Как алюминий припаять к меди: можно ли их паять и как это сделать в домашних условиях паяльником?
как спаять медь и алюминий, можно ли спаять алюминий с медью
Далеко не всегда в домашних условиях получается припаять провод или что-то другое к алюминию. Обычно для этого требуется или специальный флюс, который стоит немалых денег, или газовая горелка.
Однако всегда есть альтернативный вариант. Автор делится секретом, как припаять медный провод к алюминию обычным паяльником, без использования флюсов и газовых горелок.
Причем припаять так, чтобы провод держался намертво. И для этого потребуется лишь припой с канифолью ПОС 61 (можно использовать ПОС 40).
Рекомендуем также прочитать интересную статью на тему: пайка алюминия своими руками в домашних условиях. В этом обзоре вы найдете много полезной информации.
Основные этапы работ
1
Читайте также: Чем паять медь и латунь, чтобы получить надежное соединениеПервым делом необходимо капнуть на поверхность алюминия каплю машинного масла (в принципе, можно использовать абсолютно любое жидкое масло, включая растительное).
Для удобства, чтобы не плеснуть лишнего, масло можно предварительно набрать в медицинский шприц. В каплю масла опускаем жало паяльника и припой.
Расплавляем необходимое количество припоя, после чего несколько секунд прогреваем алюминий, затем движениями вперед-назад пытаемся залудить нужный участок.
1
Читайте также: Как припаять медный кабель к алюминию, не используя специальный флюс или припойЦарапая поверхность алюминия жалом паяльника, мы снимаем оксидную пленку, а масло выступает в качестве защитной среды от кислорода.
После этого необходимо будет залудить конец медного провода. Далее луженый конец провода припаиваем к алюминию. И никаких заморских флюсов не надо!
Подробно о том, как припаять медный провод к алюминию обычным паяльником, рекомендуем посмотреть в авторском видеоролике. Свое мнение об этом способе пишите в комментариях.
1
Читайте также: Идея для мастерской: как сделать болт с накаткойyoutube.com/embed/kD_p2kN13ac” allowfullscreen=”allowfullscreen”/>
Мне нравитсяНе нравитсяАндрей Васильев
Задать вопрос
Как легко и быстро припаять провод к алюминию. Держит так, что не оторвать | Мастерская Самоделок
Ни для кого не секрет, что пайка алюминия является проблемой, которую сложно решить без специального оборудования. Обычно используют припой для алюминия, который продается не в каждом магазине, но его можно заказать в Китае.
Сначала разберемся почему алюминий не так просто паять, в отличии, например, от меди.
При пайке процессу мешает оксидная пленка, которая очень быстро образуется на поверхности алюминия, именно поэтому лужения не происходит.
Чтобы залудить участок алюминия, нужно постоянно удалять оксидную пленку, некоторые делают это при помощи корщетки, затем разогревают деталь и водят по нему припоем. Не спеша все-таки получается залудить алюминий, но это не так быстро и легко, как хотелось бы.
Сейчас я покажу, как паять алюминий в домашних условиях бюджетно и легко с самым обычным припоем.
Наносим растительное масло в небольшом количестве на паяемое место и зачищаем корщеткой. (Листаем галерею).
Капельки масла будет достаточно, она перекроет доступ кислорода к алюминию, что не даст образоваться оксидной пленке.Корщетку можно заменить наждачной бумагой, она справляется также хорошо.Капельки масла будет достаточно, она перекроет доступ кислорода к алюминию, что не даст образоваться оксидной пленке.
Далее паяльником расплавляем припой и как бы втираем его в алюминий.
Спустя несколько секунд получается качественно залуженный участок. (Листаем галерею).
Таким способом можно припаять провод или соединить детали из алюминия друг с другом.Провод отлично припаялся.Таким способом можно припаять провод или соединить детали из алюминия друг с другом.
Также можно заделать дыру в таре, для примера я сделал надпил ножовкой по металлу, чтобы показать это наглядно.
Зачищаю наждачной бумагой место пайки.
Затем аналогично залуживаю необходимое место с использованием масла.
Я попробовал оторвать припаянный провод к алюминию, но у меня не получилось, поэтому могу уверенно сказать, что пайка надёжная.Я попробовал оторвать припаянный провод к алюминию, но у меня не получилось, поэтому могу уверенно сказать, что пайка надёжная.
Кому понравился способ, ставьте лайки, пишите комментарии и подписывайтесь на канал.
Меднение и лужение алюминия – Другие методы обработки
кстати. если уж и есть горячее желание подпаятся к алюминию во многих точках и нужен именно ПОС в качестве припоя то ни в коем случае медь в качестве подслоя применять нельзя.
адгезии нет. радикально лучше нанести химникель из любого раствора химникелирования с но добавить 2-3 грамма на литр любого фторида ( натрия, калия, аммония) рН раствора 5.5-3.5
смысл- фториды разрушают окисную пленку на алюминии и никель осаждается непосредственно на металл а не на окисел. потом можно паять обычным ПОС61, соединение очень прочное и гарантированное. Целесообразно отжечь пленку при 200 градусов 1-2 часа.процесс давно применяется в аппаратуре военного назначения
Попробовал этот метод.
Использовал следующий раствор: сернокислый никель 25г/л, натрий уксуснокислый 10г/л, натрий фосфорноватистокислый 20 г/л, натрий фтористый 5 г/л.
Процесс осаждения на алюминий идет, причем достаточно интенсивно. Однако пленка получается рыхлая и шершавая и адгезия стремится к нулю (можно сдуть при обдуве детали сжатым воздухом).
Наиболее неприятно что покрытие неравномерное – где-то вообще не хочет ложиться. Грешу на неправильную подготовку поверхности.
Подготовку поверхности делаю травлением в едком натре, затем осветление в азотной кислоте.
Притом на сталь и медь, подвешенные рядом пленка садится идеальная. Гладкая и крепкая.
Сам раствор тоже ведет себя нестабильно. Чуть перегреешь и процесс запускается на дне эмалированной кастрюли. Хоть и грею на водяной бане.
Заметил что алюминий начинает пузыриться раньше, чем сталь и медь. Может для него пониже температура раствора нужна?
Дайте пожалуйста рекомендации – как получить качественную пленку?
Пайка аллюминия – Сварпост. Переносные газосварочные посты ПГСП
Господствует мнение, что алюминий и его сплавы относятся к трудно паяемым материалам. Однако это общераспространенное убеждение можно считать верным лишь в том случае, если речь идет о пайке с использованием обычных припоев и флюсов, применяющихся для пайки меди, стали и некоторых других металлов. При использовании современных материалов, предназначенных специально для пайки алюминия, пресловутая труднопаяемость алюминия почти ничем себя не проявляет.
Трудность пайки алюминия обычными припоями и флюсами обуславливается целым рядом факторов. Прежде всего, это наличие тугоплавкой и химически стойкой оксидной пленки. Оксид Al2O3препятствует смачиванию поверхности припоем и растворению в нем основного металла. Чтобы разрушить его, применяют механическую обработку и сильнодействующие флюсы.
Создает трудности для пайки и низкая температура плавления алюминия, составляющая 660°C. При нагреве прочность металла быстро снижается, и уже при температурах 250-300°С алюминиевые конструкции могут терять устойчивость. Температура солидуса (температура, при которой плавится самый легкоплавкий компонент) основных алюминиевых сплавов, варьируется в интервале 500-640°С. Это оставляет очень узкий температурный интервал для применения высокотемпературной пайки, при которой существует опасность перегрева и расплавления самой паяемой детали.
В отношении большинства элементов, составляющих основу легкоплавких припоев (Sn, Pb, Cd, Bi, In), у алюминия имеет место слабая взаимная растворимость, что снижает прочность паяных соединений.
Материалы для пайки алюминия
Припои
При использовании высокоактивных флюсов и хорошей подготовки поверхности, алюминий можно паять и оловянно-свинцовыми припоями. Однако их выбор все же нельзя считать удачным. Помимо того, что имеет место упомянутая выше плохая растворимость алюминия в системах Sn-Pb, оловянно-свинцовые припои обеспечивают очень низкую коррозионную стойкость паяного соединения. Чтобы преодолеть этот недостаток, соединения, паянные оловянными или оловянно-свинцовыми припоями, необходимо покрывать специальными лакокрасочными покрытиями.
Качественную пайку алюминия обеспечивают припои содержащие цинк, серебро, медь, алюминий, кремний. Существует большое количество составов как отечественного, так и импортного производства, содержащих эти элементы в различном соотношении. Из отечественных припоев можно привести ЦОП40 (60% олова и 40% цинка) и 34А (66% Аl, 28% Cu и 6% Si).
Большинство припоев является низкотемпературными, однако температура их плавления выше, чем у оловянно-свинцовых. По-настоящему высокотемпературными являются алюминиево-кремниевые (силумины) и алюминиево-медно-кремниевые припои. В качестве первого можно привести припой Aluminium-13 фирмы Chemet, содержащий 13% Si и 87% Аl (припой покрыт флюсом). Его температура пайки составляет 590-600°C. Примером второго может служить, уже упоминавшийся, отечественный припой 34А, состоящий из 66% Аl, 28% Cu и 6% Si. Интервал его температуры пайки – 530-550°C. Если возникает необходимость в применении высокотемпературных припоев, они применяются для пайки алюминия и тех его сплавов, которые имеют достаточно высокую температуру плавления, или деталей имеющих массивные размеры, обеспечивающие хороший теплоотвод.
Если говорить о самых удобных материалах, то к ним относятся, конечно, бесфлюсовые низкотемпературные припои, например HTS-2000.
Припой HTS-2000
Флюсы
К выбору флюса нужно подходить очень серьезно, именно его активность определяет паяемость алюминия, особенно при использовании обычных оловянно-свинцовых припоев. Далеко не все флюсы проявляют в отношении алюминия активность, заявляемую их производителями. Одним из отечественных флюсов является состав, называемый предельно информативно – “флюс для пайки алюминия”. Ещё есть флюс Ф59А, Ф61А (содержащий триэтаноламин, фторборат цинка, фторборат аммония) и другие. Под названием “флюс для пайки алюминия” могут скрываться Ф59А, Ф61А или другие, даже если это не указано на упаковке.
Флюсы для пайки алюминия
В качестве высокотемпературного флюса можно привести флюс 34А, который содержит 50% KCl, 32% LiCl, 10% NaF и 8% ZnCl2.
Высокотемпературный флюс 34А
Подготовка деталей к пайке
Подготовка алюминия к пайке заключается в обезжиривании и механической зачистке зоны соединения. Целью последней является удаление окисной пленки. Обезжиривание производят ацетоном, бензином или иным растворителем. Зачищают поверхность наждачной бумагой, щеткой или сеткой из нержавеющей проволоки, абразивными кругами. Пленку окислов можно убрать и травлением определенными кислотами, но этот способ является более хлопотным в сравнении с механической зачисткой и применяется гораздо реже.
Нужно понимать, что после удаления старой окисной пленки, взамен ее мгновенно образуется новая, так что полностью избавиться от оксидного барьера все равно не получается. Смысл зачистки состоит в том, что вновь образующаяся пленка оказывается значительно тоньше и слабее старой, в результате чего флюсу с ней легче справляться.
Способы нагрева
В качестве основных инструментов для нагрева относительно массивных алюминиевых деталей применяются газовые горелки, работающие на пропане, бутане, или паяльные лампы.
При нагреве следует проявлять осторожность, чтобы не допустить перегрева основного металла, способного привести к его расплавлению. Нужно постоянно контролировать температуру основного металла, прикасаясь к нему стержнем припоя. При достижении рабочей температуры он начнет плавиться.
Пламя должно быть нормальным – без избытка или недостатка кислорода. В сбалансированной газовой смеси пламя только нагревает металл и не оказывает сильного окислительного действия. В случае сбалансированной газовой смеси пламя горелки обладает ярко-синим цветом и небольшой величиной. Пересыщенное кислородом пламя сильно окисляет поверхность металла, его факел бледно-голубого цвета и маленький.
Мелкие детали с небольшим теплоотводом при использовании низкотемпературных припоев паяются электропаяльниками.
Технология пайки алюминия
Процесс пайки алюминия с флюсом практически ничем не отличается от пайки меди или стали. После очистки деталей и установки их в нужное положение, на зону пайки наносится флюс, после чего соединение подвергается нагреву до температуры, при которой припой начинается плавиться. Плавление осуществляют прикосновением кончика стержня к стыку соединения.
Пайка бесфлюсовым припоем имеет особенность, заключающуюся в том, что для облегчения проникновения припоя через оксидную пленку, её желательно разрушить, осуществляя чиркающие движения твердым концом прутка припоя или стержнем из нержавеющей стали по расплаву. При этом происходит нарушение целостности окисной пленки.
Припой расплавленный на неразрушенную оксидную пленку и соединение после разрушения оксидной пенки чирканьем стержнем припоя по расплаву
Разрушать оксидную пленку можно и щеткой из нержавеющей стали, растирая ею расплавленный припой по поверхности деталей. Соединяемые элементы лучше прижимать друг к другу лужеными поверхностями и нагревать до температуры пайки. Полученное таким способом соединение получается очень прочным.
Пайка алюминия: зачистка и плавление припоя
Пайка алюминия: разрушение оксидной пленки щеткой и плавление припоя на второй детали (затем нужно обработать щеткой как первую деталь)
Пайка алюминия: соединение деталей и проверка на прочность
Примеры использования пайки алюминия
Алюминиевой пайкой можно ремонтировать и восстанавливать детали из алюминия и его сплавов любой сложности, начиная от самых простых, используемых в быту, и заканчивая изделиями, к которым предъявляются повышенные требования в отношении прочности и безопасности.
Пайка алюминия широко используется при ремонте автомобилей, тракторов, мотоциклов. Во многих случаях она оказывается предпочтительней, чем сварка, поскольку не приводит к изменению структуры металла и его деформации. Восстановление герметичности протекшего картера из алюминия, пайка алюминиевого радиатора, ремонт изношенной или разрушенной детали – для всех этих случаев пайка может оказаться безальтернативным способом устранения неисправности.
Пайкой можно отремонтировать алюминиевый блок цилиндров, заделать появившиеся на нем трещины, прогары, сколы. Восстановить резьбу в разбитом резьбовом отверстии. Для этого последнее заполняется расплавленным припоем, после чего в него вставляется болт. После охлаждения конструкции остается лишь вывернуть болт. Прочность резьбы, восстановленной таким способом, не уступает прочности исходной.
Восстановление резьбы пайкой: погружение болта в отверстие с расплавленным припоем и выкручивание болта из застывшего расплава
Пайка позволяет заделать отверстия в различных емкостях и изделиях, для которых необходима герметичность. Паять открытым пламенем емкости, в которых хранились воспламеняющиеся жидкости нельзя!!
Запаивание отверстий. После пайки поверхность зашлифовывается.
Пайкой ремонтируют алюминиевые трубопроводы компрессоров, насосов и кондиционеров. Пайка алюминия в домашних условиях позволяет отремонтировать любую вещь, изготовленную из чистого алюминия или его сплава – лестницу, водосточный желоб, посуду, алюминиевый сайдинг. При использовании качественных материалов может быть достигнута такая прочность соединения, что отремонтированное изделие окажется прочнее нового.
Если нет хорошего флюса и припоя
При отсутствии активных флюсов и предназначенных для алюминия припоев можно попытаться паять алюминий оловянными или оловянно-свинцовыми припоями, применяя способ разрушения оксидной пленки под слоем канифоли. Такой способ позволяет избежать мгновенного образования новой оксидной пленки взамен удаленной старой (как это происходит при зачистке на воздухе).
Роль инструмента, разрушающего оксидную пленку, играет специальный паяльник со скребком или добавленные в канифоль железные опилки. При трении облуженного паяльника о деталь, покрытую канифолью, скребок или опилки удаляют старую пленку, а канифоль не позволяет образоваться новой. Одновременно происходит лужение очищенной от окисла поверхности припоем, добавляемым на паяльник по мере необходимости.
Этот хлопотный и не гарантирующий успеха способ целесообразно применять лишь в случае крайней необходимости. Самый простой и естественный вариант – приобретение качественных флюсов и припоев, пайка которыми обеспечивает получение прочного и коррозионностойкого соединения без ненужной траты времени и сил.
Источник http://tool-land.ru
Пайка алюминия – флюс, припой, оборудование
Пайка алюминия — флюс, припой, оборудованиеОчень часто приходится сталкиваться с необходимостью паять алюминий: потекла кастрюля, нужно соединить провода, и т. д. При этом пайка алюминия существенно отличается от пайки меди.
Во-первых, для того, чтобы паять алюминий в домашних условиях, необходима температура значительно выше. Во-вторых, приходится сталкиваться с необходимостью разрушения оксидной пленки, которая присутствует на поверхности алюминия.
Для её удаления применяются специальные флюсы для алюминия. В этой статье сайта svarkapajka.ru мы рассмотрим процесс пайки алюминия в домашних условиях, и расскажем, какие материалы для этих целей необходимо использовать.
Припой для пайки алюминия
Для пайки алюминия подходит самый обычный припой. Чаще всего это олово, но можно использовать и свинец, цинк, висмут. Наибольше всего для пайки алюминия подходит припой 34А, с высоким содержанием алюминия, меди и кремния. Не меньшей популярностью обладает и специальный припой для алюминия ЦОП-40.
Основное отличие припоев для алюминия не только в процентном содержании всех вышеперечисленных компонентов, но и в температуре разогрева. Самым плавким припоем считается припой с большим содержанием олова. А вот такой припой, как Aluminium-13 поддаётся плавлению только при очень высоких температурах, начиная от 590 градусов с плюсом.
Поэтому если пайку алюминия приходится осуществлять в домашних условиях, то лучше взять оловянный припой. Для его разогревания понадобится самый обычный электрический паяльник, мощность которого составляла бы от 60 Ватт.
Флюс для алюминия и сплавов
Вторым материалом по необходимости для пайки алюминия, является флюс. Он содержит специальные вещества, которые способны разрушить оксидную плёнку, что даст припою нормально схватиться с металлом.
Для пайки алюминия применяются следующие виды флюса: Ф-59А, Ф-61А, Ф-64А. Все они имеют в своём составе аммоний и триэтаноламин, которые способны вступать в реакцию с алюминием.
При этом стоит понимать, что если пайка алюминия осуществляется посредством газовой горелки, то для удаления оксидной пленки применяются так называемые высокотемпературные флюсы. Одним из таких флюсов, является флюс марки 34А.
Чем и как паять алюминий в домашних условиях
Для пайки алюминия и изделий из него в домашних условиях можно использовать как газовую горелку, так и паяльник. Он должен быть достаточно мощным, поскольку пайка алюминия требует высоких температур в отличие от пайки меди. Паяльник для пайки алюминия нужен не менее чем на 60 Вт.
Сам процесс пайки алюминия в домашних условиях выглядит так:
- В начале поверхность алюминия тщательным образом обезжиривается. Для обезжиривания допускается использовать бензин, ацетон и растворители;
- Затем производится удаление оксидной пленки с поверхности алюминия. Сначала наждачной бумагой, а затем флюсом для пайки алюминия;
- После этого осуществляется нагрев места пайки (газовой горелкой или паяльником) и распределение припоя.
Припой подносится к месту пайки, после чего расплавляется паяльником и заполняет собой пустоты или место соединение деталей. Вся сложность здесь заключается в быстром остывании алюминия, поэтому часто флюс и припоя приходится подносить к месту пайки повторно, разогревая их паяльником или газовой горелкой.
Пайка бронз сплавов алюминиевых – Энциклопедия по машиностроению XXL
Флюсы особенно эффективны при пайке обычными электропаяльниками алюминиевых проводов, фольги и ряда монтажных деталей из различных металлов (меди, ее сплавов, бериллиевой бронзы и стали). [c.276]На медных сплавах, легированных алюминием, бериллием, кремнием и большими количествами цинка, образуются окислы этих элементов, характеризуемые высокой химической стойкостью и высокой свободной энергией образования. Поэтому перед пайкой латуней, бериллиевых, алюминиевых и кремнистых бронз производится особо тщательная обработка поверхности. Окислы кремния, бериллия, алюминия перед пайкой удаляют во фтористоводородной кислоте или в смеси соляной и азотной кислот, после чего поверхность сплавов защищают слоем достаточно активного флюса.
[c.307]
При пайке некоторых металлов и сплавов, покрытых устойчивыми окис-ными пленками, обычно применяемые способы удаления этих пленок (флюсование, применение восстановительных и нейтральных газовых сред и т. п.) могут оказаться недостаточными. К таким металлам относятся алюминий, алюминиевая бронза, высоколегированные стали, чугун и Др. В этих случаях для успешного затекания припоя в зазор применяют предварительное покрытие поверхности паяемых деталек припоем или металлом, на которых при пайке образуются менее стойкие и, следовательно, легче паяемые окислы металла или сплава. Для этой цели применяют олово, медь, серебро, кадмий, железо, никель и сплавы олово—свинец, олово— цинк и олово—медь. Способы нанесения металлических покрытий на поверхности деталей приведены на рис. 6. [c.221]
Пайка алюминиевых бронз между собой. с медью, латунью, черными сплавами. )
[c.124]
Известны припои, обеспечивающие низкое электросопротивление паяных соединений. Такими припоями для коррозионностойких сталей, меди и алюминиевой бронзы являются следующие. % Sn—0,5-т20 РЬ—0,2—10 Ае—0,1—5 Си—0,1—3 Zn—О—3 Si с температурой плавления 295—Э45°С и значением р=1.18-10 Ом-мм /м, а для флюсовой пайки алюминия и его сплавов припои состава, % А1—I Sv—22 Си—1—5 Si—7—16 Zn с температурой плавления 480—560 °С и электросопротивлением р=2,1Ы0- Ом-мм /м. [c.201]
При содержании в серебряных припоях более 0,01% Л1 (алюминий может попадать в жидкий припой, в частности, из алюминиевой бронзы или из сплавов А1—Ni—Со при пайке их со сталью) образуются малопрочные соединения из-за повышенной их хрупкости, обусловленной образованием на границе шва со сталью хрупких интерметаллидных прослоек. [c.113]
Алюминиевые, кремниевые и марганцовистые бронзы легкоплавкими припоями рекомендуется паять с химически активными флюсами 1) равные части соляной кислоты и хлорида цинка (25% воды) 2) ортофосфорная кислота. Для активности флюсов при пайке алюминиевой бронзы к смесям буры, борного ангидрида, фторидов и фторборатов рекомендуется добавлять 15% хлорида цинка флюсы без хлорида цинка вызывают образование черной пленки на поверхности сплава [163].
[c.307]
Твердые припои применяют для пайки меди, латуни или бронзы, когда требуется большая механическая прочность. Изготовляют их обычно из меди и цинка. Для пайки контактов прерывателя и распределителя используют твердый припой, содержащий серебро, повышающее электропроводность припоя. Пайку алюминиевых сплавов осуществляют с помощью алюминиево-медных или алюминиево-кремниевых припоев. Температура плавления, твердых припоев составляет более 550 °С. [c.113]
Алюминиевые бронзы морозостойки, не магнитны и не дают искры при ударах. Отрицательным свойством этих сплавов является то, что они трудно поддаются пайке твердыми и мягкими припоями и недостаточно устойчивы в условиях перегретого пара.

Газовую сварку применяют при изготовлении и ремонте изделий из тонколистовой стали ремонтной сварке литых изделий из чугуна, бронзы, алюминиевых сплавов монтажной сварке стыков трубопроводов малых и средних диаметров (до 75… 100 мм) с толщиной стенки до 4…5 мм и фасонных частей к ним сварке узлов конструкций из тонкостенных труб сварке изделий из алюминия и его сплавов, меди, латуни и свинца при наплавке латуни и бронзы на детали из стали и чугуна наплавке твердых и износостойких сплавов сварке и наплавке чугуна пайке-сварке ковкого и высокопрочного чугуна. [c.338]
При пайке встык некоторых медных сплавов (нейзильбер, алюминиевая бронза, сплавы медь — никель) припоем Си — 8% Р необходимо применять флюсы. Соединения из меди, паянные встык эвтектическим припоем Си — 8% Р, имеют предел прочности 196 Мн1м (20 кГ1мм ). Пайка может производиться без флюса, но при температуре несколько более высокой, чем с флюсом (730° С вместо 715° С) [240]. При пайке без флюса фосфор частично удаляется, в структуре паяного шва выделяется избыточная медная фаза.
[c.220]
Особенностью алюминиевых бронз являете повышенная по сравнению с оловяинымн бронзами величина усадки, что вызывает необходимость применения особых предосторожностей при заливке для получения качественного. литья. Алюминиевые бронзы более склонны к трещииообразованию при затрудненной усадке, повышенному газонасыщению и окислению при неблагоприятных условиях плавки и заливки. Алюминиевые бронзы как материал обладают высокой гидроирочностью, однако получить из них герметичные отливки слол -1ЮЙ конфигурации часто труднее, чем из оловянных бронз из-за образующихся в сплаве окислов алюминия. Недостатком алюминиевых бронз является также трудность, с которой они поддаются пайке. [c.224]
Литий — серебристо-белый очень мягкий металл, легко окисляющийся на воздухе. По ГОСТ 8774—75 устанавливаются три марки лития ЛЭ-1 (содержание чистого лития не менее 99,5%), Л9-2(98,8%) и ЛЭ-3 (98,0%). Применяется в машиностроении для дегазации и раскисления стали, чугуна, бронз и латуни, в баббитах — вместо олова для повышения температуры плавления и апти-фрикгцгонных свойств. Повышает качество алюминиевых, магниевых, медных, свинцовых и других сплавов, улучшает их антикоррозионные и литейные свойства и т. д., образует твердые припои для пайки без флюсов. Поставляетс.ч в виде чушек массой до 2,5 кг и хранится в плотно закрытых (запаянных) банках из белой жести (по 12—20 чушек — до 50 кг), залитых смесью трансформаторного масла (50%) и парафина (50%) с надписью Осторожно, от воды загорается .
[c.170]
Алюминиевые брснзы выделяются высокими механическими свойствами среди медных сплавов, в связи с чем их широко применяют в машиь острое-нии. В промышленности используют как двойные сплавы меди с алюминием (простые бронзы), так и более сложные по составу бронзы с добавками марганца, железа, никеля и других элементов. На поверхности алюминиевой и кремнистой бронз образуется окис-ная пленка, которая трудно удаляется с использованием обычных флюсов. Изделие перед пайкой необходимо обрабатывать во фтористс-водородпой или плавиковой кислоте. При пайке оловянно-свинцовыми припоями применяют активные флюсы с повышенным содержанием соляной кислоты. Рекомендуются предварительная очистка и флюсование поверхности алюминиевой бронзы смесью борной кислоты с хлористыми солями металлов. Марганцевые бронзы следует паять с использованием ортофосфорной кислоты.
[c.253]
Пайка меди и ее сплавов легко проводится при применении низкотемпературных припоев, при этом используются канифольные флюсы, не вызывающие коррозии. Нередко перед пайкой поверхности деталей облуживаются чистым оловом слоем толщиной 0,005 мм на стали и 0,0075 мм на меди. Применение низкотемпературных припоев не дает высокой прочности паяных соединений, поэтому рекомендуется пайка в печах с высокотемпературными твердыми припоями. Целесообразно применение медно-фос-форных и серебряных припоев. Применяются флюсы на основе буры с добавлением фтористых соединений. При пайке алюминиевой бронзы хорошие результаты получаются при серебряных припоях с никелем, который препятствует проникновению в припой алюминия и повышает производительность технологического процесса.
[c.127]
Поверхностный слой медных сплавов, содержащих кремний, подготовляют к пайке при последовательном погружении в 5%-ный раствор HaSO , затем в смесь 2% HF и 3% H,S04 и затем в раствор, применяемый для подготовки бронз, не содержащих элементов с большим сродством к кислороду. Для подготовки поверхностного слоя алюминиевых бронз применяют два раствора смесь 2% KF и 3% HaSO и смесь 2%-ного раствора бихромата натрия с 5% h3SO4. [c.266]
Слои окислов, образующиеся на алюминиевых, бериллиевых, хромистых бронзах, могут быть удалены перед пайкой также в 20— 30%-ном растворе серной кислоты в воде. Температура воды 60—80° С. Растворение окислов возможно также в водном растворе азотной кислоты (30% по объему HNO3). После снятия окалины паяемые детали должны быть промыты для удаления следов кислоты и осушены. Поэтому перед пайкой латуней, бериллиевых, кремниевых и особенно алюминиевых бронз их поверхности особенно тщательно обрабатывают. Окислы кремния, бериллия, алюминия перед пайкой удаляют во фтористоводородной кислоте или в смеси соляной и азотной кислот, после чего поверхность сплава немедленно защищают слоем достаточно активного флюса.
[c.266]
Свинцовые латуни, кремниевые бронзы, оловянные бронзы и медно-никелёвые сплавы склонны к- горячеломкости поэтому детали из них при пайке не назревают на весу, не подвергают воздействию резких усилий или нагрузок, нагрев при пайке проводят достаточно медленно. Йод действием нагрева при пайке возможно снижение механических свойств паяных соединений из бериллиевой бронзы, упрочняемой в процессе старения. Алюминиевые бронзы во избежание окисления и возможности образования хрупких интерметалл ид ов в шве следует паять, применяя быстрйе способы нагрева. [c.273]
В настоящее время достаточно хорошо отработаны методы низкотемпературных механических испытаний на растяжение. Эти испытания проводятся, как правило, на стандартных машинах, снабженных криостатом и дополнительными тягами для передачи на образец растягивающего усилия, а также системами термо- и тензометрирования I313, 377], В зависимости от конструкции криостата образец может находиться в соприкосновении с жидким хладоагентом, обдуваться его парами или быть изолированным от жидкости и паров. В последнем случае широко используется метод отвода тепла от образца по металлическому холодопро-воду. Основными конструктивными материалами при изготовлении криостатов и их элементов являются хромоникелевые стали аустенитного класса, алюминиевые и титановые сплавы, сплавы на основе меди (бериллиевые бронзы) и никеля (типа монель). В неразъемных соединениях применяется сварка и пайка серебряньш припоем. Для изготовления прокладок в разъемных соединениях используются индий, серебро, медь, алюминий, свинец, фторопласт.
[c.259]
ПСр-72 Серебро—72 Медь—28 779 360 Пайка токоведуш,и.х деталей из меди, латуни, бронзы и других металлов, кроме алюминия, алюминиевых и магниевых сплавов. Швы обладают большой механической прочностью и проводимостью
[c.203]
Бериллий, хром, цирконий и кадмий добавляют в небольшом количестве в специальные бронзы. В меди в твердом состоянии они растворяются незначительно. Присутствие их в сплаве сильно повышает механические свойства, создает условия для хорошей пайки и сварки. Такие сплавы поддаются обработке давлением в горячем и холодном состояниях. Бериллиевая бронза как высокопрочный и неискрящий сплав применяется при изготовлении специального инструмента и пружинящих деталей специального назначения. Хромистые бронзы, обладающие высокой электропроводностью, жаростойкостью и твердостью, применяются для изготовления контактов в электромашиностроении и пр. Кадмиевые бронзы применяются для троллейных, телеграфных и телефонных проводов и как присадочный металл — для сварки алюминиевых бронз. [c.83]
В нек-рых неответственных случаях в качестве присадочного материала применяются сплавы из никеля, меди, железа, марганца и алюминия в различных пропорциях. Иногда в качестве присадочного материала употребляют т. н. бронзу Тобина, к-рая состоит из меди (69—63%), олова (0,5—1,5%) и цинка (40,5— 35,5%). Темп-ра плавления этого сплава достигает 870, так что в данном случае происходит уже не сварка, а пайка. Сущностью горячей газовой заварки, как говорилось выше, является предварительный подогрев отливки, исправление и затем медленное охлаждение в специальной печи. Самый процесс горячей газовой заварки ничем не отличается от заварки холодной. Для доброкачественности отливки заваренную деталь полезно перед охлаждением еще раз нагреть докрасна и лишь затем охладить окончательно. Большое употребление получила дуговая заварка, в особенности тех мест литья, к-рые не подвергаются дальнейшей механич. обработке. При дуговой заварке расплавляющая отливку вольтова дуга зажигается мешду отливкой и специальным электродом, одновременно служащим и присадочным материалом. После очистки литье подвергается иногда термич. обработке. Стальное литье (см.) и ковкий чугун (см.
Чугун ковкий) обязательно отжигаются. Серое чугунное литье, особенно высококачественное, и легированное (см. Чугунное литье) такше м. б. подвергнуто термич. обработке аналогично стали, причем структура чугуна феррито-графито-цементи-товая переходит в структуру перлито-графитную с повышением механич. качеств. Бронзовое и алюминиевое литье такше м. б. улучшено посредством термич. обработки (см. Цеептюе литье).
[c.97]
Для пайки в среде водорода непригодны детали из алюминиевой бронзы Тг, Та, Zn. Успешно паяются в среде водорода изделия из низкоуглеродистой, среднеуглеродистой конструкционной и инструментальной углеродистой сталей, кобальто-вольфрамовых сплавов, бескислородной меди, латуней, ковара Н29К18А и инвара. [c.305]
Пайка алюминия [Архив] – LASERS.FONAREVKA.RU
Просмотр полной версии : Пайка алюминия
Hobbi TV
23.10.2011, 19:50
Кто-нибудь пробовал паять алюминий? Как его паять надо? Перепробовал множество рецептов из инета – не лудится.
Убил 2 дня на эксперименты, чтобы хоть какой-то результат получить. Но, пока он далек от идеала.
у меня дето валялся спец флюс ккак раз для пайки алюминия но я не тестил честно говоря, а по нормальному делают гальванику(наносят медь) и потом пояют вроде как…
Hobbi TV
23.10.2011, 20:14
я не тестил честно говоряЭто главный момент.
Я уже кое-что протестил. Оксидную пленку не берут:
1. паяльная паста
2. спец. флюс ф59а
3. спец. флюс, который нахваливают в инете (без названия)
4. асперин
5. паяльная кислота
6. канифоль
При этом, царапание поверхности тоже не помогает.
chem_kot
23.10.2011, 20:18
Пайка алюминия в любом случае будет непрочной. Практически всегда на поверхности будет оксидная пленка. Но даже если удастся припаяться, место спая будет ненадежным вследствие образования гальванической пары
Оксидную пленку разъедает щелочь. И то со временем…
я зачищаю поверхность, потом царапаю, и грею.

http://pripoi.ru/images/goods/flux-lo/alum.jpg
так и паяется. Остальное бесполезно. Ф59, аспирин, канифоль, кислота, всё тоже проверял. только этот флюс вступает в бурную реакцию, пузырясь на алюминии. а если разогреть, то “эффект” будет лучше.
я описывал в теме про свой фонарик, что алюминий паяется нелегко, и не всегда с первого раза… Приходится несколько раз зачищать заново, пока не получится((
о вот такой флюс и у меня)
Technic47
23.10.2011, 21:13
Al2O3 съедает серная кислота более 80%. Более никак. У него 1-ая группа механической прочности. То есть физически если только шкуркой. А химически он очень стоек.Щёлочь разъест, если доберётся до самого алюминия. То есть если расцарапать, то можно съесть. К примеру я травил дюраль от любой плёнки в KOH и потом в азотной кислоте. После этого на поверхности чистый алюминий. Но это очень сильные щёлочь и кислота. Более 90%.
Согласен. Но у меня таких адовых концентраций нет, и я просто повышаю температуру алюминиевой детали.

да, соединение нельзя назвать надёжным, но оно удовлетворительное уж точно… гнул милиметровый облуженный МГТФ, и пайка не отвалилась. А сколько под ней осталось оксида… Тут уж как повезёт…
Вот ↓ Анодированный радиатор. Шкрябал только точку нагрева. остальное флюс пожрал.
Hobbi TV
23.10.2011, 22:14
греюА чем ты ее греешь? У меня ни паяльник, ни печка с этим флюсом не сработали. А вот в паяльной ванночке этот флюс схватился.
Но, у него проблема – повышенное газообразование. В результате припой начинает бурлить и не на всем протяжении детали схватывается. Кстати, в паяльной ванночке надо его использовать только в защитных очках – легко можно без глаз остаться.
Добавлено через 3 минуты
Насколько я вычитал, самый мощный флюс из придуманных для алюминия – ф-69. А также, припой нужен с содержанием олова не менее, 60 процентов. А лучше, цинк. Вот только, где чистый цинк найти, я пока не понял.
Ф-69 нашел в продаже – завтра в магазин заеду. Заодно и припой в ванночке заменю, а то у меня там “дедушкин”. Понятия не имею, сколько в нем олова.
Грею зажигалкой либо стоватным паяльником. Бурлит сильно. но наношу раза 2. успевает всё объесть. Дым просто сдуваю от себя 🙂 И как я уже говорил, я сам не знаю насколько равномерно схватывается поверхность под припоем.
кстати насчёт флюса… Ходя по магазам обнаружил разницу в цвете. Этот флюс почему-то может иметь оттенок от жёлтого до коричневого. Причина этого мне неизвестна…
Hobbi TV
23.10.2011, 22:22
Этот флюс почему-то может иметь оттенок от жёлтого до коричневого.
Ага, я тоже внимание обратил. У тебя светлый, а у меня темный.
это фото с поисковика 🙂
chem_kot
23.10.2011, 23:48
Цинк можно содрать с новых солевых батареек (не алкалиновых) – стаканчик
А механически или просто кислотами/щелочами удалять оксид алюминия бесполезно – в воде/на воздухе он мгновенно образуется вновь.
Hobbi TV
23. 10.2011, 23:57
кислотами/щелочами удалять оксид алюминия бесполезно
Флюс же тоже не просто так придумывали.
Lum1noFor
24.10.2011, 00:06
Не смотря на все потуги разработчиков флюсов и т.д. алюминий нормально не паяется ничем. Немного схватывает, но при первой же нагрузке все отвалится. Сам раньше интересовался этой темой, а потом забросил, т.к. решения так и не нашел.
chem_kot
24.10.2011, 00:41
Флюс же тоже не просто так придумывали.Как правило, такие флюсы не на водной основе 😉 тот же глицерин…
А о невозможности нормальной пайки я писал на прошлой странице…
Есть специальный припой для пайки аллюминия. Паяет намертво и без всякого флюса. Правда достаточно высокотемпературный. В чип и дипе покупал, кажись этот: http://www.chipdip.ru/product0/79927976.aspx.
Hobbi TV
24.10.2011, 13:36
Есть специальный припой для пайки аллюминия.К сожалению, мне он не подходит. 🙁
Скорее всего, он на основе алюминия. А мне надо не алюминий с алюминием спаять, а разъем к алюминию припаять. Материал разъема без проблем лудится пастой. Подозреваю, что специализированный припой его не возьмет.
Если нагреть алюминий, и расплавить на нем припой, а потом под припоем царапнуть его то должно схватится, еще его термитным карандашом сплавляют))
А ещо можно ртутью покрыть, на амальгаме оксидная пленка не держытся, а затем паять, но он будет быстро окислятся на воздухе (сам проверял)
Паять с ртутью? Ну вы извращенец 🙂 Поделитесь противогазами.
Паять с ртутью? Ну вы извращенец 🙂 Поделитесь противогазами.
ну если безвыходная ситуация то можно и со ртутью, причем образуется амальгама алюминия, из ее ртуть не должна испарятся(ею зеркала раньше покрывали), и еще малые количества ртути безвредны, и отравление ею наступает при вдыхании ее паров на протяжении 1-2 недель, в количестве из двух градусников;)
и воще я привел это как просто еще один безотказный вариант, и ни кто вас паять с ней не заставляет
Я сначала лужу алюминий припоем “Авиа-1”, а затем паяю.
Hobbi TV
24.10.2011, 23:59
Если нагреть алюминийСудя по всему, это одна из главных проблем. Причем, не решается тривиально.
расплавить на нем припой, а потом под припоем царапнуть его то должно схватится
Куплю скальпель – попробую еще раз. Если просто паяльником царапать – ноль эффекта.
А ещо можно ртутью покрыть
Не, больничка у меня пока в планы не входит. 🙂
Добавлено через 1 минуту
Я сначала лужу алюминий припоем “Авиа-1”
Его еще достать надо умудриться – нет даже в Ч&Д. 🙁
Hobbi TV
25.10.2011, 00:08
В процессе экспериментов стало понятно только одно: прежде, чем алюминий лудить, его надо предварительно нагреть до температуры работы флюса. После этого нанести флюс, а уже потом лудить. Как }|{B@N и советовал.Кстати, ф64 – круче нонейма. Если его на алюминий нанести, то на поверхности начинается мощная реакция (флюс буквально кипит). Только, от этого пока не легче. 🙁 Паяльная ванна его не залудила, паяльник не может прогреть деталь до требуемой температуры, а паяльная печь успевает испарить флюс с поверхности до плавления пасты.
Придется покупать паяльный стол…
Ryazanec
25.10.2011, 13:32
Я паял с металлическими опилками, они насыпаются на алюминий, затем свеху флюс (когда его не было, то просто капал расплавленной канифолью) и грел паяльником с большой каплей припоя, опстепенно шкрябая по алюминию. Опилки царапали алюминий, а капля припоя постепенно прилипала к царапинам. Царапать нужн оприличное время, канифоль может выкипать – ей придетя добавлять, иногда приходится подсыпать опилки, они абразивную функцию выполняют.В любом случае пайка не очень надежная, припаяный толстый провод можно оторвать с припоем от пластины, если очень сильно потянуть за провод, в случае с пайкой к меди – отрывается провод от припоя, надрывая его.
Да, иногда этим способом не с первого раза припаять получается, есликанифоль выгорает и становится темной, то она загрязняет царапины сильно, тем же отскобленным окислом.
Паять ужно паяльником с медным жалом – необгораемое жало так испортить можно.
я зачищаю поверхность, потом царапаю, и грею. только потом наношу флюс:
http://pripoi.ru/images/goods/flux-lo/alum.jpg
так и паяется. Остальное бесполезно. Ф59, аспирин, канифоль, кислота, всё тоже проверял. только этот флюс вступает в бурную реакцию, пузырясь на алюминии. а если разогреть, то “эффект” будет лучше.
я описывал в теме про свой фонарик, что алюминий паяется нелегко, и не всегда с первого раза… Приходится несколько раз зачищать заново, пока не получится((
У меня такой-же флюс есть. Пробовал с его помощью облудить паяльником – бесполезняк. Так и валялся без дела. Сейчас, воодушевленный темой и паяльной станцией, решил снова попытать счастья. И… слава lukey 702, заработало:) Оптимальная технология получилась такая – греем люминь феном, до плавления припоя, кладем капельку припоя сверху, потом на гвоздике капельку флюса. Начинается бурная реакция и припой растекается по поверхности. Можно слегка гвоздиком подправить. И все;)
Hobbi TV
26. 10.2011, 01:37
Я припаял провод к анодированному алюминию, не счищая анодирование. При этом провод держится так, что руками не оторвать. Правда, припой у меня не захотел растекаться по поверхности – пришлось его повозить. Наверно, текучесть зависит от сплава.
Основная проблема – теплопроводность алюминия. Ставил эксперименты на заготовке 30х45х2 мм. Нагрел ее до 350 градусов, снял с паяльного стола и вставил залуженный провод в припой на ее поверхности. Секунд через 20 припой схватился (ПОС61 – температура плавления 220 градусов), а еще секунд через 40 заготовка была чуть теплая. Вот такая теплопроводность у алюминия. Обычным паяльником нормально к нему что-то припаять – без шансов.
Lum1noFor
29.12.2013, 02:12
Здесь дело не в флюсах, а в припое. Наткнулись тут недавно на припой какой-то – продается в тонких стерженьках, где-то по 5 баксов за 10 см. Температура плавления около 450 градусов, т.е. только горелкой. Но держит так, что не отодрать никак. Брали пластинки алюминия толщиной около 4 мм, спаивали их буквой Т. Зажимали в тиски и ударяли молотком. Только гнется, а место спайки намертво. Если кому интересно – могу узнать, что за припой. Паяется вообще без флюса.
Мне интересно что это за припой.
Мне интересно что это за припой.
Был в сообщении N18.
Hobbi TV
31.12.2013, 01:22
Здесь дело не в флюсах, а в припое.Еще как в флюсе.
Суть пайки то простая. Флюс растворяет окислы и замещает их собой, чтобы новые не образовались. А припой уже вытесняет флюс и вступает в контакт с чистым металлом. Без флюса не обойтись…
Паял тут провода на листовой алюминий, чисто канифолью паяльник грел до 360град
конечно пайка фигня но держится. Да KOH и NaOH вступают в реакцию значит оксид съедает, но вот попробовать щелочью припаять еще. В принципе порошок железа есть у меня.
Еще один говорил что паял так: чистил алюминия напильником под маслом что бы воздух не соприкасался и тогда оксид не образуется, и паяется норм. Он так кабель на антенны паял.
Hobbi TV
08.01.2014, 10:38
Еще один говорил что паял так: чистил алюминия напильником под маслом что бы воздух не соприкасался и тогда оксид не образуется, и паяется норм.
Можно и так. Но, это геморрой какой-то. Проще специальный флюс использовать…
была идея сделать мини камеру, по типу углекислотной… но руки не дошли.. может кто чего ковырял? )
Ryazanec
24.08.2015, 13:24
Проще канифоль с опилками смешать, и при пайке напильником шкрябать, опилки оксид сами снимут а олово прилипнет – способ для походных условий, когда есть в наличии канифоль напильник и гвоздь для получения опилок, но нет масла.
лучший способ это меднение того места где паять, проверено!
лучший способ это меднение того места где паять, проверено!
А это можно сделать легко и просто, без хитрых реактивов?
А может тогда не медь, а сразу олово наносить…
Hobbi TV
24. 08.2015, 23:53
Какое меднение? =O Я же лично алюминий паял…
Лучший способ – это специальный флюс для алюминия. Во время пайки возникает только одна проблема – нагреть деталь до температуры работы флюса. Для этого я и купил паяльный стол. Без него, проблематично. Но, если удастся деталь до нужной температуры нагреть – руками припаянный провод уже не оторвать.
ну если безвыходная ситуация то можно и со ртутью, причем образуется амальгама алюминия, из ее ртуть не должна испарятся(ею зеркала раньше покрывали), и еще малые количества ртути безвредны, и отравление ею наступает при вдыхании ее паров на протяжении 1-2 недель, в количестве из двух градусников;)
и воще я привел это как просто еще один безотказный вариант, и ни кто вас паять с ней не заставляет
очень сомнительно насчет безвредности, такая бяка склонна накапливаться в организме со всеми вытекающими. Римляне вон попили из свинцовых водопроводов )))
очень сомнительно насчет безвредности, такая бяка склонна накапливаться в организме со всеми вытекающими.
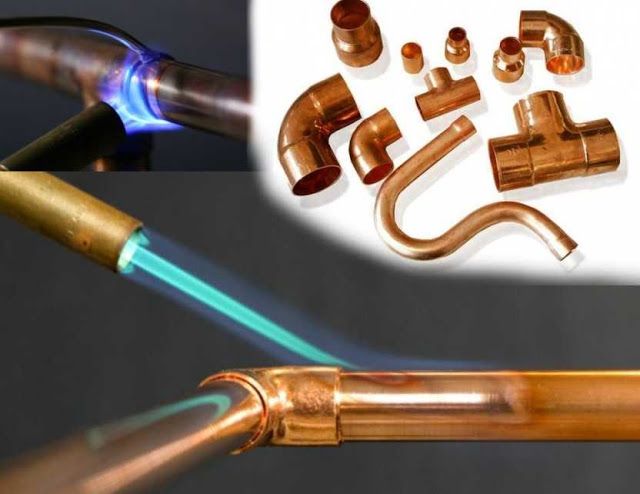
Непростой вопрос… Как-то в детстве, я разобрал старый сломанный уличный термометр, в котором было где-то полстакана ртути. Долго играл с ртутью, пока случайно не разлил на “черной” лестнице. Ртуть раскатилась на мелкие шарики по всем углам, собрать практически ничего не удалось. И никто не умер. Хорошо хватило мозгов, не баловаться с ней в комнате:)
Vlad, ну да, я еще не подумал об том что она взаимодействует с водой и изделие развалится…
Можно попробовать паять в атмосфере бутана, берем небольшую но высокую посудину, ложем туда детальку и заполняем ее бутаном из баллончика.Под слоем бутана зачищаем участок, куда будем паять, а дальше огнеопасно пожалуй… Можно очистить алюминий от оксидной пленки под каким нибудь керосином и залудить) Можно залудить сплавом розе, керосин ведь не кипит при 100С.:)
vBulletin® v3.8.7, Copyright ©2000-2022, vBulletin Solutions, Inc. Перевод: zCarot
Техника пайки алюминия Применение флюса для пайки алюминия Алюминий широко используется в качестве материала для самых разных конструкций. По прочности он лишь немного уступает стали.Алюминий гораздо легче поддается обработке, у него очень высокая электро- и теплопроводность. Однако при решении вопроса, как паять алюминий паяльником, возникает серьезная проблема, так как есть свои особенности и трудности. Дело в том, что для алюминия обычные способы не подходят. Техника пайки алюминия Сложности пайки алюминия обусловлены его способностью образовывать окисные пленки буквально за доли секунды. Поэтому для этой операции к паяльникам требуются специальные сменные жала или флюсы на ртутной основе. В то время как алюминиевые провода относительно легко паять, существует много проблем с неудобными плоскими поверхностями. Для их решения необходимо провести тщательную подготовку к работе. Процедуру пайки можно производить обычным паяльником с обычным припоем и канифолью. Из-за высокой теплопроводности алюминия паяльник должен иметь повышенную мощность от 60 до 100 Вт. Если имеющийся паяльник не в состоянии прогреть крупные детали, их дополнительно прогревают на электрической или газовой плите. Перед началом пайки стык тщательно зачищают напильником, крошащимся кирпичом или наждачной бумагой. После удаления с поверхности толстой оксидной пленки ее обезжиривают бензином или любым органическим растворителем. После этого место пайки смазывается флюсом. При этом паяльник погружается в канифоль. Появление легкой дымки свидетельствует о готовности к работе. Вместо канифоли можно использовать нашатырный спирт. Таким образом, жало паяльника очищается от оксидов посторонних металлов. Дальнейшая процедура практически ничем не отличается от работы с обычными металлами. Очищенное жало паяльника окунают в припой и держат в нем до полного покрытия пленкой. После этого небольшое количество припоя захватывают жалом, переносят на место пайки и разравнивают по всей поверхности, предварительно залудив ее. Затем наносится основное количество припоя для обеспечения прочного соединения алюминия. Подождите, пока припой остынет, а затем протрите место соединения влажной тканью.Окончательную очистку производят напильником или наждачной бумагой. Флюс для пайки алюминияФлюс играет особую роль в процессе пайки алюминиевых деталей. Эффективно удаляет содержащиеся в воздухе оксидные пленки и жир. Кроме того, флюс защищает поверхности от окисления при пайке. Флюс для пайки алюминиевый продается в готовом виде, но его вполне можно приготовить самостоятельно. Для приготовления флюса: взять 30 г хлористого цинка, 10 г хлористого аммония и растворить в 60 миллилитрах воды. Часто вместо флюса используют так называемую паяльную жидкость или паяльную кислоту. Его получают взаимодействием концентрированной соляной кислоты с металлическим цинком. Для этого кислоту наливают в стеклянную или фарфоровую посуду. Это действие нельзя проводить вблизи открытого пламени из-за взрывоопасности выделяющегося водорода. Цинк добавляют в кислоту небольшими порциями. В результате химической реакции образуется хлорид цинка. После того как водород перестанет выделяться, посуду с полученным веществом помещают в теплую воду.Готовую жидкость смешивают с нашатырным спиртом. При нормальном соблюдении технологии прочность связи выше, чем у многих металлов. |
В.![]() A: Пайка — это процесс соединения сходных или разнородных металлов с использованием присадочного металла, который обычно включает в себя основу из меди в сочетании с серебром, никелем, цинком или фосфором.Пайка охватывает диапазон температур от 900°F до 2200°F (470°C – 1190°C). Пайка отличается от сварки тем, что при пайке основные металлы не плавятся, поэтому температура пайки ниже температуры плавления основных металлов. По той же причине пайка является лучшим выбором для соединения разнородных металлов. Паяные соединения прочные. Правильно выполненное соединение (например, сварное соединение) во многих случаях будет таким же прочным или более прочным, чем соединяемые металлы. Обычно пайка используется при производстве компрессоров, циркуляционных труб дизельных двигателей, горнодобывающих инструментов, сантехники, ювелирных изделий, музыкальных инструментов, холодильников, конденсаторов и автомобильных приборов. Сварка — это процесс соединения сходных металлов. Сварка соединяет металлы путем плавления и плавления: 1) соединяемых основных металлов и 2) наносимого присадочного металла. При сварке используется точечный, локализованный подвод тепла. В большинстве случаев при сварке используются металлы на основе черных металлов, такие как сталь и нержавеющая сталь. Сварка охватывает диапазон температур от 1500°F до 3000°F (800°C – 1635°C). Сварные соединения обычно прочнее или столь же прочны, как и соединяемые основные металлы. Металлизация (а.к.а. Термическое напыление) — это процесс нанесения износостойких и коррозионно-стойких покрытий для защиты компонентов и восстановления. Ключевые отрасли промышленности включают аэрокосмическую, автомобильную, энергетическую, нефтехимическую, биомедицинскую, диэлектрическую и морское бурение. -верхний- |
Как паять алюминий: 6 простых шагов
Алюминий — один из самых ценных товаров на Земле. Это один из самых распространенных материалов на планете, но он также наименее известен и наиболее универсален. В настоящее время он используется в качестве основного металла для изготовления вещей, от дома до офиса, от промышленности до чего угодно и всего.
Это универсальный металл с многочисленными замечательными качествами. Этот кусок металла давно известен своим уникальным сочетанием легкости, долговечности, прочности и низкой электропроводности.
Кроме того, это блестящий металл серебристого цвета, обладающий высокой устойчивостью к коррозии, отличной теплоемкостью и высоким отношением прочности к весу.
Алюминийстановится все более популярным строительным материалом как для коммерческих, так и для жилых помещений. Кроме того, он имеет множество промышленных и бытовых применений, включая кухонную утварь, банки для напитков и даже сплавы, преобразующие прочность стали.
По мере роста объемов использования алюминия возрастает потребность в пайке алюминия и пайке алюминия.
Существуют различные способы изготовления алюминиевых сплавов и алюминиевых соединений. Но одним из самых популярных и надежных является пайка алюминия.
Что такое пайка алюминия?
Пайка алюминия — это процесс соединения алюминия с другим материалом, обычно со сталью, медью или латунью. Термин «пайка» происходит от припоя, используемого для соединения металлов.
Пайка – это процесс, при котором две или более заготовок соединяются вместе путем плавления и введения в соединение присадочного металла (припоя); припой остывает и затвердевает. Затем он образует сплав с основным металлом.
Пайка алюминия, также называемая пайкой твердым припоем, представляет собой процесс металлообработки, в котором для соединения металла используется присадочная проволока и электричество.Электрический ток нагревает присадочную проволоку до тех пор, пока она не вплавится в основной материал, создавая прочную связь между деталями.
Поскольку использование алюминиевых изделий в производстве с годами увеличилось, потребность в создании соединения алюминия с алюминием возрастает. Этот процесс часто используется вместо сварки, потому что он проще и при правильном выполнении может создавать прочные соединения.
Пайка алюминия — отличный навык в современном мире. И если вы тот, кто хочет заниматься пайкой алюминия, то вы попали по адресу.В этой статье мы расскажем вам каждую деталь о том, как паять алюминий. Итак, внимательно следуйте всем шагам, упомянутым ниже, и безупречно выполните свой проект по пайке алюминия.
Подготовка к пайке алюминия:
Перед началом процесса пайки вам необходимо провести некоторую подготовку, чтобы выполнить пайку безупречно. Вам необходимо сделать необходимую подготовку, упомянутую ниже.
- Защитное оборудование: Получите рубашку с длинными рукавами, брюки, ботинки, защитные очки, шлем и перчатки для рук.Эти вещи не должны быть изолированы, и вы должны надеть их перед началом метода соединения алюминия, так как некоторое время это может быть опасно.
- Классификация алюминиевых сплавов: Для пайки можно использовать чистый алюминий или алюминиевые сплавы. Но с чистыми алюминиевыми деталями работать непросто, и в основном для пайки используются алюминиевые сплавы. Хотя правила пайки для всех алюминиевых сплавов одинаковы, с некоторыми сплавами трудно работать. Итак, попробуйте идентифицировать сплавы.Классифицировать его можно по номеру или букве, обозначенной в сплаве. Однако если их нет, то классифицировать их практически невозможно. Но не волнуйтесь, потому что соединение алюминиевого листа с большинством других металлов не требует каких-либо особых действий. Но соединение алюминия со сталью требует специальных методов и опытного сварщика.
- Возьмите низкотемпературный припой: В большинстве случаев для пайки используется универсальный припой, но в случае пайки алюминия его нельзя использовать, поскольку алюминий плавится при температуре 660ºC, что является относительно низкой температурой.
Вот почему вам нужен специальный низкотемпературный припой. При покупке проверьте этикетку припоя и убедитесь, что он имеет более низкую температуру плавления. Опять же, бессвинцовый припой необходим для бесперебойной сварки.
- Выберите правильный флюс: Вы должны выбрать правильный флюс для пайки алюминия для вашего проекта. Флюс зависит от алюминиевого листа или другой металлической комбинации, которую вы собираетесь использовать. Для некоторых металлов требуется специальный флюс. Поэтому приобретайте флюс и припой из одного и того же источника, чтобы выбрать правильный.Используйте флюс для пайки, если температура плавления припоя превышает 450ºC. Но помните, флюс для пайки плохо подходит для тонкой алюминиевой проволоки и алюминиевых листов.
- Выберите источник тепла: Тепло обязательно для пайки. Для алюминиевых проводов можно использовать электрический паяльник. Но для более тонкого или более толстого алюминиевого компонента используйте пропановую горелку.
Но ваше рабочее место плохо сочетается с фонариком, используйте электрический паяльник на 150 ватт.
- Оборудование и рабочая зона: Соберите все оборудование и попытайтесь разместить дополнительное оборудование, такое как зажим, специальный раствор для очистки, ацетон и т. д.Выполняйте работу в хорошо проветриваемом помещении. Подготовьте огнетушитель и поставьте его рядом.
Сделав необходимые приготовления, приступайте к пайке. Внимательно прочитайте шаги, указанные ниже, и следуйте им должным образом, чтобы выполнить пайку безупречно.
- Чистота: Алюминий склонен вступать в реакцию при контакте с воздухом, в результате чего на поверхности алюминия образуется слой оксида алюминия, что неблагоприятно для прочного алюминиевого соединения.Итак, очистите поверхность алюминия перед пайкой с помощью щетки из нержавеющей стали. Кроме того, старые алюминиевые металлические детали склонны к большей реакции, поэтому вам может потребоваться очистить их с помощью ацетона и изопропилового спирта.
- Скрепите вместе основные металлические детали: Если вы выполняете пайку для ремонта определенного объекта, струбцины не нужны. Но если вы соединяете две алюминиевые детали или металлы, вы должны плотно сжать их вместе в соответствии с вашими потребностями и оставить зазор 1 мм или меньше между частями, чтобы припой мог течь.Вы можете потерять зажим, чтобы очистить окисленный слой или другие, а затем снова плотно зажать их.
- Нанесение флюса: После очистки и закрепления сразу же нанесите флюс на область, которую вы хотите соединить. Немедленное нанесение флюса предотвратит окисление. Наносить флюс можно с помощью паяльного стержня или любого другого небольшого металлического инструмента. Но, если вы паяете провода, то вместо того, чтобы наносить на них флюс, окунайте их во флюс.
- Начало нагрева: Выберите метод нагрева для пайки.Используйте паяльник или горелку соответственно, а затем начните нагревать металл.
Начните нагревание в начале места, где вы хотите сделать шов. Но не ставьте пламя на одно место надолго, так как это может привести к перегреву флюса и припоя. Таким образом, поддерживайте расстояние от 4 до 6,5 дюймов между основным металлом и наконечником резака. Медленно и постоянно перемещайте источник тепла, чтобы тепло распределялось равномерно.
- Нанесение припоя: После того, как флюс достигнет нужной температуры, начните нанесение припоя.Нанесите припой, непрерывно нагревая эту область на расстоянии. Перетащите припой через область, где вы хотите, чтобы соединение произошло. Движения должны быть медленными и постоянными, если вы хотите ровной и гладкой отделки. Если вы видите, что припой не склеивает металлы, то зачистите место, так как это может произойти из-за окисления, и сразу же наносите припой. Чтобы получить безупречную отделку, вам нужно больше практиковаться.
- Удалите излишки флюса и оксида: После завершения пайки дайте соединению остыть.
Затем очистите лишний флюс и оксид. Для флюса на водной основе просто смывайте его водой. А для флюса на основе смолы используйте ацетон. После того, как вы закончили удаление флюса, очистите оксиды с помощью травильного раствора. После того, как вы удалили оксид и флюс, вы, наконец, завершили процесс пайки.
Выполняя все шаги, упомянутые выше, вы сможете идеально паять. Все шаги подробно описаны, чтобы вы могли безупречно выполнить свой проект пайки.Но, конечно, чтобы стать профессионалом и иметь гладкую отделку, вам может понадобиться все больше и больше практики. Поэтому прочитайте нашу статью, подготовьте все необходимое и наслаждайтесь гладкой пайкой.
Можно ли сваривать алюминий припоем? – Theburningofrome.com
Можно ли сваривать алюминий припоем?
Алюминию требуется нагрев для принятия припоя, обычно до температуры 300°C или выше. Пайка алюминия не похожа на пайку меди; недостаточно просто нагреть и расплавить припой. Даже с правильной комбинацией флюса и припоя вы не сможете добиться пайки, если алюминий недостаточно горячий, чтобы принять припой.
Как сделать так, чтобы припой прилипал к алюминию?
Когда у вас есть чистый алюминий, вы готовите раствор из сульфата меди и небольшого количества хлорида железа. Использование соли с этим раствором, по-видимому, устраняет окисление алюминия. Затем с помощью того же раствора без соли на металл наносится медное покрытие, которое можно использовать для пайки.
Какой флюс используется для пайки алюминия?
ФлюсKX можно использовать для соединения алюминиевого сплава серии 6000; его содержание цезия помогает реагировать с магнием в этих основных материалах, чтобы смачивать поверхности более эффективно. Этот продукт часто используется в соединении трубы 3003 с соединительным блоком 6061, часто встречающимся в автомобильных трубах HVAC.
Как соединить два куска алюминия?
Существует множество методов соединения алюминия, включая механические крепления, сварку, склеивание, пайку твердым припоем, пайку и сварку трением с перемешиванием (FSW) и т. д.В зависимости от стоимости и прочности, необходимой для соединения, используются различные методы.
Какой клей лучше всего подходит для алюминия?
Цианоакрилат – также известный как моментальные клеи, суперклей, сумасшедший клей, клей ca и т. д. Все марки хорошо склеивают алюминий. Для очень высокой прочности используйте металлический связующий материал, такой как 170 или оригинальный 910®.
Как лучше всего сваривать алюминий?
Лучший способ сварки алюминия
- Используйте растворитель, такой как ацетон, или слабый щелочной раствор, такой как сильнодействующее мыло, чтобы удалить масло, жир и водяной пар с поверхности алюминия.
- Используйте проволочную щетку из нержавеющей стали (используется исключительно для алюминия) для удаления поверхностных оксидов.
Нужно ли предварительно нагревать алюминий перед сваркой?
Обычно для сварки алюминиевых сплавов предварительный подогрев не требуется. Если вы хотите предварительно нагреть, температура должна быть ограничена максимум 200 градусов по Фаренгейту. Этот тип предварительного нагрева часто полезен для удаления конденсата и влаги.
Как соединить алюминий с алюминием?
Как паять алюминиевую проволоку?
Окуните проволоку припоя в алюминиевый флюс.Когда вы решите, что алюминий достаточно нагрелся для пайки (визуально это определить невозможно), нанесите каплю флюса на алюминий, а затем прижмите проволоку припоя к поверхности. Если припой сразу плавится и смачивает поверхность, все в порядке. Если нет, то не заставляйте.
Можно ли спаять алюминий и медь вместе?
Доказано, что он эффективен при пайке алюминия с медью и алюминия с алюминием. Он имеет более низкую температуру склеивания, которая колеблется от 120 до 250°C.Соединение алюминия с медью, керамикой и другими металлами возможно, если удается устранить несоответствие теплового расширения.
Можно ли припаивать алюминий серебром?
Обычный старый серебряный припой с обычным старым флюсом не подходит для алюминия. Есть припои, которые работают с алюминием в сочетании с действительно агрессивными флюсами, но те, о которых я слышал на сегодняшний день, требуют, чтобы вы наносили флюс и припой, а затем чем-то очищали алюминий…
Материалы | Бесплатный полнотекстовый | Пайка алюминиевого сплава 7075 с использованием электроосажденных прослоек Ni-P и Cu-Cr
3.1. Электроосаждение покрытий Ni-P и Cu-Cr
Условия осаждения покрытий определяли с помощью диаграммы Пурбе [30]. Из диаграммы следует, что сплав 7075 имеет значительно ограниченную область коррозионной стойкости в диапазоне возможных гальванических ванн. Таким образом, даже если сплав 7075 можно было бы покрыть в сильнокислотных ваннах, это практически невозможно из-за положения алюминия в гальваническом ряду.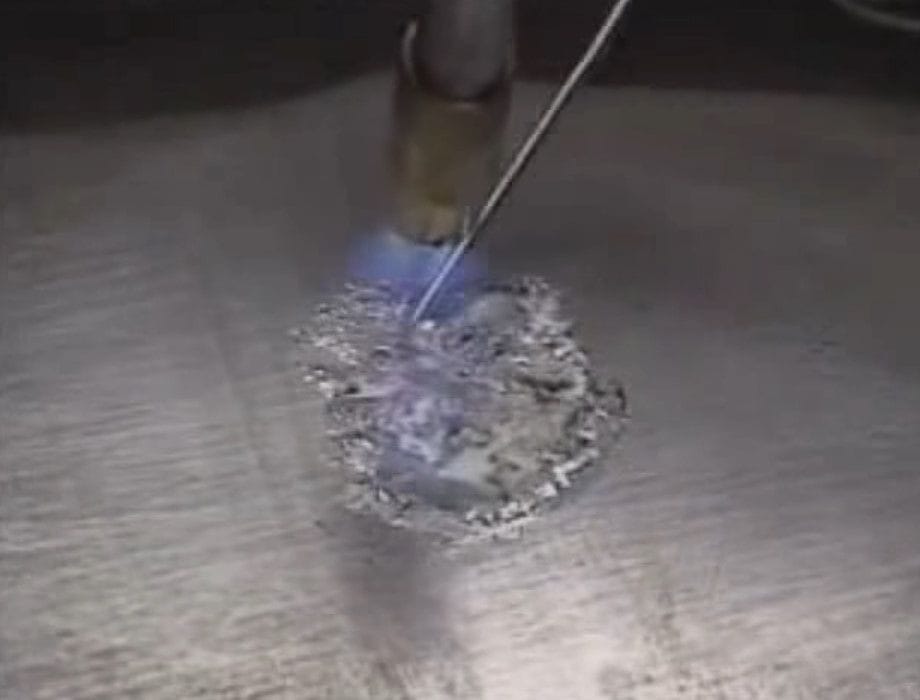
Для нанесения гальванических покрытий была построена лабораторная станция, состоящая из источника питания (Elektro-Tech тип ETZ 10/10, Elektrotech, Крынично, Дольны-Слёнск, Польша) с бесступенчатой регулировкой силы тока от 0 до 10 А и напряжения от от 0 до 10 В, магнитная мешалка (IKA тип ETS 06, IKA Sp. z oo, Варшава, Мазовецке, Польша) с бесступенчатой регулировкой скорости вращения и система нагрева с контролем температуры. На мешалку помещали химический стакан объемом 1 дм 3 , содержащий электролитическую ванну и анод 50×120×5 мм.Анод для нанесения покрытия Cu-Cr был изготовлен из титана с родиевым покрытием, а для нанесения покрытия Ni-P – из катодного никеля.
Процессу осаждения предшествовала правильная подготовка поверхности подложки. На первом этапе образцы шлифовали наждачной бумагой № 150 и 280, а затем подвергали промывке в 5% растворе SurTec 131 (Surtec Poland Sp.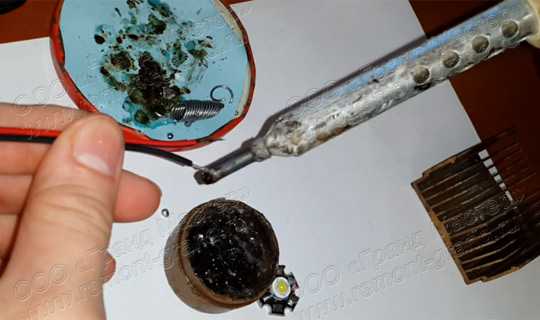
Сначала образцы были химически оцинкованы в ванне SurTec 652Q Surtec Poland Sp. z o.o., Яниково, Великопольша, Польша, при температуре от 15 до 40 °C в течение 1 мин. Далее предварительное электролитическое меднение в ванне SurTec 864 Surtec Poland Sp. z o.o., Яниково, Великопольша, Польша, с pH 9,5 проводили при 55 °C в течение 2 мин. Катодная плотность тока составляла 0,5 А/дм 2 , анод был изготовлен из бескислородной меди (ББК). На подготовленные таким образом подложки наносились соответствующие покрытия, предназначенные для пайки.Для этого были разработаны две ванны:
- Гальваническая Cu-Cr ванна – слабокислотная ванна для нанесения медно-хромового слоя, содержащая от 0,9 до 1,2 мас. % Cr [23];
- Гальваническая Ni-P ванна — новая кислотная ванна для нанесения никель-фосфорного слоя, содержащая 12 мас. % P [24].
Сплав Cu-Cr можно использовать в качестве покрытия с повышенной стойкостью к истиранию. В соответствующих источниках не упоминаются гальванические ванны для нанесения покрытий из сплава Cu-Cr, но можно найти информацию о получении этих покрытий в металлургических процессах, в основном применяемых в энергетике.
Составы ванн и параметры процесса нанесения Cu-Cr покрытия следующие:
8–12 г/дм 3 хрома металлического в виде хлорида хрома III;
12–15 г/дм 3 медь металлическая в форме хлорида меди II;
80–120 г/дм 3 хлорида аммония в качестве проводящей соли;
pH раствора в пределах 3,8-4,5;
температура процесса от 55 до 65 °C;
катодная плотность тока от 1.
от 5 до 3,0 А/дм 2 ;
время обработки от 40 до 60 мин.
Сплав Ni-P применяется, в том числе, в производстве присадочных металлов, используемых для бесфлюсовой пайки. Может применяться в гальванотехнике в качестве декоративного никелевого покрытия с повышенной коррозионной стойкостью (альтернатива хромовому покрытию).
Химически нанесенные Ni-P покрытия применяются в качестве технических покрытий с высокой коррозионной стойкостью, зависящей от концентрации фосфора.Химическое покрытие никелем также применяется в производстве пластмасс.
В литературе можно найти публикации о разработанных ваннах для электрохимического осаждения Ni-P покрытия. Ванны для нанесения такого покрытия, содержащие 18 мас. % P, являющиеся альтернативой хромовому покрытию, разработаны немецкими и итальянскими фирмами [32]. В эти ванны ионы фосфора доставляет натриевая соль фосфорной кислоты III, добавляемая в количестве 5–7 мас.%. Покрытия применяются в качестве декоративных покрытий при производстве арматуры и фурнитуры, деталей бытовой техники и в автомобильной промышленности.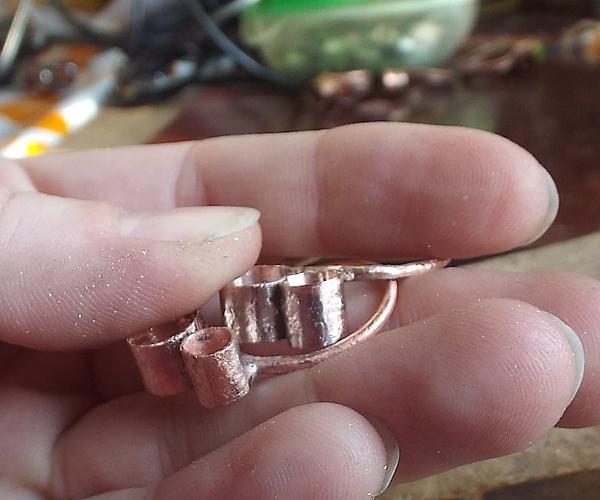
Состав ванны и параметры процесса нанесения разработанного Ni-P покрытия следующие:
15–18 г/дм 3 никеля металлического в виде сульфата никеля II;
100–150 г/дм 3 фосфора в форме нитрилотри(метилен)фосфоновой кислоты;
100 г/дм 3 лимонной кислоты;
рН раствора в пределах 1,5-2,5;
температура процесса от 45 до 55 °C;
катодная плотность тока от 1.от 0 до 2,5 А/дм 2 ;
время обработки от 15 до 25 мин.
3.2. Оценка нанесенных покрытий
Электролитически нанесенные покрытия были подвергнуты предварительному анализу. Их толщину и химический состав измеряли с помощью рентгенофлуоресцентного анализатора FISCHERSCOPE X-RAY XDL-B производства Fischer GmbH (Ахерн, Бадения-Виртембергия, Германия). Концентрация Cr (вес. %) была измерена для покрытия Cu-Cr, концентрация P (вес. %) была измерена для покрытия Ni-P, а балансом были соответственно содержания Cu и Ni.Приложения для измерения покрытия Ni-P являются коммерческими продуктами, но приложение для измерения покрытия Cu-Cr было разработано компанией Helmut Fischer GmbH Achern, Бадения-Виртембергия, Германия, для нужд данного исследования.
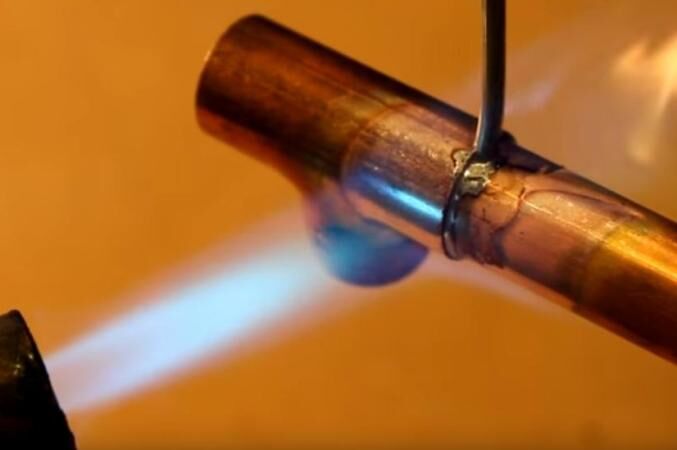
После электролиза все образцы выдерживали в электрической печи при температуре 200 °C в течение ок. 30 мин, а затем опускали в емкость с водой комнатной температуры. Через 1 мин визуально оценивали отслоение покрытия. Все образцы положительно прошли испытание на термический удар без видимого отслаивания.
Испытание на адгезию с помощью Micro-Combi-Tester начинали с измерения силы царапания непокрытой подложки, а затем измеряли усилие, необходимое для отслаивания покрытия от подложки с покрытием. Испытание проводили на расстоянии 5 мм при силе давления 29 Н. Покрытие отслаивали одновременно в двух местах и регистрировали среднее значение приложенных усилий.
Испытание на адгезию проводили следующим образом. Отдирочная головка, нагруженная с указанной силой, начинала отдирать покрытие, и компьютер фиксировал все события, сопровождающие процесс (т.г., разрыв покрытия). После проникновения в материал подложки были сделаны микроскопические фотографии во всех точках, где была нарушена непрерывность измерения, и, наконец, была сфотографирована вся царапина.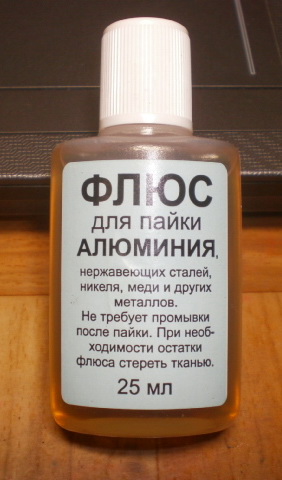
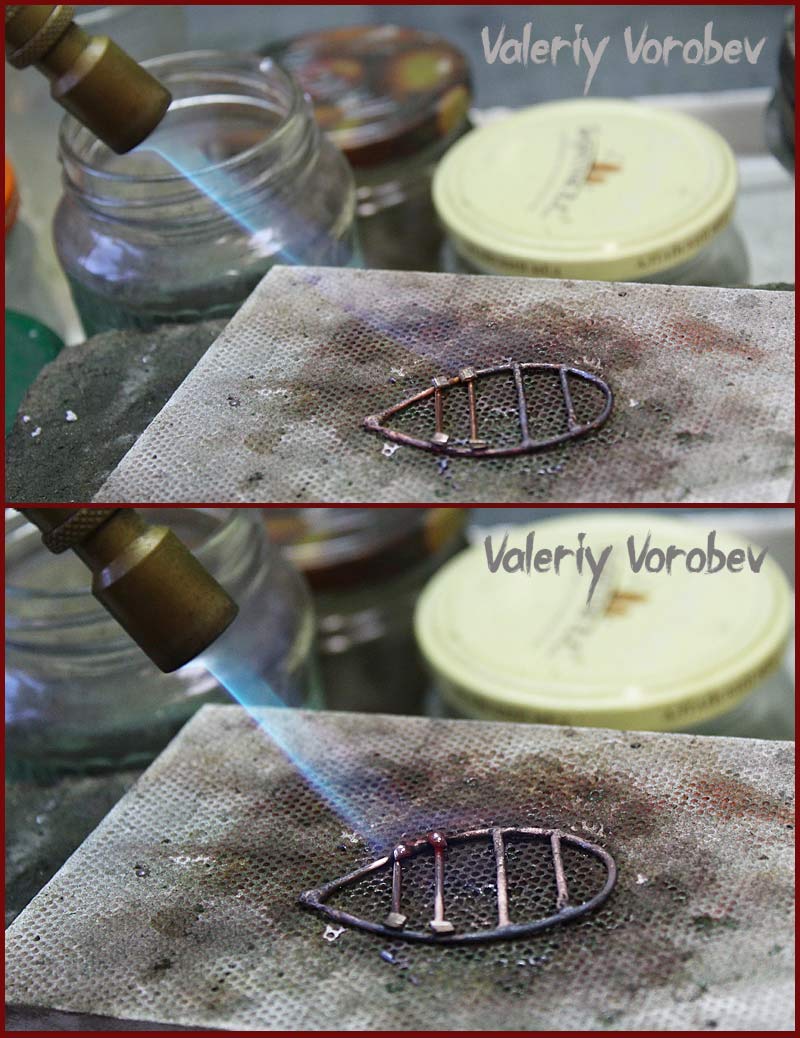
3.3. Испытание на смачиваемость
Как упоминалось выше и показано на рисунке 1, подложка из сплава 7075 не смачивается мягкими припоями. В результате невозможно сделать паяные соединения напрямую. Пригодность нанесенных покрытий Cu-Cr и Ni-P для пайки определяли путем измерения смачиваемости их поверхностей припоем на основе олова.Образцы изготавливали способом, описанным выше. По критерию смачиваемости чем меньше угол смачивания и больше площадь поверхности растекающихся капель, тем лучше паяльные свойства подложки. Принято считать, что хорошая смачиваемость имеет место, когда угол смачивания меньше 30° и стремится к 0° [34, 35, 36]. = 7,2 мм 2 ) для покрытия Cu-Cr и 59 мм 2 (σ = 8.1 мм 2 ) для покрытия Ni-P. Примеры областей растекания припоев и поперечных сечений капель припоя на подложках, использованных для определения углов смачиваемости, показаны на рис. 4. Средние значения угла смачиваемости составили 28° (σ = 7,3°) для покрытия Cu-Cr и 17° ( σ = 4,8°) для покрытия Ni-P.
3.4. Металлографическая оценка паяных соединений
Как упоминалось ранее, соединения внахлестку с нахлестами длиной 10 мм и постоянной шириной паяных зазоров фиксируются дистанционными элементами диам. 0,2 мм были подготовлены для металлографических исследований и механических испытаний. Соединения выполнены пламенной пайкой с использованием пропаново-воздушной горелки. За исключением мельчайших газовых пор и остатков флюса, других дефектов пайки обнаружено не было.После пайки покрытия оставались сплошными и хорошо прилипали к подложке из сплава 7075. Соединение, выполненное с промежуточным слоем Cu-Cr толщиной 12 мкм, показано на рис. 5. На рис.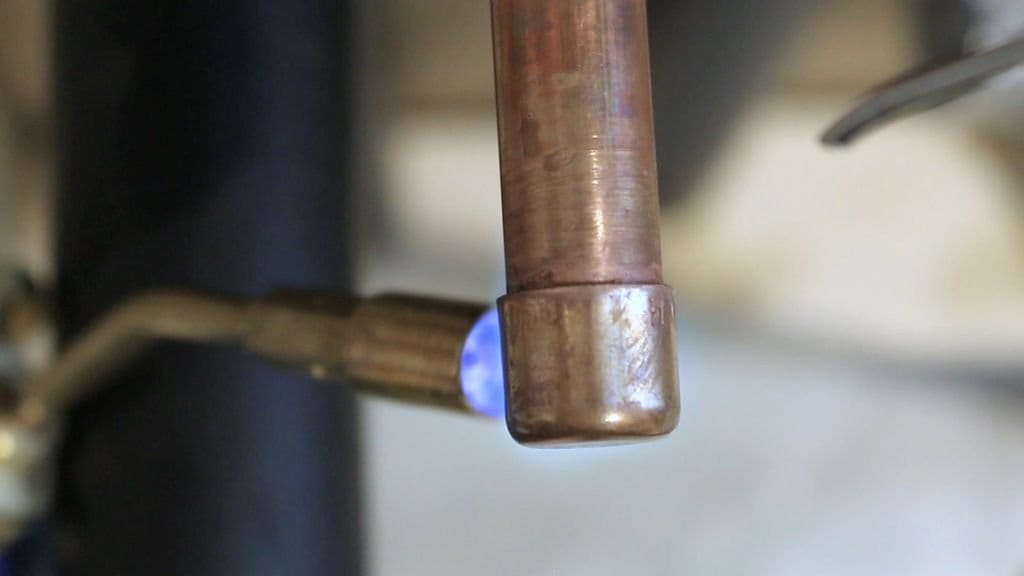
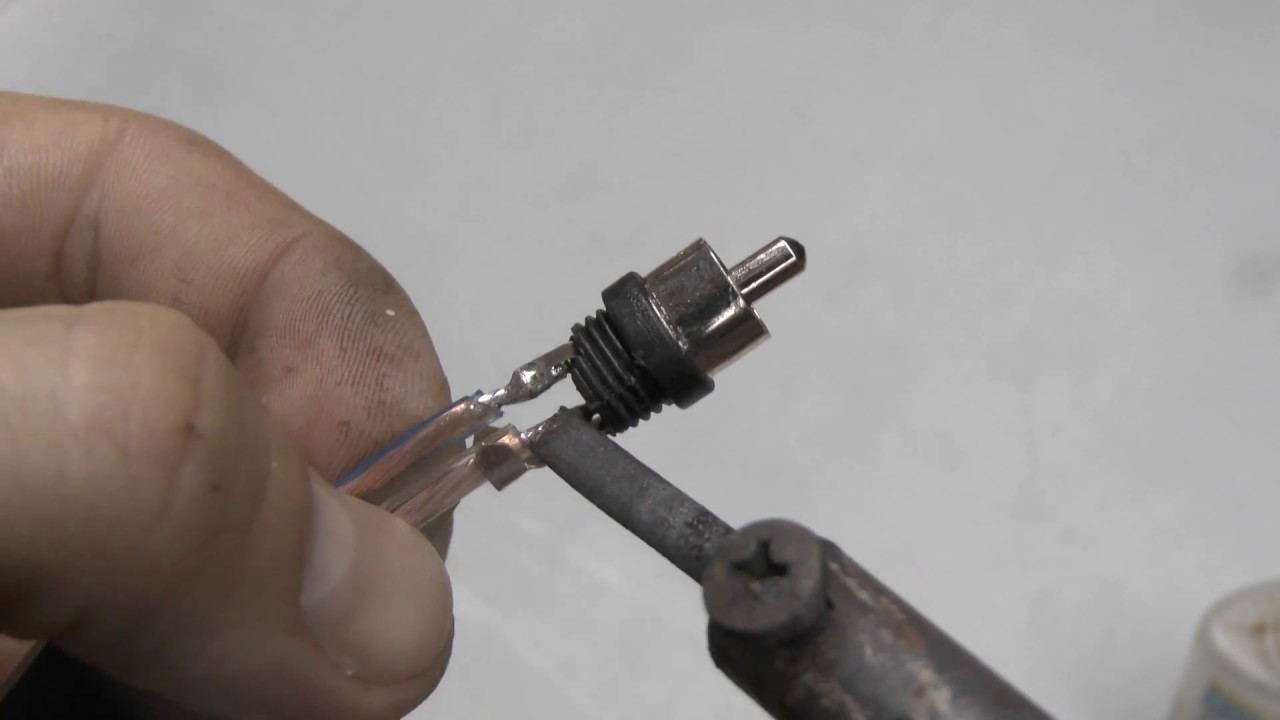
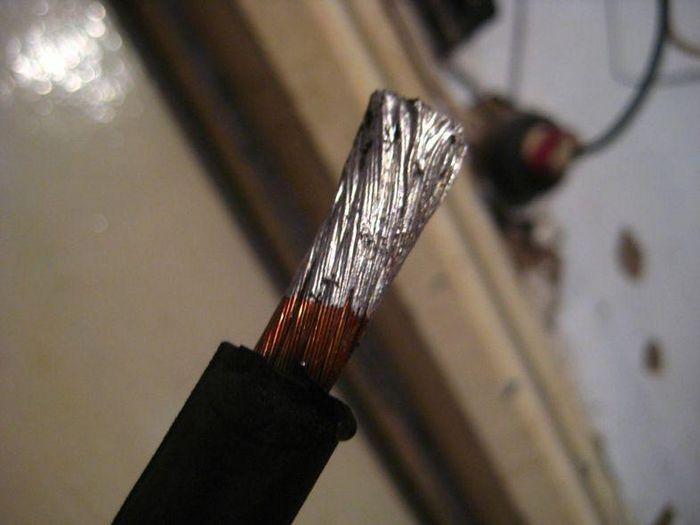

3.5. Испытания механических свойств паяных соединений
Испытания на растяжение и сдвиг соединений, выполненных с использованием прокладок Cu-Cr и Ni-P, проводились на универсальной испытательной машине Zwick/Roell Zmart-PRO (Zwick-Roell GmbH, Бадения- Виртембергия, Ульм, Германия).Паяные соединения располагались в захватах машины с использованием подходящих дистанционных вставок, а затем растягивались со скоростью 2 мм/мин. Для каждого покрытия было подготовлено пять комплектов паяных соединений. Перед испытанием на сдвиг обрывки припоя механически удаляли с обеих сторон соединения. Результаты испытания паяных соединений на статическое растяжение при сдвиге показаны в таблице 5. Прочность на сдвиг паяных соединений в обоих случаях была одинаковой и составляла ок. 35 МПа. Механизм разрушения обоих соединений носил когезионный характер и происходил в слое припоя (рис. 9).Что важно, покрытия Cu-Cr и Ni-P сохраняли сцепление с подложкой. Таким образом, можно предположить, что соединения могут выдерживать более высокие нагрузки, если механические свойства используемого припоя выше.
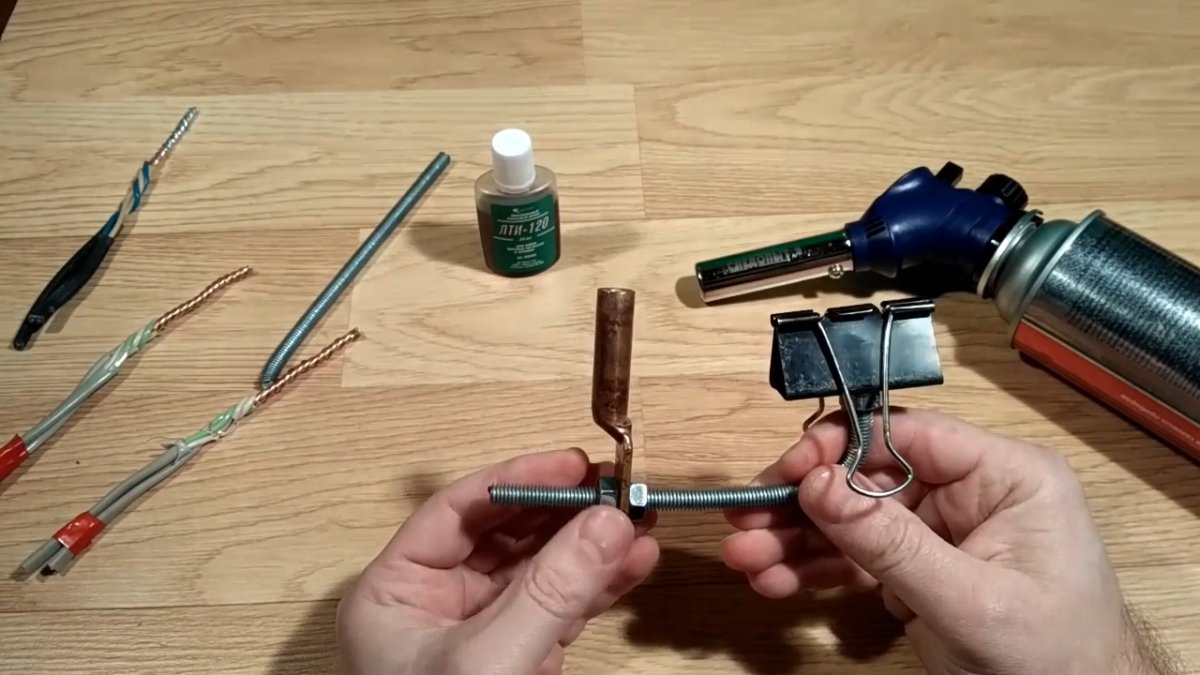
Соединение с полупроводниками на основе алюминия и меди (химический никель/золото для припоя и соединения проводов)
Технологии химического никелирования и иммерсионного золотого покрытия (e-Ni/Au) традиционно использовались почти исключительно в электронной промышленности для создать паяемую поверхность на материалах подложки, например ламинированные доски. Недавние достижения в этих технологиях нанесения покрытий, наряду с присущими им низкими затратами, связанными с процессами нанесения покрытий химическим способом, позволили расширить их использование в различных полупроводниковых приложениях, например.г. металлизация пластины уровня пластины. В этой статье описываются процессы химического никеля и иммерсионного золота для полупроводников на основе алюминия и меди. Ванна для никелирования представляет собой раствор на основе гипофосфита, а ванна для золотого покрытия представляет собой раствор на основе сульфата, не содержащий цианидов. Для интегральных схем на основе алюминия процесс цинкования используется для инициации роста никеля, а для меди палладий используется для катализа поверхности. Для обеспечения воспроизводимости требуется жесткий контроль химических реагентов, оборудования и переменных процесса во время выполнения.Оже-анализ тонких пленок после нанесения покрытия показывает четко определенные слои золота высокой чистоты и никеля/фосфора. Адгезию слоев e-Ni/Au оценивали путем измерения нагрузки, необходимой для сдвига контактных площадок ввода-вывода, покрытых высокими никелевыми выступами. Целостность никеля дополнительно оценивали, подвергая конструкции нескольким температурным циклам и тестируя на сопротивление сдвигу подушки.
Результаты показывают отсутствие деградации при поперечной нагрузке или режиме разрушения.
Нанесение никеля и золота на поверхности контактных площадок ввода-вывода позволяет в последующем использовать методы межсоединений как с проводным соединением, так и с флип-чипом (свинцовые и бессвинцовые сплавы).Целостность соединений золотой проволоки с контактной площадкой ввода-вывода с покрытием e-Ni/Au оценивалась с использованием сдвига шарика, натяжения проволоки и соответствующего анализа отказов каждого из них. Результаты показывают значения, значительно превышающие технические характеристики продукта, с режимами разрушения проволоки при растяжении в проволоке и интерметаллическим разрушением в исследованиях сдвига шарика. Для применения во флип-чипах слой e-Ni/Au был оценен с использованием технологии трафаретной печати для нанесения нескольких различных сплавов припоя. В текущем расследовании два испытательных автомобиля были успешно испытаны с припоем на основе свинца 63Sn/37Pb и 90Pb/10Sn, а также с 95. Бессвинцовый сплав 5Sn/3,8Ag/0,7Cu. Чтобы оценить совместимость этих сплавов со слоем никеля, полученного химическим способом, были проведены испытания на сдвиг припоя в зависимости от количества циклов оплавления. Результаты показывают отсутствие деградации при сдвигающей нагрузке или режиме разрушения среди всех трех испытанных сплавов, что указывает на отсутствие критического расхода никеля (т. е. чрезмерного роста интерметаллидов) во время оплавления. Были проведены дополнительные тесты, сравнивающие толщину никеля в металлургии под ударом (UBM) 1, 2 и 5 мкм.Опять же, критического расхода никеля не обнаружено.
Медно-алюминиевая паяльная паста Pure and Raw Form для сварки Выбор избранных поставщиков
Важность медно-алюминиевой паяльной пасты на Alibaba.com в основных или большинстве сварочных работ неоспорима и не может быть подчеркнута в достаточной степени из-за их защитных свойств при сварке. Эти флюсы не только предотвращают реакцию внешних газов со свариваемыми деталями, но и обеспечивают большую точность всего процесса.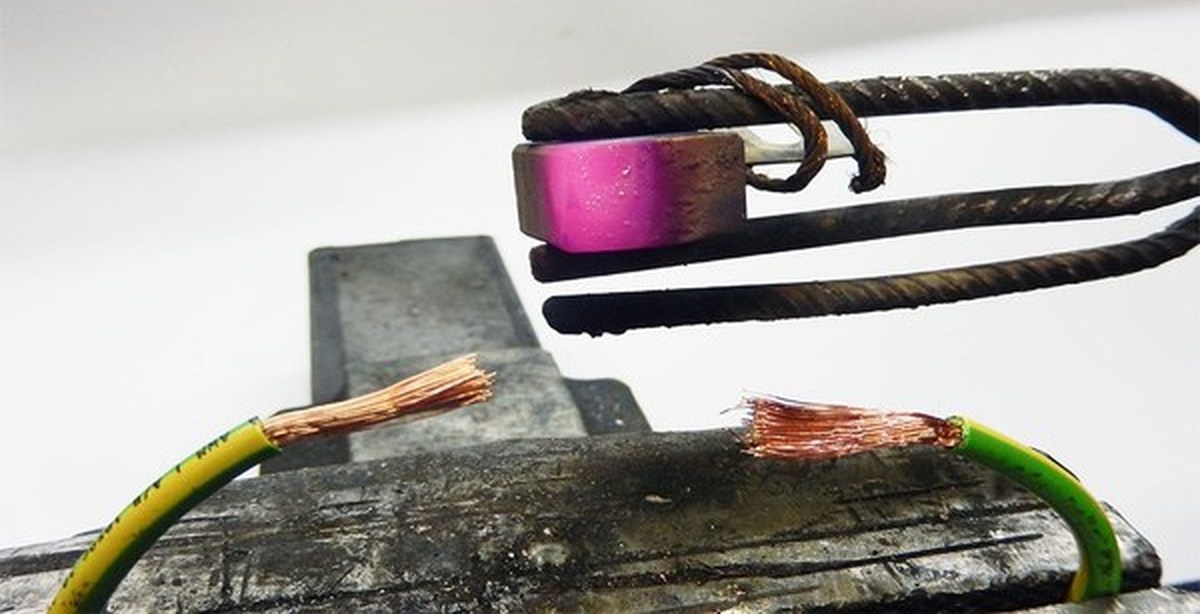
Выбирая из множества высококачественных, чистых форм медно-алюминиевой паяльной пасты , клиенты могут выбрать лучшие продукты, соответствующие их требованиям. Эти продукты являются 100% оригинальными и имеют более длительный срок хранения.Продукты, предлагаемые на сайте, идеально подходят для сварки конструкций из низкоуглеродистой стали, особенно в случае прерывистой сварки, такой как тонкие листы, или других косметических сварок, где требуется аккуратная отделка.
На Alibaba.com можно найти различные варианты медно-алюминиевой паяльной пасты , доступные как в виде порошка, так и в виде пасты, на выбор клиентов в зависимости от требований.