессоре?
Чтобы обеспечить бесперебойную работу вашего воздушного компрессора:
- Используйте масло, рекомендованное производителем, так как система предназначена для использования этого масла.
- Если вы не знаете, какое масло рекомендуется для вашего компрессора, и не можете найти руководство пользователя, используйте 30W ISO 100 ИЛИ 20W ISO 68.Это наиболее часто используемые масла.
- Избегайте масла, которое является органическим или содержит моющие средства.
Сколько масла требуется моему воздушному компрессору?
Поскольку масло очень важно для воздушного компрессора, может возникнуть соблазн заполнить его доверху для «дополнительной» защиты. Однако чрезмерное количество масла опасно, так как оно может привести к внутреннему повреждению компрессора, когда оно переливается через край. Кроме того, масло может также повредить другие детали и аксессуары, к которым прикреплен воздушный компрессор.
Заключение
Одним из лучших способов предотвратить повреждение воздушного компрессора является замена смазочных материалов в соответствии с рекомендациями производителя. Превышение интервалов технического обслуживания, особенно в жаркую и влажную погоду, приведет к выходу из строя компрессора. Убедитесь, что вы регулярно следите за маслом вашего воздушного компрессора, используя советы, описанные в этой статье.
Я надеюсь, что эта статья помогла вам лучше понять мониторинг масла в вашем воздушном компрессоре.Если это так, пожалуйста, поддержите нас, прочитав некоторые статьи по теме.
Спасибо за прочтение и хорошего дня!
-Крейг
Давление масла и давление нагнетания масляного насоса
Один вопрос, который вы часто слышите в отношении коммерческих компрессоров, заключается в том, какое давление масла им необходимо для работы. Требуемое давление масла будет зависеть от размера, типа и предполагаемого использования системы. Возраст вашего компрессора также может влиять на давление масла, потому что старые компрессоры имеют больше изношенных деталей, что создает зазоры, которые позволяют течь дополнительному маслу, тем самым снижая давление в системе.При сравнении различных типов компрессоров и требований к давлению масла важно понимать разницу между полезным или чистым давлением масла и давлением масла нагнетания. Эти два измерения относятся к разным частям вашей системы, и вы должны понимать, что есть что, чтобы убедиться, что ваш компрессор правильно смазан и работает нормально.
Прежде чем мы перейдем к полезному давлению масла, мы сначала должны начать с измерения давления масла, которое легче всего найти.Давление масла на нагнетании — это давление масла, которое измеряется на нагнетании компрессора. Это важно, потому что это единственное место, где вы сможете фактически измерить давление масла с помощью манометров, но это не является истинным измерением давления масла в вашей системе. Скорее, давление масла нагнетания представляет собой комбинацию входного давления масла и давления масла в картере, поэтому оно будет выше, чем фактическое давление масла, с которым вы работаете.
После того, как вы измерили давление масла нагнетания, вы можете работать в обратном направлении , чтобы определить чистое давление масла.Это делается путем вычитания давления масла в картере из давления нагнетания. Вы должны быть в состоянии довольно легко найти давление в картере вашей системы, потому что оно остается стабильным. Таким образом, единственное изменение в вашем расчете произойдет, если чистое давление масла увеличилось или уменьшилось.
Например, если вы прикрепите манометр к стороне высокого давления на нагнетательном отверстии и измерите 70 фунтов на квадратный дюйм, вам нужно будет проверить давление в картере. Если стандартное давление в картере составляет 15 фунтов на квадратный дюйм, вы будете знать, что 70-15 = 55. Это чистое давление масла.
Чистое давление масла в этой системе — это фактическое давление, создаваемое масляным насосом. Большинство компрессоров имеют безопасный рабочий диапазон, требующий давления от масляного насоса не менее 20 фунтов на квадратный дюйм. Если вы измерите давление масла в выпускном отверстии, вычтете давление картера и обнаружите, что чистое давление масла слишком низкое, это может означать, что ваш компрессор работает без достаточной смазки.Это также может означать, что внутренние компоненты вашего компрессора изношены до такой степени, что они не могут поддерживать стандартное давление масла при нормальной работе. И то, и другое вызывает беспокойство. С другой стороны, если вы обнаружите, что давление масла у вас чрезвычайно высокое, это может быть признаком того, что где-то в системе есть засор, который заставляет все масло течь через ограниченное пространство. Это может быть в равной степени разрушительным и должно быть устранено своевременно.
Знание разницы между давлением масла нагнетания и чистым давлением масла поможет вам получить точные показания вашей системы во время технического обслуживания.Вы не хотите ошибиться в этих двух разных измерениях, потому что они могут привести к неверным выводам о состоянии вашего компрессора. Правильное измерение и поддержание давления масла в вашем коммерческом компрессоре является жизненно важной частью исправности вашего коммерческого компрессора. Узнайте больше советов по обслуживанию коммерческих компрессоров сегодня, просмотрев другие полезные сообщения в блоге от Compressors Unlimited.
Уровень масла в компрессоре чиллера – Чиллеры Maximus
Системные испытания компрессоров чиллеров
Компрессоры чиллеров часто выходят из строя из-за неэффективного обслуживания и тестирования системы.В Maximus Chillers мы проводим обширные тесты во время наших визитов, чтобы гарантировать, что небольшие проблемы будут решены до того, как они станут большими проблемами. Если мы замечаем, что показания начинают становиться ненормальными, мы можем провести диагностику, а затем устранить проблему. Вот некоторые из показаний компрессора, которые мы отслеживаем:
Температура компрессоров чиллеров
Температура всасывания, нагнетания, обмоток двигателя и подшипников регистрируется для сравнения с предыдущими посещениями. Они часто доступны в ПЛК чиллера, или наш инженер может снять показания с помощью своего испытательного оборудования.Проблемы с масляным радиатором могут быть причиной более высоких температур компрессора, другой причиной является работа системы за пределами ее номинальных рабочих условий. Преимущество систем магнитного привода состоит в том, что они не используют масло.
Акселерометр
Портативные датчики вибрации есть в каждом транспортном средстве нашей компании. Это акселерометр для измерения вибрации. Наряду с прочими показаниями системы мы постоянно записываем уровни вибрации вокруг компрессора. Когда внутренние компоненты выходят из строя из-за износа, это вызывает дисбаланс в компрессоре. Это, в свою очередь, приводит к нарушению эффекта, в результате чего другие компоненты выходят из равновесия. Своевременное обнаружение этого состояния предотвратит выход компрессора из строя, что приведет к замене дорогостоящих внутренних компонентов.
Анализ масла для компрессоров чиллеров
Еще одним способом предотвращения серьезных проблем является периодическая проверка компрессорного масла. Образцы берутся, как правило, во время чередующихся посещений, и затем отправляются в лабораторию для анализа. Уровень кислоты проверяется для предварительного предупреждения о возможном перегорании обмоток двигателя компрессора.Это связано с тем, что кислота в компрессорном масле гниет через электрическую изоляцию обмоток двигателя. Анализируется также наличие и количество белого металла и желтого металла. Это окно для компонента, который начинает изнашиваться внутри компрессора.
0161 370 7193
✎ Контактная форма
Винт
На фото компрессор винтовой. Работает на аммиачном хладагенте.Этот хладагент обычно используется для низкотемпературных применений, в основном связанных с производством продуктов питания. Этот компрессор, однако, имеет насыщение хладагентом 1°C и используется для охлаждения компьютерных залов. Распространенные причины отказа компрессора этого типа:
Негерметичные отливки на компрессорах чиллеров
Различные компоненты компрессора уплотнены с помощью уплотнительных колец или бумажных прокладок. Уплотнительные кольца особенно склонны к утечкам из-за упрочнения и уплощения поверхности уплотнения.Систему можно откачать, а компрессор перекрыть. Затем наша бригада по подъему и смене может перевезти компрессор на наш завод по восстановлению для разборки.
Негерметичное уплотнение вала
Сопрягаемая поверхность уплотнения вала имеет зеркально гладкую поверхность. Это должно уменьшить трение и улучшить уплотнение. Со временем он начинает изнашиваться, что приводит к неэффективному уплотнению с утечкой хладагента и масла. Для замены уплотнения вала на месте может быть организован визит в сервисный центр. Муфты вала можно разъединить, затем можно снять и заменить уплотнение вала.Быстрая работа, затем машина снова работает.
Потенциометр золотникового клапана
Это электронное устройство с золотником, прикрепленным к подвижному золотниковому клапану компрессора. Устройство имеет начальную и конечную позиции, запрограммированные во время ввода в эксплуатацию. Потенциометр преобразует положение золотникового клапана, обычно в сигнал 4-20 мА, который возвращается на ПЛК чиллера. Они склонны к считыванию или застреванию чтения в одном положении. Это приводит к отключению органов управления, поскольку контроллер не может определить истинное положение золотникового клапана компрессора.У нас есть готовые запасы потенциометров золотниковых клапанов для различных моделей компрессоров. Посещение сервисного центра может быть организовано для замены детали после проведения диагностики. Элементы управления управляют загрузочным и разгрузочным электромагнитными клапанами для изменения положения золотникового клапана.
0161 370 7193
✎ Контактная форма
Центробежный
Центробежные компрессоры очень надежны, но когда они выходят из строя, они могут выйти из строя в значительной степени.Капитальный ремонт компрессора стоит дорого, его можно выполнить на месте, или лучший вариант — поднять и перенести на наш завод по восстановлению. Датчики приближения обычно устанавливаются для контроля расстояния между рабочим колесом и отливкой. Это дополнительная защита наряду с другими датчиками и преобразователями вокруг компрессора.
МКС
Мы сотрудничаем с Micro Control Systems — американской компанией, которая специализируется на изготовлении панелей на заказ для конкретных компрессоров чиллеров.Мы легко устанавливаем эту систему управления на любой компрессор, чтобы контролировать нагрузку на лопасти в соответствии с доступной нагрузкой от процесса. Панель управления ранее устанавливалась на другие машины той же модели, поэтому любые проблемы с прорезыванием зубов уже устранены. Чиллеры Maximus могут обеспечить бесперебойную работу вашего предприятия.
Масляная система для компрессоров чиллеров
Новые центробежные компрессоры не содержат масла, что устраняет любые проблемы обслуживания, связанные с маслом.Однако существует значительное количество компрессоров, в которых для смазки подшипников используется масло. Такой компрессор при правильном обслуживании может прослужить 50 лет. Масляная система улавливает загрязнения, которые улавливаются различными фильтрами. Эти фильтры можно заменять или чистить в соответствии с предписанным графиком обслуживания. Наши инженеры следят за тем, чтобы запасные части заказывались и хранились на месте до визита.
Экономичный
Наши визиты и текущее обслуживание вашего предприятия экономят деньги.Деньги, потраченные на профилактику, в долгосрочной перспективе сэкономят гораздо больше денег. Конкурентоспособные цены на специализированные внутренние центробежные компрессоры — чиллеры Maximus дополняют картину. В случае отказа компрессора вы в надежных руках благодаря многолетнему опыту работы в отрасли, вложенному в каждого из наших инженеров.
0161 370 7193
✎ Контактная форма
Свиток
Вот некоторые проблемы со спиральным компрессором:
Высокое давление нагнетания
При высоком давлении нагнетания происходит соответствующее повышение температуры нагнетания.Это означает, что компрессор работает за пределами рекомендуемых значений. Причиной этого часто является плохо обслуживаемый конденсатор. В частности, на промышленных чиллерах в графике могут быть пробелы, когда конденсатор не обслуживался должным образом. Это условие часто легко устраняется инженером на месте путем его очистки кистью. Там, где плавники согнуты, у нас есть специальный инструмент, чтобы выпрямить их так, как они вышли с завода. Мы также используем различные формулы химикатов, чтобы вымыть различные виды грязи из глубины ребер.
Высокое давление всасывания на компрессорах чиллеров
Некоторые чиллеры используются там, где из процесса может вернуться очень высокая температура воды, если чиллер отключится от сети на короткий период времени. Обычно это происходит на заводах, где осуществляются определенные производственные процессы. Когда инженеры на месте снова запускают установку, чиллер испытывает высокую тепловую нагрузку.
Расширительные клапаны MOP
Расширительные клапаны максимального рабочего давления ограничивают давление в испарителе до заданного уровня, независимо от доступной тепловой нагрузки от процесса.Они делают это, имея ограниченное количество жидкого хладагента в колбе. Когда он заканчивается, силовой элемент не может больше открыть отверстие, тем самым ограничивая давление всасывания. Это важно для предотвращения выхода из строя спирального компрессора, поскольку предотвращает дополнительную нагрузку на обмотки двигателя компрессора из-за высокого давления всасывания.
Нехватка масла и хладагента
При нехватке хладагента возникает состояние низкого уровня масла. Массовый расход хладагента переносит масло по системе и обратно в компрессор.Это сильно ухудшается, когда в чиллере не хватает газа. Масло охлаждает компрессор и смазывает подшипники вала. Эти подшипники и другие внутренние компоненты изнашиваются и заедают, что приводит к выходу из строя. Maximus Chillers может собрать пакет, чтобы свести к минимуму отказ компрессора чиллера.
Людям также нравится эта страница:
Восстановление центробежного компрессора
Связанные статьи:
Техническое обслуживание компрессора винтового чиллера
Поставщик запчастей для чиллеров
Техническое обслуживание конденсатора чиллера с воздушным охлаждением
Техническое обслуживание кожухотрубного испарителя
Техническое обслуживание компрессора спирального чиллера
Управление чиллером
Техническое обслуживание компрессора центробежного чиллера
Конденсаторы чиллеров
Техническое обслуживание поршневого компрессора чиллера
Компания Chiller Controls
Как работают чиллеры
Чтобы узнать больше о спиральных чиллерах, нажмите на тег вверху страницы.
Подробнее о рабочих колесах , которые используются в центробежных компрессорах, читайте в Википедии
Ремонт компрессора холодильника Сан-Антонио
Вам нужен ремонт компрессора холодильника Сан-Антонио сервис? Тогда немедленно свяжитесь с Southwest Appliance Repair SA. Компрессор холодильника представляет собой насос и двигатель, который перемещает охлаждающий хладагент через систему холодильника. Любое повышение температуры обнаруживается, и компрессор дает сигнал начать процесс охлаждения.Холодный газообразный хладагент всасывается компрессором, и на этот газ оказывается давление для его сжатия. Сжатие этого газа увеличивает температуру. Это заставляет компрессор выталкивать его, и из-за высокого давления газ при охлаждении становится жидкостью.
Эта жидкость в конечном итоге проталкивается через маленькое отверстие, где она превращается в холодный туман, направляясь к расширительному клапану холодильника. Туман испаряется при движении по змеевикам, забирая тепло из окружающего воздуха. Жидкость снова сжимается, поскольку змеевики снова ведут к компрессору. Этот цикл продолжает следить за тем, чтобы температура в холодильнике оставалась в пределах установленного диапазона.
Позвольте специалистам отремонтировать неисправный компрессор вашего холодильника
Со временем компрессор вашего холодильника выйдет из строя. Когда это произойдет, вашему холодильнику будет трудно поддерживать заданную температуру. К счастью, наши специалисты могут проверить компрессор вашего холодильника. Наша команда внимательно осмотрит компрессор вашего холодильника, чтобы узнать, есть ли детали, которые следует заменить, чтобы восстановить его производительность.
У нас есть навыки, опыт и инструменты, чтобы отремонтировать компрессор вашего холодильника и установить его на месте. Наши технические специалисты проверят компрессор и все компоненты, влияющие на работу вашей холодильной системы. К ним относятся масляный насос, маслоотделитель, трубопроводы и фильтры. Это очень важно, потому что гарантирует, что компрессор не будет заблокирован мусором. Мы также проводим анализ вибрации.
Запишитесь на ремонт компрессора холодильника прямо сейчас!
Компрессор вашего холодильника — это деталь, которая поддерживает охлаждение всей системы.Если специалисты не отремонтируют его должным образом, у вас могут возникнуть проблемы с другими частями вашего холодильника. Наши мастера обладают необходимыми знаниями и инструментами для проведения такого ремонта.
Позвоните нам сейчас, чтобы запланировать ремонт компрессора холодильника Сан-Антонио назначение!
Время замены масла?
Смазочные масла, разработанные специально для аммиачных холодильных компрессоров, могут повысить надежность и снизить эксплуатационные расходы, как объясняетНик Макдональд, директор по развитию рынка Kluber Lubrication GB. надежность и эффективность всей холодильной установки.С одной стороны, к смазочному маслу предъявляются более высокие требования: объемы заливаемого масла были уменьшены, а температура, давление и скорость возросли.

Кроме того, операторы установок пытаются увеличить интервалы технического обслуживания, чтобы снизить затраты. С другой стороны, используемые масла (преимущественно нафтеновые минеральные масла) не всегда соответствуют этим требованиям. Тем не менее, сегодня доступны специально разработанные смазочные масла, которые отвечают вышеуказанным требованиям и помогают предотвратить возможные проблемы.
Образование мазута и остатков
Интенсивный контакт между аммиаком и смазочным маслом в холодильных компрессорах представляет собой большую проблему. Ненасыщенные углеводороды и соединения серы, содержащиеся в минеральных маслах, могут реагировать с агрессивным хладагентом аммиаком. В результате этой химической реакции масло постепенно темнеет, пока, в конце концов, не становится черным.
Продукты реакции, нерастворимые в масле, остаются в компрессоре или контуре охлаждения (главным образом в испарителе и конденсаторе) в виде остатков или шлама.Эти остатки могут снизить эффективность холодильной установки (из-за снижения теплопередачи в теплообменниках) и заметно повлиять на эксплуатационную надежность. Опыт показывает, что почернение и закисление масла могут быть ускорены, в частности, присутствием воздуха и воды в холодильном цикле (возможно до 3% воды). Кроме того, абразивный износ, вызванный масляным шламом, может напрямую воздействовать на различные компоненты компрессора. Кроме того, масляный фильтр и сепаратор испытывают повышенную нагрузку и более подвержены засорению.Все это приводит к сокращению срока службы компонентов, падению КПД и увеличению эксплуатационных расходов.
Решение можно найти в использовании гидрогенизированных минеральных масел или синтетических смазочных масел.
Компания Klüber выбрала путь минерального масла, выпустив Klüber Summit RHT-68, парафиновое гидрогенизированное минеральное масло, разработанное для использования в аммиачных холодильных установках с температурой испарителя до -36ºC. Гидрогенизация базового масла (также называемая гидроочисткой) удаляет из масла ненасыщенные соединения и соединения серы.Таким образом, масло очищается и становится менее реактивным с аммиаком. Переход с нафтенового минерального масла на этот тип масла не представляет никакой проблемы.
То же самое касается Klüber Summit RPA-68, полностью синтетического смазочного масла на основе полиальфаолефина (ПАО) и алкилбензола. Это масло было разработано специально для низких температур испарителя до -55ºC, когда из-за высокой температуры застывания минеральные масла теряют текучесть. Наконец, Klüber Summit R-200 подходит не только для использования с аммиаком, но также может применяться в сочетании с CO2, пропаном или бутаном.Это полностью синтетическое полиальфаолефиновое смазочное масло, зарегистрированное NSF для использования в пищевой промышленности, подходит для температур испарителя до -55ºC.
Оба синтетических продукта содержат очень химически стабильные базовые масла. Их высокая устойчивость к реакции с аммиаком предотвращает почернение масел, явление, которое очень часто встречается с обычными минеральными маслами, и образование нежелательного остатка в испарителе.
Высокий расход масла компрессора
Количество масла, перенесенного из камеры сжатия в холодильный цикл, так называемый унос масла, зависит, среди прочего, от склонности к испарению (давления паров) масла при соответствующей температуре нагнетания (иногда явно выше 100°С).
Большой унос масла, вызванный сравнительно высокой скоростью испарения нафтенового минерального масла, может привести к чрезмерному расходу масла и увеличению требований к техническому обслуживанию из-за частой доливки масла. Оба явления приводят к увеличению эксплуатационных расходов.
И здесь гидрогенизированные или полностью синтетические масла представляют собой удовлетворительное решение: химически стабильные базовые масла высокой степени очистки явно снижают унос масла по сравнению с обычными минеральными маслами, способствуя тем самым снижению потребления масла компрессором.
Практический пример иллюстрирует возможную экономию: холодильный компрессор, заправленный 200 литрами минерального масла, работает около 7000 часов в год. Оператору приходилось доливать около 300 литров масла в год, что примерно в 1,5 раза превышает объем заливки. При переходе на гидрогенизированное минеральное масло объем дозаправки сократился до 70 %.
Сокращенные интервалы замены масла
Поскольку низкомолекулярные компоненты минерального масла испаряются быстрее всего в камере сжатия, вязкость масла постепенно увеличивается с течением времени.Помимо увеличения вязкости, другими причинами чрезмерного старения масла могут быть почернение масла и образование шлама и осадка. Все это неизбежно приводит к частым заменам масла, что нарушает нормальную работу и может стоить очень дорого. Высокоочищенные и специально разработанные минеральные и синтетические масла не содержат этих летучих масляных компонентов.
Таким образом, вязкость масла остается стабильной в течение длительного периода времени, что позволяет увеличить интервалы замены масла в четыре или пять раз.Оператор холодильного компрессора, который смазывался нафтеновым маслом (ISO VG 68), замерил увеличение вязкости масла с 68 до 105 мм2/с всего через 2000 часов работы. Переход на синтетическое масло позволил ему увеличить срок службы масла в шесть раз по сравнению с минеральным маслом.
Совместимость с уплотнениями
Несмотря на неоспоримые преимущества, предлагаемые синтетическими маслами, все еще остается много неопределенности в отношении перехода на эти масла, например, в отношении совместимости с уплотнениями.Нафтеновые масла часто вызывают набухание уплотнений, в то время как некоторые синтетические масла (в частности, ПАО) имеют противоположный эффект и могут привести к усадке уплотнения. В частности, в аммиачных холодильных компрессорах, где часто используются неопреновые уплотнения, утечка может произойти после перехода с нафтенового смазочного масла на полиальфаолефиновое.
В этом случае Klüber Lubrication предлагает специальное масло, которое значительно упрощает замену: полиальфаолефин, смешанный с алкилбензолом, в котором эффект усадки одного компонента нейтрализуется эффектом набухания другого, что обеспечивает нейтральное поведение по отношению к уплотнительным материалам.
При переходе с нафтенового масла на чистое полиальфаолефиновое масло с эффектом усадки уплотнения необходимо проявлять большую осторожность. Чистые полиальфаолефины, такие как Klüber Summit R 200, могут вызвать усадку уплотнения, набухшего при контакте с нафтеновым маслом, что может привести к утечке через уплотнительные кольца в корпусе или через торцевые и валовые уплотнительные кольца. При переходе на Klüber Summit R 200 (одной из причин выбора этого продукта может быть одобрение NSF для пищевой промышленности) операторам рекомендуется заменить любые уплотнительные кольца, торцевые уплотнения или уплотнительные кольца вала.
Замена масла
Klüber Lubrication предлагает индивидуальные смазочные материалы для холодильных компрессоров, а также, по запросу, помощь при замене масла. Первый этап состоит из подробного анализа масла, используемого в настоящее время, который дает представление о текущем состоянии холодильной установки и может выявить «скрытые» проблемы. После определения наилучшего решения для конкретного клиента сервисная группа может помочь с заменой масла на заводе.
Процедура во многом зависит от степени загрязнения масла и/или компрессора. Обычно достаточно просто слить масло, заменить фильтры и маслоотделители и удалить остатки масла из труб, корпусов и фильтров перед заливкой нового масла. Для сильно загрязненных винтовых компрессоров Klüber предлагает чистящий концентрат на масляной основе, который добавляется в компрессорное масло в концентрации 10 % за 60 часов до плановой замены масла.
Компрессор продолжает работать в течение этих 60 часов, а остатки и отложения растворяются чистящим средством.Компрессор не нужно разбирать для очистки.
Кроме того, после перехода на новое масло Klüber Lubrication может оказать дополнительную поддержку. Вместе с заказчиком специалисты Klüber lubrication могут через регулярные промежутки времени проверять образцы отработанного масла. В случае возникновения каких-либо проблем ситуация анализируется и могут быть немедленно приняты контрмеры. Всегда целью является снижение затрат на техническое обслуживание и достижение наилучшей доступности и надежности холодильной установки.
Переход от нафтеновых минеральных масел к гидрогенизированным минеральным маслам нового поколения и полностью синтетическим смазочным маслам дает много преимуществ. Во многих случаях эти смазочные материалы обеспечивают бесперебойную и надежную работу холодильных компрессоров без частых перерывов в работе из-за неизбежной очистки или технического обслуживания. Изношенные детали заменяются реже, а затраты на фильтры снижаются. Интервалы замены масла, с другой стороны, заметно увеличены до шести раз, а расход масла снизился на целых 70%.
И последнее, но не менее важное: благодаря отсутствию нефтесодержащих остатков должна повыситься эффективность холодильной установки в целом. Однако успешный переход требует большого опыта и ноу-хау. Поэтому компетентный поставщик масла должен консультировать клиента, предлагать индивидуальное решение и поддерживать его в течение всего периода перехода.